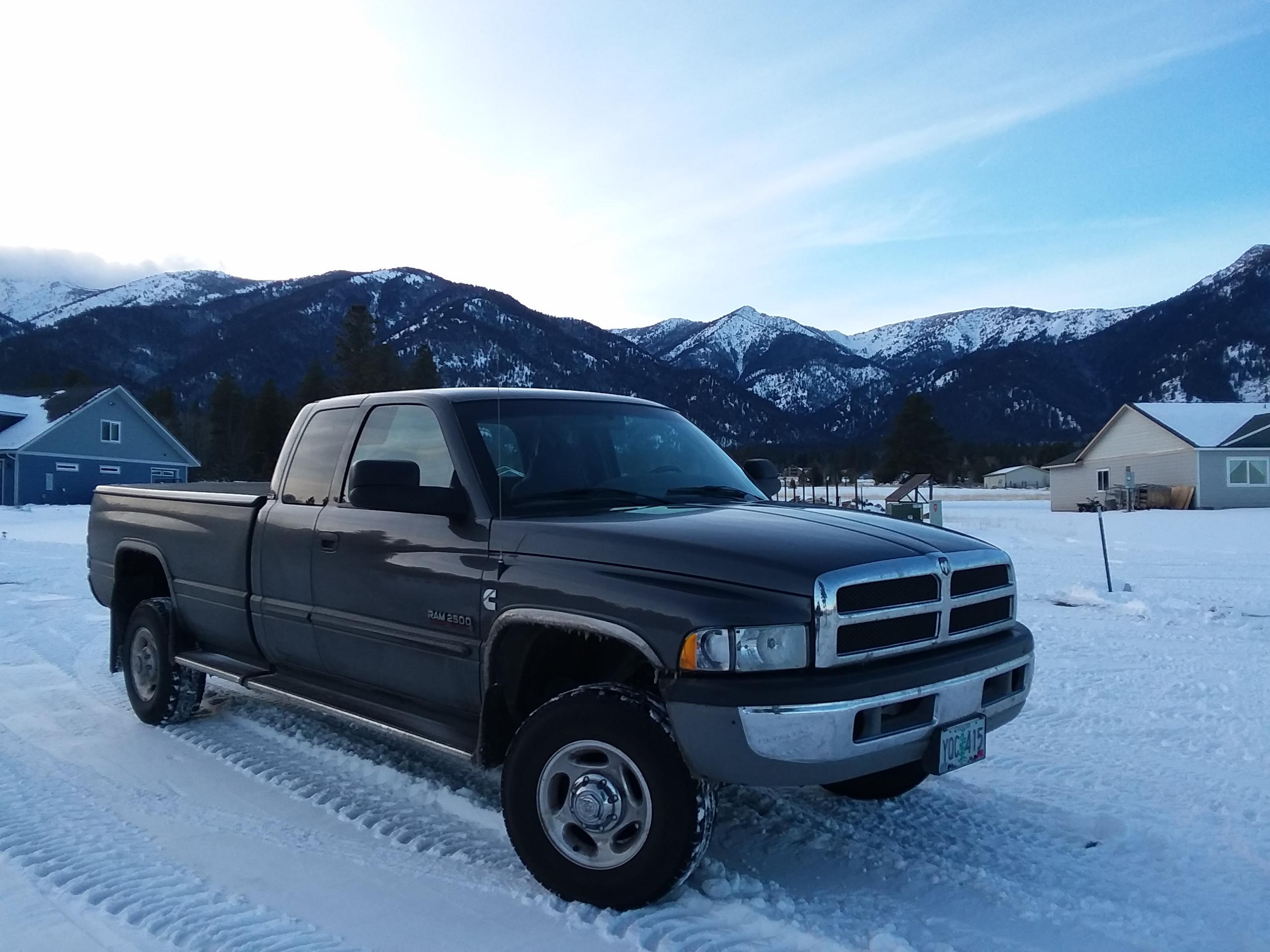
Everything posted by Tractorman
-
Vp44 Injection Pump advice
Yes, it is likely. I would verify that you have good lift pump flow, though. The P2016 code is usually a timing related code and will de-rate the engine power until it corrects itself. The advanced timing that you heard at the fueling station triggered the engine de-rate and set the code. I would not purchase the VP44 that you are asking about at Diesel Auto Power. That pump comes with a re-manufactured PSG and it is not calibrated to the pump using the Bosch 815 test stand (about a 4 hour test, I think). I believe DAP does sell a more expensive model with a new PSG that is calibrated to the pump. Maybe @Mopar1973Man can verify. You are probably okay to continue to drive the truck if you need to - you can probably change your driving techniques for the interim which will help avoid the engine de-rate. I had the same symptoms on my truck about 20 years ago. I learned how to drive the truck to avoid the engine de-rate. I drove it for another year (20,000 miles) before I had the VP44 pump replaced under warranty at the time. John
-
1689 with HVAC
Most of the the HVAC circuit consists of switches in the ground side and there is a blower motor relay and an AC clutch relay as well as a refrigerant low pressure switch. There is a 12 volt supply to the blower motor and the AC clutch relay. I would be more inclined to trace wires in the CCD bus circuit as those pair of wires can only be connected to components operated within CCD system - nothing else. Not that Joint Connector #7 is a hub for connecting to many of the CCD components in the system. John
-
1689 with HVAC
Maybe the previous owner has messed up the wiring somehow. It may be worth physically tracing the CCD bus circuit to see if any wiring has been damaged or tapped into. John
-
1689 with HVAC
Running the 10 gauge wire from the dash to the negative battery terminal was a good test, but your test results indicate that the body ground is NOT the problem. As far as I know, there are only two ground connections for the HVAC control panel and the blower motor - ground # 200 and # 201 - both are connected to the dash, just separate locations. Not sure where to got next. John
-
1689 with HVAC
You didn't answer any of the questions regarding how you did your voltage drop test. A voltage drop test will give you conclusive information regarding whether or not the circuit you are testing is good or bad. It is one of the best electrical tests that one can do, but is also one of the least understood. Reconnect the blower motor ground in the center dash. Connect your multi-meter to that ground and the battery post ground. Set the meter to DC volts on the 00.00 scale. Start the engine and turn the blower fan to high. Read and record the voltage drop. Any voltage above .1 volts during this test is considered to be excessive - the higher the number, the worse the condition . If this is the case, this means that the dash / body is not at full ground potential. This will affect the operation of any electrical devices that use the body as a ground. I like doing voltage drop tests when I find it difficult to solve an electrical problem. Voltage drop tests don't lie, but you do have to be meticulous when you perform them. The best part of using this test is that you do not have to disturb any electrical connections in order to perform the test. Done properly, voltage drop tests save time and provide accurate conclusions. Maybe you already know all of this, but I can't make that assumption. I believe there are two body-to-battery grounds for the driver side battery. One is located on the body between the driver side battery negative post in the headlight area and I think the other is under the battery tray. John
-
1689 with HVAC
