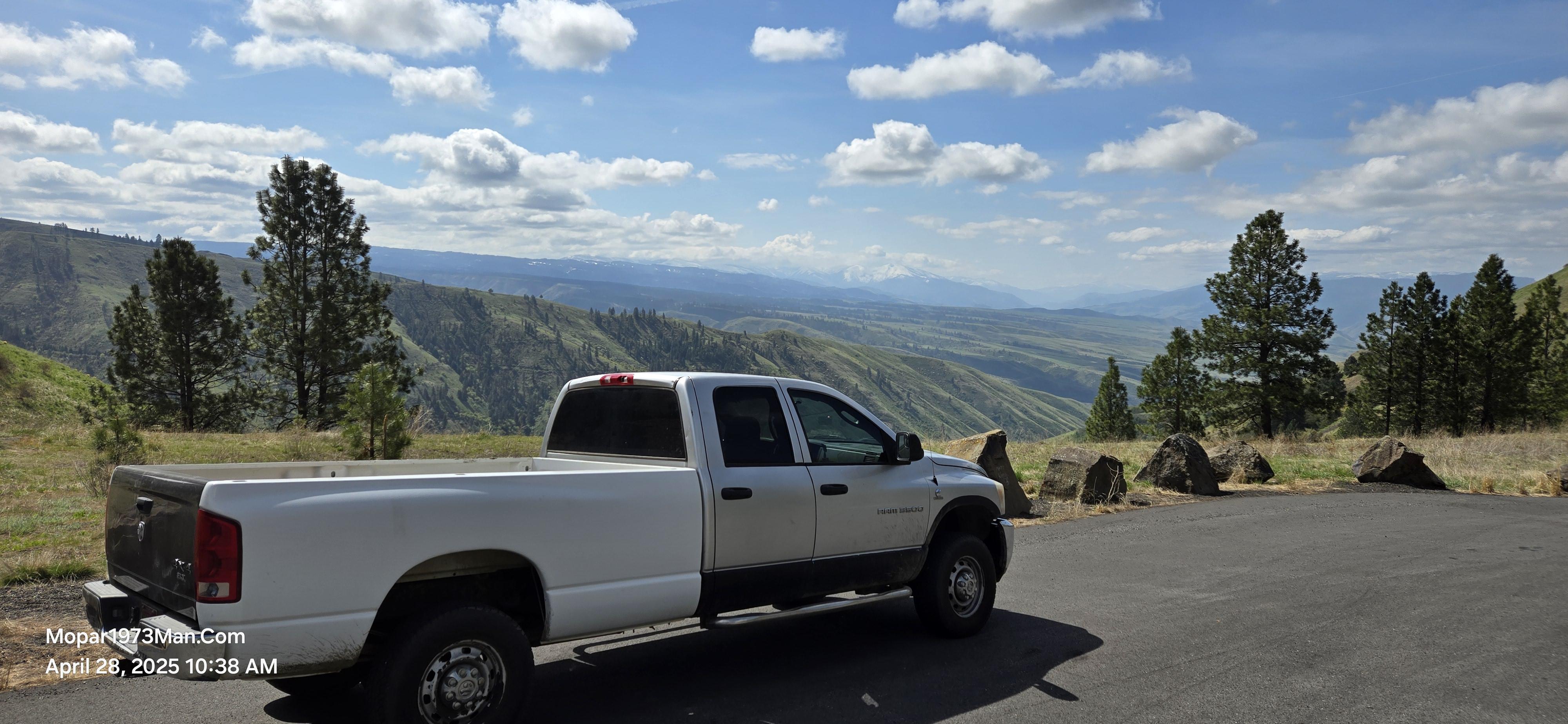
Everything posted by Mopar1973Man
-
20250407_122651.jpg
From the album: Thor
- IMG_20250407_114949.jpg
- IMG_20250407_114950.jpg
-
d00a2ab0-b680-4c64-9a2b-487ef91748c0.jpg
From the album: Thor
-
54db826a-895a-46f5-aae1-579033d798f8.jpg
From the album: Thor
-
Thor - The project continues
Yup. Thor is a running and driving truck now. I've been fighting to find a 3rd Generation bed, taillights and tailgate for Thor. Surprise, Surprise! The 3rd Generation trucks in the Boise Valley are all short bed. OMG! This is nuts. I spent over 5 miles of hiking just walking around the wrecking yards attempting to find a truck bed for Thor. Long Bed boxes are rare, and if you find one, typically the bed is completely hammered like I've got a few photos of trucks with long boxes but the truck looked as if it was put through a drier. I now realize I need to call today and find a wiring loom for Thor yet. Just made the phone call to North Verde Auto Salvage in Ontario OR. I just found my taillight loom and it will be picked up while I'm down getting the truck bed. I found another bed in way better shape and it is white in color and excellent shape. All this will be gathered on Wednesday. With all this happening, I was wanting to bring back the classified section for the website so people can sell and look for parts they need for their trucks and vehicles. Give me some time I'll see if I can build a classified ad area most likely be built on the article database idea. Ok. I managed to toss together a database and some extra fields for other information. We now have a classified ad once again. The only thing I ask that people set a expire time no longer than 1 year. Now you can see I have a flatbed for sale and winch bumper. One of the staff @Doubletrouble made a request for the return of the Classified Ads area. Sadly, there isn't much for 3rd party apps right now for this software. I created a database for listing your oddball parts and then even list vehicles you want to sell. This is all home brew design, so if there is something else you want me to add to this Classified ads area, I'll be glad to add the info slot.
