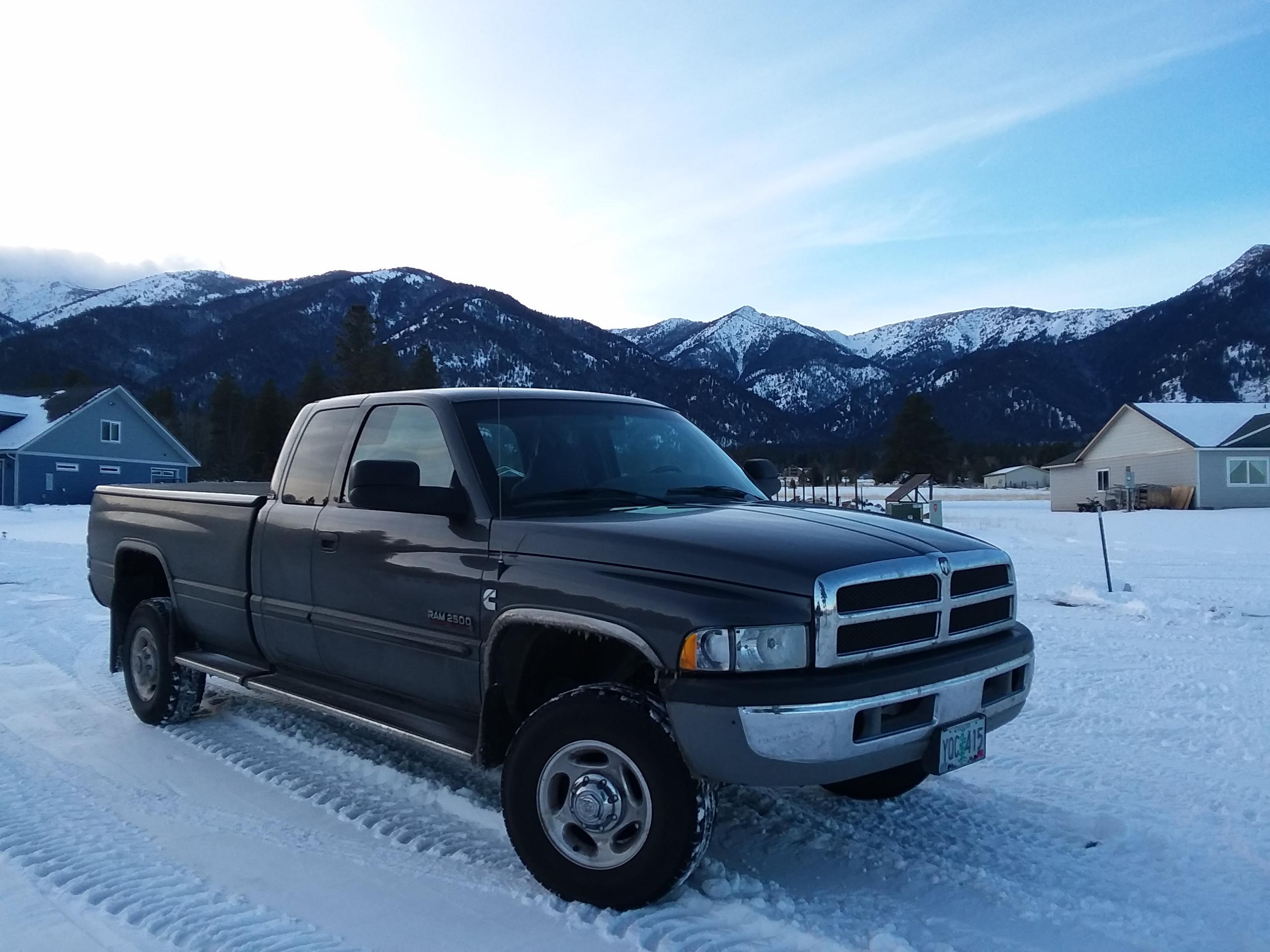
Everything posted by Tractorman
-
Weather starting to improve, Days getting Longer...
