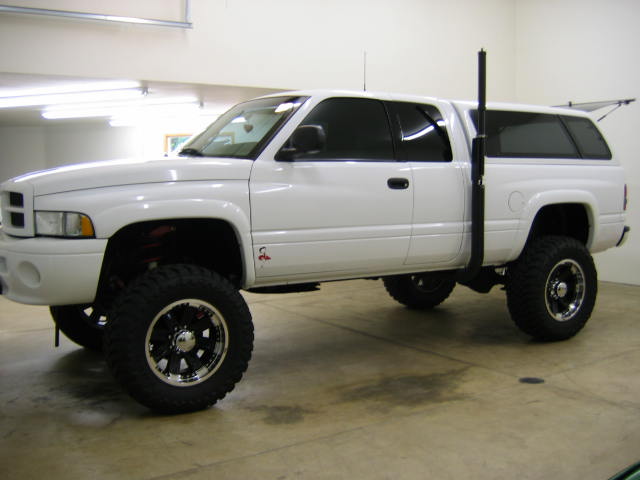
Everything posted by W-T
-
High amp alternator
@Dieselfuture Yes Sir, you are correct, multi pin weather-boot connectors should be dressed with Electronic Grade Silicon grease. It's a clean product and benefits small signal or low voltage contact points and your thoughts along corrosion prevention is spot on. The OX-Guard product commonly used in construction and house wiring especially where dissimilar wire/contact occurs. Examining OX-Guard in bright sunlight reveals a glistening shimmer in the grease structure. I would assume there is a conductive compound embedded in the "grease vehicle" and in a "connection" scenario of tightening a wire-nut, this would aid in promoting a conductive pathway. This is especially important in a "high current" path way where a poor connection would actually become "hot" due to undesired resistance. OX-Guard is only one compound that would serve well and I know there are other commercial products available, No-Lox comes to mind. Your observation of galvanic action at a contact point is direct evidence of a "hot spot" and your actions show excellent disciplines. These "power supplies" in our CTD's are very serious in nature...when we swing 14 Volts at 130 Amps, this is nearly a 2 Kilowatt arc welder in action. It is to be taken seriously with great respect.
-
High amp alternator
I must admit there are many keen minds pondering this subject matter and I'm almost afraid to continue on this path but, nothing worth while is easy. BTW...I'm still working so, when you note my absence or failure to respond, it is most likely that I'm out on the road. Yes, I have computer equipment but, it's all company issue and runs through the company servers in Minneapolis. I could dabble but, I prefer to be a low profile employee and keep my personal projects away from prying eyes in the office. Just a short refresher regarding the test instruments we are all using: The VOM (volt/ohm meter) is a must have for any observations in the basic electronics realm. These devices vary in performance and cost to obtain as a required tool. Many inexpensive devices work quite well and if you have the budget for a Fluke product do so. We do not need the $400 dollar laboratory unit and I'm using a $39 dollar digital device that is ample for my needs. The Fluke platforms do something very well and that is the ability to read complex or dirty wave-forms and provide exceptionally accurate measurements. This is important when we take measurements on DC lines and have the ability to switch the unit to "AC" and observe small saw-tooth or ripple riding on the DC line and see the actual value or level. Not all of us have or need oscilloscopes but, this was a standard for determining "exact" levels of AC wave-forms "peak to peak" prior to these solid-state handheld multi-meters. Mike Nelson and JAG1 have Fluke 77's and I'm envious....but, I'll get by for now. The reason I'm bringing this up is because for years Mike Nelson and Mike ONLY, was the first person I saw speaking of this subject matter on other web sites prior to the development of MoparMan1973.com and there are people out there today who recognize this issue and most "do know" it was MoparMan1973 who correctly identified the cause. I too was fooled for awhile and purchased "quick fix" filters and performed the "move the wires" out of the harness procedures touted by transmission rebuilding/performance facilities. No...I didn't fall into the "tin-foil" hat category but, almost... I do recall a time when my 2001 CTD didn't have the torque converter "lock & unlock" syndrome and when it became obvious to me that something was wrong...it bugged me. So here we are today pursuing answers and I must fall back on my basic electronic foundation and share what I know. Give me a moment...don't roll your eyes just yet...the subject of "ground" has been thrown around a great deal and I'm sure many are becoming tired of hearing about it but, let us look a little closer. Our "VOM's" can only see down to .2 Ohms at best. Some VOM's may show absolute "zero" when you touch both test leads together but, I highly doubt these modest (but good) test meters can actually measure "zero" Ohms. Further more, when you touch both leads together and observe your digital display as 000.2 what you are seeing is true. The VOM's ability to "read it's own inherent DC resistance".... in diesel garage terms... the VOM is sniffing it's own butt. This concept of understanding "your tool" is very important when we are searching for small level gremlins (DC resistance) that should not be present! The ability of a test instrument to measure extremely small levels of "pure DC