-
Water methanol for mpg.
Here is found it https://www.stealth316.com/2-turbotemp.htm
-
Water methanol for mpg.
80 to 140°F is optimal for MPG and daily driver.
-
Water methanol for mpg.
I'll bite. So is near zero boost is most efficient way to run. Yeah with a tweak on the retard you can control boost. Yeah with boost there is a rise in temperature. Let me dig for my turbo output calculator. It shows temperature change etc. I'll dig that up for you. I'm trapped with a HX35W styled turbo to keep my exhaust brake but if you could calm the temperature in your theory I could band-aid Beast with water/meth mix setup. Yeah 7x0.010 injectors can get hot.
-
Bad CTM?
Not off the top but should be ohm testing pin to pin per se between what the column has and the steering functions.
-
Central Timing Module problems
Yeah its the best solution to resolving the damaged modules and getting them repaired. Sucks, to make this mishap but there are solutions to the issue.
-
Central Timing Module problems
VIN number is not matching you are going to have issues. You might give Auto Computer Specialist a call and see what they are capable to handle in repairing the modules and also flashing the VIN number to them as well. Sadly you can't mix and match VIN numbers on modules.
-
Stalled The Engine
I was attempting to keep you all informed of the work happening here using the Blog system. Sadly, there were bugs in the software, some bugs have been fixed. We made it to the Invision Community Version 5 software. Things have been a bit weird and tough for me to catch up and get everything working correctly. Blogs had an error where the categories couldn't be managed. When I attempted to delete one category, it deleted both of my previous blog posts. Opps. Yeash it sucked but I'll stumble and get back up and running properly and keep making the site better and faster. Yes, the blogs are a new feature that is part of the website package now. The mobile and desktop themes both come with light and dark color themes. This can be selected at the bottom of your screen. By default, the screen will auto-adjust between the light and dark, typically dark with mobile devices. Remember, you can have light or dark at a touch of the icon at the bottom. I know there are issues with the Event calendar that is going to be used now. The design plan is that you'll notice there is no phone number listed. I'm going to start an appointment-based call back and phone support. Take notice that the only contact information is my snail mail address. Phone contact will be done by appointment base. I can no longer just give away my knowledge or my information on the website. I'm a PRIVATELY OWNED website. I'm not like Cummins Forum, which is owned by VerticalScope Inc. Mopar1973Man.Com is a small business privately owned and maintained privately. Yes, this means I'm responsible for all bills and services to keep this running. Phone Support appointment based - $50.00 an hour based on the time logged on my phone. Subscriptions - These are required to interact with Mopar1973Man or get support for your vehicle. Articles and Elite Articles will be merged, and Elite Articles will be removed soon. The download section remains fairly the same, but the Listing is now Grid Styled. Gallery Section is another new feature I'm already hard at work using for my blogs now and my artwork as well. I want to invite all the members to show off their trucks in the generation categories, and then I can start voting for Trucks of the Month. We can change up the generation categories and have fresh pictures of members' rides. I've been digging through the article database and found several little things I wanted to fix, being that the website is in a state of flux right now with the Article Database having URL edits done. You might find old URL links that might not work now. Sorry, but give a bit of time to allow Google to reindex this in the days to come.
-
A day to play with green!
Yesterday was Sunday. I wanted to keep up with my makeup artistry, work with my white face foundation, and try a few tricks. It's not my best work, but it was an improvement compared to some of the other white face makeup I've done. I've added Mehron setting powder to set the white base and pull the extra moisture out of the body paint. Green is a tough color to work with being I've got very little in a green powder palette to do my eyeshadow. Then working with green lipstains is interesting, to say the least.
- 20250330_125841.jpg
- 20250330_125826.jpg
- 20250330_125816.jpg
- 20250330_125804.jpg
- 20250330_115821.jpg
- 20250330_115755.jpg
- 20250330_115747.jpg
-
Ram air intake
No problem. Always there to help out.
-
Ram air intake
I can tell you an old member @isx did the math on cold air and hot air and there was a very very small change of amount of moles or molecules of air was in the air system even at boost. So the best is to control you turbo and airflow by timing. Always remember lower the boost better the efficiency.
-
20240917_110628.jpg
-
20240224_130418.jpg