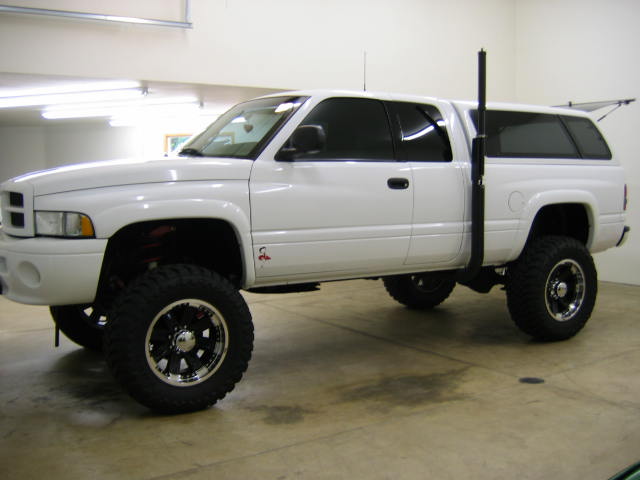
Everything posted by W-T
-
Lift Pump Question
Yes...there is a method that I incorporated into the motor end-cap that makes a remarkable difference. However; I'm going to start a new thread to encompass this material. The new thread will address this issue: @Marcus2000monster said: only thing I’m not happy with is the noise that it makes... it’s just part of it though! So far I’m happy with it! Thanks @trreed! The subject matter will be comprehensive and there is NO short cuts...a "coil" of wire is eliminated for additional noise abatement. With respect gentlemen...I don't halfarss anything, for the sake of technical excellence. We are all Cummins enthusiasts and I share this for the benefit of our fraternity. @Marcus2000monster...btw...I was born and raised in Butte, Montana...so "you" will not be excused easily. Pay attention or I'll come up there
-
Lift Pump Question
Very good, and very true however; the inductance aspect of a coil of wire ( XL= 2* pi * f * L) in regard to "frequency" is where this becomes sensitive or shall we say sympathetic. This "wide band" RF generator (lift pump armature) spinning at a given RPM is emitting a respectable amount of RF hash, my concern with small amounts of inductance even as low as 3 micro Henrys lumped at the end of a wire will enhance that lead at a particular frequency. If an owner operator has a 27 MHz transceiver or perhaps commercial two-way radio equipment on-board this unplanned resonance could become a large factor in receiver performance. I might include the unknown peculiar response of a factory sensor being permeated by a rouge RF source and passed onto the PCM or ECM for added undesired response. The engineering staff at Dodge and of course Carter Industries had some knowledge to select certain add-on elements to produce these vehicles, hopefully without error. Recalls globally, are expensive. I'm only observing the common practice of wire harness layout and avoid common errors. Keeping wire lengths short and concise fall into that practice...a simple coil to alleviate excessive length is avoidable. The "hash" being generated by a DC motor at 13 volts sinking 6 Amps is a respectable amount of energy to deal with and coupling that to a conductor that becomes sympathetically enhanced, only by chance, with a "coil of wire" can introduce unwanted results else where within a system. @trreed you are a deep thinker and I admire your observations.
-
Lift Pump Question
This additional wire should be cut and dressed into the installation properly. Avoid the "coil" method as @Mopar1973Man has indicated. A "coil" of wire in certain circumstances can induce inductive reactance into the controlled circuit. I know we are only transporting B+ and ground in this instance however; correct electronic wire layout disciplines always calls for the "shortest path" to be adopted. This avoids "sympathetic" induction on the wires themselves and any surrounding conductive elements. Your new electromechanical lift or transfer pump is being powered by a DC motor that most likely has carbon brushes making contact with the armature of the motor itself. The "spinning" of this armature at a given RPM with the "carbon brushes" are "making and breaking" contact with the armature. This is a "wide band spark gap transmitter" emitting "wide band" RF (radio frequency) hash across the entire usable Frequency Spectrum. Much of the harmful interference would be in the lower octaves of the spectrum between 500 kilohertz to perhaps the upper VHF frequencies around 165 Megahertz. Tune your factory AM radio to an unused frequency and if you hear "Hash or static" when your lift pump is operational then you have a "new" RF noise issue. The harness connects to your slave relay under the hood and provides B+ to power the lift pump. This "harness" acts as an antenna and it sympathetically radiates this RF hash through out your entire electrical system. Introducing a "coil" of wire to store unused wire length can inductively enhance this undesired aspect of a DC motor running within a closed electrical system. BTW...the original Carter Pump, though a very poor pump, was beautifully electronically by-passed internally....Carter Industries has real RF engineers on staff and the study of "silencing" the DC armature hash is FIRST CLASS ! They may make a very poor mechanical pump but, their electronics is EXCELLENT. No noise from a factory unit...all the high-end aftermarket Lift Pumps are very poorly electronically by-passed...try not to add an antenna to enhance this very undesired trait.This is the "by-pass" circuit board using "chip capacitors" that Carter uses to eliminate AC noise. I carefully cut open a Carter pump to observe their design. It's very good.
-
6.7L Cummins Alternator Mount Type
Nice Job! You're certainly accomplished and the design is first class...VERY NICE! I see you found your way to DC Engineering out of Riverside CA...Indeed, I too recently selected the XP-270 platform and I've not completed the incidentals to actually run the system yet. My requirements are not nearly as demanding as yours so I must say bravo my friend...your selection in iron is well thought out ! Cheers
-
6.7L Cummins Alternator Mount Type
Shayne...I was browsing this morning and ran across your two posts...I thought I was off the deep end until I found what you were doing... I feel better now because you're more insane than I am. Cheers my friend !
-
1/0 alternator cable path under truck
Hey Shayne...If your looking for maximum current delivery at the end of a 25 foot run of cable then you should review the composition of the material being used to conduct this current. The formula for this is also Basic Ohm's law as P= I^R Current itself, is evenly distributed through the cross sectional area of the conducting cable so the resistance of copper-clad aluminium is higher than pure copper. I don't know how much current you're expecting at the far end? I'm assuming with the plan of 1/0 Gage that you plan on providing a considerable amount of available current. You need to ascertain what your total current demand is at the remote location. You will then be able to formulate the losses on your selected cable and determine "if" it will be acceptable. Current demands of any system or "load" above 50 Amps begins to become a serious endeavor in a 13.8 Volt DC delivery layout. Seat-of-the-pants evaluation is, "Once you have every device drawing current at operational level and you can touch the insulated conductors and sense "heat" you have a considerable amount of power being lost in the conducting elements themselves" This loss is the voltage drop within the conductors due to the inherent resistance of the cable. You will see this on a test measurement from one end to the other. So....if you're imposing 13.8 volts at the input and you measure 12.1 at the far end when fully loaded at the demand current your voltage drop is 1.7 volts. Looking at this with an example load figure of say 100 Amps then: P= E*I or 1.7*100 = 170 watts being dissipated in heat. The starter motors for the CTD can sink from 450 to 700 Amps depending on the temperature of the block and oil thickness. The cable transition of 1/0 from the battery to the starter is less than 6 feet but, the demand (or on time) of this power is of short duration. This loss is acceptable for the circuit....living comfort in your 5th Wheel maybe a different. The bottom line is, "Can the electronic instrumentation tolerate a low voltage condition" when you're activating the device(s)? If you can double the Gage thickness of the cable it will provide twice the current handling capability, with half the loss. Pay attention to composition of the cable, the manufacturer's specifications of the cable will recommend maximum expected levels and you're losses. A 25 foot run of cable at 13.8 volts expected to sink 100 Amps with minimal voltage drop is a pretty serious demand...I applaud your plans...it is not for the faint of heart.