Spring has been postponed at my house for awhile. Ten inch snowfall overnight the night before last. But, it's okay as my tractor is equipped with a snow pusher. - John
-
Fass install
Your photo shows four wires connected to the module. This indicates there may be an in-tank pump. - John
-
1991 W250 12V, wiring nightmare
Good job! - John
-
P1291 No temperature rise seen from intake air heater
@Nomad2015, I apologize for being "harsh". That was not my intention. I will stay out of the discussion and maybe others can help you. - John
-
98.5 crank no start
So, the belt came off and you turned the engine off. Why did you disconnect batteries and remove fuses? I am missing the relationship here. - John
-
P1291 No temperature rise seen from intake air heater
I was hoping that you were going to answer my question from my previous post. You also haven't verified that you have battery voltage on the alternator output wire with a test light. Answering questions and performing tests are very important for moving forward with diagnostics. At this point, I still don't know which wire you left disconnected and if this wire is still disconnected. Ensure grid heaters are disconnected. If you have all of the alternator wires connected (the question that is still unanswered) and there is battery voltage at the alternator output terminal (verified with a test light), then start the engine. If battery voltage rises and steadies at around 14 volts, then the alternator is charging. - John
-
P1291 No temperature rise seen from intake air heater
Need to be clear here. There are three connection points on the back of the alternator. The two small connection points are for the two small field wires. The large insulated connection point is for the alternator output wire which has an uninterrupted path to the driver side battery. Is this the wire you left disconnected? If so, the alternator cannot deliver current to the battery. In fact, if any of the three wires are left disconnected, the alternator cannot charge the batteries. Also, there may or may not be a ground wire connection on the back of the alternator. - John
-
P1291 No temperature rise seen from intake air heater
Do not replace any parts yet! If you are in fact seeing 60 volts DC at the alternator output with everything properly connected, this means that continuity has been lost somewhere between the alternator output and the driver side battery. The 140 amp fuse is in this path along with the associated wiring. Use a test light with an incandescent bulb (not a multi-meter) and perform the following test: With engine switched off, clamp one end of the test light to a battery ground and touch the other end of the test light to the alternator output. The test light should light up brightly. If it does not, you now know where to start looking. - John
-
1991 W250 12V, wiring nightmare
Don't replace anymore parts! A simple test light (with an incandescent bulb) and a wiring diagram are your friend. It is definitely possible that a previous owner added some additional wiring as @Mopar1973Manmentioned. I would start troubleshooting by connecting a test light to the fuel pump solenoid and begin disconnecting non switched OEM power sources until the light goes out. If it doesn't go out, then I would start looking for additional wiring from an non switched source. - John
-
Replacing head gasket
Looking for "cause and effect" here. Did the cross-over tubes with a good seating pattern match up with the cylinders that were firing? Hopefully, the shop kept track of which injectors and cross-over tubes came out of which cylinders. - John
-
Fass install
I believe it is a vent / rollover protection valve. It should be present on all fuel modules. I have one on my fuel tank module. - John
-
Why I "tinker" with my truck
W-T believes that only two things need to be in a shop. You've seen one (his truck) - the other...., - John
-
Why I "tinker" with my truck
Everyone diagnoses things differently. You probably just tightened the bolts and figure all is well. I try to go directly to the root of the problem. I would have set up a security camera system to find out who was trying to steal my exhaust manifold. Good job spotting that loose bolt! - John
-
98 standard cab latch won't tighten
The accident could have caused more damage than what was observed - not that unusual. The impact likely distorted the door frame in a manner that is creating your problem. You will have to study it some to find what is bent or twisted, then come up with a way to repair it. Sometimes you can get creative and straighten something that seems impossible to straighten. It is better to fix what is wrong rather than trying to make the door fit what is wrong. Are you doing all of the work yourself? - John
-
01 24v dead in the water....
@Basranabread, good job using the test procedures you selected. You drew an informative conclusion. Let us know when you get the new pump installed. - John
-
01 24v dead in the water....
There is no doubt that recirculating the fuel inside the lift pump generates heat, but how much heat is only a guess - mainly because we don't get any real specifications for these lift pumps which leave too many variables. Then we have the fixed displacement vane pump (inside the VP44) with its own regulating valve that returns fuel back to its own inlet - so more heat generation. I am fairly sure that vane pump doesn't recirculate as much fuel as the lift pump without a dedicated return, but it does recirculate the fuel at a much higher pressure - somewhere between 100 psi to 300 psi. So, heat will be generated there as well. Again, how much? The heat generated from recirculation in both pumps could be approximately calculated IF we had information providing how much fuel was being recirculated at a given pressure in the respective pumps. The formula I used when I was in the hydraulic industry was gpm x psi / 1714 = hp. Horsepower would then be converted to watts to represent heat. Of course, these calculations were done using hydraulic oil, but there still should be some similarities. So, let's pretend there is 60 gph at 15 psi recirculating inside the lift pump. Another 20 gph is flowing out the lift pump and through the VP44 and returning to the fuel tank on this idling VP44 engine. In this example, 60 gph would be 1 gpm, hence 1 gpm x 15 psi / 1714 = .009 hp or 6.5 watts. That would be 6.5 watts of continuous heat being added to the recirculating fuel inside the lift pump. But some of that fuel would be mixing with the incoming and outgoing fuel at the rate of 20 gph, consequently carrying some of that heat away. As engine load and engine rpm increase, more fuel will be demanded by the VP44 internal vane pump and injectors, so lift pump pressure will fall, and less fuel will be recirculated inside the lift pump, which in turn will reduce heat being added to the recirculating fuel. I have no idea how accurate these calculations are, but I think it should at least give some idea as to what is going on. Feel free to punch lots of holes in this line of thinking. - John
-
Fix it while in there?
