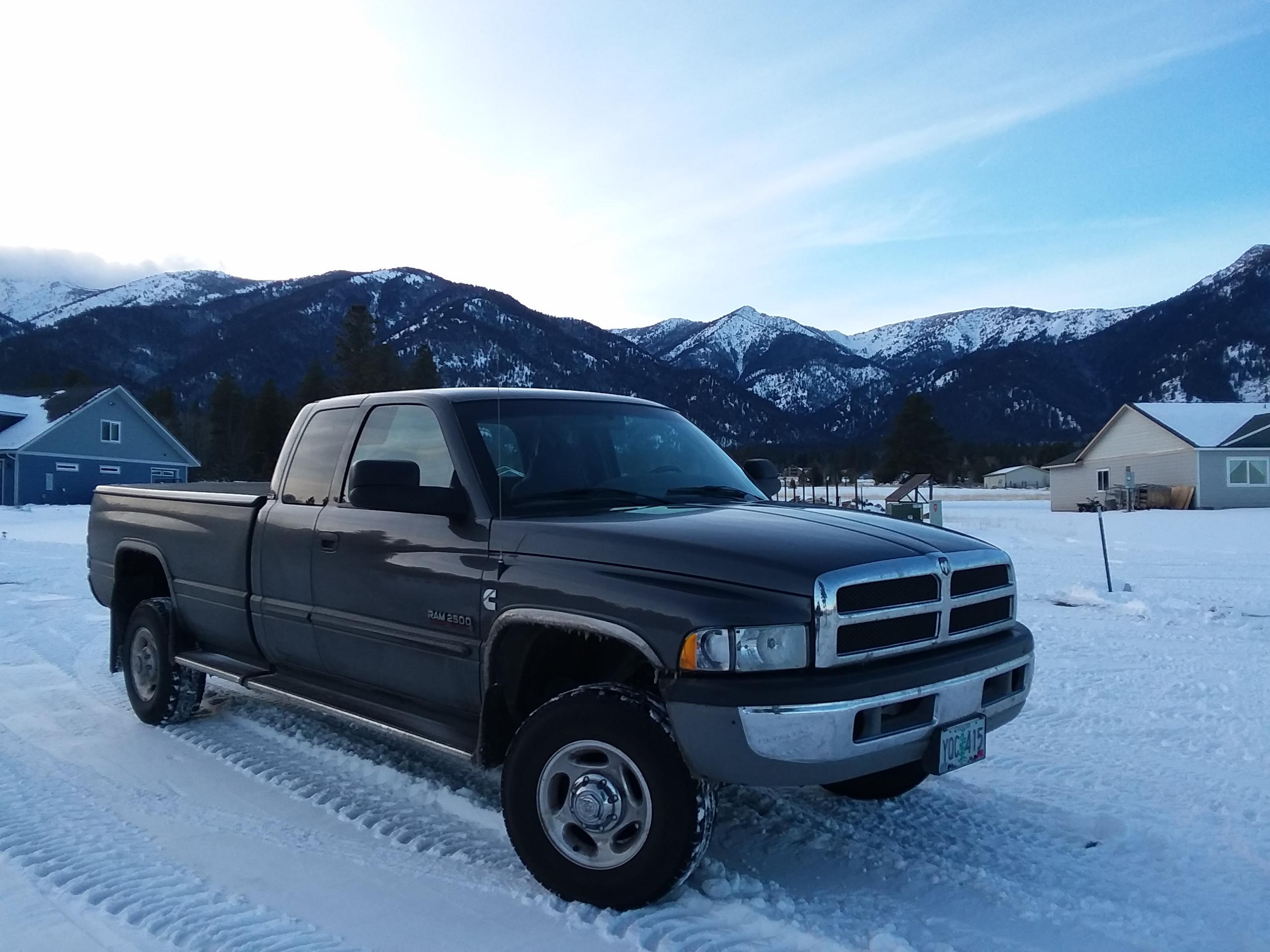
Everything posted by Tractorman
-
2000 Cummins Surge/Dead Pedal
In his first post he said that he installed new batteries last summer. - John
-
2000 Cummins Surge/Dead Pedal
Sounds like you have been thorough in taking care of things since you acquired the truck. Have you checked the conditions of all battery connections and frame / body wiring grounds? There is a wiring modification for the VP44 trucks that is called W-T ground reference wiring mod (by William Timothy Burke). The wiring modification addresses long wiring routes and poor ground connections for the PCM and the ECM. This wiring mod can reduce electrical interference in circuits joining computerized components. Here is a link to the W-T ground reference wiring mod: https://mopar1973man.com/cummins/articles.html/24-valve-2nd-generation_50/51_engine/electrical/ground-reference-vp44ecmpcmpdc-plus-tc-lockunlock-r567/?do=getLastComment&d=4&id=567 Also, check the mechanical low idle screw condition under the hood. You will have to remove the plastic throttle cover (if it is still there) to gain access. Another member posted similar symptoms as yours and it turned out to be the idle adjustment screw was loose allowing for irregular throttle positions at idle. - John
-
Bad wheel bearing or what?
