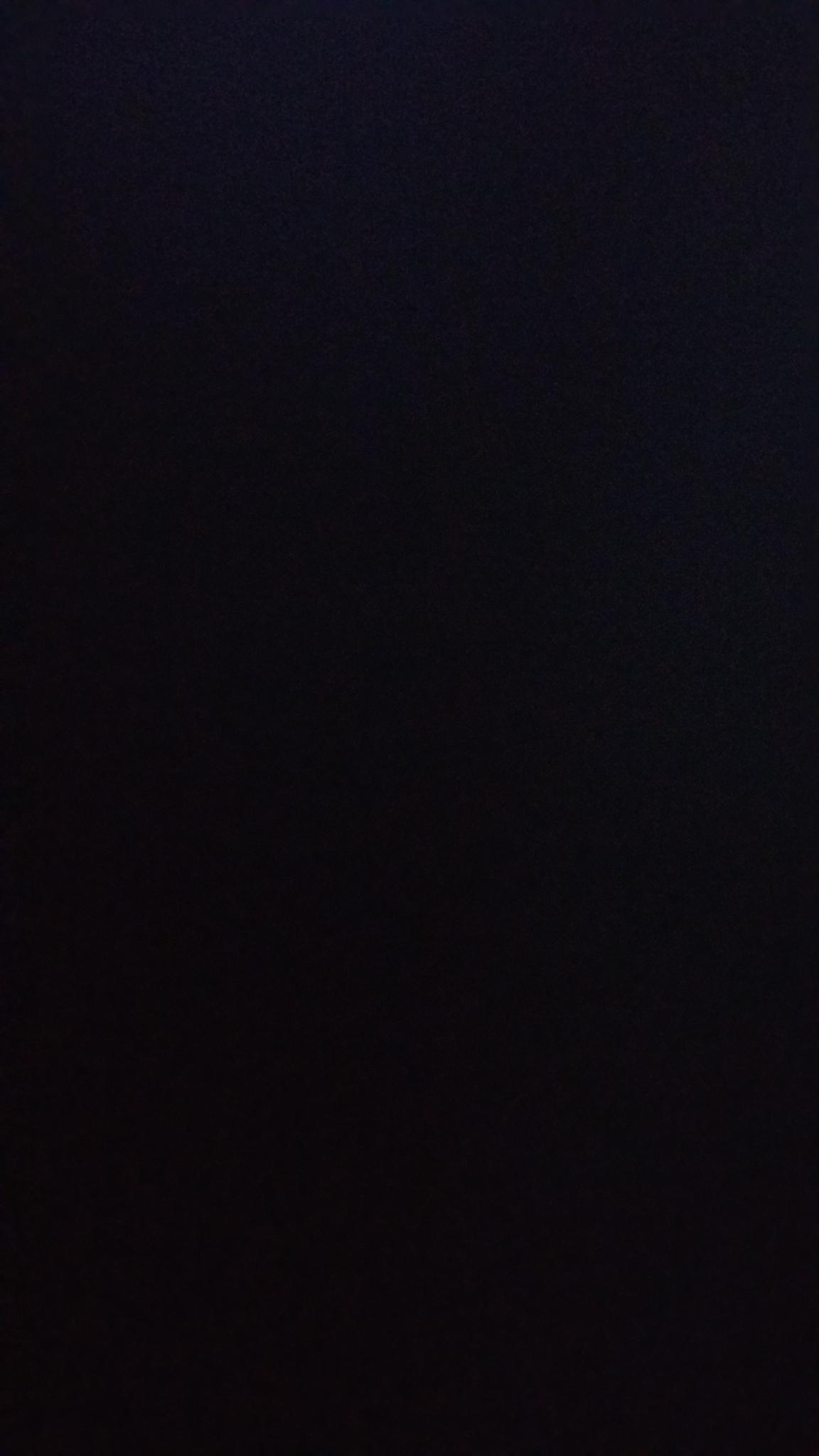
Everything posted by wh82
-
Truck randomly dies. Please help, pulling my hair out, and loosing sleep!
Thanks for the suggestion. That is one thing I noticed right after my injector swap is I had bumped one of those loose. I cleaned both of those with contact cleaner then blew them out with air... still having issues. I'm really curious about dripley's "cluster test" but it looks like that requires a scan tool. I too have seen CCD frequently on my overhead console. :| I really think this truck just wants to be retired :D
-
Truck randomly dies. Please help, pulling my hair out, and loosing sleep!
