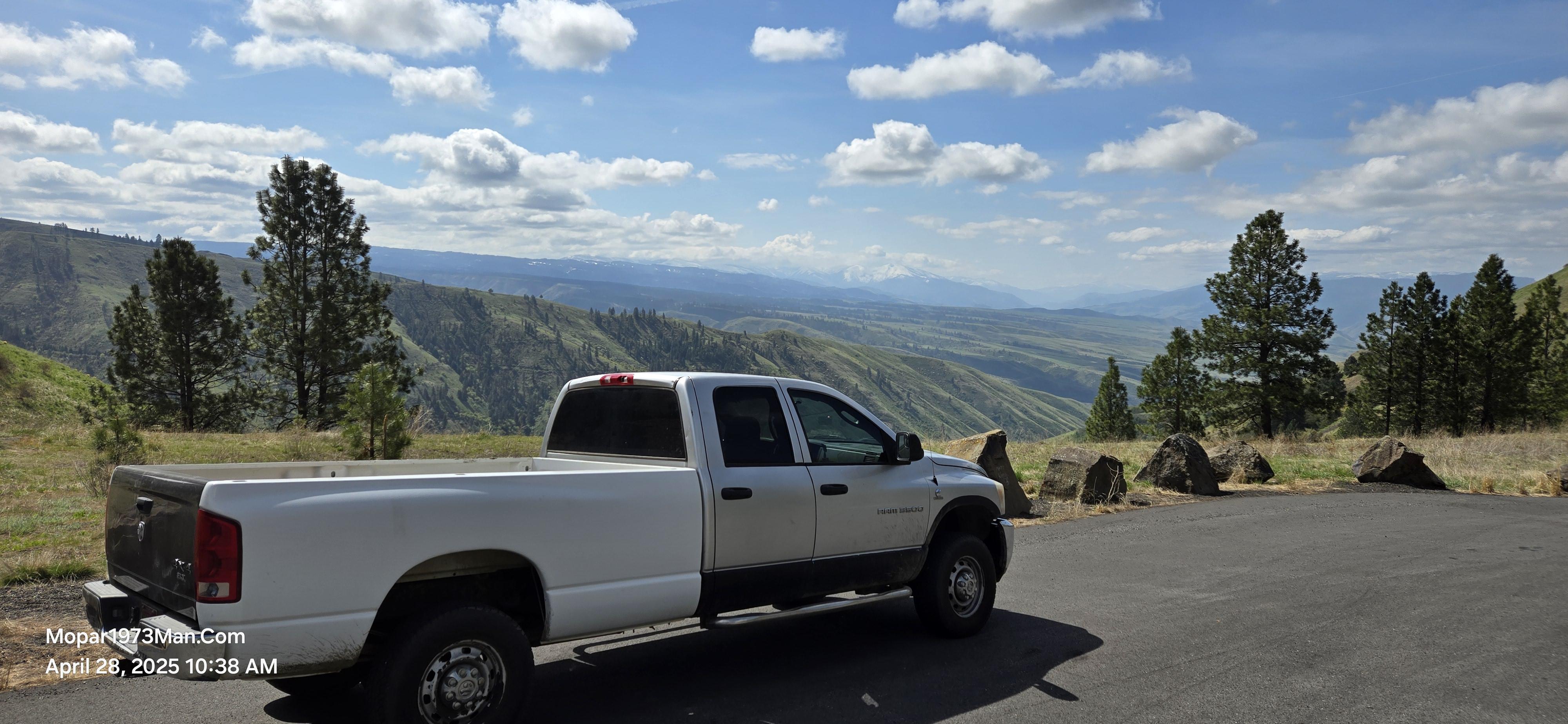
Everything posted by Mopar1973Man
-
2nd VP in 2 Weeks
Be aware all modules are VIN locked so if there is a mismatch of module VIN numbers weird thing start happening.
-
Pilothouse/RAM3500 build
Ummm... I'm going to need lot more funding to make that happen...
-
Fuel Article - AirDog Draw Straw Installation
More common than you think. This is why I made the video and showed how I've been doing it all these years without any issues. You should NEVER cut the straw at a angle it will cause more issues than its worth. It should always be cut straight. PERIOD. If I was going to notch it I cut it straight then notch with a grinder really easy and not more than 1/8 of inch deep.
-
Pilothouse/RAM3500 build
No...
-
P20B7 - (Diesel Exhaust Fluid) Reductant Pump Heater Control Circuit Low
P20B7 - (Diesel Exhaust Fluid) Reductant Pump Heater Control Circuit Low Theory of Operation The Powertrain Control Module (PCM) controls the DEF Heaters via datalink communication with the Diesel Exhaust Fluid Dosing Control Unit (DEF DCU - sometimes referred to as the Selective Catalytic Reduction (SCR) Module). The DEF DCU receives two voltage supplies: One from the SCR Relay1 (which is activated upon startup). And, the other is a fused B+ supply. The DEF Tank electric heater and DEF Line Heater power supply and ground circuits are wired directly to the DCU. The DEF Tank Heater is integrated into the DEF Supply Pump assembly and is not serviced separately. Activation of the DEF Supply Line and DEF Tank Heaters operate independent of each other. Line heating is based on the Ambient Temperature Sensor input and Tank heating is based on the DEF Tank Temperature Sensor value. Heating of the Line or Tank Heater is initiated when the corresponding temperature value is below -5°C (23°F). Heating is stopped when the corresponding temperature value goes above -4°C (24.8°F). The DEF Dosing Control Unit monitors these inputs and reports them to the Powertrain Control Module (PCM). The PCM will illuminate the MIL lamp after this diagnostic runs and fails. The PCM will turn off the MIL light when the monitor runs and passes in three consecutive key cycles. When Monitored: With the ignition on, while the SCR Module Heater is commanded off. Set Condition: The DEF Dosing Control Unit detects low voltage on the SCR Module Heater Supply circuit. Possible Causes SCR MODULE HEATER SUPPLY CIRCUIT SHORTED TO GROUND SCR MODULE HEATER SUPPLY CIRCUIT OPEN/HIGH RESISTANCE DEF DOSING CONTROL UNIT POWER DISTRIBUTION CENTER Always perform the Pre-Diagnostic Troubleshooting procedure before proceeding. (Refer to 28 - DTC- Based Diagnostics/MODULE, Powertrain Control (PCM) - Standard Procedure). 1. ACTIVE DTC NOTE: If DTC P21CA, P21CB, or P21CC are also active, diagnose and repair that DTC before continuing with this test procedure. 1. Turn the ignition on, engine not running. 2. With the scan tool, actuate the DEF Line Heater or Tank Heater Override Test. 3. With the scan tool, View DTCs. Is the DTC Active? Yes • Go To 2 No • Perform the INTERMITTENT CONDITION - 6.7L. (Refer to 28 - DTC-Based Diagnostics/MODULE, Powertrain Control (PCM) - Standard Procedure). 2. CHECK THE (F203) SCR MODULE HEATER SUPPLY CIRCUIT FOR AN OPEN/HIGH RESISTANCE 1. Turn the ignition off. 2. Disconnect the PDC C5 harness connector. 3. Disconnect the DEF Dosing Control Unit C1 harness connector. 4. Measure the resistance of the (F203) SCR Module Heater Supply circuit between the PDC C5 harness connector and the DEF Dosing Control Unit C1 harness connector. Is the resistance below 5.0 Ohms? Yes • Go To 3 No • Repair the (F203) SCR Module Heater Supply circuit for an open or high resistance. • Perform the POWERTRAIN VERIFICATION TEST - 6.7L. (Refer to 28 - DTC-Based Diagnostics/MODULE, Powertrain Control (PCM) - Standard Procedure). 3. CHECK THE (Z905) SCR HEATER RELAY 1 GROUND CIRCUIT FOR AN OPEN/HIGH RESISTANCE 1. Measure for continuity between (Z905) SCR Heater Relay 1 Ground circuit between the PDC C5 harness connector and ground. Is there continuity between (Z905) SCR Heater Relay 1 Ground circuit and ground? Yes • Go To 4 No • Repair the (Z905) SCR Heater Relay 1 Ground circuit for an open or high resistance. • Perform the POWERTRAIN VERIFICATION TEST - 6.7L. (Refer to 28 - DTC-Based Diagnostics/MODULE, Powertrain Control (PCM) - Standard Procedure). 4. CHECK THE (F203) SCR MODULE HEATER SUPPLY CIRCUIT FOR A SHORT TO GROUND 1. Measure the resistance between ground and the (F203) SCR Module Heater Supply circuit at the DEF Dosing Control Unit C1 harness connector. Is the resistance above 10k Ohms? Yes • Go To 5 No • Repair the (F203) SCR Module Heater Supply circuit for a short to ground. • Perform the POWERTRAIN VERIFICATION TEST - 6.7L. (Refer to 28 - DTC-Based Diagnostics/MODULE, Powertrain Control (PCM) - Standard Procedure). 5. CHECK THE PDC OUTPUT 1. Reconnect the PDC C5 harness connector. 2. Turn the ignition on and start the engine. 3. Measure the voltage of the (F203) SCR Module Heater Supply circuit at the DEF Dosing Control Unit C1 harness connector. Is the voltage approximately equal to battery voltage? Yes • Replace the DEF Dosing Control Unit in accordance with the service information. • Perform the POWERTRAIN VERIFICATION TEST - 6.7L. (Refer to 28 - DTC-Based Diagnostics/MODULE, Powertrain Control (PCM) - Standard Procedure). No • Check two fuses (F19-30A and F75-10A) in the PDC that both feed the SCR 1 (Heater) Relay for an open. Check the connectors at the DEF Dosing Control Unit and PDC for spread terminals causing an intermittent connection. If the fuses and connectors are good, replace the Power Distribution Center (PDC) in accordance with the Service Information. • Perform the POWERTRAIN VERIFICATION TEST - 6.7L. (Refer to 28 - DTC-Based Diagnostics/MODULE, Powertrain Control (PCM) - Standard Procedure).