Are you doing your voltage drops correctly? Is the engine running with lots of electrical devices turned on to full power? If you are doing this test without the engine running and no electrical devices are operating, then the results of this test are meaningless. A voltage drop in a normally operating electrical circuit will always register more that 0.00 volts. Typically, you would see up to .1 volt drop while a good circuit is operating. Since you are having the strange issue of setting a P1689 with no buss on the CCD when you turn your HVAC blower on, this would be a good place to perform a voltage drop test. Start the engine and turn the blower fan to "high" speed. You will want to measure the voltage drop from ground connection # 201 (Instrument Panel Right Center Support) to the negative post of a battery. The blower must be operating on high speed. A .1 volt (or less) drop would be considered normal - a 1.5 volt drop would be a problem. If your meter reads 0.00 volts, then you have a poor connection with your meter. John
-
1689 with HVAC
I suspect that you may have a poor body to frame ground, or poor body to battery ground. Since the blower motor switch grounding and the data link grounding are in the body ground circuit, a poor body to frame or body / frame to battery ground connection could influence the CCD circuit. Body ground # 200 (located on the driver side inside the cabin) and engine ground # 107 are part of the CCD circuit. You could temporarily run a jumper cable from the body directly to the battery ground post and then operate the HVAC blower fan to see if the symptoms go away. John
-
1689 with HVAC
I think you could temporarialy wire in a LED lamp to the OR/BK wire from Connector #2, terminal #11 of the PCM. Wire the other side of the LED to ground. The lamp would be on all of the time after the engine is started, but it would go out when the torque converter is commanded to lock up. I don't think it would cause you any side effects and it would do what you want. John
-
Valve lash
No, they shouldn't be tight. I think you are worrying about a potential problem that does not exist. Your explanation of your concern was well written, and I think accurate. The two valves that you referenced were closed, but the #5 and #2 pistons were 120° on their approach to TDC. The cam lobes were still ramping down or up (depending which valve is being referenced) so the clearance was not the set clearance (because of the ramp). BUT, the clearance would be a normal clearance. John
-
Valve lash
I didn't say that quite right. The intake valve would be fully closed, but would not have reached the full .010 clearance yet. John
-
Valve lash
I think everything is normal. Since you were at TDC on the compression stroke #6 cylinder, that means the cylinder #5 (next in the firing order) would 120 degrees away from arriving at TDC compression stroke. That intake valve would not be full closed until after BDC, which could explain the .003 inches. This hurts my brain. I think #2 cylinder is behaving the same way - just in the exhaust stroke. John
-
No Start problems
Dave, this is what I used. There are lots of choices - just make sure that the free flow direction requires very little pressure differential to flow. John
-
No Start problems
There are a couple of things you can do for better reliability for the VP44. First, get over the idea that 14 psi lift pump pressure is needed to ensure there is always return fuel flowing to the fuel tank from the VP44 (if you still believe this). The lift pump pressure has no influence whatsoever on the quantity of return fuel from the VP44. The VP44 return fuel flow is controlled only by the VP44's internal vane pump and its regulating valve (over 100 psi) and the 14 psi overflow valve. Being that the internal vane pump is of fixed displacement design, the pump's output flow is always the same at a given engine rpm - regardless of engine load or lift pump pressure. When I performed VP44 fuel return flow testing, I installed a lift pump bypass circuit with a one-way check valve to demonstrate that turning off the lift pump did not change the return flow volume from the VP44. I did a 30 mile road test without the lift pump operating and the engine performed flawlessly under all operating conditions. So, when I reconnected things after my testing, I thought why should I remove the lift pump bypass circuit with the one-way check valve? If the lift pump stops working, the bypass circuit would go into action and continue to feed the VP44 pump - a win, win situation. If a lift pump should fail on a road trip, my low fuel pressure indicator lamp would light to make me aware of a problem, but I could continue driving to a place to do the repair without harming the VP44. For lift pump pressure sensor reliability (fuel gauge or warning light system) install a snubber and 24 inches of grease hose with 1/8" NPT fittings on each end. This arrangement will greatly increase the life sensors. I used a pressure switch for a warning LED light on the dash. John