-
High amp alternator
My error in communication...the making and breaking of large current demands can mark or scar conductive surfaces. The inductive principles of an alternator are subject to outside source back-pulse if the electromagnetic force is large enough. Sorry Mike, I must question the integrity of the rebuild facility and your observations of solenoid action could be a contributing aspect to shortened life of the alternator. There is NO arc suppression on these solenoids and the event is only dampened by the parallel presence of the storage battery(s). Also, solid state principles of a silicon PN junction, for a large 50 Amp diode...they will open and not conduct but, they never become a full conductive element...so what we deal with is that it, works good or not at all. The load rating...this system will provide 135 Amps from an alternator at speed...we also have two large storage batteries with approximately 1000 Amps each so...if we add this up as a parallel source we have 2135 Amps at 13.8 volts, the power level is 29,463 Watts available at full on insanity grunt. This is extremely impressive...the alternator is the smallest element in this equation. However; when the large current demand of both Grid Heaters activated at the same time the current demand of 190 Amps is paralleled from the systems sources. The large storage batteries are directly providing this current and the alternator only replenishes the loss of "head charge" being removed from the storage batteries. From a straight DC current observation at say 14 volts (engine running alternator charging) we are seeing a timed period where 2,660 Watts being dissipated as heat. Funny enough...this is not quite 10% of what this system is capable of....in a controlled circumstance of course. Now I'm not saying "nothing" is wrong...but, I do not understand why you've lost so many alternators in a short period of time. I don't think you have unknown sources sinking current....I question the supply line of where are these alternators are coming from? If the alternator was providing 135 Amps for extended periods of time I would expect the heat aspect to become excessive. Also, that factory #6 encapsulated in the harness running across the front of the engine and finally breaking out and feeding into the PDC...wow that number 6 is going to melt and fuse with all the other wires within that harness...God forbid ! So...just from a reasonable stand point...is your alternator running at red-line? Is it providing charge at maximum level nonstop for excessive periods of time? Are your storage batteries in such poor condition that the alternator can't replenish the head charge in a reasonable period of time? Knowing you...I could not imagine any of these conditions would be present under your command. With great respect....I must return to the question...where are these alternators coming from? Sorry, I'm not budging on this...light bulbs do not begin to sink additional current in age. It's very uniform across the life due to the vacuum of the glass envelope. These Grid Heater elements are very large conducting surfaces and in time they will out live the power supply. A grievous error of dropping a conductive tool across the elements would indeed cause a parallel circuit and knowing the resistance is around .073 Ohms...less resistance would of course result in additional current being dissipated....however, who would leave a 3 inch extension across the grid face and put the airhorn back in place? These inductive devices will provide an indication of current but, not shop level reference. High current spec's are obtained by calibrated "shunted" instruments and they are easy to build. Be cautious shipping jeweled movement instruments through the mail.
-
High amp alternator
Excellent results Mike, and with a 3 phase 6 diode platform the ripple percentage is well within specification. I have no reason to question the integrity of your storage batteries regarding interconnection cabling. Your anal retentive maintenance disciplines are beyond reproach and as I bow to your examples I will recite, " I am not worthy". But, your hypothetical observation of the solenoids is very interesting. This "extremely high current" switching system may require some investigation. These devices are "switches" and the environment they survive in is hostile at the instantaneous moment in time where they are "hot switched" making or breaking the current path. Now this event is really quite catastrophic for the "point contacts" of these devices. These solenoids have been "hot switching" 95 Amps @14volts plus DC for many years. The entire "power load" appears across these conductive elements (P=E*I...14*95= 1,330 Watts) as the conductive path is energized each and every time the system triggers a demand. The event is both coming and going if you will. Now observing this, equates to an arc-welder and we certainly see this visually...no delicate instrument required. Fresh, new contacts within the solenoids structure has a pair of contacts with physical dimensions of proportional aspects to what this solenoid is "rated" at. The spacing of these contacts is determined by the "peak voltage" rating of the solenoid...these ratings are absolute. Now, as we energize (spark on) and de-energize (spark off) the metal structure of the contact points are blown-away with each action event. In time, the contact surfaces become pitted and also...over time, the length of time it takes for the solenoid to open or close (on & off) increases. The "dwell" of this rouge SPARK begins to lengthen and visually becomes more impressive. I'm wondering, is it possible to consider this event "from a time stand point" that as our alternators are in motion and the "making and breaking" action of the alternator brushes on the "rotor" is being assaulted by the lengthening of the "sparked dwell"....the timing of this could possibly be a contributing factor of "short run life" of an alternator? I have not considered this on our vehicles...again Mike, your observations cause me pause. Perhaps a review of of high current switching contact points within a solenoid needs to be addressed with a simple snubber-RC circuit to aid in arc suppression. This wouldn't correct out of tolerance contact points but, it would help promote contact life and eliminate the "stroke of lightening" splashing the entire electrical platform within these trucks... could this also be an excellent preventative measure to help the VP-44, ECU and PCM electronic failure rates? Holy cow Mike...these speculations are very interesting. Allow me some time to digest your observations.