-
P07C0 - 00 - Input - Turbine Shaft Speed Sensor 1 Circuit High
P07C0 - 00 - Input - Turbine Shaft Speed Sensor 1 Circuit High For a complete TRANSMISSION wiring diagram, (refer to the Wiring Information) . Theory of Operation The purpose of the diagnostic is to check the turbine speed sensor circuit for electrical failures by continuously monitoring the sensor output circuit for voltage high, low, or open conditions. The turbine speed sensor is a Hall Effect sensor that has an output range that alternates between normal high and normal low voltages as the turbine tone wheel rotates. If the measured turbine speed sensor output circuit voltage is greater than or equal to a calibrated high threshold (circuit high) or is less than or equal to a calibrated low threshold (circuit low or open) for a calibrated amount of time, a DTC will set. When Monitored and Set Conditions When Monitored: This diagnostic runs continuously when the following conditions are met: TCM supply voltage is between 10 and 16 volts. Ignition switch Run position signal is detected via dedicated circuit to TCM. Engine speed (CAN Message) is greater than 550 rpm. There are no ignition switch failures. Set Conditions: • Input speed sensor circuit voltage is greater than or equal to 1.821 volts for less than 1 second. Possible Causes INPUT SPEED SENSOR SUPPLY (+) CIRCUIT SHORTED TO BATTERY VOLTAGE INPUT SPEED SENSOR SUPPLY (+) CIRCUIT SHORTED TO ANOTHER CIRCUIT INPUT SPEED SENSOR SIGNAL (-) CIRCUIT SHORTED TO BATTERY VOLTAGE INPUT SPEED SENSOR SIGNAL (-) CIRCUIT SHORTED TO ANOTHER CIRCUIT INPUT SPEED SENSOR TRANSMISSION CONTROL MODULE (TCM) Always perform the PRE-DIAGNOSTIC TROUBLESHOOTING PROCEDURE before proceeding. (Refer to 28 - DTC-Based Diagnostics/MODULE, Transmission Control (TCM) /Standard Procedure). 1. CHECK FOR AN ACTIVE DTC 1. Record the Event Data and Environmental Data. 2. With the scan tool, erase DTCs 3. Using the recorded Event and Environmental Data, along with the When Monitored and Set Conditions above, operate the vehicle in the conditions that set the DTC. 4. Read TCM DTCs. Did the DTC return? Yes • Go To 2 No • Go To 12 2. CHECK THE INPUT SPEED SENSOR 1. Turn the ignition off. 2. Connect diagnostic scan tool and confirm Input Speed Sensor A/D voltage. 3. Starts the engine. NOTE: It may be necessary to allow the vehicle to allow the vehicle to roll while in a driven gear to see the voltage switching. If necessary to perform this test with the vehicle not stationary, enlist the aid of another person to operate the vehicle while monitoring the scan tool. 4. Place the vehicle in gear. 5. Monitor the voltage value Input Speed Sensor A/D voltage. 6. Does the voltage switch voltage Hi and Lo continually? (HI Voltage Over 1.20V / LO Voltage Under 0.80V) Yes • Go To 3 No • Replace the Input Speed Sensor and the transmission internal wire harness in accordance with the SERVICE INFORMATION. (Refer to 21 - Transmission and Transfer Case/Automatic - AS69RC/SENSOR, Speed/Removal) . • Perform the TRANSMISSION VERIFICATION TEST (Refer to 28 - DTC-Based Diagnostics/MODULE, Transmission Control (TCM) - Standard Procedure). 3. CHECK WIRING AND CONNECTIONS AT THE I-255 CONNECTOR 1. Turn the ignition off. 2. Disconnect and check the I-255 connector. 3. Inspect the harness connectors and all male and female terminals for the following conditions: Proper connector installation. Damaged connector locks. Corrosion. Other signs of water intrusion. Weather seal damage (if equipped). Bent terminals. Terminals that have been pushed back into the connector cavity. Perform a terminal drag test on each connector terminal to verify proper terminal tension. 4. Using the schematics as a guide, inspect the wiring and connectors specific to this circuit. 5. Wiggle the wires while checking for shorted or open circuits. Were any problems found? Yes • Repair as necessary. • Perform the TRANSMISSION VERIFICATION TEST. (Refer to 28 - DTC-Based Diagnostics/MODULE, Transmission Control (TCM) /Standard Procedure). No • Go To 4 4. CHECK THE (T69) INPUT SPEED SENSOR SUPPLY (+) CIRCUIT FOR A SHORT TO ANOTHER CIRCUIT 1. Disconnect the I-255 harness connector. 2. Disconnect the Input Speed Sensor harness connector. 3. Check for continuity between circuit (T69) and all other circuits in the I-255 (Transmission Side) harness connector. Is there continuity between any other circuits and the (T69) Input Speed Sensor Supply (+) circuit? Yes • Repair the (T69) Input Speed Sensor Supply (+) circuit for a short to another circuit. • Perform the TRANSMISSION VERIFICATION TEST (Refer to 28 - DTC-Based Diagnostics/MODULE, Transmission Control (TCM) - Standard Procedure). No • Go To 5 5. CHECK THE (T52) INPUT SPEED SENSOR SIGNAL (-) CIRCUIT FOR A SHORT TO ANOTHER CIRCUIT 1. Disconnect the I-255 harness connector. 2. Disconnect the Input Speed Sensor harness connector. 3. Check for continuity between circuit (T52) and all other circuits in the I-255 (Transmission Side) harness connector. Is there continuity between any other circuits and the (T52) Input Speed Sensor Signal (-) circuit? Yes • Repair the (T52) Input Speed Sensor Signal (-) circuit for a short to another circuit. • Perform the TRANSMISSION VERIFICATION TEST (Refer to 28 - DTC-Based Diagnostics/MODULE, Transmission Control (TCM) - Standard Procedure). No • Go To 6 6. CHECK THE (T52) INPUT SPEED SENSOR SIGNAL (-) CIRCUIT FOR A SHORT TO VOLTAGE 1. Disconnect the I-255 connector. 2. Disconnect the Transmission Harness Pass Through Connector. 3. Turn the ignition switch to the RUN position, engine off. 4. Measure for voltage between chassis ground and the (T52) Input Speed Sensor Signal (-) circuit at the I-255 (Transmission Side) harness connector. Is there voltage present on (T52) Input Speed Sensor Signal (-) circuit? Yes • Repair the (T52) Input Speed Sensor Signal (-) circuit for a short to voltage. • Perform the TRANSMISSION VERIFICATION TEST (Refer to 28 - DTC-Based Diagnostics/MODULE, Transmission Control (TCM) - Standard Procedure). No • Go To 7 7. CHECK THE (T69) INPUT SPEED SENSOR SUPPLY (+) CIRCUIT FOR A SHORT TO VOLTAGE 1. Disconnect the I-255 connector. 2. Disconnect the Transmission Harness Pass Through Connector. 3. Turn the ignition switch to the RUN position, engine off. 4. Measure for voltage between chassis ground and the (T69) Input Speed Sensor Supply (+) circuit at the I-255 (Transmission Side) harness connector. Is there voltage present on (T69) Input Speed Sensor Supply (+) circuit? Yes • Repair the (T69) Input Speed Sensor Supply (+) circuit for a short to voltage. • Perform the TRANSMISSION VERIFICATION TEST (Refer to 28 - DTC-Based Diagnostics/MODULE, Transmission Control (TCM) - Standard Procedure). No • Go To 8 8. CHECK THE (T69) INPUT SPEED SENSOR SUPPLY (+) CIRCUIT FOR A SHORT TO VOLTAGE 1. Disconnect the I-255 connector. 2. Disconnect the TCM C-1 and C-2 harness connectors. 3. Turn the ignition switch to the RUN position, engine off. 4. Measure for voltage between chassis ground and the (T69) Input Speed Sensor Supply (+) circuit at the I-255 (TCM Side) harness connector. Is there voltage present on (T69) Input Speed Sensor Supply (+) circuit? Yes • Repair the (T69) Input Speed Sensor Supply (+) circuit for a short to voltage. • Perform the TRANSMISSION VERIFICATION TEST (Refer to 28 - DTC-Based Diagnostics/MODULE, Transmission Control (TCM) - Standard Procedure). No • Go To 9 9. CHECK THE (T52) INPUT SPEED SENSOR SIGNAL (-) CIRCUIT FOR A SHORT TO VOLTAGE 1. Disconnect the I-255 connector. 2. Disconnect the TCM C-1 and C-2 harness connectors. 3. Turn the ignition switch to the RUN position, engine off. 4. Measure for voltage between chassis ground and the (T52) Input Speed Sensor Signal (-) circuit at the I-255 (TCM Side) harness connector. Is there voltage present on (T52) Input Speed Sensor Signal (-) circuit? Yes • Repair the (T52) Input Speed Sensor Signal (-) circuit for a short to voltage. • Perform the TRANSMISSION VERIFICATION TEST (Refer to 28 - DTC-Based Diagnostics/MODULE, Transmission Control (TCM) - Standard Procedure). No • Go To 10 10. CHECK THE (T69) INPUT SPEED SENSOR SUPPLY (+) CIRCUIT FOR A SHORT TO ANOTHER CIRCUIT 1. Disconnect the TCM C-2 harness connector. 2. Disconnect the I-255 harness connector. 