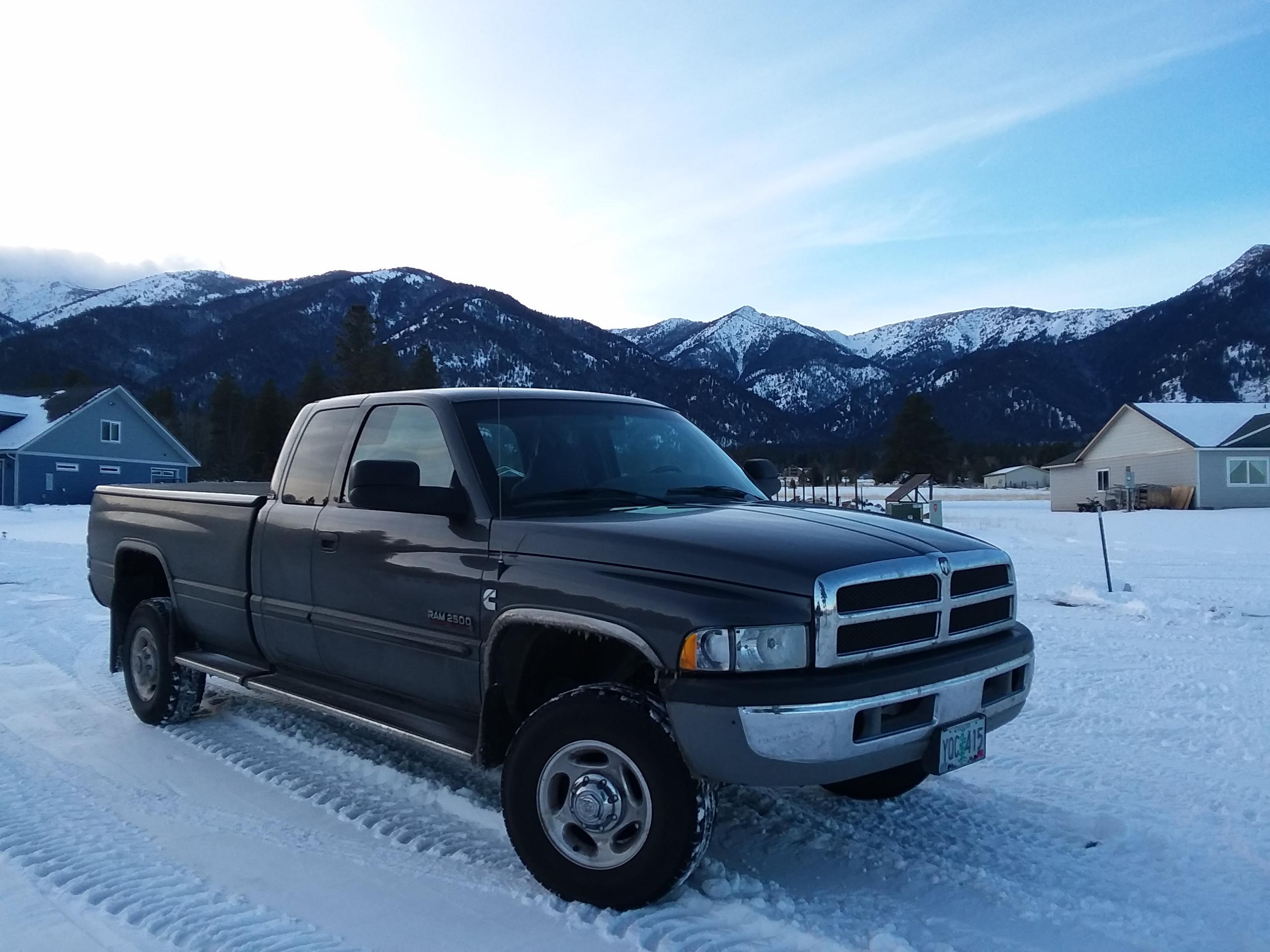
Everything posted by Tractorman
-
Allen head bolt head gasket question
Now I see why you are concerned about the high mileage original head gasket. When I return from a camping trip (leaving tomorrow) in about a week, I may post your question on the TDR (Turbo Diesel Register) and see what kind of response I get. I have settled for RV275 hp injectors and a mild tune on a Smarty S03. - John
-
Allen head bolt head gasket question
Thanks for posting the video - it definitely sheds a better light on your project. The fellow with the beard seems to know a lot about fasteners. What I have learned about fasteners over the years aligns exactly with what he is saying. Good information. I can see why you are pursuing this. Back to your project - if enough oil was left in a bolt hole, a hydraulic lock could occur when the fastener is nearing the bottom of the bore. Since oil is virtually non-compressible, the oil would be forced around the threads (spiral leakage). That could be why the fastener wants to keep turning as you near maximum torque. Did you have any issue with the washer size in your application? Just curious, as I may consider doing what you are doing. Also, are you running stock power? If not, what power level? - John
-
Allen head bolt head gasket question
I think there are too many variables in what you are trying to accomplish to make an accurate conclusion as to whether or not you will prolong the life of the head gasket. One variable is that two bolts of same thread diameter and hardness, but different shank diameters (as you have noted) could have performance differences. Those differences could affect the elastic limits of either bolt. So, while both bolts may provide an equal clamping force, one may be able to maintain its clamping force through a longer clamping stretch distance, which would perform well in a large thermal expansion / contraction range. There is no way to have that information just by looking at two different bolts. Another variable is that you are using a maximum torque specification with a torque wrench while Cummins is using a "torque to angle" specification to reach a final torque. These different applications could have different clamping force results. A third variable is that one has no way of knowing the rate of deterioration or the actual condition of the head gasket material at any given point in time during the engine's operational life. Additional clamping force may offer no help. I have the same concern as you regarding the life of my head gasket (I'm at 389,000 miles), but I have decided to run as is until I see the symptoms of a head gasket failure. It may not be the best decision, just my decision. Of course, I would also like to mention that I certainly have no expertise in this subject - only my experiences. So, when my head gasket fails and yours doesn't because you performed some pro-active measures, be sure to let me know! - John
-
Runs rough, stalls, dies, fault code P0320
To muddle your issues even more, there may not be a crank position sensor on your engine. Somewhere around the year 2001 model engines, Cummins stopped using a crankshaft position sensor began using a cam position sensor only. If this is the case with your turck, that sensor is located on the timing gear cover housing just below and close to the bottom of the VP44 injection pump. If your engine has a cam sensor, it will have 3 wires attached. One for 5 volt supply, one for ground, and one for signal to ECM (terminal #9 on the ECM). Sometimes the sensor can be faulty - sometimes the wiring or connector can be faulty. Also make sure that all battery connections and grounds are clean, tight, and in good working order. - John