-
High amp alternator
If you have determined that the AC ripple is beyond what is tolerable along with experiencing other undesired operational irregularities (TC lock/unlock, erratic cruse control) then a replacement alternator would be in order however; prior to making that expenditure a diligent review of the extensive "key DC" grounds should be reviewed. The alternator itself must be at a solid DC ground in order to produce the least amount of AC ripple on it's own B+ output. I expressed quite a surprise when I removed my original equipment alternator to discover the lack of ground continuity through the beautiful beefy mounting system. These 135 Amp factory alternators are very stout power producing devices and with a healthy system (batteries in proper condition) there maybe no reason to spend the money. If the performance has satisfied your needs for years then perhaps a quality rebuild is all that is required. My requirements include a system of power demanding devices that can sink an additional 100 Amps when fully powered up. Hence, the procurement of a 270 Amp device but, I wouldn't advise that for everyone. Any higher powered generating device will require additional upgrades but, mostly just the main B+ DC lead. The factory #6 encapsulated in the harness passing in front of the engine prior to terminating in the PDC (power distribution center) is only barely able to survive at a full 135 Amp draw if your batteries sagged enough to require that continuous level of current requirement. That #6 will cause problems if left within the factory harness. Adding an additional B+ lead as a parallel lead will divide the current equally and remove the worry of possible melt down during high current demand situations. As for Grid Heater elements requiring additional current as they age...no that is not the case. They react just as light bulbs do...you run them, they get hot and they someday, cease to conduct and open up. They are strictly resistive elements and the robust nature of these heating elements represents long life. If you do elect to procure a new alternator, one feature for consideration would be a 6 phase platform over the OE 3 phase. The higher phase product is inherently cleaner DC....the ripple frequency is higher and the excursions in amplitude would be much less....hence you get a cleaner power supply. The upper-end manufacturers do not require you to purchase a smaller serpentine belt...this also aids in the "just drop in a new alternator" simplification factor.
-
High amp alternator
This thread High Amp Alternator, has branched into several areas of Electrical and Electronic subtopics. It may cause a little confusion however; this topic with it's highly comprehensive structure will reveal an overview of value to all who take the time to digest the contents. With generic terminology, we are building a DC (direct current) power supply to correct and alleviate errors. The two substantial storage batteries and the generating source (alternator) are the heart of the system. All Dodge CTD's were produced with substantial "power supplies" and the Bosch or Denso brand alternators are excellent choices to perform the task. These devices can produce up to 135 Amps of power when needed. Properly cared for and serviced they will provide years of trouble free service. Is this system perfect? No, however....they serve the average owner very well. As for Canadians in Saskatoon or Edmonton, Alberta, the design is reaching the upper limit in fortitude and may require additional effort to maintain reliability. I am not implying that Daimler/Chrysler cheated or cheapened the system...I'm simply stating, that any system (electrical) has it's limitations but, again, the average "Joe" rarely sees the maximum demand of conditions on a daily basis. Our Canadian friends experience such conditions...so they would be an excellent example of NOT being the average "Joe". There are other geographical areas that fall into this exception category...and each has particular thermal dynamics that places demands on designed vehicular "mobile power supplies". Moving forward, with sub-topic information, allow me to return to the dreaded "TC lock-unlock" syndrome. The majority of CTD owners with automatic transmissions have experienced this very annoying and detrimental error. The CTD owners with manual transmissions experience similar errors in a different way. Example; speedometer readings that are inconsistent, cruse-control erratic behavior...all of this comes right back to "power supply" problems. @Mopar1973Manhas documented this and shined the light on the cause of this. There is NO doubt, to the validity of Mike Nelson's technical research. Prior to Mike's efforts, the "syndrome" was being discussed on several diesel oriented web sites. The enthusiasm of the CTD's fraternity encouraged a search for answers and Dodge dealership's were being approached to resolve the issues with reportedly poor resolve. Dealerships with under-trained or mildly experienced service technicians were being inundated with troubled service requests. Several aftermarket diesel retailers and specialty performance transmission facilities jumped into the game and offered their "fix" to the situation. Many of you viewing this thread may very well have fallen into this unfortunate happenstance. I too, was pulled into this and purchased a device to alleviate the TC lock/unlock error. I noted several suggestions from transmission specialists to "reroute" certain wires contained in harness assemblies in hope of separating signal (sensor) wires from an offending source within the bundle of wires. Again @Mopar1973Manhis research identified the cause and correctly suggested "fixing the power supply". Mike also warned against utilizing the "fixes" because it was masking the real issue. This is also very true and must be seriously considered. I would like to call your attention to the APPS (accelerator peddle position sensor) "signal-wire" that is routed directly to the PCM entering the most right hand connector. This control module is located on the passenger-side firewall. The "wire" is orange with a dark blue stripe. This photo depicts the "focus connector, black, far right hand" location. This next photo I'm holding the "subject wire" with a small screwdriver (note the heat-shrink) where I removed a "fix" filter and surgically corrected my error. This next photo depicts the actual device, that I have carefully removed the "shrink-wrap" to expose the internal electrical component that was encapsulated.This is a 180uF (180 microfarad) electrolytic capacitor. This component was encapsulated in shrink-wrap with two #18 copper wires exiting the package. One lead had a red-capped "piercing" connector, that allowed connection to the APPS signal wire at the PCM input (orange/DrkBlu) and the other lead was an eighteen inch pigtail ground lead. (Wow 18 inches to ground...silly). This photo (poorly done) is the actual instructions from the retailer who provide these type(s) of devices. (I can't believe I actually did this to my truck) This type of "fix" implemented on a "variable resistance" lead is improperly thought out. Note: the cost of this electrolytic capacitor is approximately 35 cents, the entire structure, build of material cost is less than $1.25 US. An electrolytic capacitor is "large" in nature, electrically. They are used to "filter" DC power. Electrolytic capacitors have specified "voltage" ratings and from the above photo you can see the 25 volt rating. Note, in "all electronic" design, one would determine the maximum DC voltage present in the circuit and in selecting individual components that have a "voltage rating", the designer will specify a rating of at least "twice" the voltage level that the component will be "working in". This aspect was determined correctly by "who ever" designed this. There is an issue here...electrolytic capacitors are "typically" used as a "filter" in DC power supplies. They "act" as large filters absorbing and containing (storing) an electric charge much like a battery stores an electrical state of charge at 12 volts. I wish to keep this at a very basic level...and that is all we need here. Now...we have all experienced working with our VOM's (volt-ohm meters)... we have all measured voltage and resistance with our test instruments. I believe most of us have some form of a "digital" ohm meter... that we have all used to "calibrate" the settings on our APPS, located above the VP-44. Once this is done, the procedure of "turning the ignition key to the ON position" (non-start) and slowly depressing the accelerator peddle to the floor and then releasing the peddle slowly, this then completes the important service of having the PCM recognize the "value" of the APPS. This is just an "electronic" handshake..."Hi, I'm your APPS" and the PCM says, "Well hello there, I'm certainly pleased to meet you"..."What did you say your name was again"? ...."Well, my name is APPS, and I'm zero ohms all the way up to five thousand ohms",...