I would just do the tappet cover for sure. It will make access easy for removal / installation of the tappet cover - something you don't want to fight. - John
-
01 24v dead in the water....
@LorenS, I have a similar setup - a frame mounted FASS without a dedicated return line. Not sure of the volume because it is a used pump, but I think it is about 65 gph. I know it does heat the fuel some. I modified my VP44 fuel return line by installing a directional valve to allow fuel to return into the fuel basket during the winter months and to allow the fuel to return into the fuel tank filler neck during the summer months. I have no way to monitor fuel temperature other than to place my hand onto the lift pump body. I can definitely tell the difference when I switch the fuel return valve, though. I am fairly certain that Mopar1973Man's lift pump dedicated fuel return line and his VP44 fuel return line return fuel well away from the fuel basket, consequently he runs low fuel temperatures. - John
-
01 24v dead in the water....
@Great work!, you make a good point here. I did mention a possible lift pump problem in my previous posts. But, what you say about a poor mechanical connection could certainly match the symptoms. Good observation on your part. - John
-
01 24v dead in the water....
I very much agree with everything you stated. But, in this case I don't think his symptom is caused by an air leak. Here is why. He performed the free flow test into a five gallon bucket. He reported that the bucket filled to about halfway in one minute. That volume of fuel coincides with the 150 gph rated flow specification for that particular lift pump. An air leak would have certainly showed during this test because this would have been the time for air to have been drawn in because this is the only time the lift pump can flow maximum fuel through the suction line, hence the largest pressure drop. He did not report a stream of air saturated fuel. And, if the fuel would have been saturated with air, I don't think the bucket would have been as full. Once the lift pump is reconnected to the fuel system to perform as a normally operating lift pump, it will never flow 150 gph again. The maximum flow from the fuel tank to the inlet of the lift pump would be less than 50 gph on a stock or mild tune, even if the engine is placed under a demanding load. This is because even with injectors at max fuel flow and engine at max rpm, the sum of injector fuel consumption (approximately 10 gph) and the return flow from the VP44 (approximately 30 gph) via the internal vane pump would be less than 50 gph. Also, if enough air is entrained in the fuel to cause loss of engine performance under a load, the engine would likely die when the throttle is released to idle. At best, the engine would not restart without bleeding some injectors. One more thing to add - in my experience I have always seen lift pump pressure even when there is a fair amount of air in the fuel system. The lift pump will pump fuel entrained with air quite easily. It is the fuel injection pump that can't deal with the compressible solution. @Basranabreadreported a few times that fuel pressure was at "0" psi. To me, a "0" psi reading is indicative of a restriction on the inlet side of the lift pump, not entrained air. Now, of course, if it turns that his problem is air getting into the fuel system, you can just disregard everything I have posted - consider it as "buffoonery". I know I will. - John
-
01 24v dead in the water....
I have seen that video. As I recall, the video does not replicate what is going on in the VP44 fuel system. In the video I believe the pump outlet is completely blocked forcing all fuel to flow over the regulating valve and return to the lift pump's inlet. With this condition sustained, I can understand the continuous heat generation will begin to vaporize some of the fuel and cavitation could occur at the inlet. But, this is not the real life condition that the lift pump is operating in. In the VP44 fuel system, there is always a minimum of 18 gph returning from the VP44 injection pump to the fuel tank and that minimum flow occurs at engine idle. The internal fixed displacement vane determines that volume. This means there is always a minimum of 18 gph leaving the outlet of the lift pump on an idling engine. The fuel that is recirculated within the lift pump housing (over the regulating valve and back to the inlet) is mixed with incoming fuel which will quickly stabilize heat buildup inside the lift pump. In normal designed operation the heat will not rise to the point of vaporizing fuel, so conditions for cavitation will not occur. As engine throttle is increased, more fuel will return to the fuel tank, thus more fuel will be leaving outlet of the lift pump, consequently less fuel will be recirculating inside the lift pump housing. The point that I am trying to make is that the OP has installed a new lift pump that does not use a dedicated return line. If his lift pump is cavitating, it because there is a restricted suction - whether it be in the lines, tank, or inside the lift pump - not because there isn't a dedicated return line. The link below gives a good explanation of cavitation vs. aeration. Only need to view the first couple of minutes for the explanation. https://www.google.com/search?client=firefox-b-1-d&q=airdog+caviatation+video#fpstate=ive&vld=cid:72664d2a,vid:hWeQUDyDEnY - John
-
01 24v dead in the water....