3. Check for continuity between circuit (T69) Input Speed Sensor Supply (+) and all other circuits in the I-255 (TCM Side) harness connector. Is there continuity between any other circuits and the (T69) Input Speed Sensor Supply (+) circuit? Yes • Repair the (T69) Input Speed Sensor Supply (+) circuit for a short to another circuit. • Perform the TRANSMISSION VERIFICATION TEST (Refer to 28 - DTC-Based Diagnostics/MODULE, Transmission Control (TCM) - Standard Procedure). No • Go To 11 11. CHECK THE (T52) INPUT SPEED SENSOR SIGNAL (-) CIRCUIT FOR A SHORT TO ANOTHER CIRCUIT 1. Disconnect the TCM C-2 harness connector. 2. Disconnect the I-255 harness connector. 3.Check for continuity between circuit (T52) Input Speed Sensor Signal (-) and all other circuits in the I-255 (TCM Side) harness connector. Is there continuity between any other circuits and the (T52) Input Speed Sensor Signal (-) circuit? Yes • Repair the (T52) Input Speed Sensor Signal (-) circuit for a short to another circuit. • Perform the TRANSMISSION VERIFICATION TEST (Refer to 28 - DTC-Based Diagnostics/MODULE, Transmission Control (TCM) - Standard Procedure). No • Replace the Input Speed Sensor in accordance with the SERVICE INFORMATION. (Refer to 21 - Transmission and Transfer Case/Automatic - AS69RC/SENSOR, Speed/Removal) . • Perform the TRANSMISSION VERIFICATION TEST (Refer to 28 - DTC-Based Diagnostics/MODULE, Transmission Control (TCM) - Standard Procedure). DTC returned after TRANSMISSION VERIFICATION TEST. • If the DTC returns after replacing the Input Speed Sensor, replace the Transmission Control Module (TCM) in accordance with the Service information. (Refer to 08 - Electrical/8E - Electronic Control Modules/MODULE, Transmission Control/Removal) . • Perform the TRANSMISSION VERIFICATION TEST. (Refer to 28 - DTC-Based Diagnostics/MODULE, Transmission Control (TCM) /Standard Procedure). DTC did not return after TRANSMISSION VERIFICATION TEST. • Test Complete. 12. CHECK WIRING AND I-255 CONNECTOR FOR INTERMITTENT CONNECTIONS NOTE: The conditions necessary to set the DTC are not present at this time. The code set because of an intermittent condition. Try to determine the cause in this step. Turn the ignition off. 1. Disconnect all TCM harness connectors. 2. Disconnect all related in-line harness connections. 3. Disconnect the related component harness connectors. 4. Inspect harness connectors, component connectors, and all male and female terminals for the following conditions: Proper connector installation. Damaged connector locks. Corrosion. Other signs of water intrusion. Weather seal damage (if equipped). Bent terminals. • Terminals that have been pushed back into the connector cavity. • Perform a terminal drag test on each connector terminal to verify proper terminal tension. 5. Using the schematics as a guide, inspect the wiring and connectors specific to this circuit. 6. Wiggle the wires while checking for shorted and open circuits. Were any problems found? Yes • Repair as necessary. • Perform the TRANSMISSION VERIFICATION TEST. (Refer to 28 - DTC-Based Diagnostics/MODULE, Transmission Control (TCM) /Standard Procedure). No • Perform the TRANSMISSION VERIFICATION TEST. (Refer to 28 - DTC-Based Diagnostics/MODULE, Transmission Control (TCM) /Standard Procedure). • Test complete.
-
P07BF - 00 - Input - Turbine Shaft Speed Sensor 1 Circuit Low
P07BF - 00 - Input - Turbine Shaft Speed Sensor 1 Circuit Low For a complete TRANSMISSION wiring diagram, (refer to the Wiring Information) . Theory of Operation The purpose of the diagnostic is to check the turbine speed sensor circuit for electrical failures by continuously monitoring the sensor output circuit for voltage high, low, or open conditions. The turbine speed sensor is a Hall Effect sensor that has an output range that alternates between normal high and normal low voltages as the turbine tone wheel rotates. If the measured turbine speed sensor output circuit voltage is greater than or equal to a calibrated high threshold (circuit high) or is less than or equal to a calibrated low threshold (circuit low or open) for a calibrated amount of time, a DTC will set. When Monitored and Set Conditions When Monitored: This diagnostic runs continuously when the following conditions are met: • TCM supply voltage is between 10 and 16 volts. • Engine speed (CAN message) is greater than 550 rpm. Set Conditions: • Input speed sensor output circuit voltage is less than or equal to 0.225 volts for less than 1 second. Possible Causes INPUT SPEED SENSOR SUPPLY (+) CIRCUIT OPEN INPUT SPEED SENSOR SUPPLY (+) CIRCUIT SHORTED TO GROUND INPUT SPEED SENSOR SIGNAL (-) CIRCUIT OPEN INPUT SPEED SENSOR SIGNAL (-) CIRCUIT SHORTED TO GROUND INPUT SPEED SENSOR TRANSMISSION CONTROL MODULE (TCM) Always perform the PRE-DIAGNOSTIC TROUBLESHOOTING PROCEDURE before proceeding. (Refer to 28 - DTC-Based Diagnostics/MODULE, Transmission Control (TCM) /Standard Procedure). Diagnostic Test 1. CHECK FOR AN ACTIVE DTC 1. With the scan tool, read TCM DTCs and record on the repair order. 2. Record the Event Data and Environmental Data. 3. With the scan tool, erase DTCs. 4. Using the recorded Event and Environmental Data, along with the When Monitored and Set Conditions above, operate the vehicle in the conditions that set the DTC. 5. With the scan tool, read TCM DTCs. Did the DTC return? Yes • Go To 2 No • Go To 12 2. CHECK THE INPUT SPEED SENSOR SUPPLY 1. Connect the scan tool to the vehicle. 2. Start the engine. NOTE: It may be necessary to allow the vehicle to allow the vehicle to roll while in a driven gear to see the voltage switching. If necessary to perform this test with the vehicle not stationary, enlist the aid of another person to operate the vehicle while monitoring the scan tool. 3. Place the vehicle in gear. 4. Monitor the Input Speed Sensor Supply voltage with the scan tool. Does the voltage switch from high (more than 1.2V) to Low (less than .8V) continuously? Yes • Go To 3 No • Replace Input Speed Sensor Supply and Transmission internal wiring in accordance with the Service Information. (Refer to 21 - Transmission and Transfer Case/Automatic - AS69RC/SENSOR, Speed/Removal) . • Perform TRANSMISSION VERIFICATION TEST (Refer to 28 - DTC-Based Diagnostics/MODULE, Transmission Control (TCM) - Standard Procedure). 3. CHECK WIRING AND CONNECTIONS AT THE I-255 CONNECTOR 1. Turn the ignition off. 2. Disconnect and check the I-255 connector. 3. Inspect the harness connectors and all male and female terminals for the following conditions: Proper connector installation. Damaged connector locks. Corrosion. Other signs of water intrusion. Weather seal damage (if equipped). Bent terminals. Terminals that have been pushed back into the connector cavity. Perform a terminal drag test on each connector terminal to verify proper terminal tension. 4. Using the schematics as a guide, inspect the wiring and connectors specific to this circuit. 5. Wiggle the wires while checking for shorted or open circuits. Were any problems found? Yes • Repair as necessary. • Perform the TRANSMISSION VERIFICATION TEST. (Refer to 28 - DTC-Based Diagnostics/MODULE, Transmission Control (TCM) /Standard Procedure). No • Go To 4 4. CHECK THE (T69) INPUT SPEED SENSOR SUPPLY (+) CIRCUIT FOR AN OPEN 1. Disconnect the I-255 harness connector. 2. Disconnect the Transmission Harness Pass Through connector. 3. Measure the resistance of the (T69) Input Speed Sensor Supply (+) circuit between the Transmission harness connector and the I-255 (Transmission Side) harness connector. Is the resistance below 3.0 Ohms? Yes • Go To 5 No • Repair the (T69) Input Speed Sensor Supply (+) circuit for an open. • Perform the TRANSMISSION VERIFICATION TEST (Refer to 28 - DTC-Based Diagnostics/MODULE, Transmission Control (TCM) - Standard Procedure). 5. CHECK THE (T69) INPUT SPEED SENSOR SUPPLY (+) CIRCUIT FOR A SHORT TO GROUND 1. Disconnect the I-255 harness connector. 2. Disconnect the Transmission Harness Pass Through Connector. 3. Check for continuity between ground and the (T69) Input Speed Sensor Supply (+) circuit at the I-255 (Transmission Side) harness connector. Is there continuity between ground and the (T69) Input Speed Sensor Supply (+) circuit? Yes • Repair the (T69) Input Speed Sensor Supply (+) circuit for a short to ground. • Perform the TRANSMISSION VERIFICATION TEST (Refer to 28 - DTC-Based Diagnostics/MODULE, Transmission Control (TCM) - Standard Procedure). No • Go To 6 6. CHECK THE (T52) INPUT SPEED SENSOR SIGNAL (-) CIRCUIT FOR AN OPEN 1. Disconnect the I-255 harness connector. 2. Disconnect the transmission pass through harness connector. 