I'm with you, I hope it's not the ECM... Electronics are my thing but it's hard without access to FULL schematics, FULL software code and of course some nice scan tools. I just don't have any of that and am waiting on a friend who has the actual dodge scanners to have time for me. my WTS light always has worked through this... but the ECM cutting the lift pump randomly and then the truck surging back up and running without lift pressure at least kind of tells me the VP44 is strong still.. (not for long at this rate) ****, it drove my truck for at least 3 months when my original pump was dead when I purchased the truck and didn't know it prior to getting gauges back in the day... But now, keep cutting lift pressure and brand new strong injectors... that's when this all started.. I just took a look at your thread, very similar problems, completely overlooked it in my panic to get help. :| very odd, heat starts, both have similar issues... maybe the ECMs are melllllting, MELLLLLLTIINGGG...
-
Truck randomly dies. Please help, pulling my hair out, and loosing sleep!
😕 Did that when I installed the sensor...
-
Truck randomly dies. Please help, pulling my hair out, and loosing sleep!
Got the Timbo APPS installed (also removed the AC filter (Capacitor) from the line to the PCM) Still have a brand new alternator on it, re-conditioned all the battery connections for the 5th time on this truck (need new cables) and guess what... Edge still shows the APPS jumping around 0% 4% 1% 8% 0% *GRRR* ok, I've had this since 2014 and yeah, killed a trans but learned to live with it. -Removed the edge here for further testing as we know the APPS is acting up, bye bye my precious guages... Truck is as stock as it can be (still have my version of the big-3 upgrade in place, verified no ground loop induced noise) and the truck is still randomly choking and turning off the lift pump and firing right back up while cruising down the road =( Anybody want to buy a truck? I'm about done with this one.
-
Truck randomly dies. Please help, pulling my hair out, and loosing sleep!
Also while replacing the injectors I just moved the lines enough to the side to get the connector tubes out I didn't take the entire line sets off disconnecting from the VP like I saw in several YouTube videos
-
Truck randomly dies. Please help, pulling my hair out, and loosing sleep!
I ordered a timbo APPS yesterday, unfortunately it won't be in till Friday when I was supposed to be gone, with this truck such is life... been investigating all possible parts with no luck... I called DAP and they suggested if I didn't bleed the injector lines I probably have an air bubble killing the engine... My simple mind can't wrap my head around that one, if it can't build fuel pressure, how could it run at all down the road for 10 or so miles till it warms up? Wouldn't the fuel eventually push it out of the injector??
-
Truck randomly dies. Please help, pulling my hair out, and loosing sleep!
Interesting... so, to add to my confusion, I was in a spot today while troubleshooting where it would not stay started for more than 30 seconds to a minute and just die... so I thought, now's my chance and started removing everything I could... no change until I removed the alternator and ran on battery, so even though all indications point to good, I think it's bad when it heats up. I'm going to verify tomorrow at peak heat again and throw the new alt back in there to see. It's rare to see an intermittent failure like that with an alternator though... but fingers crossed.
-
Truck randomly dies. Please help, pulling my hair out, and loosing sleep!
Oh and the light does come on... Removed my voltage booster and my edge... No change.
-
Truck randomly dies. Please help, pulling my hair out, and loosing sleep!
I thought everybody said the truck wouldn't start if the ECM wasn't booting... The truck starts and runs and then randomly dies but comes right back. Removing all the ground mods is impossible as original ground wires no longer exist.. Good ground is critical to all vehicles I understand where you're coming from going back to square one but in this case my alternator is fine my grounds are fine... I'm really thinking it's that voltage box... Since I had tried everything else on the APPS for my hunting issue which by the way the capacitor did kind of fix by smoothing out the pedal only... I just ordered an APPS since that's the only thing that has never really been switched. I don't think that has anything to do with my truck dying. And it's really weird to me that the truck dying started after changing my injectors yay for coincidences!
-
Truck randomly dies. Please help, pulling my hair out, and loosing sleep!
