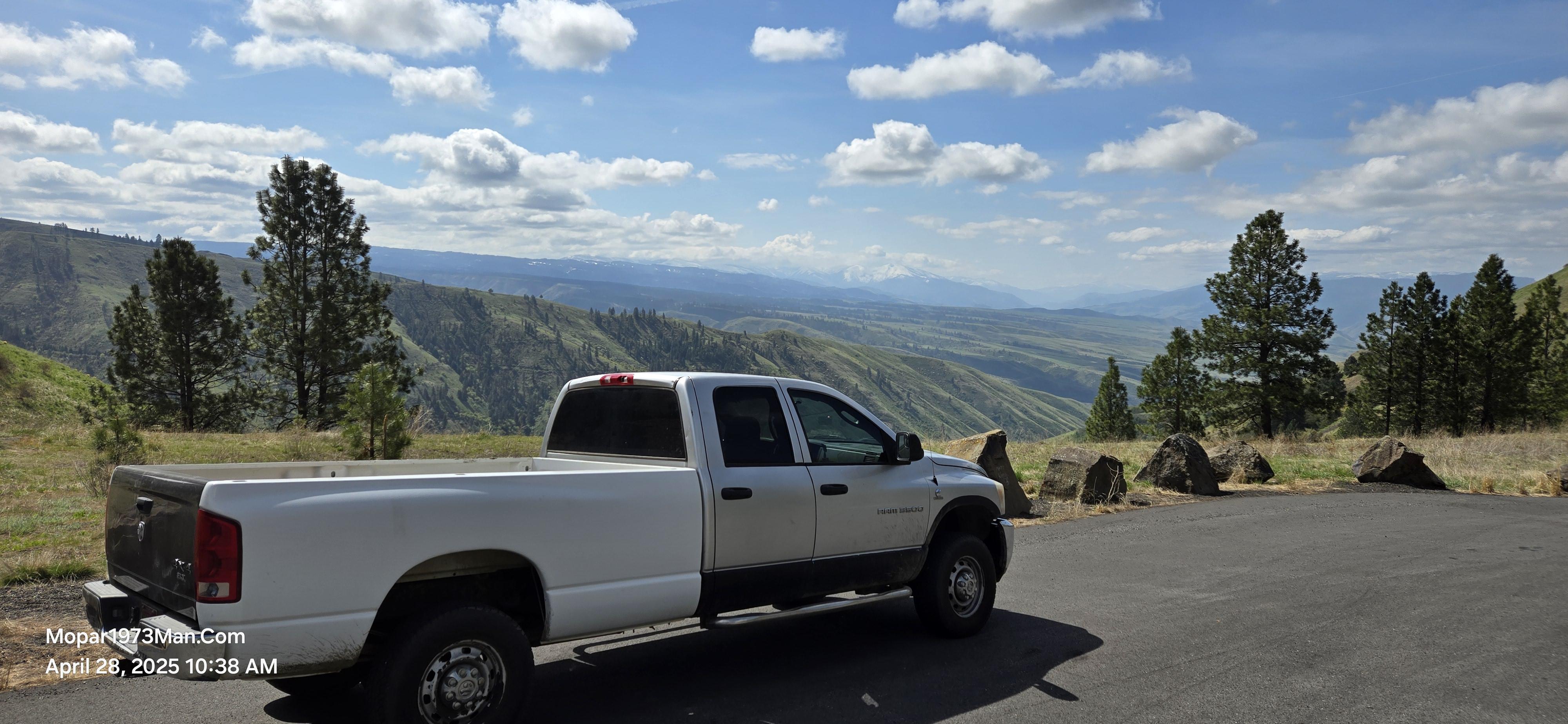
Everything posted by Mopar1973Man
-
Strap to U-bolt conversion
The only thing I can suggest is contacting https://idahodrivetrain.com/ . You should be able to get information from them,
-
Off to see the insurance company
Oh, today was an awesome day. I had two younger gals walk up to me and read my shirt, and then they wanted to pose with me in the Albertson's store. Then several others made comments on my appearance. I really do have an enjoyable day just being all dressed up and in makeup. My shirt says, " If you don't like me, remember its mind over matter. I don't mind and you don't matter"
-
Drop rpms
Technically, the coolant sensor will control idle, but only in an OVERHEAT condition, it will drop existing RPM by about 400 RPMs. This is not the solution, but a normal reaction. I found this way back in the day by using a rheostat to vary coolant temperature. Just to let you know, this is a normal reaction to the sensor unplugged because it's a high volt code (+5V) and the ECM reacts accordingly. Still, you have an APPS issue, most likely on the APPS sensor is not providing a proper idle validation signal. This will force the ECM to drop the APPS sensor signal and run the Cummins idle software, which is a perfect 800 RPM's. Now the only other way to raise idle is bad injectors. If your injectors have over 100k miles you need to replace the injectors being as pop pressure falls and idle speed rises. I've seen trucks idling at ZERO percent engine load and idle speed of 900 RPM, being the ECM cannot cut fuel any deeper, and idle cannot be obtained.