I think I know what you are saying, but since there is an inner and outer bearing on each side, I would say it like this: When the vehicle is turned hard left, the inner bearing on the passenger side would have a lateral force placed against it while the outer bearing on the driver side would have a lateral force placed against it. I think that the left front wheel bearing should at least be taken apart and inspected. How many miles were / are on those front wheel bearings? - John
-
Bad wheel bearing or what?
Have you checked that the wheel lug nuts on both front wheels are tight? Also, have you checked the front wheels for any cracks? - John
-
P0216 and P0602 codes, intermittent loss of power, weird MAP reading
It's tough to have to do the job twice, but I'm glad to hear that DAP is taking care of you. - John
-
P0216 and P0602 codes, intermittent loss of power, weird MAP reading
Please let us know what DAP has to say. - John
-
P0216 and P0602 codes, intermittent loss of power, weird MAP reading
I recommend giving DAP a call and tell them what you have written here. The P0216 sounds like a timing failure and is likely to be internal to the VP44. From the FSM: P0216 (M) Fuel Injection Pump Timing Failure High fuel supply restriction, low fuel pressure or possible wrong or incorrectly installed pump keyway. Is your fuel pressure sensor located right at the VP44? If so, assuming that your reading of fuel pressure is steady, then you don't have a lift supply problem. - John
-
P0216 and P0602 codes, intermittent loss of power, weird MAP reading
Is your engine stock, or are using a tuner? I use a Smarty S03 and the 0602 code is normal (as stated by Smarty). The 0216 code does not sound good, especially with good lift pump pressure. Did the VP44 pump you bought from DAP use a remanufactured PSG or a new PSG (1 yr vs. 2 yr warranty)? You want to have a VP44 that has be run through a program on the Bosch 815 test stand - no exceptions. - John
-
Good amount of oil blew out of crank vent, freaking out
@YeaImDylan, how did the seal fail - leaking around the lip or seal pushed out? Also, did you check lift pump pressure with a mechanical gauge? What were the results? I seriously doubt there are any issues with the overflow valve. The overflow valve is of simple design and very reliable. The VP44 input shaft seal would only be exposed to lift pump pressure. Any fuel flow passing over the internal vane pump (also referred to as "feed pump") pressure regulating valve is returned directly to the suction side of the feed pump. The suction side of the feed pump is in common with fuel entering the VP44 from the lift pump. Those pressures would be equal. This is the pressure the shaft seal would see. - John
-
Good amount of oil blew out of crank vent, freaking out
So, are you saying the seal lip did not fail - the whole seal just got pushed out? - John
-
Good amount of oil blew out of crank vent, freaking out
If the engine idles smoothly and runs normally under load, I don't think the injectors would be the cause. Just curious - what is your lift pump pressure? - John
-
Good amount of oil blew out of crank vent, freaking out
You could do a quick check for engine blow-by using the bouncing oil cap method. Otherwise, I would just clean up the engine compartment, then start the engine and perform very short drives inspecting the engine compartment frequently for leaks, blow-by, etc. Doesn't sound good. - John
-
Front wheel hub
I don't have any recommendation, but Rock Auto usually has many choices ranging from economy to heavy duty parts. Just out of curiosity, how many miles on your truck. I would think that front wheel bearings on a two-wheel drive truck would last for a very long time - especially a truck with a manual transmission. Edit: Never mind my comment. I just looked up the part on Rock Auto and it appears that unit bearings are used. I thought they were the old style inner and outer bearing which would last forever. - John
-
Hunting at idle when in gear
I have been camping for the past few days, consequently I am giving a late response. The APPS is for the '98.5-'02 Cummins VP44 fueling system.