-
5v reference circuit? Ecu? All of the problems!
Success! John
-
No Start problems
Glad to hear the truck is up and running well. Looks like your first VP44 lasted about 100,000 miles longer than the second one. My first VP44 failed at 87,000 miles and the second one is still going at 397,000 miles on the odometer, so 310,000 miles on the second Vp44. I won't be surprised to see a failure in the near future, but that's okay - it has been reliable and has had a long life. John
-
tuning recommendations
I believe a stock 2016 truck came with 3.42 gears. Did you make a change? I don't have the answer, but my neighbor would like to do the same with his 2011 truck. I am not sure how that would work, because even in the manual mode, the gear number displayed in the dash isn't necessarily the gear the transmission is in - it is the gear the transmission is limited to up shifting to. Which transmission do you have - 68RFE or the Aisin? - John
-
47RE kicking out of O/D
Good thinking on your part! - John
-
Ford 6.7L issues
You guys!...., that piston is not in backwards - that cylinder is only supposed to be used when backing up! - John
-
ECM failure
- John
-
2006 Dodge Ram 3500 - Thor Project
8°F below zero at my house this morning, 20°F below zero at the airport reporting station (National Weather Service). - John
-
2006 Dodge Ram 3500 - Thor Project
It is possible. I have worked on a few common rail Dodge Cummins engines. What I have found is that it can be very difficult to troubleshoot this fuel system, even with the use of the right diagnostic equipment. You may be fairly certain that a high fuel return rate is occurring, but that could be caused by a leaking PRV, a CP3 pump, one or more injectors, crossover tube / tubes not seating, etc, or even a combination of the these. It is for the above reasons that I would want to prove (which can easily be done) that there are no issues with fuel supply, first - then move on to other diagnostics if the fuel supply is good. One thing for sure..., if there is a problem with the fuel supply, then the high pressure part of the injection system cannot run right. - John
-
2006 Dodge Ram 3500 - Thor Project
Pretty much the same as our VP44 engines. When my VP44 replacement and in-tank lift pump mod was done by the dealer under warranty, it was replaced with the same in-tank pump that was used for the common rail system. I agree - that's why I am recommending temporarily plumbing the lift pump to a remote fuel container and then going for a test drive. - John
-
2006 Dodge Ram 3500 - Thor Project
The lift pump pressure falling to zero at WOT may be trying to tell you something. I think it is time for a different approach. I would rig a five gallon container with fuel supply and return. I would anchor the container in the bed of the truck and go for a test drive and document the results. - John
-
47RE kicking out of O/D
@TCMagnum, Good job determining that that it is actually downshifting to 3rd gear. I don't think you have an AC noise issue, although performing the W-T ground reference mod would be a good idea, if you haven't done that already. Usually, AC noise affects torque converter lockup stability which is the problem most people have. When the transmission does an unwanted downshift, does the torque converter lock up, or does it stay unlocked? What about the code - P0122 Accelerator Position Sensor (APPS) Signal Voltage Too Low, is it still there? If it is, I would get that cleared up first. - John
-
Pilothouse/RAM3500 build
I had a feeling that you would go back to the first running board after you had better results with the second running board. That's not "OCD" - that's a "good decision"! - John