Sure, a little fact about older vehicles, they dont do well with AGM batteries, AGM batteries need 13.8v as a float and 14.5 to 14.8 as a charge voltage, if your alternator is doing less than that, they dont charge and it kills the battery. Same thing applies in any application and its written on the battery. Their resting voltage when fully charged is around 13.3, so when your PCM checks it, it thinks it's full and doesnt send the field signal to the alternator and therefore doesnt really charge your battery fully which over time destroys the AGM battery fast. The best battery to use is a simple flooded, however. I loathe them for many reasons, so there are many ways to fix this, one of which is to "trick" the ECM with a dangerous hack... There's a box you can buy from a company (or two) I won't name that sits inline of your PCM power feed (fuse 3 on a 2001 cummins) It's a little computer chip that makes the voltage read just a bit lower as it passes through to the PCM, so at 14.6v for instance your computer 'sees' 13.8ish (or at least mine does) and at 13.3 it knocks it down to about 12, basically it makes the computer think you have a normal type battery... The advangage of this of course is that the alternator is still PCM controlled, the disadvantage, well, the power to your PCM flows through it, I originally thought it just to be the sense line, but looking at the diagrams, this is the main power feed. Other methods for doing the same include external voltage regulators, but often these just make your alternator always on, which isn't necessarily good for a battery.
-
Truck randomly dies. Please help, pulling my hair out, and loosing sleep!
Every light but that light comes on. I saw it recently. But not since this started. That fluctuation I always have assumed noise and tried absolutely every trick to fix.. so maybe it is just the apps. P0122 voltage low recently plaguing me so did the set screw adjust and recalibrate... But now im also getting p1693 companion code which i can't fully read of course. But many say is the vp44 dieing... Im in the process of removing the edge and also my agm voltage boost mod.
-
Truck randomly dies. Please help, pulling my hair out, and loosing sleep!
Wire mods such as the apps capacitor or *sponge*, the apps direct re-wire from ATS... and yes, the ground mod. The ECM is definately working, there is no Wait to Start light (I think it's too hot for that) I just drove it today to lunch, its fine until I've driven it for a good 20 minutes or so and it's warmed up. Then, randomly died like 4 times but only at lowwwww throttle, high throttle doesnt effect it. Can the APPS really case the whole truck to shut down? My friend said my voltage guage dropped to zero a couple times. Oh crap, maybe it's the battery mod... (gonna go bypass that and test drive again...) The alternator has almost zero ripple, the noise i'm reading on 2 meters and my oscilloscope are present when not even connected to the vehicle, so its just atmospheric noise at this point. I saw a really comprehensive APPS test somwhere that was like, check 10 different wires but not sure where i placed the bookmark
-
Truck randomly dies. Please help, pulling my hair out, and loosing sleep!
So, before you guys tell me to search if this has been answered before, believe me, I've searched this forum and the other Cummins forums to the point where I can't even think anymore I'm soo tired. I've been having torque converter lockups for a long time on my 2001. I've done every rewire out there, even bought the "sponge" (capacitor) from ATS to compliment their transmission and it still doesn't like being in between 30 and 40, you give it any throttle and it jumps back to 3rd and let off and its back into 4th... I've long suspected the alternator but it always tests clean, I'll get to that in a moment. So this weekend, I decided due to excessive smoke and lag with my Edge disabled it was time for injectors. I went with some DAP +75s and Saturday night dug in and got them installed. Following numerous posts and YouTube videos I got through the process since I've never done it before I was a bit worried but it was actually easy (I'll be honest here, I may have skipped over any sort of priming/cracking open fuel lines (I didn't know) and started the truck up, but it started right up and is really smooth, quieter than ever). Got everything torqued back down. Test drove the truck for about an hour and wow, big difference. I don't even think I need the Edge anymore other than for gauges. Next day (Sunday) we decide to go for a drive, got on the freeway, tons of power, actually fairly scary to be honest about 3/4 through the loop while heading back towards my house the truck dies and then springs itself back to life, however looking at the gauges, I notice no fuel pressure at all... I kill and restart the truck make it to the next stop light and it does it again. Loss of fuel, truck stutters and then springs back to life aggressively! Luckily, I make it back home and first thing I start checking is power to the relay to the fuel pump. It's got power at start, but even just sitting in my driveway, the power just vanishes from the fuel pump causing the truck to stutter and then fire back to life with 0psi on the lift. WTH? Checking the relays, the weird massively zip-tied wiring job (the pump was installed at the same time as my trans) and 2 unused wires touching the body... grrr. During all this