3. Measure the resistance of the (T52) Input Speed Sensor Signal (-) circuit between the Transmission Assembly harness connector and the I-255 (Transmission Side) harness connector. Is the resistance below 3.0 Ohms? Yes • Go To 7 No • Repair the (T52) Input Speed Sensor Signal (-) circuit for an open. • Perform the TRANSMISSION VERIFICATION TEST (Refer to 28 - DTC-Based Diagnostics/MODULE, Transmission Control (TCM) - Standard Procedure). 7. CHECK THE (T52) INPUT SPEED SENSOR SIGNAL (-) CIRCUIT FOR A SHORT TO GROUND 1. Disconnect the I-255 harness connector. 2. Disconnect the transmission pass through harness connector. 3. Check for continuity between ground and the (T52) Input Speed Sensor Signal (-) circuit at the I-255 (Transmission Side) harness connector. Is there continuity between ground and the (T52) Input Speed Sensor Signal (-) circuit? Yes • Repair the (T52) Input Speed Sensor Signal (-) circuit for a short to ground. • Perform the TRANSMISSION VERIFICATION TEST (Refer to 28 - DTC-Based Diagnostics/MODULE, Transmission Control (TCM) - Standard Procedure). No • Go To 8 8. CHECK THE (T69) INPUT SPEED SENSOR SUPPLY (+) CIRCUIT FOR AN OPEN 1. Disconnect the TCM C-1 harness connector. 2. Disconnect the I-255 harness connector. 3. Measure the resistance of the (T69) Input Speed Sensor Supply (+) circuit between the TCM C-1 harness connector and the I-255 (TCM Side) harness connector. Is the resistance below 3.0 Ohms? Yes • Go To 9 No • Repair the (T69) Input Speed Sensor Supply (+) circuit for an open. • Perform the TRANSMISSION VERIFICATION TEST (Refer to 28 - DTC-Based Diagnostics/MODULE, Transmission Control (TCM) - Standard Procedure). 9. CHECK THE (T69) INPUT SPEED SENSOR SUPPLY (+) CIRCUIT FOR A SHORT TO GROUND 1. Disconnect the TCM C-1 harness connector. 2. Disconnect the I-255 harness connector. 3. Check for continuity between ground and the (T69) Input Speed Sensor Supply (+) circuit at the I-255 (TCM Side) harness connector. Is there continuity between ground and the (T69) Input Speed Sensor Supply (+) circuit? Yes • Repair the (T69) Input Speed Sensor Supply (+) circuit for a short to ground. • Perform the TRANSMISSION VERIFICATION TEST (Refer to 28 - DTC-Based Diagnostics/MODULE, Transmission Control (TCM) - Standard Procedure). No • Go To 10 10. CHECK THE (T52) INPUT SPEED SENSOR SIGNAL (-) CIRCUIT FOR AN OPEN 1. Disconnect the TCM C-1 harness connector. 2. Disconnect the I-255 harness connector. 3. Measure the resistance of the (T52) Input Speed Sensor Signal (-) circuit between the TCM C-1 harness connector and the I-255 (TCM Side) harness connector. Is the resistance below 3.0 Ohms? Yes • Go To 11 No • Repair the (T52) Input Speed Sensor Signal (-) circuit for an open. • Perform the TRANSMISSION VERIFICATION TEST (Refer to 28 - DTC-Based Diagnostics/MODULE, Transmission Control (TCM) - Standard Procedure). 11. CHECK THE (T52) INPUT SPEED SENSOR SIGNAL (-) CIRCUIT FOR A SHORT TO GROUND 1. Disconnect the TCM C-1 harness connector. 2. Disconnect the I-255 harness connector. 3. Check for continuity between ground and the (T52) Input Speed Sensor Signal (-) circuit at the I-255 (TCM Side) harness connector. Is there continuity between ground and the (T52) Input Speed Sensor Signal (-) circuit? Yes • Repair the (T52) Input Speed Sensor Signal (-) circuit for a short to ground. • Perform the TRANSMISSION VERIFICATION TEST (Refer to 28 - DTC-Based Diagnostics/MODULE, Transmission Control (TCM) - Standard Procedure). No • Replace the Input Speed Sensor in accordance with the Service Information. (Refer to 21 -Transmission and Transfer Case/Automatic - AS69RC/SENSOR, Speed/Removal) . • Perform the TRANSMISSION VERIFICATION TEST. (Refer to 28 - DTC-Based Diagnostics/MODULE, Transmission Control (TCM) /Standard Procedure). DTC Returned after TRANSMISSION VERIFICATION TEST. • If the DTC returns after replacing the Input Speed Sensor, replace the Transmission Control Module (TCM) in accordance with the Service information. (Refer to 08 - Electrical/8E - Electronic Control Modules/MODULE, Transmission Control/Removal) . • Perform the TRANSMISSION VERIFICATION TEST. (Refer to 28 - DTC-Based Diagnostics/MODULE, Transmission Control (TCM) /Standard Procedure). DTC did not return after TRANSMISSION VERIFICATION TEST. • Test complete. 12. CHECK WIRING AND I-255 CONNECTOR FOR INTERMITTENT CONNECTIONS NOTE: The conditions necessary to set the DTC are not present at this time. The code set because of an intermittent condition. Try to determine the cause in this step. Turn the ignition off. 1. Disconnect all TCM harness connectors. 2. Disconnect all related in-line harness connections (if equipped). 3. Disconnect the related component harness connectors. 4. Inspect harness connectors, component connectors, and all male and female terminals for the following conditions: Proper connector installation. Damaged connector locks. Corrosion. Other signs of water intrusion. Weather seal damage (if equipped). Bent terminals. Terminals that have been pushed back into the connector cavity. Perform a terminal drag test on each connector terminal to verify proper terminal tension. 5. Using the schematics as a guide, inspect the wiring and connectors specific to this circuit. 6. Wiggle the wires while checking for shorted and open circuits. Were any problems found? Yes • Repair as necessary. • Perform the TRANSMISSION VERIFICATION TEST. (Refer to 28 - DTC-Based Diagnostics/MODULE, Transmission Control (TCM) /Standard Procedure). No • Perform the TRANSMISSION VERIFICATION TEST. (Refer to 28 - DTC-Based Diagnostics/MODULE, Transmission Control (TCM) /Standard Procedure). • Test complete.
-
Tire Size
Consider it carefully on the rear axle gearing and the top gear of the transmission. As you found how it changed your truck getting the gearing correct. I've got that other member with Allison Transmission and the final gear is pretty tall and running way too low in top gear at 65 MPH.
-
P06D8 - Sensor Reference Voltage 6 Circuit High
P06D8 - Sensor Reference Voltage 6 Circuit High Theory of Operation This sensor supply circuit provides a 5-Volt supply to the Fuel Rail Pressure (FRP) Sensor. The Powertrain Control Module (PCM) illuminates the MIL lamp immediately after the diagnostic runs and fails. The ETC lamp will also flash. During this time the customer will be in a limp home mode. The PCM will turn off the MIL lamp after the diagnostic runs and passes in four consecutive drive cycles. When Monitored: While the engine is running. Set Condition: Voltage detected on the 5-Volt Supply circuit is above a calibrated value. Possible Causes 5-VOLT SUPPLY CIRCUIT SHORTED TO VOLTAGE POWERTRAIN CONTROL MODULE (PCM) Always perform the Pre-Diagnostic Troubleshooting procedure before proceeding. (Refer to 28 - DTC-Based Diagnostics/MODULE, Powertrain Control (PCM) - Standard Procedure). Diagnostic Test 1. ACTIVE DTC 1. Turn the ignition on. 2. With the scan tool, record all Freeze frame data. 3. With the scan tool, erase DTCs. 4. Turn the ignition off for 75 seconds. 5. Turn the ignition on. 6. With the scan tool, read DTCs. Did the DTC reset? Yes • Go To 2 No • Perform the INTERMITTENT CONDITION diagnostic procedure. (Refer to 28 - DTC-Based Diagnostics/MODULE, Powertrain Control (PCM) - Standard Procedure). 2. CHECK THE (K350) 5-VOLT SUPPLY CIRCUIT FOR A SHORT TO VOLTAGE 1. Turn the ignition off. 2. Disconnect the FRP sensor harness connector. 3. Turn the ignition on. 4. Measure the voltage of the (K350) 5-Volt Supply circuit at FRP sensor harness connector. Is the voltage reading above 5.1 Volts? Yes • Repair the (K350) 5-Volt Supply circuit for a short to voltage. • Perform the POWERTRAIN VERIFICATION TEST - 6.7L. (Refer to 28 - DTC-Based Diagnostics/MODULE, Powertrain Control (PCM) - Standard Procedure). No • Go To 3 3. CHECK THE (K350) 5-VOLT SUPPLY CIRCUIT FOR A SHORT TO ANOTHER CIRCUIT 1. Turn the ignition off. 2. Disconnect the PCM C1 harness connector. NOTE: Check connectors - Clean/repair as necessary. 3. Measure the resistance between the (K350) 5-Volt Supply circuit and all other circuits in the PCM C1 connector. Is the resistance below 10k Ohms? Yes • Repair the short from the (K350) 5-Volt Supply circuit to the circuit that measured below 10k Ohms. • Perform the POWERTRAIN VERIFICATION TEST - 6.7L. (Refer to 28 - DTC-Based Diagnostics/MODULE, Powertrain Control (PCM) - Standard Procedure). No • Replace the Powertrain Control Module in accordance with the service information. • Perform the POWERTRAIN VERIFICATION TEST - 6.7L. (Refer to 28 - DTC-Based Diagnostics/MODULE, Powertrain Control (PCM) - Standard Procedure).