resistance" has limits. Please note the term "pure resistance" is what we are talking about. The complex term "impedance" applies to complex AC wave-form angles and should not be used in this topic. Our trucks and DC power supplies are just straight DC resistance subjects and it's an easy path. I'll annoy all of you later and loose 90% of my readers if I were to go down the "impedance" path at this time. So...is there a way to read extremely small resistance values? Yes...with a Wheatstone Bridge you could measure less than a hundredth of 1 Ohm or less. Hold on...NO, we do not need to measure anything at this level. Now...let me present another way of viewing this basic electronic aspect that we call "resistance". Resistance is measured in Ohms and when it comes to "DC ground" the least amount of resistance is highly desirable ! Resistance is "resistance to current" flow...it is an undesirable aspect in "ground". The opposite (or reciprocal) of the term " Ohm " is the " Mho" (like Moe of the Three Stooges) this term, is to describe the " quality " of "conductance or acceptance " in the DC circuit or...in our case a better or enhanced DC ground. Earlier in this thread I believe we covered "electron" flow and this IS the conductive path we wish to correct. The factory alternator has been removed for this part of the presentation. The mount for the alternator is a magnificent piece of shaped steel ! This is the typical 2nd Gen structure and certainly has physical prowess. It also has a beautiful hardened black implement enamel paint job, from factory production. The Cummins staff certainly know how to mount a peripheral component with no physical compromise. Removing the high grade quality bolts began to show a possible electrical continuity issue.... I noted the minor rust signature deposited on the heavy black paint of this mounting plate. (poor conductive surface) I was alarmed when I extracted this "pivot through" bolt and observed pronounced electrolysis evidence at the threads. Note, the painted rust contaminated surface where this bolt terminated. Very large Ohms and very few Mhos The entire BODY of the alternator is Negative and MUST BE AT SOLID GROUND ! Upon removal of the mounting bracket...I became fully aware of the complete lack of DC continuity to ground. This view exposes the flat pivot-plate attached to the "hoist" head plate. Note the skirted bolts mounting this plate...the skirts are kissing paint ! With the bolts removed you can observe the unbroken paint divots where the bolt skirts kissed the surface. This view allows a clean view of "immaculate" bolt holes ! Wow someone knew electrical integrity was required here ! This clean bolt-hole appearance and the embossed "feet" of the cast pivot-mount, mating to this "hoist-plate" with "paint in tact" tells me the Daimler/Chrysler assembly line and pre-production crew lacked critical detailed information as to the reasoning of these cast and machined components in regard to electrical continuity. This next photo in hand is the pivot-plate...let me set it on the bench for a "rear-shot" photo of the protruding "feet".Again...beautiful protective paint application on this cast piece. Now...for the rear shot to observe the "protruding" feet that are precision "milled" to flat mount against the "hoist" plate.Note, the "milled" surface of these protruding feet snugly kiss the painted ( non surface prepared) "hoist" plate when mounted in place. This photo is the "two" structures that carry the full current (130+ Amps) at the "integrity" of Ground Reference !!!This is so disappointing to observe the "overlooked" aspects of electrical integrity...is it built well?... Oh Heck Yeah ! But, it doesn't have electrical properties...it has tremendous resistance ! The "body" of the alternator is "floating" above true ground !!! In any power supply, where the primary AC energy wave form is to be rectified (converted to DC) in a full wave bridge, the cathodes of the diodes MUST be at full chassis reference ground. Lifting a single diode's cathode or the entire bridge above true ground reference will induce large "ripple" currents. This disassembly procedure and individual examination at each contact point reveals extreme galvanic action created by the alternators ability to generate 130 plus Amps at 13.8 volts and more. Let's do the math on this...basic Ohms Law for Power is: P=E*I or Power equals voltage times current. 