I found the one connector above the valve cover I was just working with and likely bumped.. the one with the gray lock was unlocked and about 1/4 open... as deep as it goes, still probably fine, made sure that and the other connector there were clean and made sure they were locked. Cleaned the fuel pump relay connector (the stock connector that goes to the original pump) and every other connector within my reach including all 3 PCM connectors with contact cleaner and air. At this point I notice my APPS reading on the Edge all over the place, thinking back to all my issues I'm like, "That damn alternator noise" so. I grab my meter and quickly do an AC test... .019 .5, truck stutters 2.5!, .02... well the 2.5 was a fluke apparently because the truck was stuttering. Pissed off, I remove the alternator.. I had not purchased a fancy one that I had planned on like on my other truck yet. I'm shocked to find a Chrysler branded Bosch alternator when soooo many talk about Denso units on their trucks. I went to O-Really?'s and had them test it, their machine measures PASS with .40 ripple voltage (their threshold is 2.5!?) and I went, hmm I want to try something else. I run to AutoZone instead and theirs tested at .45, a brand new one actually tested .55 so I'm like, their machines are inaccurate anyway because of the motor that drives. I take a new unit and an old unit back to the house. I test the old unit's diodes and they are fine so I put it back on for now. Start the truck, now it's like 10 to 15 degrees cooler outside and the truck has been sitting 2 hours since it's last stutter episode and it's fine, it runs just fine... grr and the APPS is reading a nice flat 0% at idle.. however watching it, it eventually crawls up to 5%. I'm at a loss on what to try next, is it just the APPS, can the APPS freak-outs make the whole computer shut the truck down, including dropping the fuel. Am I looking at a dreaded ECM replacement? Is the heat causing the ECM to be intermittent? At this point, I doubt the alternator... TL;DR; Changed injectors, did valve adjustment, next day... It was hot, drove normal even APPS bounces around a bit as usual. truck died multiple times but only when foot off the pedal and came back to life... each time Airdog dropped out, Relays, Alternator, everything else appear fine, truck cooled down and idles fine, but afraid to drive it now.
-
Lift Pump Question
Yeah, but that's what eventually causes people to go "Search for it" when someone searches and searches and cant find the answer and opens a new thread ;) Very frustrating, I'm all for open conversation, used to run a large forum site years ago, but each topic has it's place? I dunno, was just a suggestion. I don't mind either way.
-
Lift Pump Question
guys... think of the poor future googlers... they are going to be searching for RF and 5G and end up here, or the opposite, looking for lift pump advice and having to weed through this to find it. I would love to join the 5G conversation but this is indeed as many have pointed out, a Lift Pump thread.
-
Lift Pump Question
Hmm, everyone here is worried about motor noise (ac noise) from the lift pump but not that single wire across an alternator.. lol. No there shouldn't be any problems here because coils will actually help shed noise in some cases, think a coil of coax at the bottom of an antenna.. but as someone mentioned the harness from FASS uses twisted wires, but remember the twist frequency determines a specific frequency where noise can jump into them. Twists are put in wire to reject outside noise, if the noise enters directly into the wire end from the pump then twisted pairs will not help. A coil, ferrite or other noise isolation device will be helpful, but in this case its just a set of power wires, headed for the battery.. which will filter. And back to grounding, if the grounding is good. It will help dissipate anything on the grounds. I had fuel pump noise very clear in my radios until I upgraded the chassis ground to battery. I'd be way more concerned with audible noise, I hear the fass's are horrible in that regard. Regarding the 5G discussion that sprung up, did someone start a thread for it in the general section? Being in the network world, I have thoughts.
-
Time for a new Alternator
Just looked closer at some of his posts, he knows his stuff. And in one he mentioned capacitors filter, which is what i was trying to say, he said it better. Noticed this other question I missed yesterday earlier in this thread: yes, the characteristics of many things including diodes and even the inductance of the coils change based on temperature. yes, load can increase the field strength but the regulator should keep the amplitude of the AC within a range so it should change much. there's another component here, frequency, the faster the alternator is spinning the frequency changes, which can effect how much leaks out in the method I've been describing, not through the diodes but through the casing, a higher frequency has a higher chance of making it through the little vent holes and onto the close-by wire. So that RPM impacts the noise frequency which mixed with all the other RPM sensors your computer is trying to read and hello issue. So this could completely appear intermittent but really its just everything needs to be in the right conditions, load, temperature, frequency, other vehicle components, etc.. Anyway, I think I've beat the topic up enough.
