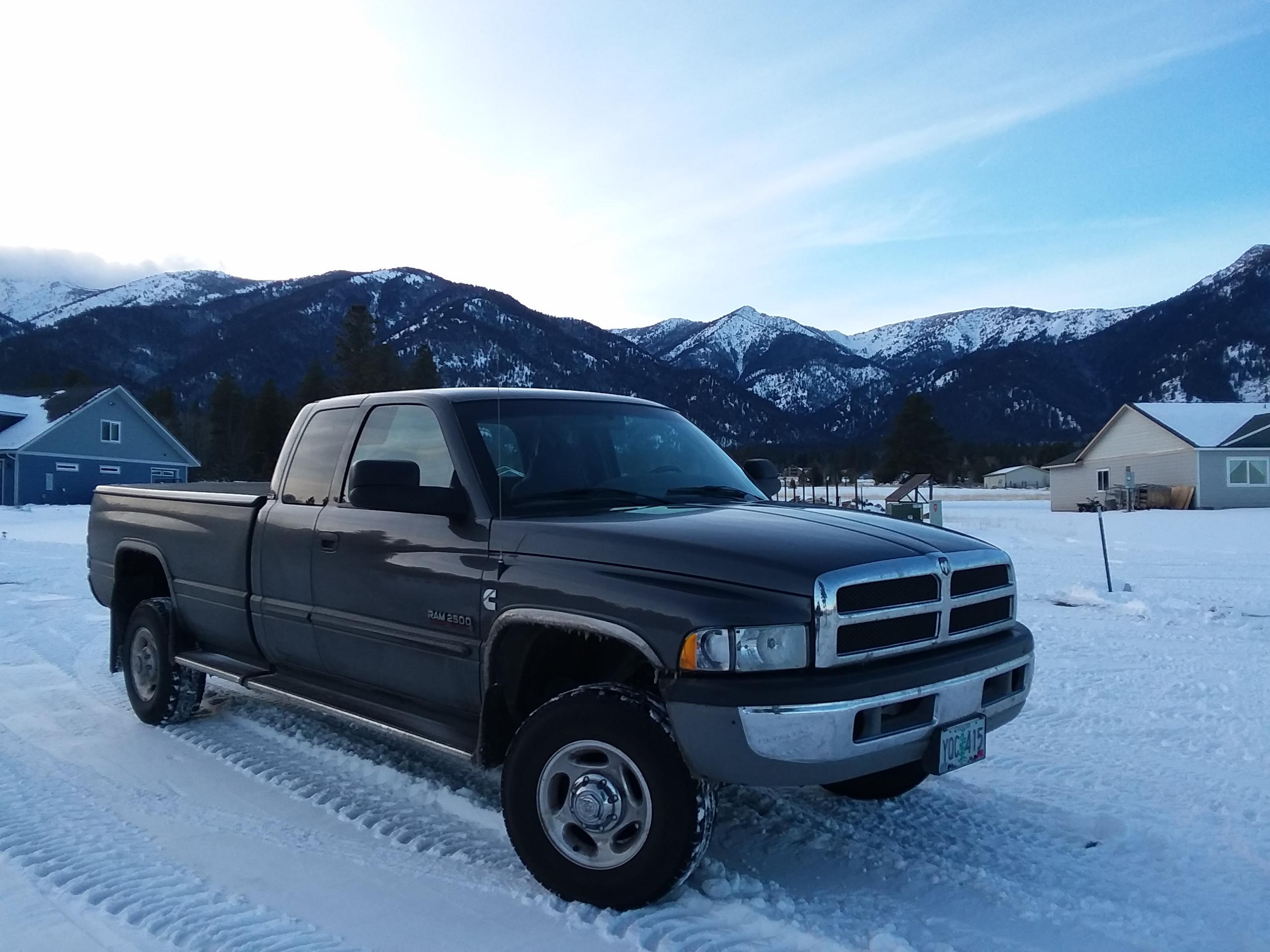
Everything posted by Tractorman
-
P0121, P0237, P0234, P1689,p0236 all at once.
Double-check that your positive cross-over cable is connected. Verify that you didn't miss any other wiring connections. I would start the engine and quickly check voltage at each battery individually to see if it agrees with what dash voltmeter is showing. Both batteries should read the same voltage. Report back what you find. - John
-
P0121, P0237, P0234, P1689,p0236 all at once.
