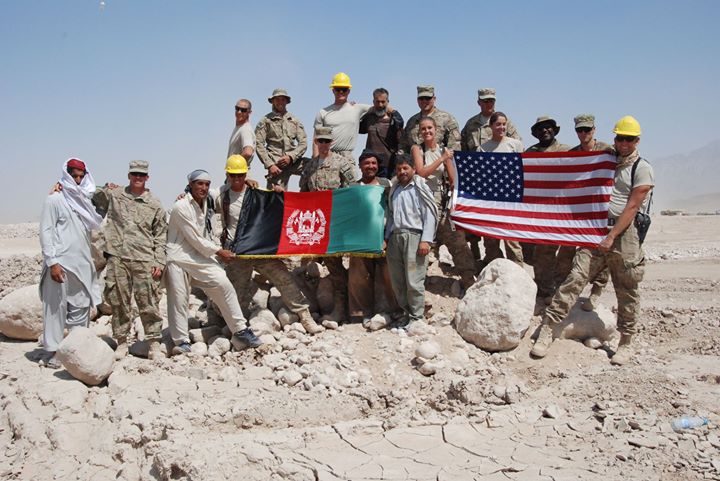
Everything posted by Llamajwc
-
He351ve stand alone Arduino controller code for 2nd Gen Cummins
I have it that way. in the code and in the serial monitor drop down. I loaded up the other HE351ve_control.ino, and it is showing up on the serial monitor. But for some reason the latest mega 1.12 doesn't.
-
He351ve stand alone Arduino controller code for 2nd Gen Cummins
Hey, I'm really sorry to have to ask. but the Arduino serial monitor is disabled by default, correct? For the version 1.12? How is it enabled?
-
24v ppump swap
Both the Throttle and the ppump FSS are all the way forward.
-
24v ppump swap
Evening all, I've been searching and trying things for awhile now, and still no luck. Long story.. I have a 99 24v 5.9l that I have swapped to a brand new rebuilt ppump from Scheid diesel, new Crazy Carls kit, with 0.093 lines and DFI SAC 7x0.010 injectors. air dog 4g 165, new sump. Initially I bought the ppump from a guy that needed to be rebuilt, but i installed the pump and was able to get the truck running. but then the Rack was sticking so i sent it out. Since i got it back I haven't been able to get the truck to run, 3 of the new fuel lines weren't seating properly so they were replaced. I bought a used Airdog 100, but replaced it with a 4g 154, and new Baldwin filters. since the Airdog100 was loud. i figured clogged filters, but when I took the motor apart I found that the seal was worn and diesel had gotten in and corroded the inside. after replacing that it was still loud, and not as quiet as it should be. (1 Problem) I'm guessing theirs still air getting in somewhere. I have a fuel pressure gauge hooked up before the Ppump, reading a steady 50 psi When installing the rebuilt ppump, i set it at Sheid diesels recommended 18 degree pin timing. Ran the Airdog pump, cracked open the overflow valve fitting on the ppump until the bubbles stopped and steady stream of fluid entered. closed it off, then started cranking the engine with the nuts on the head/injector side cracked open (1,3,0 until they were pissing out. closed them off, then would open the others until they sprayed.) at this point im getting a slight mist of smoke. then closed those ones off. and would crack open 1,3 again. this is as far as it gets I have 2 batterys, and I've been cranking and cranking. till nothing. I've changed out the return fuel lines, new fpv and washers. Ive pressurized the tank to check for leaks, and sprayed all the lines, and still nothing. Even the ppump to injectors I've tightened and loosened to try and get a good seal. How could the High pressure side loose prime? I don't understand how this could be so difficult.. where else could their be a leak? Does anyone have a bomb proof fuel line setup? I'm thinking about switching to AN fittings, i hate the stupid banjo bolts. Sorry for the long post, I'm still new and learning cummins. I've asked other forums, looked online and I'm still lost. any and all help is greatly appreciated
-
Big change in my life...
Thoughts n prayers!