-
Time for a new Alternator
I absolutely agree with the video on a failed diode. What I've been trying to say is you can get alternator noise without a failed diode. When I had the lockup issue I had minimal ripple, almost none. This ground mod fixed it for me and apparently others. Some may never see an issue. I'd rather make that wire more efficient than risk it. So I thought I'd offer it again for those who want to try it. Exactly, but a failing ground connection will make AC noise easier to pick up... Especially when running right over a noise producing device... (Alternator) Of course in true AC there is no ground... in this case its a ground wire that would possibly pick up noise, failed diode or not. If the connection to the battery is solid, that waveform will tend to flow across the battery and get filtered a little, not necessarily cancelled but its got nowhere to push past the battery when its just noise vs when a diode fails the whole system sees the wave because the circuit is complete. But if that connection is bad, that noise will go to the computer and mess with it instead. Path of least resistance. We are kind of saying the same things in respect to the failed diodes.
-
Time for a new Alternator
5V Signal yes, analog, a really fancy variable resistor. and its going to be relative to the computer. Regardless of which sensor, I'm sure the computer takes into account multiple at the same time. (Dodge does recommend the alternator and APPS when having this issue) your computer needs a strong ground, the electrical systems on our vehicles float. So the ground needs to be a strong reference to the battery negative. The battery provides the reference for the entire vehicle, if left to the alternator it wouldn't be stable as the battery provides the capacitance needed to smooth it all out. To get this everything needs to have clean, electrically strong grounds, battery to chassis, chassis to engine, engine to battery. If done wrong you'll still have a difference in potential and a ground loop which causes noise as well. This is like any other logic circuit and needs a strong ground reference and all things communicating need to have the same reference, that cable running across the alternator can pick up stray voltage changing that reference so on the up swing of any waveform the voltage would appear to drop on a sensor that has a strong un-interfered with reference to the battery. causing the voltage to appear to dip to the computer. For example you get 1v p-p AC on that line, your computer would vary up and down from 4.5 to 5.5v. Now the computer may or may not see it that way as the regulator for 5 volt floats on that ground wire in question and there's enough head room to the 12/14v but other things connected would suddenly be seeing this variation unless they are powered from and floating on that same regulator for the computer, ground and all. so if the APPS doesn't share a ground the equivalent would be stomping and releasing the pedal quickly and it not knowing what you want. During my personal lock up issues I saw the TPS (APPS) reading on my scan gauge jumping around like it couldn't read the APPS so I believe this to be true. My original issue with this occurred when my alternator was still OK with no AC ripple at all it barely started getting some almost a year later and I replaced it just because I was adding on my usual mix of equipment I knew that the stock could not handle. My APPS is the same one that was in use but I could see the change in the readings immediately upon moving that cable. The more load you put on the alternator or even the faster you spin it along with your engine, the more possibility for the noise to be inducted into that wire, so I'll respectfully disagree since I know you know a lot about these vehicles but I believe that that wire should be nowhere near the alternator and not even run across the engine at all. That's why I moved it to the driver side battery directly. The other weak point is that clip connector that's there, if that gets even a bit corroded, your ground strength will be lessened, and more prone to picking up these voltage fluctuations from the alternator. Too many years of excessive Stereo (SQ competitions) and Radio gear in my vehicles (Ham, CB, Commercial etc...) I've had ground loops, fuel pump noise, alternator noise, the works, RF and Audio amplifiers are really sensitive to noise. I'm not an EE (too much math) I'm not making this up either, was a firmware developer and test engineer for a really long time. Too much time debugging hardware and logic circuits. Wow, sorry everyone for the long winded reply.
-
Lift Pump Question
So it sounds like you're doing exactly what i wanted your fass with the carter backup? whats a fic fitting? It may not be optimal may be lower power but i definitely like the idea of being able to move while I wait for the replacement large pump. I like redundancy.