A lift pump without a dedicated return line flows 100% of its displacement from its internal discharge location. What fuel doesn't leave the pump outlet to the VP44 gets returned to its own inlet internally. There is no cavitation. A lift pump with a dedicated return line also flows 100% of its displacement from its internal discharge location. What doesn't leave the pump outlet to the VP44 gets returned to the fuel tank. There is no cavitation. Cavitation only occurs when when the pressure on the inlet side of the lift pump falls so far below atmospheric pressure (usually greater than 15"HG vacuum) that some of the fuel will vaporize (changing from a liquid state to a vapor state) and expand before it enters the lift pump inlet. When that fuel vapor passes to the pressure side of the lift pump, the fuel vapor will suddenly collapse as it condenses to a liquid state. That sudden collapse (always in the same location) causes an implosion that is so severe that pieces of metal can be removed repeatedly at the surface of where the implosion occurs. Any pump can suffer from cavitation if there is a severe restriction on the inlet side of the pump. Neither type lift pump is truly deadheaded, even if you block the discharge port - one has an external dedicated return line, the other returns fuel to the inlet internally, but BOTH will flow the same volume fuel over the regulating valve if they are equal displacement pumps. As far as I know, Air Dog, FASS, and Carter lift pumps are all positive displacement pumps. They cannot be truly deadheaded- if they are truly deadheaded, the pump will be forced to stop rotating, or a fuse will blow, or something is going to break. And, yes, there are benefits to having a lift pump with a dedicated fuel return line, but cavitation is not one of them. - John
-
01 24v dead in the water....
You could have a faulty lift pump or you could have a random very restrictive blockage between the fuel tank and the inlet of the lift pump. I don't think it is air getting into the suction lines. I am leaning toward the blockage. There is a fixed displacement vane pump inside the VP44. With the engine idling, that pump is returning fuel at about 18 gph to the fuel tank via the overflow valve. Under full rpm the vane pump will return fuel at about 30 gph to the fuel tank. With the engine off and the lift pump running, very little fuel is returned to the fuel tank because the fuel is being forced around the very small clearances of the vanes in the non-rotating vane pump inside the VP44. I don't think you need to drive the truck to make the symptoms happen. Try this: Bring the engine to 2500 rpm and hold it there. See if the fuel pressure begins to drop like it did on your test drive. If it does, then perform the following test: * Run a fuel line from a 5 gallon container filled with clean diesel. Connect the fuel line directly to the inlet of the lift pump. * Start the engine and let it idle to let the fuel pressure stabilize. * Bring the engine to 2500 rpm and hold it there If the fuel pressure drops slightly, but remains steady at 2500 rpm, then you know you have a suction problem. If the fuel pressure at 2500 rpm behaves like it did on your test drive, then you know you have a lift pump problem. If you can't make the symptoms happen, you may have to secure the 5 gallon fuel container in the bed of the truck and drive the truck to duplicate the symptoms. Just make sure you are being safe. When the lift pump is operating normal, what is the fuel pressure? - John
-
Weird Defueling Issue, any advice can help.
Definitely let us know what the outcome is. - John
-
Weird Defueling Issue, any advice can help.
Hmmm, seems like there are three questions here. Since I think you have been driving the truck already, you probably should tag and insure it. As far as driving the truck with the existing P0216 code, if the truck were mine, I would drive it for awhile before replacing the VP44. In fact, my truck set the P0216 code back in 2004 and the engine would de-rate at times. I drove the truck one more year (for over 20,000 miles) before I had the VP44 replaced under warranty. I learned how to get around the de-rate mode (kind of like you have learned with your truck). Since your particular problem is rather unique, driving the truck for awhile may give you time to try some other ideas to solve the problem. I can't see that it would hurt anything and time is your friend. If it turns out the pump needs to be replaced, so be it - at least you will have had the time to come up with other possible solutions. It will also give you time to find out if there are any other problems associated with the VP44 when the truck is running in the warmed up mode. It would be interesting to let the truck fully warm up and then clear the P0216 code. Immediately, start driving the truck for an hour or so and then, before the engine has a chance to cool down, recheck to see if the code P0216 has returned. - John