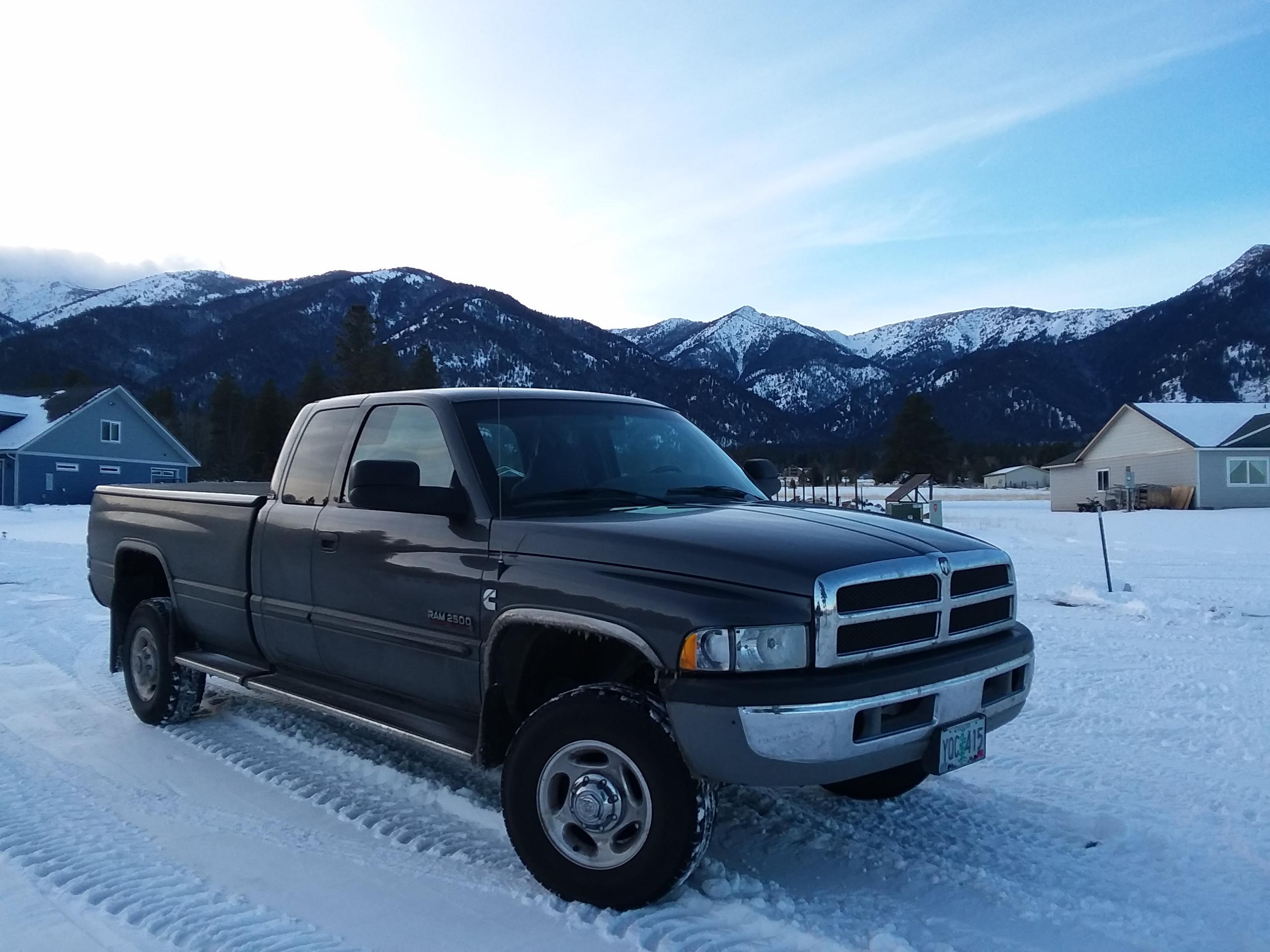
Everything posted by Tractorman
-
Batteries, Alternator, Winching, Check Gauges
@W-T, what a great troubleshooting technique! Such a simple and reliable method to test a DC motor! I do have one thing to add. I looked up the word "wench" . So, for those of you who have a wench on your front bumper AND have a significant other, the two may not mix. Be careful - especially if you hook up electricity to her. You can disregard if you have a winch on your front bumper. - John
-
Batteries, Alternator, Winching, Check Gauges
Yup, you've been busted. Shame on you! Uh....? I guess I should install mine, too. - John
-
Batteries, Alternator, Winching, Check Gauges
It is quite possible that what you are saying is true. You just won't know until you have a voltmeter attached to one of the batteries when the situation occurs. If the PCM does turn off the alternator under those conditions, it could be normal - the PCM could be protecting the alternator by stopping unusual current flow under an abnormally low voltage condition. Only a guess. - John
-
Batteries, Alternator, Winching, Check Gauges
I don't know. The only way to really know is by having a multi-meter connected to one of the batteries to measure voltage while the winch is under a load as you described earlier. This is one thing that I don't really care for regarding computers - they can be programmed in many ways to perform certain tasks under varying conditions. If you aren't privy to the program's instructions, you are not going to know what will happen under certain conditions. It could be that the alternator is still charging, but the voltmeter in the dash has been instructed to turn off when battery voltage drops to a certain threshold. Just don't know. Reading battery voltage at either battery with a multi-meter won't lie, it will tell you if the alternator is charging immediately when you stop the winch operation. - John
-
Batteries, Alternator, Winching, Check Gauges
The dash voltage gauge is fine to use for general reference, but it is not a reliable diagnostic tool. A voltage reading at each battery will tell the story. When winching current well exceeds charging current for 30 seconds at a time doesn't mean the alternator has quit charging (indicated by dash voltmeter). A voltmeter at the batteries will immediately show rising voltage when the winch is turned off if the alternator is charging. The dash voltmeter may / will not. - John
-
Batteries, Alternator, Winching, Check Gauges
First, I commend you on having a proper setup for winching, and for you giving a great description of your symptoms! When batteries and a charging system are tested to the limit (winching will do that), then the smallest inefficiencies of the electrical system can come into play. To help with figuring this out, more information is needed - mainly two factors. Was the engine at idle? Do you know the maximum current rating of the winch? Other things that could cause the symptoms: * The batteries (even though they are new) need to be at a fully charged capacity just prior to winching. * The alternator could be at fault (charging at reduced capacity) Alternator output can easily be checked at a good auto / electric shop * The