-
Time for a new Alternator
Ah, got it, I missed that somewhere. I did see the pictures from the other Manufacturer on their site though so that's why I've been saying that. The ground wire is and isn't a band-aid, agreed that its not the source of the issue, but you'll likely still get some inductance if the wire's right across the alternator, AC can jump wires so that wire laying there can POSSIBLY pick up noise pre-rectifier. Or maybe its even acting as a pick-up wire like all those wires inside the alternator. That's why I said it's still a good idea to move it. How often on other vehicles do you see wires that close to the alternator that aren't specifically for the alternator? I just thought of a quick test, most people know to test alternator ripple just use your meter on AC across the battery terminals, but to see if this wire is indeed picking up noise aside from the diodes, put it on the 2 ground points 1 on the battery ground passenger side where this wire heads to and the other on the pcm ground while the wire still goes across the alternator...(with your brand new clean alternator) there's probably still AC there. All I know is moving it away fixed it for me. I tend to re-do all grounds on all my vehicles, you'll find 0 guage wire and no braided straps anywhere on my truck, all soldered, no crimp-and-go and I removed that quick disconnect out of that particular ground cable and shortened it, the shorter the run for any electrical circuit the better. It's all time consuming but in my opinion, worth it.
-
High amp alternator
Just as I suspected... That's why I keep excluding them from the article I posted below which seems to be invisible with the amount of alternator questions recently. Grounds, Grounds, Grounds!.. Even if you're not running things like I run (Stereo, Radio gear, etc) All vehicles can benefit from cable upgrades... A lot of people refer to it as the "Big 3 upgrade" Bad ground cables (either corroded as @mopar1973man pictured) or insufficient quality/size will help amplify the noise and restrict current.
-
High Idle Switch
On mine I use 3cyl for any warmup unless its 50 degrees already. Bought mine because all I ever hit here in Boise was cold enough for 6cyl high idle, i want to warm up fast. Although I had always heard that putting a load like that on a cold engine is not good... Cummins built these modes in for exactly that, extremely cold weather. I'd think Cummins would know what they are doing. Your comp box shouldn't hurt it, my JWA doesn't. you could always return it to stock when using the feature... then turn it up as you drive. I'm not sure the COMP has the same back-down features the JWA has, mine wont let me hot-rod until the truck has warmed up fully. I have the same question regarding the MPG though, is it safe to be changing the fuel / timing to think its 143F out when its really only 20? Does it add or remove fuel?
-
Lift Pump Question
*sigh this is what has kept me from upgrading to FASS or AirDog... both of them have their warranty process as a cross-ship but if I'm thousands of miles away from home I don't want to sit and wait for the shipping, I want to be able to go to a store and buy a new one. And of course a spare would be pricey. Has anyone done what I was reading about recently where you add a SUMP.. definitely beans single hole single o-ring, the fass one has like 20 screw holes which seems like a leak waiting to happen... then a AirDog or FASS up to a ball valve and a T feeding into the stock canister filter/heater? I'm thinking that is the route I want to try so my stock system is still there, just turned off at the ball valve and the harness disconnected because its connected to the better pump, and if anything should ever happen I could at least move the harness back to the stock pump and flip the 2 valves to the opposite positions and be back up and running.. Thoughts?
-
Time for a new Alternator
For your original lock-up issue there's a post somewhere out there about moving your ground wire for the PCM, you'll definitely want to do that regardless of any alternator repairs. The reasoning behind it is Even though you have some AC ripple in your system (and you will always have SOME) the sensors (mainly the APPS for this issue) and computers run at either 3.3 or 5v which has been regulated down from 12v using the fluctuating ground reference but some of that is filtered by your batteries. And the regulator's ground reference of course changes with the computer's ground reference when regulating so its still a cleanish 5v. Dodge did something really odd and ran this ground right across the alternator to the battery on the opposite side of the truck instead of to the closest battery. This causes your ground reference for the computer to be off because it picks up noise like an antenna being right on top of the alternator. Easiest thing is to undo the zip ties and a couple of bolts to give it some slack and run it across the top of the radiator support which will provide someone of a shield and increase distance. I did this when I was away from home without the proper tools to solve my problem (which was rapid lock-unlock while towing 7000 up a steep hill, it was scary loud clunking and jerking). When I got home, I cut that ground completely and put it into the battery terminal closest to it. I haven't had a lockup issue since. Later on I replaced my alternator with a 270XP (200A at idle) Since it's a high current alternator it actually has a little more ripple than stock but not bad enough to do any damage to anything. I noticed in another thread you bought the Nations alternator you mentioned at the top of this one. just curious if it has any markings like the others I've seen that indicate the actual brand? Update: Cant find the post I originally went off of but this guy's explanation is identical to what I did: http://www.kentsoil.com/dodgebug1.htm