-
turbo output to firewall allowable gap
I think it should work. - John
-
turbo output to firewall allowable gap
Something looks different in the bottom photo versus the top photo. It appears that you made a large cavity in the firewall? Sometimes photos are deceptive - I may not be interpreting the photo right. Are you still going to add a heat deflector on the turbo elbow? - John
-
turbo output to firewall allowable gap
I would think that there would be very little engine movement axially. Torsional movement (left or right) shouldn't have any adverse effect. Maybe a combination of a heat shield and exhaust wrap would work the best. Modify the firewall to gain as much clearance as possible, wrap the exhaust, use the bosses to mount a heat shield. Wouldn't matter if the exhaust wrap contacted the heat shield. Just allow at least 1/2" inch or more between the heat shield and the firewall for air flow. Of course, these are just my thoughts - I have no real expertise - just my own experiences. From the photo it looks like the lower boss is the closest to the firewall. It would be this area that will need the most attention to gain more more clearance by modifying the firewall. The head of a heat shield mounting bolt would consume some of that clearance. - John
-
turbo output to firewall allowable gap
It might be hard to get an exhaust wrap in that tight of space to be effective. The wrap could contact the firewall under certain operating conditions. If it did, there would be wear on the exhaust wrap and the associated noise could be annoying. What about forming a heat shield to fit in the space without contacting the exhaust or the fire wall? It would be easy to monitor for effectiveness. An effective heat shield can dissipate a lot of heat. - John
-
Aux Lighting and Negative Switching Advice
One good reason to stay with the negative switching with headlights and fog lights is because the batteries and lights are in the same compartment - under the hood. This makes it easy to run a short hot fused wire directly to the the headlights or fog lights. Then the very long and circuitous route for the ground wire from the lights into the cab, through the various control switches, and then eventually to a ground makes it impossible to blow a fuse if a wire is unintentionally grounded after leaving the headlight or fog light. It reduces the ingredients for a possible fire. But, in the end, either way will work fine. - John
-
Fog lights on randomly
Thanks for the information. The wiring diagram below is from the 2002 FSM. I don't know if it applies to your 2000 year model truck. If by chance the wiring diagram is the same, then I would check the condition of the fog light wires that were cut and repaired. The 15 amp Fuse G in the PDC supplies battery voltage directly to the fog light. If a grounding wire leaving either fog light were unintentionally grounded prior to the fog light relay, then the fog lights would come on. - John
-
Fog lights on randomly
Need more info about your truck. Is your truck a standard 2 bulb headlight system or a 4 bulb Quad headlight system? Do you have factory daytime running lights (Canadian truck)? And last, has your headlight / fog light system been modified? Also, what year and model is your truck? - John