heavy cable and cable connections (even though they are new and routed properly) could have one poor connection. Think of it this way - every battery cable has four connections. Example (using the battery crossover cable): passenger side battery to clamp, clamp to passenger side cable wire, cable wire to driver side clamp, and finally clamp to driver side battery. So, one wire - four connections. Multiply that by number of cables used means a heck of a lot of connections. Something that I always remind myself - an electrical system can only perform at the level of its worst connection. It only takes one poor connection to dramatically reduce performance - especially under heavy electrical load. I recommend hooking up your winch to a heavy continuous load. With a helper operating the winch, use your voltmeter to check voltage at each battery and relevant connection points while under load. - John
-
Good Source for Re-manufactured 47RE Automatic Transmission
It is not full My Inbox shows, "Used 0% messenger storage" and "storing 5 messages (max 1000)." So, I am not sure exactly what is going on. - John
-
Good Source for Re-manufactured 47RE Automatic Transmission
Thanks @Mopar1973Man. I contacted Dynamic Transmission via email a couple of hours ago. They seem to be the unanimous "go to" transmission place. - John
-
Good Source for Re-manufactured 47RE Automatic Transmission
Thank you @IBMobile, we may be moving forward with this re-builder. I just talked to my brother-in-law about the Stage II transmission from Dynamic Transmission. He has determined that he will likely be keeping the truck, so this transmission would be a good match for his needs. - John
-
Good Source for Re-manufactured 47RE Automatic Transmission
Thank you. I will check with them. - John
-
Good Source for Re-manufactured 47RE Automatic Transmission
My brother-in-law in Crescent City, CA has a 2002 4wd Cummins 2500 truck that has logged 175,000 miles. The stock automatic transmission has failed l- no second gear. I don't have any real details of the exact failure. The truck is still stock - no tuner and original injectors. The truck occasionally tows a very heavy 5th wheel (around 14,000 lbs), usually less than 200 miles round trip two or three times a year. He has no near future plans of doing anything different. Sometime down the road he may become a full-time RV-er and he will purchase a truck to match whatever he tows. I was thinking of a quality rebuild with a lower stall speed converter that would work for his current situation. Any vendor recommendations would be appreciated along with any helpful suggestions. Thank you, - John
-
Good source for a new dipstick
I never lean on a dipstick. You're not supposed to. However, once in awhile my wife leans on a dipstick. - John
-
It's always something
The lines you are referring to are vacuum lines for the operation of HVAC system ventilation doors, 4WD selection, and in your case cruise control (automatic transmission). The large 90° fitting in the middle close-up photo is the connection to the source of vacuum - the vacuum pump. You probably have many deteriorated lines / fittings that will need to be addressed due to the age of your truck. - John
-
So, I got gauges for Christmas!