-
Hunting at idle when in gear
It appears that you have an OEM style APPS. It appears that there is a hand throttle connected to the throttle (in your photo). Make sure that the hand throttle is not interfering with the idle stop adjustment. The link below should help with checking the operation of the APPS. - John
-
Hunting at idle when in gear
I am assuming that you used a Mopar APPS to communicate with the a Cummins ECM for the era of engine you put into your F250. The idle validation switch is part of the APPS. When the throttle is released, the mechanical throttle stop should allow for the idle validation switch inside the APPS to be activated. This action removes all inputs to the ECM and allows only the ECM to maintain idle rpm. When you installed this engine and controls into your F250, did you use the ECM, PCM, APPS, etc. from a sacrificial Dodge Cummins truck? It is hard to offer help in your situation, mainly because I don't know how your conversion was done or what parts were involved. - John
-
Hunting at idle when in gear
Since you are getting several DTC's that are all over the map and your engine is not an OEM application, I would double check the integrity of all related wiring connections (both positive connections and ground connections) that you performed to make this conversion work. Also, make sure that the APPS home position at idle activates the idle validation switch. An engine idle stop that is mis-adjusted could provide some of the symptoms you mentioned. You could disconnect the APPS and check for smooth operation using an ohmmeter and also check the operation of the idle validation switch at the same time. - John
-
No Start problems
I would double check Pin #6 (ground) test. This test should produce a steady voltage. I would use a test lamp with an incandescent bulb, if possible. This will place a small electrical load on the circuit being tested. Pin #6 is connected to Splice #168 which splices into two ECM grounds and an engine block ground. Splice #168 has been know to be troublesome. So, try retesting Pin #7 to Pin #6 with a test lamp - ignition on for the first test, engine cranking for the second test. The lamp should dim slightly, but remain steady for the engine cranking test. If the test fails, then keep one lead of the test lamp on Pin #6 and connect the other lead to a battery positive post. Note the results of the test. Are there any DTC's stored? If so, knowing what they are could help with troubleshooting. Your high mileage injectors should be replaced. The injectors are not the cause of your no-start, but you have gotten a good service life from them - time to replace them. Using a multi-meter to check resistance at connectors is a common practice, but it has its limitation, i.e., a single strand of wire in multi-strand wiring maybe the only connection, which can falsely indicate that a circuit is good. This is why I use a test lamp whenever I can - to place a small electrical load on the circuit during the test. - John
-
Did i burn up my dimmer switch?
I use software called DesignCad 2018. It started out as Prodesign in 1985, when I first started using it. . i think the filament works as a resistor to limit the current draw. Still this set up causes a constant drain on the battery when truck is off because it is in fact shorting at the headlight bulb. There is no short to ground when the headlight switch is turned off and headlight beam selector switch set on low beam. It is just battery voltage potential with an incomplete path, so no current flows. - John
-
Did i burn up my dimmer switch?
I think you would be correct. Sounds like you will have a new relayed headlight system that you will be happy with, soon. The diagram below shows how I wired relays into the existing 2 headlight system when my truck was new. Later, I modified the diagram for a Sport headlight system. The numbers by the wiring represent wire gauge. Years ago, I lost my high beam indicator lamp - I always thought that it burned out, but now I am wondering if I sabotaged that circuit! - John
-
Did i burn up my dimmer switch?
I think that "someone" is correct, although I don't consider it to be a fault. The stray voltage is coming from the high beam bulb. That bulb is fed by Fuse #14 (10 amp from battery) in the PDC. That bulb is grounded when high beam is selected. When low beam is selected, the bulb is not grounded - hence, voltage is present at the RD/OR wire via Fuse #14 and the high beam indicator bulb. So, I think your OEM headlight circuit is working as it should. - John
-
Did i burn up my dimmer switch?