14 volts x 135 amps = 1,890 Watts .... impressive power generation and again the "bolts" and "mounting plates" are passing this electron flow when the alternator is spinning and there is a demand for this amount of current. When does this happen? Every time you start your engine and in the winter time, let's bring "grid" cycling into this equation. This poor little alternator is screaming it's guts out quite often. I neglected to mention heater/blower, heated seats ( I love mine ) windshield wipers, stereo sound system, headlights, running/fog lights....I left wench out because you should have your butt out of the vehicle if your using that device. Oh...hold on...this is going to get worse ! This next photo is a "review" of previous information regarding the VOM. Please note at the bottom of the photo you can see the two test-probes touching. This modest VOM floats between 000.2 and 000.1 Ohms in the "test" with both leads contacting one another. Again this Dodge was produced with some excellent components and physical integrity is not to be questioned. Even the selection of Grade 8 bolts and WOW !!! The brute force hooligans elected to provide black anodized coating to prevent rust and contribute to extreme longevity! Now that is so very cool ! NOT!!! Oh...hold on...anodized surfaces in the industrial world are great for rust resistance however; it now renders the treated component Non Conductive. I would like to know who the Einstein was who made this decision Check my probes out ! (I did not load this photo sideways) Note, the surface of the bolt was wiped clean and the test-probes are just sitting on the anodized surface. As you can see the display shows OL over-limit and this bolt is acting like a non conductive piece of dry wood. Nice ! Surface preparation is required on all assembly components and bracket surfaces. This was never done at the assembly plant and the "almost, kind of conductive paths" that "kind of sort of maybe worked a little bit" to get this Iron sold and off the car lot inventories and into the buyers hands....was just enough electrical integrity to do so. Afterwards the conductive aspects began to deteriorate....some were in the shop right away...some took years. Lets do the right thing...after all "we are building" our power supplies! Please see the next photo and NOTE, all surface preparation is done with BRASS wheels and Brass brushes. Never use steel wire wheels on dedicated conductive surfaces or assembly hardware. Using Brass is "magic" and during the procedure the molecular aspects of Brass will transfer to the steel surface and enhance electrical pathway properties. Steel is not a great conductor...yes it works but, we can't get physical strength from pure copper, silver is even better but, that's way expensive and Gold would be ludicrous...hey...check out my Gold alternator bracket... ain't I cool Use what ever it takes to remove paint but, once down to bare metal...treat it sweetly...a smooth clean, shinny, surface conducts best especially if you massage the steel with Brass. Look how my bolt passes current now ! Note, the contacting surfaces of this bolt including the "backside" of the skirt will make contact with the flat prepared surface of the alternator mounting bracket. The meter is floating between .3 and .4 Ohms but, pressing down on the probes with only slight physical force the meter will drop to .2 Ohms, simulating the "tighten'" into place during the alternator mounting procedure. Golly...this whole procedure is getting pretty sexy...and it's being done just to attract "electron flow"....or enhance electron flow that was never there to begin with...I think we had best start thinking about personal lubrication From here forward on heavy duty contact points and assemblies that carry "high current" electron flow... this will be the lube! I keep this in the night stand on my side of the bed. The small tube is my traveling companion...you never know when you'll have a wild connection that needs taming This lube is tenacious and stays put....it penetrates and promotes strong current paths....and maintains a cool connection. You do know my truck's name is Betty...Betty Boop,,,, and she just loves this. Surface preparation on the alternator bracket is featured here. This was slow careful work as I wish to maintain the factory appearance and avoid running a separate ground cable...that would suffice for a ground but, Betty wouldn't allow that. This photo depicts the method of removing non-conductive paint from "bolt holes" and YES...I'm using one of my brushes from the gun-cleaning kit. It is "Brass" and does a nice job of preparing the threaded hole. This was quick work with the drill driver. This was also performed on the "clean bolt holes" at the "hoist plate" location. I tried to get the light and contrast to reveal how well this brass brush prepared the threaded bolt holes.This alternator mounting bracket and the related bolts for assembly will certainly