(you depressing the accelerator peddle)....the PCM says, "Oh yes...now I see your full name, I'm so glad we will be working together". The APPS is just a "volume control" it is a potentiometer ( called a "pot" electronic slang)...these controls are everywhere and we use them all the time. To look at this a little closer...it is a variable "resistance" and when we drive, on occasion, we must step on the peddle to accelerate or release the peddle to slow down. The PCM sees this change in resistance and calculates what we want. Now...let us review the basics. We showed the PCM what "zero" resistance was....yes? We showed the PCM what 5000 ohms looked like....yes? This is the "range" that the "handshake" (calibration) wishes to see between these two gentleman (APPS talking to the PCM). Now...let us throw a little garbage into the mix...let's say a "bad diode" in a large (135 amp) alternator or perhaps a "poorly ground" frame of an alternator...or heck...let's make it really smelly garbage, with both aspects...leaky diode and poor ground reference ! (It's stinky) Now...we have a poorly behaving "system". We all know this ! Now...let's refer to the "key" word here..."reference"....Ground reference...is ground! It was so important to teach (calibrate) our APPS to "talk to" the PCM and use the "language" that both would understand or agree to..."zero" to 5000 ohms...yes...they both "liked this" and they shake hands in agreement. (BTW...I'm just using zero to 5K as an example) it doesn't really matter. Now...with a poorly performing "power supply" (noise,ripple, bad grounds) and the introduced complications this brings to our poor and "misunderstanding" Mr.PCM ...he doesn't know what to do with this stinky (language) garbage. So...he starts do do some funny things! We all know this and we all dislike his humor. Now...let's go back to this "fix"...someone, somewhere with just enough knowledge to be dangerous decides this CTD problem needs a band-aid to fix the boo-boo. (Mike Nelson knew right away) We now know an electrolytic capacitor acts like a battery or filter ....yes? If you place this rather large (filter/battery) at the input of the PCM...it kills the stink (ripple). But...something new is now introduced...recall our efforts to calibrate the value between the APPS and the PCM? We wanted both of these guys to talk to one another and shake hands as friends. The starting point is "zero" or zero ohms that both could see eye-to-eye and fully agree as to what "ground reference" IS ! This new device in the circuit pathway is being "bump charged" by the ripple current...this positive charge is now being stored in the "electrostatic medium" (or battery) structure of the capacitor ( it's holding voltage) at a level that is supposed to be zero or ground reference! Now...Mr. APPS is standing on a chair above the floor (ground) and Mr. PCM can no longer look Mr. APPS in the eye...in fact Mr. PCM does not like this and starts doing funny things. Also, when you "snap" your throttle to rev the Cummins and release the throttle the instantaneous physical action is something we all experience...NOW with this "filter/battery" inline with the APPS and PCM...the electrolytic has a disturbing trait...he's kind of slow on the uptake and slow on the "i'm done now" performance. You know...the poor kid who always got picked last on the flag-football team back in 5th grade because he was to slow to carry the ball?...and when the whistle blew at the end of the play he refused to give the ball back to the coach? Nobody wanted this guy on the team...sorry...I think I was that guy. When you watch a movie on satellite TV...have you seen that funny thing where the voice doesn't match up with the moving lips of the actor? This "latency" is an example of what an electrolytic capacitor does in a circuit...yes they are used in correctly designed circuits that require the properties of an electrolytic capacitor...they do NOT belong in the conversation between Mr. APPS and Mr. PCM. Who ever elected to implement this into this "circuit", introduced many other issues. The time it takes to calibrate an APPS and then perform the handshake with the PCM is fully void when you drop bulk capacitance into this equation. We do not need this here. For all who have installed "filters" to correct TC lock/unlock issues, I would encourage a review of this decision. Bottom line...fix your power supply first. Cheers,
-
High amp alternator
@notlimahThe AGM's I'm using are Optima but, there are other band names available. The Red Top Optima is what I selected because of the cost factor. The real "high end" AGM's featured in the audio world are extremely robust and investment at that level was beyond my requirements. My primary reason for AGM is only to avoid the slow lingering corrosive out-gassing that is prevalent with wet lead acid packages. AMG's gas too but, at extremely low levels and if you experience profuse gassing from an AGM package there is real issues in the charging system. @outlaw7 would have experience with AGM plaftorm selection due to his background in high-current,demand, audio systems. Oh... and yes Garet...wow...your efforts and extreme fortitude in that project is off the hook ! Perhaps I missed it but, I must ask ?...did you address the "ground" regarding the four blk/tan wires "glue spliced" in the harness at the front of the engine? This is the ground lead (#8 blk/tan) that is connected to the passenger side battery tray. I'm very concerned about that particular aspect. The method Dodge implemented with this ground assembly and routing, is in my opinion, a real error. @dripley this "ground" assembly I'm referring to is something you should look at...you're going to truly dislike the procedure if you elect to do so but, knowing about your long term telemetry observations I think it would be prudent to invest the effort. I'm going back out in the garage to continue with this project...@outlaw7 is out pacing me by miles.
-
High amp alternator
@dripley Good evening Sir...I certainly hope I'm not becoming a major annoyance on this site...I'm here for the brotherhood of Cummins Turbo Diesel enthusiasts I understand your concerns...may I suggest in your service disciplines that grounds should be a first step...I know I sound like beating a dead horse here but, it's extremely important. Secondly, any time the service requires removing a "connector" whether it's under the dash or in the engine bay sometimes just the action of unplugging and reconnecting does some good but, for outright service a shot of Kegg product is real magic.This is the only product I use on large connectors or delicate component service. It is not "just another ******" product. Chemically this product is the only stuff NASA and high end manufacturers utilize as a standard. It will actually enhance connections. I use it sparingly and any connector I remove for any reason gets an injection of this liquid. Over time compounds in dust and airborne matter eventually causes errors on small signal contact points...the electrical flow on telemetry devices is extremely small and any debris at the contact points can cause erratic or unreliable, intermittent readings. This product is produced by Kegg Industries and is available through several suppliers...I obtain mine from Mouser Electronics or Digi Key...only high end electronic facilities would have this....Oh...I forgot, Fry's electronics,would have this. It's a bit pricey but, used correctly a can like this will last years. This can is 3 years old and I still have 1/3 fill available. BTW the push button top control, has adjustable flow control for frugality. I too do not wish to get started off subject but, I do not have lead acid batteries under the hood of my truck. I use AGM platforms only and avoid the gassing effect. Vehicles at ten years of age who have lived with a fart-cloud of sulfuric acid fumes under the hood require high-end maintenance disciplines to alleviate the unseen cancer of electronic corrosion. Sorry...I didn't wish to go off the rails here...lead acid batteries and Fred Flintstone cars get along quite well.