No judging at all - you have to use the tools that you have on hand. Appreciate you answering all the questions. Just double checking here - "bulb" is singular - both bulbs need to removed for the test, otherwise back-feeding will occur through the bulb filaments. Also, with your relay adapter harness removed, is the wiring harness now completely stock? This sounds like stray voltage to me. This can happen when a wire both ends of a wire a renot connected in a particular switching operation. It is one of the reasons that I use a test light with an incandescent lamp when testing these circuits. The imposed electrical load from the incandescent lamp eliminates stray voltage from the picture. Multi-meters will easily read any voltage present - even if it is stray and is not backed. The fact that the voltage disappeared when high beam was selected indicates the circuit is working - maybe not the best it could be, but it is working. The .5 voltage drop to ground when the high beam is activated sounds like a poor ground connection, but should not be causing you any problems. - John
-
Did i burn up my dimmer switch?
I am still not sure where you are getting Pin #1, #2, and #3 information from. Regardless, the wire colors you mention are for the right side headlight. I am going to use the FSM wiring diagram for reference. RIght side headlight: ** A - VT/RD - 15 amp hot fuse from PDC ** B - VT/WT - low beam wire to dimmer switch, then headlight switch, then to ground C - RD/OR - high beam wire to dimmer switch, then to ground Left side headlight is the same except that **A is VT and has a separate 15 amp hot fuse from the PDC. What does "everything" mean? - both headlight connectors? dimmer switch, headlight switch? Have the bulbs be removed? I would not use a power probe for testing. I would use a test light with and incandescent bulb. I would leave everything connected except for the left and right headlight connectors. Both connectors should have the 9004 bulbs removed. I would turn the headlights to the "ON" position and have the dimmer switch selected to low beams. **A - test lamp clamped to battery ground and test lamp probe connected to **A. Test lamp should light (power from 15 amp fuse). **B - test lamp clamped to battery positive post and test lamp probe connected to **B. Test lamp should light (ground through headlamp switch via dimmer switch). C - Activate high beam switch. Test lamp clamped to battery positive post and test lamp probe connected to C. Test lamp should light (ground through high beam selector switch. Just for general information (and maybe you already know this), but the headlight switching is all in the ground circuit. When the bulbs are removed, the only voltage that can be present is at terminal **A at both headlight connectors. The remaining terminals will be either open or grounded depending on position of switches. Hopefully, I have not made any errors - feel free to correct them if I did. - John
-
Did i burn up my dimmer switch?
I am a bit lost with your explanation. I don't see any of the terminal pin numbers that you refer to, so I don't know which connectors you a referring to. Also, the type of relay you are using (not part of the diagram below) isn't identified. The headlight wiring diagram below is for a 2002 Dodge Ram (probably the same for a 2001). The "double asterisk" by each headlight represents the connection to a "non Quad" headlight system. You will note that terminal "A" at each headlight is always hot via two separate 15 amp fuses in the PDC. Low beam is selected by grounding terminal "B" of the headlight via the multi-function switch and then the headlight switch. High beam is selected by grounding terminal "C" of the headlight via the multi-function switch. It will help if you show the type of relay that you are using so that the wiring can be understood easier. - John
-
Clutch burn question
The one thing that hasn't been mentioned in this topic is the "break in" procedure for high performance clutches, so I thought I would mention it. I just installed a South Bend 1947-OK-HD single disc organic clutch (450 hp/900 torque) in my truck. Required break-in instructed by South Bend is mostly city like driving with lots of starts and stops - empty truck, no full power for 500 miles. This results in the best holding power quality for the clutch and lasts for the life of the clutch. Any slipping of the clutch (after engagement) during break-in will reduce the holding torque of the clutch up to about 200 lb/ft - permanently. So, no matter which high performance clutch is used, the break-in procedure provided by the manufacturer should absolutely be followed. I just returned from a camping trip with my 19 ft travel travel - gross combined weight around 12,500 lbs. When I started the trip, I only had about 50 miles of city driving on the new clutch - nowhere near the 500 miles. I was very concerned about unintentionally slipping the clutch under load. I thought I had a lot of leeway because my truck only develops just over 600 lb/ft of torque - RV 275hp injectors and a mild Smarty S03 tune. I was wrong. It didn't slip climbing up long passes. It slipped when I pressed the cruise control resume switch at 60 mph with cruise set at 65 mph - definitely caught me by surprise. The engine raised about 200 rpm for less than 1/2 second. Hopefully, I haven't done any permanent damage. The return trip was uneventful, but I was a little more careful. So, whichever clutch you get, be sure to follow the break-in instructions. - John