-
He351ve stand alone Arduino controller code for 2nd Gen Cummins
Ooooo that makes sense! but it case it didnt, could you say it another way? I went through and changed the mcp can1 (10), from 1 through 15. mcp can1 (1), mcp can1 (2), mcp can1 (3), mcp can1 (4) etc.. and none of them would result in moving the actuator.
-
He351ve stand alone Arduino controller code for 2nd Gen Cummins
Anyway to send you a video? I've taken the Arduino out of the equation. It still does the same thing. When power and GND are applied it spools up.
-
He351ve stand alone Arduino controller code for 2nd Gen Cummins
When I connect the power and ground to the actuator, whether its connected to the arduino or not, the motor starts spinning. accelerating, and then decelerates. It doesn't jog like its supposed to. Jog, like the motor twitches for a moment. RX receive led on the Canbus shield is solid lit up.
-
He351ve stand alone Arduino controller code for 2nd Gen Cummins
Alright, new arduino mega, and Canbus shield. Tried different libraries. Still does the same thing. Spools up for a second then stops. Tt doesn't jog RX is still solid lit. Is their somewhere in the coding that the Can has to be defined or something? I find it hard to believe that this actuator after being sent out, new board and updated software.
-
He351ve stand alone Arduino controller code for 2nd Gen Cummins
ARGHH, So I sent out the actuator to AVI electronics in Illinois, who updates and rebuilds vgt and other stuff. I got it back today. Hooked everything up and it does the same as before. I hook up the pos n gnd and the actuator spools up for a second. I hook up the Can to the arduino (arduino +Canbus + lcd shield to calibrate) and RX led illuminates. On the serial plotter it is sending the commands, but theirs no response. Everything is straight connected. Any thoughts? I'm going to go back an reread everything...
-
Everyone post a picture of your truck!
Hahaha, it is, only because it was temporary. it was local, and available at the parts store just needed something until i got the baldwin in the mail.
-
Everyone post a picture of your truck!
-
He351ve stand alone Arduino controller code for 2nd Gen Cummins
Yea, that's what I was afraid of. Thanks ?
-
He351ve stand alone Arduino controller code for 2nd Gen Cummins
I was using a 12v small engine battery, then tried a 12v 3 amp bench power supply. I just got the actuator today from a guy, he said it was a known good actuator with low miles.
-
He351ve stand alone Arduino controller code for 2nd Gen Cummins
I have triple confirmed the connections are correct. I see it's getting sent a message on the plotter. It doesn't jump when power is applied, it. Just runs for 2 seconds then stops. I can disconnect the power, reconnect and it runs again for 2 more seconds.
-
He351ve stand alone Arduino controller code for 2nd Gen Cummins
I dont know whats going on. I have the code uploaded to the arduino, I can go into the serial plotter and see the data changing. when I hook up POTS, I'm able to change the veins on the serial data. But, when I connect the power, and Can wires I dont get movement. The only thing that happens, is when I connect the power wires the motor spins for a second then stops. From the he351ve actuator, heres hot I have the wires hooked up. Red/blue = 12v power Green/white = GND Yellow = CanH Green = CanL Most likely dont have those connected correctly, eh? I dont want to screw up the actuatur.
-
Truetrac good for towing backhoe
It all depends on your driving methods, applications. If you are driving just the truck on pavement, mud, ice etc. Or if you are hauling all the time on pavement, mud ice etc.. IMO 2wd truck with 3.55 gears is a personal transport vehicle, that occasional uses the bed to haul things. Or has a trailer to be used on pavement occasionally. Next step up is the 4x4 for is the vehicle Is To be used on more demanding roads, ice, mud etc. Add a spring or clutch posi for the next step up. Then a fully geared Eaton next But for extreme duty, hauling on mud, or deep snow, a full time locker is best to be added. And depending how much your are pulling a weighted trailing through it all then you can go to a 4.10 gearing Again, just my opinion. But getting back to, if truetrac is good for towing, it depends on how you are using the truck.
-
He351ve stand alone Arduino controller code for 2nd Gen Cummins
Hows it going with the OBD2 interface? Which one of the products did you try/ go with?