-
P06D7 - Sensor Reference Voltage 6 Circuit Low
P06D7 - Sensor Reference Voltage 6 Circuit Low Theory of Operation This sensor supply circuit provides a 5-Volt supply to the Fuel Rail Pressure (FRP) Sensor. The Powertrain Control Module (PCM) illuminates the MIL lamp immediately after the diagnostic runs and fails. The ETC lamp will also flash. During this time the customer will be in a limp home mode. The PCM will turn off the MIL lamp after the diagnostic runs and passes in four consecutive drive cycles. When Monitored: With the ignition on, PCM powered. Set Condition: Low voltage detected at the 5-Volt Supply circuit. Possible Causes FUEL RAIL PRESSURE (FRP) SENSOR 5-VOLT SUPPLY CIRCUIT SHORTED TO GROUND POWERTRAIN CONTROL MODULE (PCM) Always perform the Pre-Diagnostic Troubleshooting procedure before proceeding. (Refer to 28 - DTC-Based Diagnostics/MODULE, Powertrain Control (PCM) - Standard Procedure). Diagnostic Test 1. ACTIVE DTC 1. Turn the ignition on. 2. Using the scan tool, record all Freeze frame data. 3. Using the scan tool, erase DTCs. 4. Turn the ignition off for 75 seconds. 5. Turn the ignition on. 6. Using the scan tool, read DTCs. Did the DTC reset? Yes • Go To 2 No • Perform the INTERMITTENT CONDITION diagnostic procedure. (Refer to 28 - DTC-Based Diagnostics/MODULE, Powertrain Control (PCM) - Standard Procedure). 2. CHECK THE FRP SENSOR 1. Turn the ignition off. 2. Disconnect the FRP sensor harness connector. 3. Turn the ignition on. 4. Measure the voltage on the (K350) 5-Volt Supply circuit at the FRP sensor harness connector. Is the voltage reading between 4.9 and 5.1 Volts? Yes • Replace the Fuel Rail Pressure Sensor in accordance with the service information. • Perform the POWERTRAIN VERIFICATION TEST - 6.7L. (Refer to 28 - DTC-Based Diagnostics/MODULE, Powertrain Control (PCM) - Standard Procedure). No • Go To 3 3. CHECK THE (K350) 5-VOLT SUPPLY CIRCUIT FOR A SHORT TO GROUND 1. Disconnect the PCM C1 harness connector. 2. Measure the resistance between ground and the (K350) 5-Volt Supply circuit at the PCM C1 harness connector. Is the resistance below 10k Ohms? Yes • Repair the (K350) 5-Volt Supply circuit for a short to ground. • Perform the POWERTRAIN VERIFICATION TEST - 6.7L. (Refer to 28 - DTC-Based Diagnostics/MODULE, Powertrain Control (PCM) - Standard Procedure). No • Replace the Powertrain Control Module in accordance with the service information. • Perform the POWERTRAIN VERIFICATION TEST - 6.7L. (Refer to 28 - DTC-Based Diagnostics/MODULE, Powertrain Control (PCM) - Standard Procedure).
-
P06D4 - Sensor Reference Voltage 5 Circuit High
P06D4 - Sensor Reference Voltage 5 Circuit High Theory of Operation This sensor supply circuit provides a 5-Volt supply to the Accelerator Pedal Position 2 Sensor (APPS), Diesel Particulate Filter Pressure Sensor, Soot Delta Pressure Sensor, and the Transmission Pressure Sensor. The Powertrain Control Module (PCM) illuminates the MIL lamp immediately after the diagnostic runs and fails. The ETC lamp will also flash. During this time the customer will be in a limp home mode. The PCM will turn off the MIL lamp after the diagnostic runs and passes in four consecutive drive cycles. When Monitored: While the engine is running. Set Condition: Voltage detected on the 5-Volt Supply circuit is above a calibrated value. Possible Causes 5-VOLT SUPPLY CIRCUIT SHORTED TO VOLTAGE POWERTRAIN CONTROL MODULE (PCM) Always perform the Pre-Diagnostic Troubleshooting procedure before proceeding. (Refer to 28 - DTC- Based Diagnostics/MODULE, Powertrain Control (PCM) - Standard Procedure). Diagnostic Test 1. ACTIVE DTC 1. Turn the ignition on. 2. With the scan tool, record all Freeze frame data. 3. With the scan tool, erase DTCs. 4. Turn the ignition off for 75 seconds. 5. Turn the ignition on. 6. With the scan tool, read DTCs. Did the DTC reset? Yes • Go To 2 No • Perform the INTERMITTENT CONDITION diagnostic procedure. (Refer to 28 - DTC-Based Diagnostics/MODULE, Powertrain Control (PCM) - Standard Procedure). 2. CHECK THE (F856) 5-VOLT SUPPLY FOR A SHORT TO VOLTAGE 1. Turn the ignition off. 2. Disconnect the components listed in the theory of operation. 3. Turn the ignition on. 4. Measure the voltage of the (F856) 5-Volt Supply circuit at the Accelerator Pedal Position harness connector. Is the voltage reading above 5.1 Volts? Yes • Repair the (F856) 5-Volt Supply circuit for a short to voltage. • Perform the POWERTRAIN VERIFICATION TEST - 6.7L. (Refer to 28 - DTC-Based Diagnostics/MODULE, Powertrain Control (PCM) - Standard Procedure). No • Go To 3 3. CHECK THE (F856) 5-VOLT SUPPLY CIRCUIT FOR A SHORT TO ANOTHER CIRCUIT 1. Turn the ignition off. 2. Disconnect the PCM C2 harness connector. NOTE: Check connectors - Clean/repair as necessary. 3. Measure the resistance between the (F856) 5-Volt Supply circuit and all other circuits in the PCM C2 connector. Is the resistance below 10k Ohms between the (F856) 5-Volt Supply circuit and any of the circuits? Yes • Repair the short between the (F856) 5-Volt Supply circuit and the circuit that measured below 10k Ohms. • Perform the POWERTRAIN VERIFICATION TEST - 6.7L. (Refer to 28 - DTC-Based Diagnostics/MODULE, Powertrain Control (PCM) - Standard Procedure). No • Replace the Powertrain Control Module in accordance with the service information. • Perform the POWERTRAIN VERIFICATION TEST - 6.7L. (Refer to 28 - DTC-Based Diagnostics/MODULE, Powertrain Control (PCM) - Standard Procedure).
-
P06D3 - Sensor Reference Voltage 5 Circuit Low
P06D3 - Sensor Reference Voltage 5 Circuit Low Theory of Operation This sensor supply circuit provides a 5-Volt supply to the Accelerator Pedal Position 2 Sensor (APPS), Diesel Particulate Filter Pressure Sensor, Soot Delta Pressure Sensor, and the Transmission Pressure Sensor. The Powertrain Control Module (PCM) illuminates the MIL lamp immediately after the diagnostic runs and fails. The ETC lamp will also flash. During this time the customer will be in a limp home mode. The PCM will turn off the MIL lamp after the diagnostic runs and passes in four consecutive drive cycles. When Monitored: With the ignition on, PCM powered. Set Condition: Low voltage detected at the 5-Volt Supply circuit. Possible Causes APP 2 SENSOR DIESEL PARTICULATE FILTER PRESSURE SENSOR SOOT DELTA PRESSURE SENSOR TRANSMISSION LINE PRESSURE SENSOR (66RFE ONLY) 5-VOLT SUPPLY CIRCUIT SHORTED TO GROUND POWERTRAIN CONTROL MODULE (PCM) Always perform the Pre-Diagnostic Troubleshooting procedure before proceeding. (Refer to 28 - DTC-Based Diagnostics/MODULE, Powertrain Control (PCM) - Standard Procedure). Diagnostic Test 1. ACTIVE DTC 1. Turn the ignition on. 2. With the scan tool, record all Freeze frame data. 3. With the scan tool, erase DTCs. 4. Turn the ignition off for 75 seconds. 5. Turn the ignition on. 6. With the scan tool, read DTCs. Did the DTC reset? Yes • Go To 2 No • Perform the INTERMITTENT CONDITION diagnostic procedure. (Refer to 28 - DTC-Based Diagnostics/MODULE, Powertrain Control (PCM) - Standard Procedure). 2. CHECK THE APPS SENSOR 2 1. Ignition on. 2. Disconnect the Accelerator Pedal Position Sensor harness connector. NOTE: Check connectors - Clean/repair as necessary. 3. Measure the voltage on the (F856) 5-Volt Supply circuit at the Accelerator Pedal Position Sensor harness connector. Is the voltage reading between 4.9 and 5.1 Volts? Yes • Replace the Accelerator Pedal Position Sensor in accordance with the service information. • Perform the POWERTRAIN VERIFICATION TEST - 6.7L. (Refer to 28 - DTC-Based Diagnostics/MODULE, Powertrain Control (PCM) - Standard Procedure). No • Go To 3 3. CHECK THE DIESEL PARTICULATE FILTER PRESSURE SENSOR 1. Disconnect the Diesel Particulate Filter Pressure Sensor harness connector. NOTE: Check connectors - Clean/repair as necessary. 2. Measure the voltage on the (F856) 5-Volt Supply circuit at the Diesel Particulate Filter Pressure Sensor harness connector. Is the voltage reading between 4.9 and 5.1 Volts? Yes • Replace the Diesel Particulate Filter Pressure Sensor in accordance with the service information. • Perform the POWERTRAIN VERIFICATION TEST - 6.7L. (Refer to 28 - DTC-Based Diagnostics/MODULE, Powertrain Control (PCM) - Standard Procedure). No • Go To 4 4. CHECK THE SOOT DELTA PRESSURE SENSOR 1. Disconnect the Soot Delta Pressure Sensor harness connector. NOTE: Check connectors - Clean/repair as necessary. 2. Measure the voltage on the (F856) 5-Volt Supply circuit at the Soot Delta Pressure Sensor harness connector. Is the voltage reading between 4.9 and 5.1 Volts? Yes • Replace the Soot Delta Pressure Sensor in accordance with the service information. • Perform the POWERTRAIN VERIFICATION TEST - 6.7L. (Refer to 28 - DTC-Based Diagnostics/MODULE, Powertrain Control (PCM) - Standard Procedure). No • Go To 5 5. CHECK THE TRANSMISSION LINE PRESSURE SENSOR (66RFE ONLY) 1. Disconnect the Transmission Pressure Sensor harness connector. NOTE: Check connectors - Clean/repair as necessary. 2. Measure the voltage on the (F856) 5-Volt Supply circuit at the Transmission Pressure Sensor harness connector. Is the voltage reading between 4.9 and 5.1 Volts? Yes • Replace the Transmission Line Pressure Sensor in accordance with the service information. • Perform the POWERTRAIN VERIFICATION TEST - 6.7L. (Refer to 28 - DTC-Based Diagnostics/MODULE, Powertrain Control (PCM) - Standard Procedure). No • Go To 6 6. CHECK THE (F856) 5-VOLT SUPPLY CIRCUIT FOR A SHORT TO GROUND 1. Turn the ignition off. 2. Disconnect the PCM C2 harness connector. 3. Check connectors - Clean/repair as necessary. 4. Measure the resistance between ground and the (F856) 5-Volt Supply circuit at the Diesel Particulate Filter Pressure Sensor harness connector. Is the resistance below 10k Ohms? Yes • Repair the (F856) 5-Volt Supply circuit for a short to ground. • Perform the POWERTRAIN VERIFICATION TEST - 6.7L. (Refer to 28 - DTC-Based Diagnostics/MODULE, Powertrain Control (PCM) - Standard Procedure). No • Replace and program the Powertrain Control Module in accordance with the service information. • Perform the POWERTRAIN VERIFICATION TEST - 6.7L. (Refer to 28 - DTC-Based Diagnostics/MODULE, Powertrain Control (PCM) - Standard Procedure).