I've got five daughters. Not a single one of them sent me any gauges for my truck! What the heck?! - John
-
No cold start problem.....help
Can you imagine an upside down picture of @wil440with pins in his eyes!? Here is something that will help build trust in the government. Not. In the mid '90's, my wife and I moved from Colorado to about 20 miles east of Redding, California. We built a house there on a 3.5 acre lot. At the time we had a 1985 Subaru (49 states emissions - so not California) and my 1991 Ford F150 4x4 powered by a Cummins 4BTA 4 cyl diesel engine. I was proactive in finding out what it would take to pass emissions on my truck even though the Cummins engine was emissioned for 50 states, so that includes California. Because I knew the test station would be stumped when they opened the hood on the truck, I made an appointment with the California Air Resource Board (CARB) and brought my truck to their testing station. The fellow looks under the hood for a long time. Finally, I asked if I could help with any questions he may have. He said, "No questions, I was just looking at your installation of the Cummins. We don't test diesel engines in California, but, there is a Smog Impact Fee." I said ok, how much. He said, "$400." What!!?? So, when it came time to Smog test the Subaru, the fee was around $350 - yup, Smog Impact Fee because it was only a 49 state emission engine. A few years go by. We have moved to Oregon in 1999. A few months later I get a phone call from the real estate guy that sold us our property in California - he says California is refunding millions of dollars collected for Smog Impact Fees. He told us how to file. It turns out that the money collected by CARB was deposited into the General Fund for years and used for many things that were not air quality related. We were refunded about $750. By the way, the real estate guy bought my truck with the Cummins. - John
-
Last minute prep for first measurable snowfall
Not really. Part of the "Bendix" incorporates a one-way clutch right next the to the drive gear teeth. It is likely the teeth of the starter drive gear engage the flywheel, but due to the extreme cold, the clutch slips resulting in no movement of the flywheel and lots of movement of the starter motor. The resulting friction quickly warms the slipping clutch, which then allows it to work properly the next time you engage the starter switch. You can rebuild some parts of the starter or have a shop rebuild the starter. Just don't replace the starter with another brand if it is still the OEM starter (a Denso). They are quality starters. - John
-
No cold start problem.....help
@Doubletrouble, I am glad to hear that your gelling problem has been resolved. I suspected that it may clear itself when you said that the engine ran for thirty seconds and then died with zero fuel pressure. Your subsequent attempts to keep the engine running likely brought treated fuel to the fuel filter and then to the VP44. @W-Tand I were replying to an earlier post at nearly the same time. After reading his post, I did not post my reply, but rather sent it to him just from sheer respect for his knowledge about many things. He readily suggested that I post the reply anyway. So, here it is, albeit a bit late. I personally have not done what you have suggested, but I question the ability to hear the fuel returning into the fuel tank. The volume of fuel returning to the tank is very limited because the VP44 internal vane pump is not rotating. So, the lift pump forces internal leakage around the vanes of the internal vane pump at a greatly reduced volume. That fuel works its way to the tiny orifice in the overflow valve and returns to tank. If the fuel basket is still stock, that return fuel enters the tank below fuel level. With the reduced fuel flow and with fuel returning to the tank below fuel level makes me think that it would be very difficult to hear the return fuel - assuming the fuel system has a stock fuel basket. I certainly can be wrong about this, The photo below shows the reduced volume of fuel returning to the tank with engine off and lift pump running. So, I am curious to know if you have done that procedure with your truck and were you able to hear the fuel returning into the fuel tank? Also, does your truck still use the OEM fuel basket with accompanied fuel return flow? I was also going to add that I thought it may be wiser to use the lift pump circuit in its normal operation (for 20 seconds at a time) because it was unknown where the fuel blockage / restrictions was located. If it was in the in-tank suction screen (assuming OEM fuel basket), then prolonged use of the lift pump with the blockage / restriction could possibly harm the lift pump. If the blockage / restrictions was in the fuel filter mounted on the engine (downstream), then I would not be concerned for lift pump running continuously. Once the OP said that his engine ran for about 30 seconds and then lost fuel pressure and died, I was fairly certain that his engine may run after many attempts of priming and starting, just because the treated fuel in the tank was slowly making its way to the injection pump. - John This response clearly adds value to this thread, because now we know for sure there was a gelling problem and we know for sure the cause of the gelling problem. Your last post (the most important one) is very informative and shows all of us how we can sometimes create our own problems. Thank you! - John