-
High amp alternator
@outlaw7Wow...Garet, I'm not sure of the reason you have delved so profusely into removal of these multiple harness assemblies. I certainly applaud your diligence and if there is an error in your control or instrumentation then bravo to your detailed focus. This segment (page) of this running thread...I only wished to bring attention to the horrendous "sub-Master ground" regarding the black/tan #8 wire (previous photo) where four (smaller) black/tan wires are "poorly spliced" and my experience leads me to strongly suggest a correction of this particular ( and supposedly important) multi-lead ground. Your disassembly does cause me to pause and question the validity of your efforts? None the less, since your "surgical" removal of these harnesses.... I would like to call attention to an assembly nuance that may elude understanding and also possibly stop a fellow enthusiast from altering the assembly technique. I call your attention to this photo depicting the "water temperature sensor lead"...this particular lead is contained within the harness that runs across the front of the engine. Yes, I too am involved with disassembly of this harness but, not quite to the level Garet has taken this.The reason I wish to bring this to everyone's attention is because, this "pair" of sensor wires are "twisted" together. This sensor lead is only one pair of multiple leads within this rather larger harness... that IS "assembled" or "twisted" in this fashion. This harness also contains the #6 B+ charge wire that runs to the PDC (alternator Hot lead) and of course the "focus" #8 black/tan (sub-Master ground) run returning to the passenger side negative battery terminal. I'm not trying to make a mountain out of a mole hill but, this "twisted" preparation of the water temperature sensor has meaning from an electrical stand point. It is common practice in "point to point" wiring within chassis assemblies where multiple wire runs are are all confined to a particular location within the chassis confinement area. This holds true with "harness" assemblies that we see within our CTD's engine bay compartment. The practice of "twisting" a particular pair of wires in an assembly where "other" wires are in close proximity to one another is actually done to reject "interference" or "confine" the "electrical charge field" to the "twisted pair". (am I killing you guys yet)? Let me explain...this twisted-method is a poor mans way of providing isolation between "signal carrying" wires where the assembly has "no choice" of location. Any time you run two electrical wires that carry electrical charge in close proximity there is an "interaction" between the two wires due to the "EMF" electromagnetic force or electromagnet "charge" of the near by wire(s)...this is a subtle but, a real phenomena that occasionally causes issues. Some of the wires in this particular harness are "low voltage/current" pairs, the B+ charge lead from the alternator to the PDC is a large current conductive element and of course the "messed up" multi-ground" black/tan #8 running "bass-akwards" is also in the mix. I found this interesting when I disassembled this harness to remove the B+ line ( my original focus) when I discovered this water-temp sensor lead to be "dressed out" in this fashion. I had to smile to myself with the fleeting thought, that Daimler/Chrysler might have a "real" Electronic Engineer on staff. (Just kidding...I'm being disrespectful)...they have such people. (my apologies) The art of "twisting" a pair is beneficial for "all confined" pairs. Any of you sporting "CB radios" ...the antenna line is "coax"... this is a self contained unbalanced "shielded" line. I am not suggesting that everyone tear the harnesses apart and install "coax" or shielded lines on every pair. This would be unthinkable.... I'm thinking of you Garet @outlaw7 (just funnin)...the use of "concentric line" known as coax today, is an ideal way of fully containing or promoting "isolation properties" of sensitive signal lines. We need not go overboard here...however; if a fellow enthusiast were to delve so deeply into a harness with multiple pairs and reassembly "allowed" such a procedure on any sensor line...then do so. By twisting standard insulated wires you are creating a self-protective phase reversal of the line itself...it has a natural physical property where an outside interfering "spike", "static", or "RF" (radio frequency) source is permeating the confined area where the wire runs lay. This is again the "poor mans" way of providing some isolation characteristics without busting the bank. Is it perfect....no, but, this method does provide a minor amount of "rejection" or "confinement" and is considered prudent. It is better than nothing! You needn't twist to tight...and depending on size (wire Gage) 5 or 6 turns per inch is ample. It is too bad that due to budget, during assembly, of the massive harness structures occupying the engine bay, that this old-school method was not implemented....or perhaps it was... when a "test scenario" was executed and the engineering staff suggested preparing the "water temperature sensor" lead to be subject? I know from experience that running small signal lines near "massive" B+ lines" can create insidious consequences and logical "best practice" wiring geography is a must aspect to consider or....perhaps rethink? I share this topic with respect to technical excellence and the development of a better understanding. Cheers,
-
High amp alternator
Good morning, Guys...I do not wish to distort the desires of any technician that wishes to have an instrument for careful measurement of electrical parameters. The art of high current measurement is really very simple and inexpensive. All high current measurement is done with a 100 or 50 milliamp meter. These are what Radio Shack sold for $4.98....NOW the key to using a little meter like this is to install a "high current shunt" in "series" with the high current line to be measured. You then connect the meter in "parallel" at the "shunt" connections. This photo shows the two screws where you make your meter connections. The major amount of electrons ( minus forces) race through the "shunt" unimpeded...the little side "pick off point" provides a calibrated amount of current to deflect your tiny mV (millivolt) meter accurately. Calibrated "shunts" are available for $17 to $27 dollars...nice meters are $7 dollars. No one in their right mind would plump #0 Gage wire into their dashboards to read hundreds of "Amps" on a meter face...that's insane ! Besides...every meter you view is a cheap little 50 or 100 mV (millivolt meter) shunted by a pricey calibrated shunt. The photo depicts a 200 Amp shunt that would drive a little 50 mV meter to full deflection. The meter can be in a remote location for viewing and the "shunt" does the "grunt work" while you run a couple of #14 Gage tickle wires to the meter....simple...clean and safe. Cheers,
-
High amp alternator
I just had to do this...and I did expect to see this. Sorry for this size of the file Mike...I used my iPad on macro for close view. This IS the Master Ground (?) of the large conduit from the harness passing in front of the engine on it's way to the "three connectors" with the first at the battery tray on the passenger side.I did careful surgery here to peel back the high quality shrink tubing that was extremely difficult due to the seal/adhesive compound that was used to encapsulate this assembly prior to heat shrink application. NOTE: the four smaller black/tan ground wires are merely "stuffed" into the #8 Gage black/tan ground wire. NO CRIMP, NO SOLDER and NO TWIST...this is the factory assembly "glued together" and heat shrink to hide the sin. Mike...I think you told me this contains the primary ground for the VP44 electronics? None the less...this is NOT how to splice any wire(s) in any application. If this is a true identification of a VP44 lead that is supposed to be at ground, I'm very glad I took the time to inspect this. I will not take credit for this discovery as I did read about this on another web site. There was no photo so...here is my contribution. This is NOT funny guys...when you discover how to access this mess for correction you will NOT be happy. I believe this electronic error to be as important as the "Killer Dowel Pin" for the second Gen CTD's. If you don't inspect this assembly and provide the service required, it would be highly questionable. Sorry to bare this bad news but, I've disassembled the entire electrical conduit assembly on the front of my engine...it's quite challenging. I am very confident in the worthiness of my efforts to eliminate the possibility of poor continuity. I need some sleep... Cheers