have corrected continuity for the new war-head installation. ( DC Power Engineering XP270 will be produce 200 Amps at idle when needed) Each bolt and flat-mating surface during the assembly will be dressed with OX-Guard. The product is common and available at any hardware store. It is the ONLY thing to use in this regard. Electronic Grade Silicon Grease is for highly sensitive electronics and weather-pack connectors where additional moisture incursion prevention is required. In high current situations such as this alternator subject, OX-Guard is superior. I use Q-Tips to apply this mascara in precision methods and avoid messes...once done...nobody knows she's all lubed up. There is so much more to address...please allow me some time and I'll complete this project. I know there will be questions...and I haven't really done anything yet. Well yeah...let's correct some errors and perhaps save some money and avoid another alternator...a real ground eliminates ripple. I'm going to get some sleep...Cheers
-
Alternator AC noise explain in detail
Mike is correct...the large current load on these 3 phase hairpin stators in conditions where all the available current is delivered does tax the design of the factory alternators. The diode's are all created on a single silicon substrate to assure uniform junction characteristics. This method allows for the PIV (peak inverse voltage) to closely match across all six diodes in a "three phase" rectified bridge. The old school would be to use individual large stud mounted diodes however; they would have to be curve traced to create a matched set of six diodes with close PIV and forward current avalanche voltage drops. All silicon diode junctions have a .6 volt drop turn-on when forward biased or conduction. Variations of these characteristics cause a dirty wave-form of the desired sinusoidal wave appearance. Hence; we have "ripple" witch is what Mike has explained so many times and why we must avoid this situation. Our trucks arrived with a "bare minimum" alternator design to get the vehicles off the sales lot. The grid heater configuration along with head lights and a fan blower for heat or defrost on early cold mornings takes the demand for these wimpy alternators to their design limits. Once we begin to "pound or beat" these diodes into forward and reverse current conduction we begin to see changes in the silicon junctions. It is cumulative and in time between hot summer and cold winter conditions our diode bridges become "leaky" and the "ripple" (AC component) becomes excessive and certain electric system devices begin to balk or react strangely with the imposed "ripple" floating on the DC(direct current) rail. Excellent mil-spec electronic devices or space-bound instruments MUST HAVE bullet proof power supplies. PURE DC hard-core power supplies are normal components and can be built without much effort today. Our alternators and dual batteries ARE the DC supplies for our trucks. The error is budget on Daimler/Chrysler's decision to put these 135 amp alternators into the Cummins platform. The standard rule of thumb for all electronic design regarding power supplies is, "If you have a demand of 100 amps maximum in a given system, you build a supply with 50% more headroom minimum. Now, take conditions into consideration...heat, cold and perhaps a poor matched battery in a dual battery (paralleled batteries) storage supply and the occasional "starter" operation (the Cummins starter is INSANE on current demand!) and WE have a real MONSTER to feed! Boys and Girls...if you want bullet-proof DC, double the available current at idle. Yes...this is correct...go with a 6 phase (twelve diode pack) and a hand-wound "square wire" hairpin-stator. The six-phase stator and companion rotor will cut the ripple to near zero in conjunction with proper storage capacity (really good paralleled batteries) you will have the power supply for your Cummins. The "square" wire wind is best for current demand when an "AC field wave-form" is cutting the coil to impose current into the inductive system. It is the cutting edge in design for transformers with high efficiency and LESS HEAT. Heat is "loss" and also destroys the surrounding aspects of the generating device. BTW...not even Nations builds to these specifications....they buy their upper-end higher current devices from a source in Riverside California. Just for grins... 