-
P06A5 - Sensor Reference Voltage 4 Circuit High
P06A5 - Sensor Reference Voltage 4 Circuit High Theory of Operation This sensor supply circuit provides a 5-Volt supply to the Accelerator Pedal Position 1 Sensor (APPS) and the A/C Pressure Sensor. The Powertrain Control Module (PCM) illuminates the MIL lamp immediately after the diagnostic runs and fails. The ETC lamp will also flash. During this time the customer will be in a limp home mode. The PCM will turn off the MIL lamp after the diagnostic runs and passes in four consecutive drive cycles. When Monitored: With the ignition on, PCM powered. Set Condition: Voltage detected at the 5-Volt Supply circuit is above a calibrated value. Possible Causes 5-VOLT SUPPLY SHORT TO VOLTAGE POWERTRAIN CONTROL MODULE (PCM) Always perform the Pre-Diagnostic Troubleshooting procedure before proceeding. (Refer to 28 - DTC-Based Diagnostics/MODULE, Powertrain Control (PCM) - Standard Procedure). 1. ACTIVE DTC 1. Turn the ignition on. 2. With the scan tool, record all Freeze frame data. 3. With the scan tool, erase DTCs. 4. Turn the ignition off for 75 seconds. 5. Turn the ignition on. 6. With the scan tool, read DTCs. Did the DTC reset? Yes • Go To 2 No Perform the INTERMITTENT CONDITION diagnostic procedure. (Refer to 28 - DTC-Based Diagnostics/MODULE, Powertrain Control (PCM) - Standard Procedure). 2. CHECK THE (F855) 5-VOLT SUPPLY CIRCUIT FOR A SHORT TO VOLTAGE 1. Turn the ignition off. 2. Disconnect the Accelerator Pedal Position harness connector. 3. Turn the ignition on. 4. Measure the voltage of the (F855) 5-Volt Supply circuit at the Accelerator Pedal Position harness connector. Is the voltage reading above 5.1 Volts? Yes • Repair the (F855) 5-Volt Supply circuit for a short to voltage. • Perform the POWERTRAIN VERIFICATION TEST - 6.7L. (Refer to 28 - DTC-Based Diagnostics/MODULE, Powertrain Control (PCM) - Standard Procedure). No • Go To 3 3. CHECK THE (F855) 5-VOLT SUPPLY CIRCUIT FOR A SHORT TO ANOTHER CIRCUIT 1. Turn the ignition off. 2. Disconnect the PCM C2 harness connector. NOTE: Check connectors - Clean/repair as necessary. 3. Measure the resistance between the (F855) 5-Volt Supply circuit and all other circuits in the PCM C2 connector. Is the resistance below 10k Ohms between the (F855) 5-Volt Supply circuit and any of the circuits? Yes • Repair the short to the circuit that measured below 10k Ohms. • Perform the POWERTRAIN VERIFICATION TEST - 6.7L. (Refer to 28 - DTC-Based Diagnostics/MODULE, Powertrain Control (PCM) - Standard Procedure). No • Replace the Powertrain Control Module in accordance with the service information. • Perform the POWERTRAIN VERIFICATION TEST - 6.7L. (Refer to 28 - DTC-Based Diagnostics/MODULE, Powertrain Control (PCM) - Standard Procedure).
-
P06A4 - Sensor Reference Voltage 4 Circuit Low
P06A4 - Sensor Reference Voltage 4 Circuit Low Theory of Operation This sensor supply circuit provides a 5-Volt supply to the Accelerator Pedal Position 1 Sensor (APPS) and the A/C Pressure Sensor. The Powertrain Control Module (PCM) illuminates the MIL lamp immediately after the diagnostic runs and fails. The ETC lamp will also flash. During this time the customer will be in a limp home mode. The PCM will turn off the MIL lamp after the diagnostic runs and passes in four consecutive drive cycles. When Monitored: With the key on. Set Condition: Voltage detected on the 5-Volt supply circuit is below a calibrated value. Possible Causes 5-VOLT SUPPLY CIRCUIT SHORTED TO GROUND APP 1 SENSOR A/C PRESSURE SENSOR POWERTRAIN CONTROL MODULE (PCM) Always perform the Pre-Diagnostic Troubleshooting procedure before proceeding. (Refer to 28 - DTC-Based Diagnostics/MODULE, Powertrain Control (PCM) - Standard Procedure). 1. ACTIVE DTC 1. Turn the ignition on. 2. With the scan tool, record all Freeze frame data. 3. With the scan tool, erase DTCs. 4. Turn the ignition off for 75 seconds. 5. Turn the ignition on. 6. With the scan tool, read DTCs. Did the DTC reset? Yes • Go To 2 No • Perform the INTERMITTENT CONDITION diagnostic procedure. (Refer to 28 - DTC-Based Diagnostics/MODULE, Powertrain Control (PCM) - Standard Procedure). 2. CHECK THE APP SENSOR 1 1. Ignition on. 2. Disconnect the Accelerator Pedal Position Sensor harness connector. NOTE: Check connectors - Clean/repair as necessary. 3. Measure the voltage on the (F855) 5-Volt Supply circuit at the Accelerator Pedal Position Sensor harness connector. Is the voltage reading between 4.9 and 5.1 Volts? Yes • Replace the Accelerator Pedal Position Sensor in accordance with the service information. • Perform the POWERTRAIN VERIFICATION TEST - 6.7L. (Refer to 28 - DTC-Based Diagnostics/MODULE, Powertrain Control (PCM) - Standard Procedure). No • Go To 3 3. CHECK THE A/C PRESSURE SENSOR 1. Disconnect the A/C Pressure Sensor harness connector. NOTE: Check connectors - Clean/repair as necessary. 2. Measure the voltage on the (F855) 5-Volt Supply circuit at the A/C Pressure Sensor harness connector. Is the voltage reading between 4.9 and 5.1 Volts? Yes • Replace the A/C Pressure Sensor in accordance with the service information. • Perform the POWERTRAIN VERIFICATION TEST - 6.7L. (Refer to 28 - DTC-Based Diagnostics/MODULE, Powertrain Control (PCM) - Standard Procedure). No • Go To 4 4. CHECK THE (F855) 5-VOLT SUPPLY CIRCUIT FOR A SHORT TO GROUND 1. Turn the ignition off. 2. Disconnect the PCM C2 harness connector. 3. Check connectors - Clean/repair as necessary. 4. Measure the resistance between ground and the (F855) 5-Volt Supply circuit at the Accelerator Pedal Position Sensor harness connector. Is the resistance below 10k Ohms? Yes • Repair the (F855) 5-Volt Supply circuit for a short to ground. • Perform the POWERTRAIN VERIFICATION TEST - 6.7L. (Refer to 28 - DTC-Based Diagnostics/MODULE, Powertrain Control (PCM) - Standard Procedure). No • Go To 5 5. CHECK THE (F855) 5-VOLT SUPPLY CIRCUIT FOR A SHORT TO ANOTHER CIRCUIT 1. Measure the resistance between the (F855) 5-Volt Supply circuit and all other circuits at the PCM C2 harness connector. Is the resistance below 10k Ohms between the (F855) 5-Volt supply circuit and any of the circuits? Yes • Repair the short to the circuit that measured below 10k Ohms. • Perform the POWERTRAIN VERIFICATION TEST - 6.7L. (Refer to 28 - DTC-Based Diagnostics/MODULE, Powertrain Control (PCM) - Standard Procedure). No • Replace and program the Powertrain Control Module in accordance with the Service Information. • Perform the POWERTRAIN VERIFICATION TEST - 6.7L. (Refer to 28 - DTC-Based Diagnostics/MODULE, Powertrain Control (PCM) - Standard Procedure).