-
High amp alternator
Additional grounding of any mobile, nautical or aircraft is a standard. Most civilian vehicles are produced with bare minimum efforts (budget) but, usually just enough to get by. As time advances all structures that have mobility will develop a loss of electrical continuity especially if it was produced for civilian use. It's difficult to get near or approach a jet black Chevy Suburban with CIA employees commanding the vehicle but, if you could....a close inspection would reveal exceptional electronic communication and data platforms within. A closer examination would reveal exceptional platform preparation done by real electronic black-op technicians who know how to prepare for extreme compromise conditions and having a vehicular failure electronically does not happen. DC continuity of all vehicles does not make specification with only minimal design. Bonding an entire vehicle takes time and effort. ($) The standard common vehicles seen on the road, driven by the average person....goes to work, goes to the store, goes to school and comes home. The vehicle is just the everyday "Joe" device. Now let's put a 130 Amp alternator into this and all electronic aspects become more important. As @JAG1wrote "quoting" Ohms Law...14 volts X 190 Amps = 2660 Watts of power....this amount of power being dissipated is EXCEPTIONAL ! Yes...there are little foo-foo cars with 100 Amp alternators and ZO-6 Corvettes are very cool but, they do not sink 190 Amps at a single meal. The grids of the Cummins platform require above average DC supplies. The starter in the Corvettes and the Prius do require considerable current to start the engines. Once running, it's pretty easy....Now a Cummins 5.9 is a bit different, it requires 700 Amps just to run the starter on a cold day. The grids, depending on temperature, have a cycle rate.... Mike...I know you have a better experience with this than I do because of the temperatures where you reside. The time it takes for an old 1960's something with a 55 Amp alternator to develop ground issues, due to current-flow aggravating electrolysis degradation at "contact points" is not even in the same ball park with 130 Amp generators and moments during a cold winter where grid heaters sinking 190 Amps is a reality! These CTD's are real diesel "flame throwers" when it comes to WATTS going on. (I'm trying to be clever) If someone took some needle-nose pliers and precisely inserted the tool into a 120 volt wall socket in the kitchen...I think that would get everyone's attention. Pretty dumb thing to do...yes? Now...this event would only be exciting for a fraction of a second and the circuit-breaker in the house breaker panel will open. Now...this is not something anyone does with a sound mind....yes? OK...we are dealing with Bart Simpson...this little unruly hooligan does it AGAIN ! Now...I think it is time for your guest to leave the house and go home....yes? Now...let us do the math... OHMS LAW front and center: 120 volts x 20 Amps (circuit breaker) = 2400 watts ! So...it's "hair raising" when Bart Simpson sticks a needle nose pliers into the wall out-let in the kitchen.... But....it's NO BIG DEAL when our vehicles sink 190 Amps at 14 volts....let me see which event is transferring more electrons....Holly BajeeBers....the CTD wins ! @2600 WATTS So....I would encourage all interested enthusiasts to examine the standards of Power...the CTD's are very authoritative platforms....it is our "weapon of choice"...they are not for the average "Joe" and require some added diligence on our behalf. Needle nose pliers....test with a VOM...looks like a dead-short to me....my VOM only goes down to .2 Ohms and a dead-short is less than that....yes? VOM at grid terminals on any CTD ....WOW looks like a dead short...but let's do the math. OK lets's say 14 volts (we know that's close) and we know the total current demand is 190 Amps....yes? OHMS LAW to the rescue : R= Voltage/Current....R= Voltage (divided by) Current 14 volts / 190 Amps = 0.0736842 Ohms I think that is very close to a dead short...it is below what your VOM can read....yes? You need a Wheatstone Bridge to read small amounts of resistance. But, if we have two values, we can do the math for the unknown. Electronics 101 So....on a cold day....I think I'm going to go stick a needle-nose pliers into the socket...and it's so fun I think I'll do it more than once...in fact I'm going to do this every winter, 6 days a week for 14 years...oh don't worry my 130 amp alternator will handle this along with my storage batteries. By the way....my wife says Bart can't come over anymore...he is not allowed. She thinks he's going to burn our house down. Tongue in cheek...presentation, with great respect to all. Cheers,
-
High amp alternator
@Dieselfuture No...this is NOT a ground loop. You have done the correct procedure...this is known as "bonding" and is standard Military procedure for "hardening the electronic platform". Any dissimilarity in the intrinsic DC resistance between body, body panels, frame and hood should be eliminated by "bonding" with sufficiently gauged wire or strap. This silences all noise from an electrical standpoint and creates an electrical platform with uniformity. All Military platforms are bonded to extreme levels of efficiency. My compliments to your disciplines of electrical integrity !
-
Newb from Colorado
Welcome aboard...that is a very nice looking truck, the front bumper blends very well.
-
High amp alternator
@notlimah...yes DC Power Engineering produces this to maintain factory aspects of mounting the alternator and using the factory serpentine belt. Again, this alternator is superior in design to all other manufactured devices. My purpose is: 1) Eliminate the TC lock and unlock issue ( due to out of spec AC component from the factory Denso). The small AC ripple from all alternators is "smoothed" by the battery(s) however; time takes the toll on the grounding integrity of the entire system. 2) Provide additional current on demand when needed. ( I operate some high demand current devices) @outlaw7 The method of providing additional "filtering" is not without merit however; the parallel batteries have great capacitance to dampen slow or moderate AC excursions due to poor DC rectification issues. Large wet cell batteries do an excellent job of "filtering" but, it occasionally is not enough. The primary inspection must begin at the generating source and then follow the path of filtering (smoothing) to achieve the results of "clean DC". In working with "audio" I'm sure you're well versed with "cross over networks" where the audio content is directed to specific speakers. The cross-over is "frequency" specific for certain segments of the desired audio spectrum. In building the cross over network you choose a component structure that "passes" bass but, is not electrically sympathetic or conducive to pass the "audio energy" from a high frequency treble instrument. Following this example in your knowledge base of audio lends well to this subject matter. The AC component that cause the TC lock and unlock syndrome is a "higher frequency" excursion. Where the activation of the headlight switch to provide current flow is a "slow" human function of activating the switch. This one time action is causing current to flow but, the "initial turn on" IS, the fractional moment when the system is taxed for only a single momentary event. No problem...that small "spike" was absorbed by the eminence capacity of our large storage batteries....and if all is well the headlights are illuminating the road before us. Now...knowing the clock-speed from the PCU...that is controlling the the torque converter... is a "pulse-width-modulated" DC square-wave. This wave form is turning on and off at a very fast speed compared to a human turning on a light switch. How fast is it...?...I don't know but, let us say it's perhaps 120 KHz (on and off 120,000 times a second) this of course,is way faster than a human could turn on and off a headlight switch. Now...audio is relatively slow compared to the control pulses emanating from within the computer control of our trucks and when you select capacitors