1 Amp...what is this? Electronics 101: Current flow is "electrons" ( remember 5th grade science?) the Atom is composed of three elements the Proton, Neutron and the little Electron flying around the other two elements like an orbiting satellite. It is the "electron" we are interested in when it comes to DC (direct current) when we refer to "current flow" in a circuit. SO...the question is? When we measure "current flow" the term Amps is used....how many "electrons" flow through a piece of wire at a given point in "one second" ??? One Amp is (physics term "Coulomb" ) equals 1x10 to the eighteenth power....hence; when you start your mighty Cummins you are transferring 1x10x18 x 600 electrons in order to spin the Beast into run condition ! Take a look at the size of this number ! This is why you need "FAT" wire to allow all those little (minions) electrons to race at the speed of light through the wire to the given load. As you can see...current flow is from "negative" to "positive" in our world. The battery has a "positive" terminal and it is "sucking" to become satisfied. It attracts ("sucks") electrons off the frame-rail of your truck "as current flow" in order to spin the armature of the starter motor. SO..."negative" (electrons) flow towards the "positive" (hole or sucking-action)....seems we have an "upside down" world !!!! Now this leads us to another interesting Physics observation...you see...lights Do Not Give Off Light ! They suck "dark" and you will notice when a light bulb "burns out" and no longer provides luminescence....we say "it is burned out" however; we now know that is not true!.... IT IS FULL of Dark and we need a new bulb ...Look at the bulb...it's "dark". Sorry...had to share this funny tid-bit...none the less...our Cummins platforms were not produced with Mil-Spec in mind. Sorry, our ECM and PCM's must be provided "clean" stable DC in order to function correctly. The design guys never considered 6 millivolts of "ripple" to be critical for converter "lock and unlock" syndrome and yet we see the result and unwanted operational characteristics. I build killer DC power supplies for various electronic devices...you need a shop oscilloscope to even see the minor "AC ripple" and as for regulation, from zero to 100 Amps at 14.8 volts there is NO DC drop in voltage. It is like taking and engine from "zero" to "red line" in a heart-beat and you don't even see a fraction of a voltage drop...this is called a "Stiff DC Regulated Supply". Build your DC Supply...the Cummins platform is a Nobel Beast....feed it a good stiff DC diet with NO sag and Zero ripple and all will be well. ALSO...guys I lurk around out here...I've seen photos you have all taken "under the hood" of your beloved vehicles...gosh golly!!! The appearance of the battery terminals and cable connectors...it is pretty sad. You can't transfer billions and billions of electrons (with NO heat) through the scum I have viewed. Again...No worries...we are all in this together... I share this respectfully as intellectual content with just a touch of humor Cheers
-
High amp alternator
Mike is correct...the large current load on these 3 phase hairpin stators in conditions where all the available current is delivered does tax the design of the factory alternators. The diode's are all created on a single silicon substrate to assure uniform junction characteristics. This method allows for the PIV (peak inverse voltage) to closely match across all six diodes in a "three phase" rectified bridge. The old school would be to use individual large stud mounted diodes however; they would have to be curve traced to create a matched set of six diodes with close PIV and forward current avalanche voltage drops. All silicon diode junctions have a .6 volt drop turn-on when forward biased or conduction. Variations of these characteristics cause a dirty wave-form of the desired sinusoidal wave appearance. Hence; we have "ripple" witch is what Mike has explained so many times and why we must avoid this situation. Our trucks arrived with a "bare minimum" alternator design to get the vehicles off the sales lot. The grid heater configuration along with head lights and a fan blower for heat or defrost on early cold mornings takes the demand for these wimpy alternators to their design limits. Once we begin to "pound or beat" these diodes into forward and reverse current conduction we begin to see changes in the silicon junctions. It is cumulative and in time between hot summer and cold winter conditions our diode bridges become "leaky" and the "ripple" (AC component) becomes excessive and certain electric system devices begin to balk or react strangely with the imposed "ripple" floating on the DC(direct current) rail. Excellent mil-spec electronic devices or space-bound instruments MUST HAVE bullet proof power supplies. PURE DC hard-core power supplies are normal components and can be built without much effort today. Our alternators and dual batteries ARE the DC supplies for our trucks. The