I would do the W-T ground wiring mod first and then recheck the alternator for stray AC voltage. Also, I think the test should be done after the grid heaters stop their post cycling, otherwise you can have higher than normal readings. I am still running my original alternator (replaced brushes and bearings at 216,000 miles) Currently at 380,000 miles with no AC voltage issues. - John
-
Lift pump
The bouncing needle could be caused by a lift pump ball check valve vibrating or by a faulty gauge sending unit depending on your gauge setup. - John
-
Lift pump
The fuel pressure gauge should always be steady, regardless of the pressure reading. That needs to be corrected. A reading of 5 psi at WOT is fine for the needs of the VP44 injection pump. Moving to a 150 gph pump will raise the fuel pressure somewhat, but it does not change the volume of fuel returning to the fuel tank from the VP44. The VP44 has its own fixed displacement vane pump inside that controls fuel flow and pressure for the VP44's internal components, and for the fuel volume returning to the fuel tank. - John
-
Lift pump
That sounds about normal for a 100 gph lift pump. What is your lift pump pressure at wide open throttle driving with engine under full boost at around 2200 rpm? Is your lift pump mounted in the OEM position on the engine block? Or, is it frame mounted (a better option)? This site owner uses a frame mounted Air Dog lift pump. He will probably post the specific information about his pump in a little while. - John
-
Lift pump
What is it that you are not satisfied with? What are your mods? - John
-
Fast Idle Solenoid Install
I used that same system before, but I couldn't figure out how to drive the truck without the clamp falling out all of the time. - John
-
Fast Idle Solenoid Install
Back in July, I installed an adjustable idle solenoid on my truck. I wanted the engine to run at about 1150 rpm fast idle for winter time warm-ups and for summertime air conditioning during hot weather, should I need to be parked for a while and want to be comfortable. After some research, I decided on an AC Delco carburetor idle stop solenoid, part number 214-2138. It looked durable and the idle stop was adjustable. Under the hood I removed the APPS mounting bracket and fabricated a mount for the idle stop solenoid bracket to bolt to. I welded the new idle stop solenoid mount to the APPS mounting bracket. I installed the idle stop solenoid in a location that utilized the lever that operated the cable that would control shift points for an automatic transmission. Before I welded the mount onto the APPS mounting bracket, I did some measuring and I adjusted the solenoid plunger to its center position with the solenoid activated. I then determined where to weld the mount onto the APPS bracket. I installed a switch with an indicator lamp to operate the fast idle solenoid (not shown). Note - because of the mounting location, this install can only be done on a manual transmission truck. After the install was completed, I adjusted the fast idle to 1150 rpm using the threaded hex head adjusting screw. To operate - activate the fast idle switch. Slightly depress the throttle and the solenoid will snap into place giving the 1150 rpm fast idle. Turn off the switch and the engine rpm's drop back to normal idle. I decided to wait awhile before I posted this modification because I wanted to make sure that it worked reliably over a period of time. So far, it has passed the test. After strapping down three pallets of pavers in the 95° heat, the cab is nice and cool and the AC doesn't have to struggle to keep it that way. Definitely worth the effort. - John
-
Trans problems
So, what are the specs on the engine? Bore, stroke, peak torque and peak torque rpm, peak horsepower and rpm, etc? Does it come with a 5 spd manual transmission? Is there an auxiliary gearbox or a two-speed axle? I think you should at least put the Dodge Sport Headlights on it. - John
-
Trans problems
So, is this what you bought to replace your 98.5 Dodge Cummins truck? (Note that the photo is right side up) - John
-
1999 Dodge lift pump
@WesHawkins, the 10 amp draw sounds like a healthy lift pump. You are probably right regarding an overlooked fuse holder condition. - John
-
AC from AC?
@Andyba20, I think you are being led astray here. There are many, many things that affect compressor cycle time. Here are a few dynamic variables that occur every day and have a major affect on compressor cycle time in a fully charged and properly functioning air conditioning system: * blower fan speed * recirc or outside air * ambient temperature * ambient dewpoint * engine rpm * air flow across the condenser * sun load So, without naming some parameters, no one can say what is normal for compressor cycling frequency. On our 2nd generation trucks, compressor cycling is controlled by a low pressure switch downstream of the evaporator core. When refrigerant pressure falls to around 30 psi, the compressor will cycle off. 30 psi equates to about 30°F. This means that condensation from air passing through the evaporator core can collect and freeze onto the core which would impede air flow into the cabin if the refrigerant pressure remains at 30 psi or lower for a long period of time. When the cooling demand is low (75°F ambient air, 45° dewpoint, blower fan on low bringing in outside air, truck parked in the shade), the compressor will cycle frequently - I am not going say how frequently. When the cooling demand is high (85° ambient air, 70° dewpoint, blower fan on medium bringing in outside air, truck parked in the sun), the compressor will probably run continuously. It isn't "locked on", it simply cannot reach a low enough suction pressure to cycle off. Now, with all of that said, if your truck's cooling demand was high and it was hot outside and your compressor is cycling frequently, then it is likely there is a low charge of refrigerant in the system. Recovering the refrigerant and weighing what goes back in is the most accurate method for charging the AC system. - John
