Turbo Inspection
Operation
Exhaust gas pressure (drive pressure) and energy drive the turbine, which in turn drives a centrifugal compressor that compresses the inlet air (boost pressure), and forces the air into the engine through the intercooler and plumbing. Since heat is a by-product of this compression, the air must pass through an intercooler to cool the incoming air and maintain power and efficiency. Increasing air flow to the engine provides:
- Improved engine performance
- Lower exhaust smoke density
- Improved operating economy
- Altitude compensation
- Noise reduction.
The turbocharger also uses a wastegate, which regulates intake manifold air pressure and prevents over boosting at high engine speeds. When the wastegate valve is closed, all of the exhaust gases flow through the turbine wheel. As the intake manifold pressure increases, the wastegate actuator opens the valve, diverting some of the exhaust gases away from the turbine wheel. This limits turbine shaft speed and air output from the impeller. The turbocharger is lubricated by engine oil that is pressurized, cooled, and filtered. The oil is delivered to the turbocharger by a supply line that is tapped into the oil filter head. The oil travels into the bearing housing, where it lubricates the shaft and bearings. A return pipe at the bottom of the bearing housing routes the engine oil back to the crankcase.
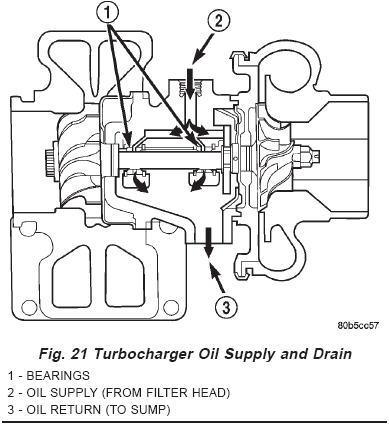
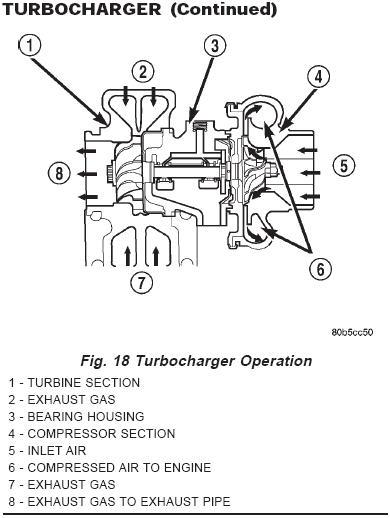
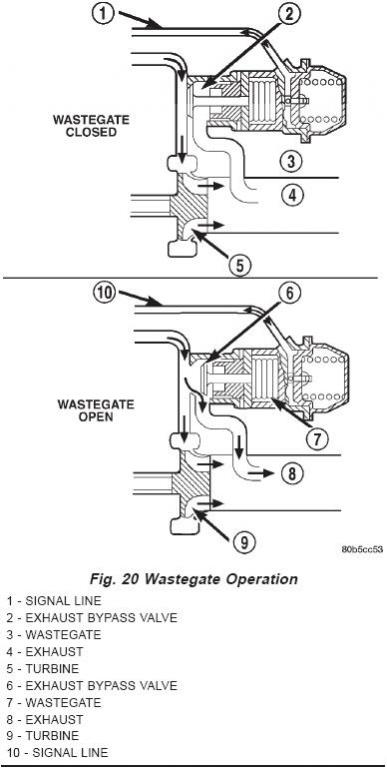
The most common turbocharger failure is bearing failure related to repeated hot shutdowns with inadequate “cool-down” periods. A sudden engine shutdown after the prolonged operation will result in the transfer of heat from the turbine section of the turbocharger to the bearing housing. This causes the oil to overheat and breaks down, which causes bearing and shaft damage the next time the vehicle is started. Letting the engine idle after extended operation allows the turbine housing to cool to normal operating temperature.
Mopar's Notes: You should allow your pyrometer to fall below 300°F before shutdown. If you don't have a pyrometer I highly recommend you purchase a pyrometer gauge and install it. There is also turbo timers that allow the driver to turn off the ignition and lock up the vehicle. The engine will continue to run for set time and then shut down. These add-ons will extend the life of your turbo greatly.
Turbo Inspection Procedure
Visually inspect the turbocharger and exhaust manifold gasket surfaces. Replace stripped or eroded mounting studs.
1. Visually inspect the turbocharger for cracks. The following cracks are NOT acceptable:
Cracks in the turbine and compressor housing that go completely through.
Cracks in the mounting flange that are longer than 15 mm (0.6 in.).
Cracks in the mounting flange that intersect bolt through-holes.
Two (2) Cracks in the mounting flange that are closer than 6.4 mm (0.25 in.) together.
2. Visually inspect the impeller and compressor wheel fins for nicks, cracks, or chips. Note: Some impellers may have a factory placed paint mark which, after normal operation, appears to be a crack. Remove this mark with a suitable solvent to verify that it is not a crack.
3. Visually inspect the turbocharger compressor housing for an impeller rubbing condition (Fig. 25). Replace the turbocharger if the condition exists.
4. Measure the turbocharger axial end play:
a. Install a dial indicator as shown in (Fig. 26). Zero the indicator at one end of travel.
b. Move the impeller shaft fore and aft and record the measurement. Allowable end play is 0.038 mm (0.0015 in.) MIN. and 0.089 mm (0.0035in.) MAX. If the recorded measurement falls outside these parameters, replace the turbocharger assembly.
5. Measure the turbocharger bearing radial clearance:
a. Insert a narrow blade or wire style feeler gauge between the compressor wheel and the housing(Fig. 27).
b. Gently push the compressor wheel toward the housing and record the clearance.
c. With the feeler gauge in the same location, gently push the compressor wheel away from the housing and again record the clearance.
d. Subtract the smaller clearance from the larger clearance. This is the radial bearing clearance.
e. Allowable radial bearing clearance is 0.326mm (0.0128 in.) MIN. and 0.496 mm (0.0195 in.) MAX. If the recorded measurement falls outside these specifications, replace the turbocharger assy.
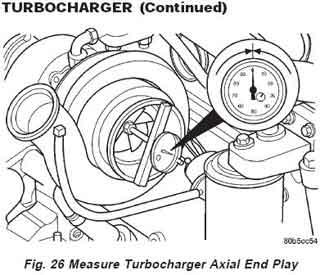
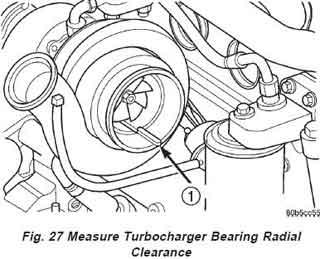
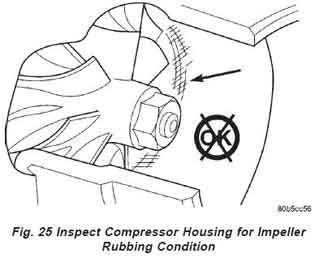
There are no reviews to display.