-
P04E4 - Crankcase Ventilation Hose Connection Sensor Circuit Intermittent/Erratic
P04E4 - Crankcase Ventilation Hose Connection Sensor Circuit Intermittent/Erratic When Monitored: Ignition on and battery voltage above 10.4 Volts. Set Condition: At key on, engine not running the Crankcase Hose Pressure Sensor Signal being sent to the Powertrain Control Module is higher or lower than a calibrated threshold. Or, during engine operation, the Crankcase Pressure Hose Sensor Signal is not changing with engine operating conditions. Possible Causes CRANKCASE HOSE PRESSURE SENSOR POWERTRAIN CONTROL MODULE (PCM) Always perform the Pre-Diagnostic Troubleshooting procedure before proceeding. (Refer to 28 - DTC-Based Diagnostics/MODULE, Powertrain Control (PCM) - Standard Procedure). Diagnostic Test 1. DTC ACTIVE 1. Turn the ignition on. 2. With the scan tool, record all Freeze frame data. 3. With the scan tool, erase DTCs. 4. Turn the ignition off for 75 seconds. 5. Start the engine and let idle for one minute. 6. With the scan tool, read DTCs. Did DTC P04E4 return? Yes • Go To 2 No • Perform the INTERMITTENT CONDITION diagnostic procedure. (Refer to 28 - DTC-Based Diagnostics/MODULE, Powertrain Control (PCM) - Standard Procedure). 2. OTHER DTCS 1. With the scan tool, continue to read DTCs.. Does the scan tool display DTC P04E2 or DTC P04E3 active? Yes • Perform the diagnostics and repairs for those active DTCs before proceeding with this diagnostic tree. No • Go To 3 3. CRANKCASE HOSE PRESSURE SENSOR 1. Turn the ignition off for 75 seconds. 2. Turn the ignition on, engine not running. 3. Disconnect the Crankcase Hose Pressure Sensor. 4. With the scan tool, read DTCs. Does the scan tool display DTC P04E2 active? Yes • Replace the Crankcase Hose Pressure Sensor in accordance with the service information. • Perform the POWERTRAIN VERIFICATION TEST - 6.7L. (Refer to 28 - DTC-Based Diagnostics/MODULE, Powertrain Control (PCM) - Standard Procedure). No • Replace the Powertrain Control Module in accordance with the service information. • Perform the POWERTRAIN VERIFICATION TEST - 6.7L. (Refer to 28 - DTC-Based Diagnostics/MODULE, Powertrain Control (PCM) - Standard Procedure).
-
P04E3 - Crankcase Ventilation Hose Connection Sensor Circuit High
P04E3 - Crankcase Ventilation Hose Connection Sensor Circuit High When Monitored: Ignition on and battery voltage above 10.4 Volts. Set Condition: The Crankcase Hose Pressure Signal being sent to the Powertrain Control Module is above a calibrated threshhold. The Powertrain Control Module (PCM) will illuminate the Malfunction Indicator Lamp (MIL) after the diagnostic runs and fails in two consecutive drive cycles. Possible Causes CRANKCASE HOSE PRESSURE SIGNAL CIRCUIT SHORT TO VOLTAGE CRANKCASE HOSE PRESSURE SIGNAL CIRCUIT OPEN/HIGH RESISTANCE CRANKCASE HOSE PRESSURE RETURN CIRCUIT OPEN/HIGH RESISTANCE CRANKCASE HOSE PRESSURE SENSOR POWERTRAIN CONTROL MODULE (PCM) Always perform the Pre-Diagnostic Troubleshooting procedure before proceeding. (Refer to 28 - DTC-Based Diagnostics/MODULE, Powertrain Control (PCM) - Standard Procedure). Diagnostic Test 1. DTC ACTIVE 1. Turn the ignition on. 2. With the scan tool, record all Freeze frame data. 3. With the scan tool, erase DTCs. 4. Turn the ignition off for 75 seconds. 5. Start the engine and let idle for one minute. 6. With the scan tool, read DTCs. Did the DTC return? Yes • Go To 2 No • Perform the INTERMITTENT CONDITION diagnostic procedure. (Refer to 28 - DTC-Based Diagnostics/MODULE, Powertrain Control (PCM) - Standard Procedure). 2. CHECK THE (K664) CRANKCASE HOSE PRESSURE SIGNAL CIRCUIT FOR A SHORT TO VOLTAGE 1. Turn the ignition off. 2. Disconnect the Crankcase Hose Pressure Sensor harness connector. 3. Measure the voltage on the (K664) Crankcase Hose Pressure Signal circuit at the Crankcase Hose Pressure Sensor harness connector. Is the voltage above 5.1 Volts? Yes • Repair the (K664) Crankcase Hose Pressure Signal circuit for a short to voltage. • Perform the POWERTRAIN VERIFICATION TEST - 6.7L. (Refer to 28 - DTC-Based Diagnostics/MODULE, Powertrain Control (PCM) - Standard Procedure). No • Go To 3 3. CHECK THE (K664) CRANKCASE HOSE PRESSURE SIGNAL CIRCUIT FOR AN OPEN/HIGH RESISTANCE 1. Disconnect the PCM C1 harness connector. 2. Measure the resistance of the (K664) Crankcase Hose Pressure Signal circuit between the Crankcase Hose Pressure Sensor harness connector and the PCM C1 harness connector. Is the resistance below 10k Ohms? Yes • Repair the (K664) Crankcase Hose Pressure Signal circuit for an open/high resistance. • Perform the POWERTRAIN VERIFICATION TEST - 6.7L. (Refer to 28 - DTC-Based Diagnostics/MODULE, Powertrain Control (PCM) - Standard Procedure). No • Go To 4 4. CHECK THE (K916) CRANKCASE HOSE PRESSURE RETURN CIRCUIT FOR AN OPEN/HIGH RESISTANCE 1. Measure the resistance of the (K916) Crankcase Hose Pressure Return circuit between the Crankcase Hose Pressure Sensor harness connector and the PCM C1 harness connector. Is the resistance below 10k Ohms? Yes • Repair the (K916) Crankcase Hose Pressure Return circuit for an open/high resistance. • Perform the POWERTRAIN VERIFICATION TEST - 6.7L. (Refer to 28 - DTC-Based Diagnostics/MODULE, Powertrain Control (PCM) - Standard Procedure). No • Go To 5 5. CRANKCASE HOSE PRESSURE SENSOR 1. Reconnect the PCM C1 harness connector. 2. Turn the ignition on. 3. With the Crankcase Hose Pressure Sensor still disconnected, check the scan tool for DTCs. Does the scan tool display DTC P04E2 active? Yes • Replace the Crankcase Hose Pressure Sensor in accordance with the service information. • Perform the POWERTRAIN VERIFICATION TEST - 6.7L. (Refer to 28 - DTC-Based Diagnostics/MODULE, Powertrain Control (PCM) - Standard Procedure). No • Replace the Powertrain Control Module in accordance with the service information. • Perform the POWERTRAIN VERIFICATION TEST - 6.7L. (Refer to 28 - DTC-Based Diagnostics/MODULE, Powertrain Control (PCM) - Standard Procedure).
-
P04E2 - Crankcase Ventilation Hose Connection Sensor Circuit
P04E2 - Crankcase Ventilation Hose Connection Sensor Circuit Low When Monitored: Ignition on and battery voltage above 10.4 Volts. Set Condition: The Crankcase Hose Pressure Signal sent to the Powertrain Control Module is below a calibrated threshhold. The Powertrain Control Module (PCM) will illuminate the Malfunction Indicator Lamp (MIL) after the diagnostic runs and fails in two consecutive drive cycles. Possible Causes CRANKCASE HOSE PRESSURE SIGNAL CIRCUIT SHORT TO GROUND CRANKCASE HOSE PRESSURE SIGNAL CIRCUIT OPEN/HIGH RESISTANCE CRANKCASE HOSE PRESSURE SENSOR POWERTRAIN CONTROL MODULE (PCM) Always perform the Pre-Diagnostic Troubleshooting procedure before proceeding. (Refer to 28 - DTC-Based Diagnostics/MODULE, Powertrain Control (PCM) - Standard Procedure). Diagnostic Test 1. DTC ACTIVE 1. Turn the ignition on. 2. With the scan tool, record all Freeze frame data. 3. With the scan tool, erase DTCs. 4. Turn the ignition off for 75 seconds. 5. Start the engine and let idle for one minute. 6. With the scan tool, read DTCs. Did the DTC return? Yes • Go To 2 No • Perform the INTERMITTENT CONDITION diagnostic procedure. (Refer to 28 - DTC-Based Diagnostics/MODULE, Powertrain Control (PCM) - Standard Procedure). 2. CHECK THE (K664) CRANKCASE HOSE PRESSURE SIGNAL CIRCUIT FOR A SHORT TO GROUND 1. Turn the ignition off. 2. Disconnect the Crankcase Hose Pressure Sensor harness connector. 3. Disconnect the PCM C1 harness connector. 4. Measure the resistance between ground and the (K664) Crankcase Hose Pressure Signal circuit at the Crankcase Hose Pressure Sensor harness connector. Is the resistance below 10k Ohms? Yes • Repair the (K664) Crankcase Hose Pressure Signal circuit for a short to ground. • Perform the POWERTRAIN VERIFICATION TEST - 6.7L. (Refer to 28 - DTC-Based Diagnostics/MODULE, Powertrain Control (PCM) - Standard Procedure). No • Go To 3 3. CHECK THE (K664) CRANKCASE HOSE PRESSURE SIGNAL CIRCUIT FOR AN OPEN/HIGH RESISTANCE 1. Measure the resistance of the (K664) Crankcase Hose Pressure Signal circuit between the Crankcase Hose Pressure Sensor harness connector and the PCM C1 harness connector. Is the resistance below 10k Ohms? Yes • Repair the (K664) Crankcase Hose Pressure Signal circuit for an open/high resistance. • Perform the POWERTRAIN VERIFICATION TEST - 6.7L. (Refer to 28 - DTC-Based Diagnostics/MODULE, Powertrain Control (PCM) - Standard Procedure). No • Go To 4 4. CHECK THE CRANKCASE HOSE PRESSURE SENSOR 1. Reconnect the PCM C1 harness connector. 2. Turn the ignition on. 3. While monitoring the scan tool, use a jumper to connect the (F857) 5-Volt Supply circuit to the (K664) Crankcase Hose Pressure Signal circuit at the Crankcase Hose Pressure Sensor harness connector. Does the scan tool display DTC P04E3 active? Yes • Replace the Crankcase Hose Pressure Sensor in accordance with the service information. • Perform the POWERTRAIN VERIFICATION TEST - 6.7L. (Refer to 28 - DTC-Based Diagnostics/MODULE, Powertrain Control (PCM) - Standard Procedure). No • Replace the Powertrain Control Module in accordance with the service information. • Perform the POWERTRAIN VERIFICATION TEST - 6.7L. (Refer to 28 - DTC-Based Diagnostics/MODULE, Powertrain Control (PCM) - Standard Procedure).