- 20250708_090224.jpg
-
Titanium
My adventure of having a second run at bladder cancer and going back and forth to chemo treatments and surgeries. "Titanium" the character, kept me going and helped me with depression and stress of the idea I might not make it. I've made several new friends and found a new way to enjoy life as I continue to dress up and do my Titanium makeup. I'm always taking my adventure out into the public and share my artwork with everyone!
-
20250708_090224.jpg
-
20250708_090151.jpg
-
20250708_090133.jpg
-
20250708_090129.jpg
-
20250708_090118.jpg
-
20250509_111108.jpg
-
20250509_111112.jpg
-
20250509_111120.jpg
-
20250509_111136.jpg
-
20250509_115727.jpg
-
20250509_115719.jpg
-
20250509_115750.jpg
-
20250509_120007.jpg
-
20250428_103050.jpg
-
20250424_093005.jpg
-
20250424_092936.jpg
-
20250405_110238.jpg
-
IMG_20250407_114949.jpg
-
IMG_20250407_114950.jpg
-
20250330_125841.jpg
-
- 20250708_090133.jpg
- 20250708_090151.jpg
- 20250708_090118.jpg
- 20250708_090129.jpg
-
Off to see the insurance company
Yes, I'm off to McCall, ID, to meet with my insurance agent and review the actual insurance policy, word for word. Just to give me a boost today, I went a bit more like Clown Goth. I've a few other stops today, including picking up medications and doing some other shopping. I've got several fans in McCall who enjoy my makeup work and love the reactions of people. Oh, check out the gallery photos. I've got a new shirt. Gotta keep building my character up. I'm hunting for a second shirt, but still searching for something particular.
- 20250708_090224.jpg
- 20250708_090151.jpg
- 20250708_090129.jpg
- 20250708_090133.jpg
- 20250708_090118.jpg
-
Personal Note
https://www.tiktok.com/t/ZT6eATWry/
-
Flashing WTS light
Could you bring that over here so I can review what is going on? I'd love to help I need to know what they found to help you out. Stupid HOA rules.
-
Crankcase oil volumes
Geno's sells the replacement dipsticks if needed. 2nd Gen Cummins have been 11 quarts for a long time. Its only when you switch to 3rd Gen the 12 quart oil system came to being.
-
Drop rpms
Most likely a bad APPS sensor. The is a idle validation switch inside the APPS sensor. So if you have mess with or adjusted the sensor its possible you are stuck in throttle mode and idle will not happen. I suggest getting a Timbo's APPS and replace your APPS sensor, this should fix your idle issue. No ELECTRONICS the Timbo's APPS is fully mechanical. Now stock APPS. As you can see it requires electronics to make the idle validation work and misadjustment can and will affect idle speed.
-
Flashing WTS light
@Sycostang67 I'm sorry that you're stuck with your ECM not working. I know you're upset, but calmly call ACS and find out what information you can about the repairs they have done and any other process or testing BEFORE the ECM is hooked up again. There is a solution, but we have to make sure the truck is ready and does not have another issue in the wiring or another device that will cause the same damage over again.