-
Pump code P0216 is gone, but now a slight intermittent engine flutter at idle
Excellent! - John
-
Pump code P0216 is gone, but now a slight intermittent engine flutter at idle
Sounds like a good approach. Good extra step your part for re-checking the valve clearance. I agree that a faulty injection pump likely would not isolate one injector. The only way it could would be if there was a problem in the distributor head or in the constant pressure valve for the injector firing #3 cylinder. I would think a problem there would show up while the pump was being operated on the test stand. Please let us know the results after you install the new injectors. - John
-
Pump code P0216 is gone, but now a slight intermittent engine flutter at idle
@01_Cummins_4x4, have you heard anything regarding your VP44 injection pump from Oregon Fuel Injection? I am assuming that you have talked to them about your engine idle flutter. - John
-
Pump code P0216 is gone, but now a slight intermittent engine flutter at idle
I am very interested to hear the final outcome - what the actual problem is. - John Did you make any valve adjustments, or did you just check them? Just trying to rule out any other potential cause. - John
-
Forced high Idle
My brother-in-law has 2003, manual 6 spd. I will have to check his truck for the high idle feature. Thank you, - John
-
Forced high Idle
@Lund1990, what year is your truck? Also, automatic or stick? - John
-
Pump code P0216 is gone, but now a slight intermittent engine flutter at idle
No chance of that. Those remaining injectors bled themselves of air long before you even pulled out of the driveway. - John
-
Pump code P0216 is gone, but now a slight intermittent engine flutter at idle
Just out of curiosity, do you feel the slight flutter, with transmission in "Drive" at idle, or in "Park" at idle? - John
-
Pump code P0216 is gone, but now a slight intermittent engine flutter at idle
Could be related to your 150 hp injectors and the symptoms just showed up with your newly installed VP44. Maybe nothing to worry about? - John
-
Pump code P0216 is gone, but now a slight intermittent engine flutter at idle
From what I understand, there are no inputs at idle - the ECM takes over. When the throttle is returned to idle, the "idle validation switch" takes over in the APPS sensor which switches to ECM only to control idle. So, I don't think any sensors (good or bad) on the engine would be recognized by the ECM at idle. Is it just the tachometer fluctuating, or do you hear the idle fluctuate, as well? - John
-
Pump code P0216 is gone, but now a slight intermittent engine flutter at idle
I bet it felt good to hear that engine fire up and run like it is supposed to, especially after working on it until midnight to get it done.. Good job! - John
-
Rear Axle Noise
Just a followup. Jim's Drive Train Specialties finished the repair on my truck on two days ago. Jim's crew installed a Dana 80 differential overhaul kit which included axle shaft bearings, pinion bearing and pinion seal. He said that visually the ring and pinion gear looked to be in very good condition. However, after setting up the gears and checking the pattern, he said the pattern was where in should be, but there was some wear on the ring gear. He said that it would not be a problem, but it will be noisy - just not as noisy as it was before the repair. It turned out not to be noisy at all - quiet under all operating speeds on the 150 mile trip home. I am very pleased with the service from Jim's Drive Train Specialties. If anyone is needing drive train or axle work done in the Boise, Idaho area, I highly recommend these folks. - John