-
P04DB - Crankcase Ventilation System Disconnected
P04DB - Crankcase Ventilation System Disconnected When Monitored: Engine at operating temperature, driving at a steady speed. This monitor takes 10 minutes to completely run. Set Condition: Crankcase Pressure readings have been significantly elevated, as compared to historic trends saved in the Powertrain Control Module. Possible Causes DISCONNECTED CRANKCASE VENTILATION HOSE INTAKE SYSTEM LEAK CRANKCASE BREATHER FILTER CLOGGED Always perform the Pre-Diagnostic Troubleshooting procedure before proceeding. (Refer to 28 - DTC-Based Diagnostics/MODULE, Powertrain Control (PCM) - Standard Procedure). 1. CHECK THE CRANKCASE VENTILATION HOSE NOTE: If there are any DTCs present for the EGR Valve, EGR Airflow Control Valve, or any of the pressure sensors, perform the diagnostics for those DTCs before proceeding with this test procedure. 1. Visually inspect the Crankcase Ventilation Hose. Is the hose disconnected, cracked, pinched or damaged? Yes • Repair or replace the Crankcase Ventilation Hose in accordance with the service information. • Perform the POWERTRAIN VERIFICATION TEST - 6.7L. (Refer to 28 - DTC-Based Diagnostics/MODULE, Powertrain Control (PCM) - Standard Procedure). No • Go To 2 2. CHECK THE INTAKE SYSTEM FOR LEAKS 1. Perform the INTAKE AIR SYSTEM PRESSURE TEST diagnostic procedure. (Refer to 29 - Non-DTC Diagnostics/Drivability - Diesel - Diagnosis and Testing) . Were any Intake System leaks found? Yes • Perform the appropriate repair. • Perform the POWERTRAIN VERIFICATION TEST - 6.7L. (Refer to 28 - DTC-Based Diagnostics/MODULE, Powertrain Control (PCM) - Standard Procedure). No • Replace the Crankcase Breather Filter in accordance with the service information. • Perform the POWERTRAIN VERIFICATION TEST - 6.7L. (Refer to 28 - DTC-Based Diagnostics/MODULE, Powertrain Control (PCM) - Standard Procedure).
-
Pilothouse/RAM3500 build
I would love to see that truck when its done. I'm going to be heading east to Pigeon Forge TN. To bad I can't cross paths with you and see it sooner. I gather I'll just have to be patient.
-
Fuel Article - AirDog Draw Straw Installation
I know my camera work needs some improvement but I'm learning as quickly as a can to keep pumping videos and articles out. Hopefully this will help other install a draw straw the right way and stopping the 1/4 tank slosh issues. I've got to finish up the install of the AirDog. There will be another article on the custom install of the pump and bracket for this truck it will not be a standard install at all being the truck is not a stock fit and finish truck so this will be another article and video coming very soon.
-
Squeak/Screech noise in reverse only
Just had that same conversation with him on the phone. Great minds think a like. @Tractorman
-
Sorry guys but I've been drinking some tonight
If it was me I would keep your truck and store it away till you can deal with things easier.
-
Tire Size
Non standard tire that will most likely be difficult to get. Here is the math on the 235/75 R16 tires.
-
AirDog Draw Straw Installation
AirDog Draw Straw installation You will need a 15mm socket and 1/2 ratchet for the bands on the tank. You'll also need a flat blade screwdriver, hammer, floor jack, and a ratchet strap. The way I remove the fuel tank is to place the jack under the tank just to support the weight. Then wrap a ratchet strap around the fuel tank and hook it to the jack pivot pin. Tighten the strap lightly not enough to crush the tank. You need to take a screwdriver and hammer and lightly tap on the sender ring and loosen the ring up to allow the sender to stand up out of the fuel tank. No need to unhook any lines leave that alone for now. Now using a 15mm socket you can remove the two nuts holding the fuel tank bands up to the frame. Pull your bands down and might have to bend them a bit to get out. Then easy the fuel tank down to the floor slowly and carefully to the floor watching the sender not to damage the fuel, sender in the tank, Once the tank is on the floor the sender can be lifted out of the fuel tank and the fuel tank moved out of your way. NOTE: You'll want to have a friend or buddy help you tip the tank over and dump the fuel out of the tank. The tank needs to be empty as much as possible to get the measurement correct. The current AirDog Draw Straw is different than the older generation I have in my truck. Make sure to support the tank at the normal band locations with 2x4 boards. WARNING: Do not leave the tank laying on the floor for measuring or any work it will deflect the tank bottom inward and skew your measurements also will create the 1/4 tank slosh issues! This now requires a 1-inch hole drilled into the top of the tank. You will need to inspect the location of where you're going to install that draw straw and be sure there is nothing going to interfere with the lines or the bulkhead sticking up. Make sure to clean the area where you are going to drill the 1-inch hole. Now drill the hole and collect all the drilled crumbs without getting into the tank if possible, Grab two quarters and lay them in the bottom, and stack the straw on top of the quarters. Now using a Sharpie mark the straw at the top of the tank. Now you want to measure from the bulkhead down to your mark and take note of that measurement, Now measure from the tip back up to the same measurement and mark the cut line. NOTE: If you are using 1 quarter you want to follow the AirDog method of holes drilled in the straw. If you use 2 quarters then no notches should be required. WARNING: Cut the straw "straight". Do NOT cut the straw at an angle or anything else but straight. When the straw is cut now place the sealing washer on the bulkhead and install the draw straw. The flat washer, star washer, and nut go inside to nut the straw in. You'll want to check the gap in the straw tip to the tank bottom should be the same as the number of coins you used for the gap. The closer the better for the tip. No, the tip will not suck to the bottom, the weight of the fuel will deflect the bottom downward making more of a gap when filled. This is why closer is better. Now just install your fitting into the bulkhead connector. Now you can reinstall the fuel tank which is super easy being the fuel tank is empty and light to lift up by a single person. Just reverse the process.
-
Fuel Article - AirDog Draw Straw Installation
AirDog Draw Straw installation You will need a 15mm socket and 1/2 ratchet for the bands on the tank. You'll also need a flat blade screwdriver, hammer, floor jack, and a ratchet strap. The way I remove the fuel tank is to place the jack under the tank just to support the weight. Then wrap a ratchet strap around the fuel tank and hook it to the jack pivot pin. Tighten the strap lightly not enough to crush the tank. You need to take a screwdriver and hammer and lightly tap on the sender ring and loosen the ring up to allow the sender to stand up out of the fuel tank. No need to unhook any lines leave that alone for now. Now using a 15mm socket you can remove the two nuts holding the fuel tank bands up to the frame. Pull your bands down and might have to bend them a bit to get out. Then easy the fuel tank down to the floor slowly and carefully to the floor watching the sender not to damage the fuel, sender in the tank, Once the tank is on the floor the sender can be lifted out of the fuel tank and the fuel tank moved out of your way. NOTE: You'll want to have a friend or buddy help you tip the tank over and dump the fuel out of the tank. The tank needs to be empty as much as possible to get the measurement correct. The current AirDog Draw Straw is different than the older generation I have in my truck. Make sure to support the tank at the normal band locations with 2x4 boards. WARNING: Do not leave the tank laying on the floor for measuring or any work it will deflect the tank bottom inward and skew your measurements also will create the 1/4 tank slosh issues! This now requires a 1-inch hole drilled into the top of the tank. You will need to inspect the location of where you're going to install that draw straw and be sure there is nothing going to interfere with the lines or the bulkhead sticking up. Make sure to clean the area where you are going to drill the 1-inch hole. Now drill the hole and collect all the drilled crumbs without getting into the tank if possible, Grab two quarters and lay them in the bottom, and stack the straw on top of the quarters. Now using a Sharpie mark the straw at the top of the tank. Now you want to measure from the bulkhead down to your mark and take note of that measurement, Now measure from the tip back up to the same measurement and mark the cut line. NOTE: If you are using 1 quarter you want to follow the AirDog method of holes drilled in the straw. If you use 2 quarters then no notches should be required. WARNING: Cut the straw "straight". Do NOT cut the straw at an angle or anything else but straight. When the straw is cut now place the sealing washer on the bulkhead and install the draw straw. The flat washer, star washer, and nut go inside to nut the straw in. You'll want to check the gap in the straw tip to the tank bottom should be the same as the number of coins you used for the gap. The closer the better for the tip. No, the tip will not suck to the bottom, the weight of the fuel will deflect the bottom downward making more of a gap when filled. This is why closer is better. Now just install your fitting into the bulkhead connector. Now you can reinstall the fuel tank which is super easy being the fuel tank is empty and light to lift up by a single person. Just reverse the process. View full Cummins article