-
Bent Rear Sway Bar
I fully agree with you there. Not even close to being heavy duty. - John
-
1999 Dodge lift pump
Personally, I have never found a multi-meter with a DC amp clamp connector to be reliable for direct current measurements. I think you are having the same issue with your meter. From a couple of other sources, 12 amps was the response for current draw for stock lift pumps. Years ago my truck had a factory in-tank lift pump with relay installed under warranty by a Dealer. The power to the relay was supplied by an added 20 amp fuse. If the lift pump truly only drew .5 to 1.5 amps, then a 5 amp fuse would be more than adequate. There is a positive displacement vane pump (called the feed pump) inside the VP44 injection pump. It is this pump that drew the fuel into the VP44 without the lift pump operating. As long as there is not a blockage from the fuel tank, the engine will run. The purpose of the lift pump is only to supply a positive pressure at the inlet of the VP44. - John
-
1999 Dodge lift pump
Not sure how you are testing for current draw, but those numbers are way low. I don't think they are real. The current draw should be more like 8-12 amps. I would suspect that you are getting a severe voltage drop across the fuse connections while the pump is running, which will generate lots of heat, even from a perfectly good lift pump. Since the fuse holder was already damaged from a previous situation, the fuse holder needs to be replaced. I would jumper the existing fuse holder with an in-line 20 amp fuse and re-test the lift pump. If the fuse holder still gets hot, then you have a lift pump that is beginning to seize. If the fuse holder stays cool, then you have found the problem. - John
-
Bent Rear Sway Bar
Your hitch receiver should be a Class 4 - 1000 lb / 10,000 lb with weight distribution, but only 500 lb / 5,000 lb weight carrying. Horrible safety factor. Is the label still on your hitch receiver? - John
-
Dodge 2500 OEM Hitch Receiver Failure
Yup, looks to be in good condition. - John
-
No buss with new ecm
There is a ground wiring modification in the Articles section on this site that is called the W-T ground wiring mod. This mod primarily reroutes the alternator output wire to the passenger side battery and addresses some poor electrical grounds that could affect the PCM and the ECM. In particular, there is a factory ground splice that isn't even crimped near the front left side of the engine. One of the wires in the splice is a ground for the ECM. I am not saying that this will fix your problem, but it is an important step for protecting computers and electronic devices, such as the PCM and the ECM. Double check wiring connectors for the PCM and ECM and any associated connectors for pins that may have been pushed back inside the connector and are not making contact. Hopefully, you will hear back from your ECM repair guy. - John
-
Dodge 2500 OEM Hitch Receiver Failure
I guess that relates to the geographical differences of where our trucks have been. I didn't have to deal with any rust - no broken tabs, the bolts just came right out. Just curious, did you see any evidence of separation at the rear of the OEM hitch receiver (like in the above photo)? I realize you didn't use it much, so it was probably okay. - John
-
No buss with new ecm
There are many things that can cause an engine crank, but no start condition. What made you focus on the ECM? What are the symptoms? Did the problem come on suddenly? Any codes set? Any information you can provide about how the truck was running prior to the problem as well as some history on the truck would be helpful. - John
-
Dodge 2500 OEM Hitch Receiver Failure
@Max Tune, I don't know any source of information regarding the strength of the truck frame where the hitch receiver mounts. I tried to get that information from Etrailer.com, but I just got a canned response. Personally, I think the frame is far stronger than the hitch receiver. I saw no signs of stress whatsoever on the frame after removing the OEM hitch receiver and inspecting the frame. The new Curt hitch receiver is six inches longer consequently using more of frame's strength. I seriously doubt that I will ever have any hitch issues again. However, I will perform better inspections in the future. - John
-
Bent Rear Sway Bar
Yes bumper pull, well actually truck hitch receiver pull. You may not have read my post regarding my OEM hitch receiver failure. I have replaced the hitch receiver with a Curt Class V hitch receiver which allows for a much better safety margin. OEM hitch receiver: Curt hitch receiver: - John
-
Bent Rear Sway Bar
You may recall that during the late '90''s and early 2000's, trucks were being sold with the "Camper Special Package" option. This included auxiliary rear leaf springs and a rear anti-sway bar for carrying slide-in truck bed campers. Otherwise, trucks did not come with those options, even if they had the trailer tow package. - John
-
Bent Rear Sway Bar
I have removed my OEM rear anti-sway bar. I no longer have my truck camper (high center of gravity load), so the rear anti-sway bar is not needed. Get a little better ride with the truck empty on certain roads. The truck tows very well without the bars. Just arrived home from a round trip to Boise picking up two pallets of pavers. GCW coming home at 18,000 lbs. - John
-
dash lights and gauges powering up with key off
For sure, I think you need to call in an exorcist. Until then, don't park the truck by your house. If that doesn't work, then try this. There are wires that break or chafe from flexing over time in the tilt wheel area. You can remove the lower cover and inspect these wires. I have had to repair some of these wires over the years. - John