-
1999 24v cummins changes engine tone while keeping steady speed on highway
@daav544, here is a tire size comparison for the tire you currently have and the future tires you will install later. Below is a sample of how these different tires sizes will have a minor effect on road speed and engine torque put to the ground. The first chart reflects your bald 215/85 R16 tires (30.4" diameter) The second chart reflects the tire you are going to purchase - 235/85 R16 (31.7" diameter) The numbers high-lighted in yellow represent the direct gear (1:1 ratio) for each transmission. I can change the numbers in blue to reflect different engine rpms, different axle ratios, and different tire sizes. - John
-
1999 24v cummins changes engine tone while keeping steady speed on highway
I believe you are correct. A 245/75 R16 tire is about 30.5" inches in diameter (30.5 x 3.14 equal 95.77 inches in circumference). This is more of a perception or a "feels like" ratio comparison. I have never seen or heard of a good explanation regarding this comparison, but I think it has validity. Here is what it means to me. I am apologizing ahead of time if it gets too confusing. A lot of people believe that the 3.73:1 axle (beginning in the 3rd generation trucks) was the best axle ratio for towing performance when equipped with the stock 265/70 R17 tires and wheels. I tend to agree, it fits right in the middle of a 3.54:1 and a 4.10:1. * The 265/70 R17 tire is 31.6" diameter (3rd generation) * The 265/75 R16 tire is 31.6" diameter (2nd generation stock tire installed on later 2nd generation trucks) * The 245/75 R16 tire is 30.5" diameter (2nd generation specified on driver side door jamb) From this point on, the only way to fairly demonstrate how tire size affects different axle ratio comparisons is to find a gear that is common in all transmissions for the 2nd generation trucks and the early 3rd generation trucks. This common gear is a direct gear in which the engine rpm (transmission input shaft) and the transmission output shaft rpm are equal. The direct gear is different in different transmissions as shown below: * NV4500 - 4th is direct gear * NV5600 - 5th is direct gear * 47RH, 47RE, 48RE - 3rd with converter locked is direct gear Note that when comparing with automatic transmissions, the converter must always be locked. From this point forward it will be assumed that all axle ratio comparisons or tire size ratio comparisons or transmission comparisons will be in direct gear without mentioning the word "direct gear". So, back to the tire size and axle ratio comparisons. The standard to shoot for is the 265/70 R17 tire (31.6" dia) with a 3.73 axle on a 3rd generation truck. It turns out that the 265/75 R16 tire on the second generation truck is also 31.6" dia, but with a 3.54 axle. So, knowing that the tire diameter is the same for both trucks, the 3.73 axle will put more engine torque to the ground than the 3.54 axle. So, what if we put a 245/75 R16 tire (30.5" dia) on the 2nd generation truck? The smaller diameter will make the 3.54 axle "feel like" it is performing like a 3.69 axle - just like @Mopar1973Mansays. That's all folks. - John