error is budget on Daimler/Chrysler's decision to put these 135 amp alternators into the Cummins platform. The standard rule of thumb for all electronic design regarding power supplies is, "If you have a demand of 100 amps maximum in a given system, you build a supply with 50% more headroom minimum. Now, take conditions into consideration...heat, cold and perhaps a poor matched battery in a dual battery (paralleled batteries) storage supply and the occasional "starter" operation (the Cummins starter is INSANE on current demand!) and WE have a real MONSTER to feed! Boys and Girls...if you want bullet-proof DC, double the available current at idle. Yes...this is correct...go with a 6 phase (twelve diode pack) and a hand-wound "square wire" hairpin-stator. The six-phase stator and companion rotor will cut the ripple to near zero in conjunction with proper storage capacity (really good paralleled batteries) you will have the power supply for your Cummins. The "square" wire wind is best for current demand when an "AC field wave-form" is cutting the coil to impose current into the inductive system. It is the cutting edge in design for transformers with high efficiency and LESS HEAT. Heat is "loss" and also destroys the surrounding aspects of the generating device. BTW...not even Nations builds to these specifications....they buy their upper-end higher current devices from a source in Riverside California. Just for grins... 1 Amp...what is this? Electronics 101: Current flow is "electrons" ( remember 5th grade science?) the Atom is composed of three elements the Proton, Neutron and the little Electron flying around the other two elements like an orbiting satellite. It is the "electron" we are interested in when it comes to DC (direct current) when we refer to "current flow" in a circuit. SO...the question is? When we measure "current flow" the term Amps is used....how many "electrons" flow through a piece of wire at a given point in "one second" ??? One Amp is (physics term "Coulomb" ) equals 1x10 to the eighteenth power....hence; when you start your mighty Cummins you are transferring 1x10x18 x 600 electrons in order to spin the Beast into run condition ! Take a look at the size of this number ! This is why you need "FAT" wire to allow all those little (minions) electrons to race at the speed of light through the wire to the given load. As you can see...current flow is from "negative" to "positive" in our world. The battery has a "positive" terminal and it is "sucking" to become satisfied. It attracts ("sucks") electrons off the frame-rail of your truck "as current flow" in order to spin the armature of the starter motor. SO..."negative" (electrons) flow towards the "positive" (hole or sucking-action)....seems we have an "upside down" world !!!! Now this leads us to another interesting Physics observation...you see...lights Do Not Give Off Light ! They suck "dark" and you will notice when a light bulb "burns out" and no longer provides luminescence....we say "it is burned out" however; we now know that is not true!.... IT IS FULL of Dark and we need a new bulb ...Look at the bulb...it's "dark". Sorry...had to share this funny tid-bit...none the less...our Cummins platforms were not produced with Mil-Spec in mind. Sorry, our ECM and PCM's must be provided "clean" stable DC in order to function correctly. The design guys never considered 6 millivolts of "ripple" to be critical for converter "lock and unlock" syndrome and yet we see the result and unwanted operational characteristics. I build killer DC power supplies for various electronic devices...you need a shop oscilloscope to even see the minor "AC ripple" and as for regulation, from zero to 100 Amps at 14.8 volts there is NO DC drop in voltage. It is like taking and engine from "zero" to "red line" in a heart-beat and you don't even see a fraction of a voltage drop...this is called a "Stiff DC Regulated Supply". Build your DC Supply...the Cummins platform is a Nobel Beast....feed it a good stiff DC diet with NO sag and Zero ripple and all will be well. ALSO...guys I lurk around out here...I've seen photos you have all taken "under the hood" of your beloved vehicles...gosh golly!!! The appearance of the battery terminals and cable connectors...it is pretty sad. You can't transfer billions and billions of electrons (with NO heat) through the scum I have viewed. Again...No worries...we are all in this together... I share this respectfully as intellectual content with just a touch of humor Cheers
-
Lund Roll Up Tonneau Cover
I too have been looking at the same idea. I removed my shell and my recent photos do not reveal this change but, I need to do something. Great addition Mike.