for the "low frequency" path of the cross over network you would choose components that have the capacitive reactance or to "favor" the lower ( or bass ) signals. The batteries in our trucks act as very "large capacitors" ...I do not want to say "Farads" but, this could be used to correlate a comparison. The "problem" is the interfering AC ripple that is combing with the PCU's primary "clock" and causing the torque converter to lock and unlock is an unwanted high frequency signal. To dampen or eliminate this "interfering" signal much smaller capacitence values would be the key. Adding "Farads" will not help this situation...adding micro-farads may very well help. The parallel batteries ARE our "low frequency" filters or perhaps a better unscientific term "big slow "reactive" garbage cans". @Mopar1973Manhas reiterated this many times...the truck was fine for so many years... what happened? His research took us all, to the "source" of this unwanted noise. Yes, the alternator is the generating source and the diodes aging, tough environment to endure, good grounds that have deteriorated over time, extreme current demands (grids) at intermittent moments. All of these contribute to a small error...the small AC ripple component is really no big deal...now, let's put a large #6 wire on the alternator's output B+ post...for giggles...let's make this wire 5 feet long and direct this "antenna" into plastic conduit containing other small "signal" sensor wires...direct the physical path of this #6 B+ charge wire, all the way across the front of the engine compartment and terminate this "antenna" into the Master Power Distribution Center with NO by-passing or attention to "possible" extraneous and unwanted noise (ripple) that might occur at some point in time? Bottom line by Mike Nelson...excessive AC ripple is the problem, period ! While we are at it (commencing in a parade of electronic buffoonery) let us take four rather key ground wires (all within this "front engine conduit") splice these four and connect them to a black/tan stripe #8 and run this back across the front of the engine compartment stopping to couple and uncouple THREE times in very nice connectors only to finally terminate at the PCU. All standards for "DC Ground"...you shall run the lead as short as possible and terminate with integrity. Note...the term "antenna" I am using this because a solid perfect DC line does not "radiate" a signal...an AC wave-form imposed onto a piece of wire does act as an antenna and will impose this signal onto and into any surrounding conductive structures. This AC wave-form ( ripple) has a fundamental frequency (3 phase rectification) with a spinning revolution of 700 RPM...1400 RPM or 2000 RPM....??? The frequency varies with condition....this frequency is high in nature...the PCU's clock (oscillator) is high in nature...it is the imposed mathematical equation of two fundamental frequencies "mixing" together as a product. The PCU can not differentiate the correct signal once an interfering extraneous source enters the equation. You and I experience a transmission with bad manors. Again, grounding with "integrity" with as "short" leads as possible and DO NOT CREATE GROUND LOOPS. You must maintain a single central primary ground source that all grounds will reference to. If your generator has the potential to produce high current (anything over 90 Amps) the stakes are now elevated to arc-welder status and your disciplines must be keen. These CTD's were produced reasonably and for the most part serve well with competent maintenance. The engineers who planned this out are exceptional individuals... from a standpoint of "what if" we have a little "ripple" on our B+ line...what would happen? They all confirmed that most likely there would be NO issue. These are civilian motor vehicles...we need not worry about subtle errors...they will correct themselves. Viewing the outright grievous errors in basic "DC 101" theory...I give these men a D- as for all else...I love this truck. After 18 years of service it is excellent however; I'm going to correct these small errors and with the help of the members on this web site, I believe things will only get better. Sorry...I've seen many questions semi directed my way and I'm trying to catch up...my apologies...I'll continue to address this as time goes forward. As I close out for now...build your Power Supply with the integrity that you expect from the circuits that demand current. A poorly designed power supply will plague all else that you prize. A well built power supply provides years and years of trouble free service....if it is built marginally than all else is marginalized.
-
High amp alternator
Good Morning @JAG1hey brother don't bother with connectors...if you can work directly at the point of connection just solder them and shrink wrap each connection. A large piece of shrink to encapsulate your surgery when complete will suffice nicely. Boy...you started this and a good deed never goes unpunished ! I'm glad you found all of this and YES...it snowballed but, finding all of this will return good measure. With @Mopar1973Manlooking into the discreet components at the control level perhaps the full circle will prevent these catastrophic failures we have all seen over the years. There is back-EMF in several key locations and in time this can prove to be harmful. Now if @IBMobile would chime in and bless our findings and procedures perhaps I could view the Super Bowl in good graces. Oh...your soldering gun...break the little nuts loose that hold the "hair-pin" element to the posts and re-tighten ...you have debris at the connection and it's preventing current flow. Cheers...I'm going back out to the lab and continue the saga
-
High amp alternator
Oh Gosh...your right...I forgot about the "Bafoonery" factor !
-
High amp alternator
The extra B+ charge line is very good. As a parallel lead this will help lower the resistance of the factory #6 in the system. Now as for the 140 Amp fuse in the PDC...that fuse is for the entire system and there is no accumulation of more than a 140 amp demand. The engineer that selected this also knew they were providing an alternator that can only provide 130 Amps so,the method they chose is fine. Now if you upgrade current supply and you feed that factory input at the PDC as designed you will defeat the design of the new power supply generating device. Hence, when you have the Grid Heater trigger demand the grunt of the new power supply (big honkin alternator) will blow your 140 Amp fuse because it is in series with the drivers side battery. The drivers side battery directly feed the Grid Heater relays...these relays are controlled but, the raw DC current at the relay contacts are directly from the battery. This system only replenishes the battery after the head-charge has been ripped off by the starter action and the continued demand of the Grid Heaters are now taxing the original design. With an upgraded "monster device" generating current your batteries are no longer being swamped and the alternator has less work to do in a shorter period of time. Better grounds by every method is BETTER !
-
High amp alternator
The DC Power Engineering company out of Riverside California produces their own products from scratch. Many other companies produce higher current devices all within the same frame of an original platform. Custom stator and rotor combinations will produce additional heat during operation and with the lack of "mass" and better internal cooling fans there could be a longevity issue. Also...note "square-wire" symmetry wound stators with no overlap on the field coils are superior transformer coils. The sinusoidal electromagnet fields cut the stator wires and induce currents at a much enhanced efficiency. Also....Note the "true Idle" spec's on these units...if the supplier tells you a new serpentine belt of a slightly longer length is required...spinning a small shaft at a much higher speed reveals a design difference. The DC Power Engineering design allows you to drop the alternator into place. The 270 XP does 305 Amps at redline...it's speck'ed at 270 normal run and reduced to 250 at above normal temperatures. It will produce 200 at idle with our 5.9's...gosh the Grid Heaters on a twenty degree morning...you won't see the headlights dim anymore. These beasts are bad to the bone ! You had best be sure your DC integrity is top notch...this thing will melt your truck !