-
Personal Note
Hey there gang, I'm still here working at the website. I know there are people there that just don't understand why I've changed in appearance and my nature of being. Sadly, the whole aspect of my life was permanently altered when I had my last run of cancer. You have to realize I'm no longer able to work as a mechanic and do Cummins diesel work at a commercial level. I have an ostomy bag hanging on the front of my belly that is a constant reminder of the cancer I fought through alone. I deal with depression on a mild level because all the things I enjoy doing are gone! I can't lift more than 40 pounds because of hernia risk. My makeup is my way of making the most of the life I have left. As much as I love to turn wrenches now you toss in the fact that my shop is gone due to the mudslide here. Some people ask why you don't just put on your cowboy hat and go back to wrenching. Sorry, I can't I've got medical limits that prevent me from doing the things I love. This is why the character Titanium was created to help deal with my depression of not being able to work on diesels, I can't do a lot of things now because I need to keep my stoma and ostomy clean at all times. Infection at this point could cause huge problems for my health. What is left of my toolbox and tools, a lot of my sockets spilled out. My makeup and character "Titanium" create that boundary because I'm usually dressed up. Yes, the dress code I wear some usually shirts like my "Don't like me F___ OFF Problem solved! I've got another shirt that says Fun Fact: I Don't Care. At any rate, this is all about the laughter and smiles I create while I'm in Titanium character. My medical team loves the makeup and shirts I wear. Even when I'm out in public I've got teenagers yelling out over the parking lot of Albertson's, "I Love You Titanium!". The more I'm experimenting with movie set makeup, like Mehron and other high-quality makeup providers. This is what I now enjoy as fun is getting into makeup and making smiles and also supporting other cancer patients and medical patients. Yes, I have a following on TikTok members with similar issues. As for the nature of being. That has been changed too. I'm tired of the people who just say, "I'll pray for you" and offer zero help. It's gotten even worse now. Just now found out my neighbor, who actually his water line actually caused this issue, is willing to create a GoFundMe page for Mark, but no help for me. That is just absolutely rude. The fact since the landslide, the Dischinger Family is the only one to come help us with the clean up. Even my church group is not even offering to help. I'm sick and tired of all the "fake love" or "fake help" towards us as a family unit. I'm sick and tired of people posting this all over Facebook in turn does nothing to bring help. Everyone knows what happened but no additional help has come, and it has led to a lot of conversations. Yeah, it's been over a month still a huge mess. Month later its just the Dischinger Family and Us (Mark, Suzanna, and I) cleaning this up. Just a few days ago, the Rupp Family had a major mudslide come down through their orchard and cow pasture and made a huge mess. I know they are very religious people too. I told the owners, "I'm NOT going to say the same old, I'll Pray for you." No, I did the right thing. "Is there anything I can do with my abilities to help you and your family with getting your business back on its feet?" Yes, even as broken as I am I offer help to my local community. Beast, sitting in Rupp's parking lot, While I offer help to the Rupp family after the mudslide.
-
Mysterious Knock on VP44 Truck – Need Help! No one can figure this out!
Auto Computer Specialist does full wiring repairs and testing. Just a tidbit to aid in the adventure.
-
2000 Cummins Surge/Dead Pedal
My only problem is this test was designed for home person to test. If you pull the alternator and bench that is done under full load. Either way excessive AC noise will cause... VP44 damage (PSG, P1688 or P1689) ECM damage (P0606 but could be a all hi or lo volt codes of all sensors) PCM damage (P1698 code typically but also code have hi or lo volt code of sensors) AC noise puts a lot of stress on transistors and IC chips. On my truck it made the cruise control to wander +10 or -10 cycling past it's set point of 65 MPH. Either way AC noise pollutes the AC signals from HAL effect sensors like crank sensors or speed sensors like ABS.
-
2000 Cummins Surge/Dead Pedal
Small correction...
-
We are back from our camping trip
@Tweety Bird And I had to get out of here and get some downtime. Extremely stressful to get up every day, looking out the living room window at an entire mess of my shop buried under tons of mud and dirt. It was wonderful to just go out north of McCall, ID for about 4 days. We didn't do anything but rest. Now we have returned home and are going to start making moves to clean up the main house with all the unpacking from moving to my place. Lots to do. Then still need to handle the mess in my driveway of my shop. Here shortly I'm going to post up a Go Fund Me Page and we are going to attempt to start heading towards normal life again some how. Anyone who wishes to help out, I will not turn you down. As for those who just want to send Prayers, thank you, but it doesn't clean up the mess, replace my shop or my tools that were lost. Beast and the RV are up near Upper Payette Lake, Idaho Miss Mollie on her first camping experience.