-
check engine light error codes P0113 and P1693
Hey Tim Access the board Pin out Molex connector looking at it straight on 8 7 6 5 X X X X X X X X this is the bottom of the board as you look at this connector 4 3 2 1 The switch OFF posistion check continuity at the following pins Pin 1 and 5 = 0 ohms Pin 2 and 3 = 0 0hms The switch in posistion 1 (MPG) Pin 1 and 4 = 2.2K Pin 2 and 3 = 0 ohms The switch in posistion 2 (6 cyl High Idle) Pin 1 and 4 = 39K Pin 2 and 4 = 3.3K The switch in posistion 3 (High Idle 3 cyl drop out) Pin 1 and 4 = 55K Pin 2 and 3 = 0 ohms If you do not see these values in any test posistion as noted above get some contact cleaner ****** your switch and hit it gently with compressed air to dry...then re-test as above and confirm the resistance values. Plug your control cable back into your board and remount into posistion. Grab your Smarty and clear your codes. Restart your CTD in posistion 2 and observe the ramp-up idle function. You should not see any codes appear and all will be normal. If NOT then you have harness continuity testing and or ECT or IAT out of spec's to review. I use Keg contact cleaner available from some Radio Shacks or Mouser and DigiKey carry it...it is the best product. Cheers, William
-
The time has come to produce the Mopar1973Man High Idle & MPG fooler switches again.
Hey Guys...received my switch assembly on Thursday and installed it yesterday afternoon. Very nice...and the quality build of this device is excellent. Each spring I dissable the Grid Heaters as they are not required in this climate...then come fall I forgot what I had done hence; the first cold morning where Grid Heaters would be nice, I must rehook my DC feed to the relays. With this excellent MOD, this aspect is no longer required by selecting the 1st step MPG posistion. Again Mike and the Administration of this site THANK YOU...
-
New member as of Nov 28 2016
Hey guys, Thanks for the warm welcome...I'm out on a business trip hence, I've not been able to respond. i attempted to fill out my signature however; I messed up and couldn't remove the oversized photo and kept making additional errors until I ran out of time. When I get home Friday I'll correct the buffoonery and show my truck. Mike, I was an avid member withTDR and made small contributions to the intellectual subject matter several years back and I believe we spoke on the phone once regarding ecm aspects but, it was some time ago. BTW...I should have joined many months ago but, when I saw the restocked high idle kits back in stock and knew I have up coming vacation time to tinker with my truck and the deal of getting a membership with an order I couldn't pass that up! Anyway...sorry for the delay and I'd better get back to the task at hand...I will continue to annoy all of you later? Cheers, William
-
New member as of Nov 28 2016
Hello all, I have been in the background reading for a long time...greetings from a fellow Cummins enthusiast. Thank You William