-
High amp alternator
@notlimah...The 270 XP is large Frame to accept the robust Stator and companion 6 Phase rotor within the embodiment however; the CNC design engineer compiled the dimensions required and produced the platform to bolt directly into place with ZERO changes to the factory geometry for mounting. It's amazing what these 3D prototype printers are able to do today in creating a mock-up of a structure and be able to "expand" the dimensions within a target zone. Once done they feed the data into a CNC data logger and "mill-out" a solid metallic body from a billet piece. My company also produces assembly chassis's for our widgets and to observer the process is amazing. Clean...well I'm really anal and I do "doodle" under the hood with little rags and a squirt of oil. I approach maintenance clean-up the same way I clean weapons. I purchased this CTD new in 2001. The day I took delivery in Billings Montana at Billings Dodge I was out in the lot with the hood up. It was a blasted thunderstorm as the sales staff stood inside and watched the idiot (me) in the rain place fine mesh screen in front of the radiator/condenser-cooling structures to prevent bugs from plugging holes in the cooling units. I drove home and immediately removed that stupid puke bottle from the front of the engine and ran a "road-draft" tube straight down. There has never been an "oily shower mist" encapsulating the entire engine-bay compartment. That "blow-by" fog-syndrome poops all over everything including the cowl-seal where the hood meets the upper mantel of the firewall. This exit precisely deposits "oily film" on the front windshield and creates a never ending battle during rain events. It's also a constant visual detraction as I pilot this 7000 Lb device down the road...I really dislike a murky view through the front windshield. Most people who view this machine are astounded to find that it IS 17 years old with 154,000 miles on it. Yes...I'm a real A-hole ... at the local car shows...they let me in for free just because this thing is full-on-goon stupid ! I put mirrors under it at the shows to expose the extreme efforts to detail. BTW...Thank You. Again, Mike Nelson has a keen eye and has been pouring over this schematic for years...YOU are very right and it appears there is NO "back pulse EMF" protection on the Grid Heater relays. Boy...where is @IBMobileat this time ? He has documented several times on the procedure and merit of such disciplines...it is standard protocol in all electronic design to prevent transients from collapsing field-coil inductive currents.This is a generic example of what is at hand. Any time a DC current passes through a coil of wire there is an expansion of electromagnetic energy surround the coil. This is a normal property of a coil. Now...the problem ocures when the current is turned off. The electromagnetic field collapses back into the coil itself and creates a strong "back-pulse" of "opposite" polarity ! Remember, the exciting current is most likely 12 volts in potential however; depending on the "size" of the coil ( how many turns) or how many microhenries , this will determine how strong the potential of the collapsing electromagnet force. In simple terms...if you excite a coil at 12 volts, the collapsing force (back-EMF) will be MUCH larger in reverse polarity. The 12 volts input to the coil now becomes a 50 volt back-fart into your control device. This rouge reverse current will damage sensitive solid state devices and perhaps make your speedometer bounce wildly for just a moment as the field collapse dissipates. To prove this to your self, go find a relay...apply 9 volts from a transistor radio battery to the coil. You will hear the relay close (or operate) NOW...wet your finger and place it across the contacts where your 9 volt transistor battery is hooked up. Now disconnect the 9 volts while keeping your wet finger on the coil contacts.... Yeah Baby...can you hear me now! Ok...so this is another electronics 101... @Mopar1973Man has again located and identified an additional "danger" aspect in our CTD's...good eyes Mike ! With this small presentation...let's go fix this and prevent back-EMF damage.
-
High amp alternator
@JAG1 Good catch on additional information. After speaking with you on the phone today I believe we both started looking at this. Yes...Turbo Diesel Register member AKGriz has a 1999 3500 and his info is valid however; The production changed and my photo shows a little different evidence.This is my "2001" CTD and it appears after two years, the assembly procedure depicts full shrink-tubing and note.... the sealed ends. I'm not giving this a pass and I'm going to surgically open this up and inspect the wire to wire splice. Done correctly all four wires should be soldered to the #8 black/tan stripe that comes out of this large harness way over on the passenger side. Guys...I'm so sorry to become side tracked with additional issues and observations but, WHY in the world would an Engineer run nearly 38 inches of wire across the front of the engine, terminate this single #8 into a connector on the battery box, pick up this connection with a mated-connector that is another "splice" at the negative terminal of the passenger side battery and the "spliced" connector is then mated to an additional run of #10 that is a dedicated ground at the PCU ??? I'm astonished to see this. The four black wires...3 are #18 Gage... 1 is #14 Gage all are black with a lite Tan or off white stripe.Sorry...fuzzy...I'm using a small wrench to display the single #14 wire...the other three are #18 Gage. Here is the #8 Gage with the first set of connectors at the battery tray.Nice connectors but, this IS an additional maintenance point in the ground system. Here is the two #8 Gage wires "spliced" to a single "negative terminal" battery connector.Nice factory job...and this IS connected directly to the negative post connector/battery. Then...here is the #8 Gage connector engaging the final run of of #10 Gage to the PCU. Three connectors all dedicated as The PCU Master Ground and the final run of 20 inches is dropped to #10 at the mating connector. I guess is was budget Here is how I am going to do it. 1) I am removing the #6 Gage alternator B+ line from the large harness entirely. 2) The four grounds on the drivers side of the engine will terminate at the negative terminal of the drivers side battery directly. 3) One, and ONLY one #4 will be run from the negative terminal of the drivers side over the radiator and terminated directly at the negative terminal of the passenger side battery. 4) I will use the clean #8 Gage scrap and run directly from the PCU to the negative terminal on the passenger side. My method has superior integrity, additional "Mho's by using #4 to directly tie both negative terminals of the batteries. Directly bring the integrity of the PCU's ground without the use of connectors and cleanup the appearance of the entire spaghetti-mess of a very poorly thought out grounding system. (who did this?) 5) The new alternator (XP-270 DC Power Engineering, of Riverside Ca) will have the B+ delivered directly to the passenger side positive terminal via #4 Gage silver welding cable with a total length of approximately 23 inches. The factory #0 Gage from the passenger to the drivers side has excellent "current squared/resistance loss" characteristics and will allow this DC presentation to be a true lossless "parallel" system. 6) The B+ DC to the PDC will remain with the factory #6 Gage and allow the factory 140 Amp fuse to remain as a "master fuse" for the fed system. This new "Large Frame 270 Amp alternator, 6 Phase" device could NOT be bolted in place for service with the factory B+ configuration. Also, with the factory B+ line and the "PCU Ground" lines having been removed from the large flexible conduit at the front of the engine...this is now reduced in size considerably and will now be just "sensor feeds" in a much smaller flex-conduit configuration. I do believe I will have alleviated the TQ converter "lock and unlock" syndrom and I can remove my tin-foil hat. The 270 XP key points: 6 Phase, Large CNC machined housing, Square-wire wound stator with no overlap, 200 amps at true idle. The finish work is excellentHair pins are epoxy dippedclose up view12 diodes 6 Phase and high performance alloyed heat sink. When the installation is complete I'll provide engine bay photos.