-
Truck Not Running Right
I do recommend to install the 150 amp fuse. This fuse will not protect the alternator as the alternator is only capable of about 130 amps under the right conditions. However, this fuse offers protection from a potential engine compartment fire. Should the an aged alternator acquire a short to ground, there will be nothing to stop very high uncontrolled current flow from two Group 27 batteries to flow directly to that short to ground through the alternator charge wire. This wire could quickly reach a nice cherry red glow and remain that way anywhere from a second or so up to a couple of minutes. Ripe conditions for an engine fire. I installed mine on my OEM air filter housing. An alternate location could be in a protected area on the fan shroud near the passenger battery. This is what I purchased from Amazon. - John
-
No cold start problem.....help
@W-T, would it be okay to send you a private message? - John
-
No cold start problem.....help
@Doubletrouble, in the early stages of diesel fuel gelling, wax crystals form. The wax crystals typically collect and block a filter or a suction screen. The rest of the fuel in lines and the fuel in the tank are usually okay. The fuel in your fuel filter may look good, but the wax crystals may have formed which will make it difficult for fuel to passed through the filter. If you have a stock fuel basket in the tank, then the fuel inlet screen is likely to be restricted in the same manner. Not much you can do about that one, except maybe build a protected area under the fuel tank and apply heat with an electric space heater - carefully! You could put a drop light with an incandescent bulb under fuel filter housing in the engine bay and block the air flow around the filter housing. I would not crack any fuel lines open anymore, as there is no benefit and you do risk introducing air each time. The likely reason the engine lost fuel pressure and died is because the VP44 internal vane pump (you know, the one nobody talks about) is pumping fine and was trying to draw fuel in faster than the lift pump and related components could provide. I don't think your lift pump is damaged. Be patient - think it through..., enjoy your Christmas Day! - John
-
Getting on site
I am only guessing here, but sometime in November I could not access the site from my computer nor my wife's Ipad. Turned out the that Mr. Nelson's updated firewall would not accept my IP address. He called me and he fixed it in a matter of minutes. Could be something like that happening to you. - John
-
Insulating Heater Hoses?
@JAG1wants to insulate them so they will already be warm when he starts his truck on a cold morning. He's thinking ahead! (Holding back sarcasm makes me physically ill, so I had to let some out) 5 below zero here this morning. - John
-
Unpaid members
You don't know!? Well, I'll be gobsmacked! - John
-
01 24v dead in the water....
I have tried several engine oil pressure switches, but they don't last. The high frequency pulses from the VP44 destroy them in a relatively short period of time, even with a snubber. The longest lasting one lasted for about a year. I installed the switch in the photo below one year ago this month (10,000 miles ago). So far, I like this one the best. It comes with 3 terminals - common, normally closed, and normally open. It is adjustable (a winner here) and comes preset at about 10 psi. I also like this one so far, mainly because it is still working! I am posting the following information because I think you have not purchased your AirDog Raptor 150Gph lift pump, yet. I think that lift pump volume is way overkill for your application. After years of thorough research I have found at least two groups of people who have installed a flow meter in the return flow line between the VP44 and the fuel tank and test drove their trucks under many different operating conditions. I have done my own fuel return flow testing of the VP44, as well, In fact, I even went one step further and disabled the lift pump and routed a hose around it. The return flow from the VP44 remained unchanged. I drove the truck for 30 miles under all kinds of throttle applications. It drove no different than it did with an operational lift pump. All of our test results have come to the same conclusion - lift pump pressure has no bearing on the volume and pressure of fuel flowing inside the VP44, or how much fuel is returning to the tank from the VP44. We have all learned that it is the VP44 internal fixed displacement vane pump that provides the fuel flow for the operational and cooling needs of the VP44 injection pump. The lift pump does not provide this. However, the lift pump does provide a flow of fuel greater than the volume required by the VP44. As long as there is a positive pressure at the inlet of the VP44, the fuel supply required will have been met, even under the most demanding VP44 operating conditions. How a fluid under pressure and flow behaves is much like how electricity behaves. In electricity you have the following:. * Electromotive force (electrical pressure) measured in volts. * Electron flow (current) measured in amperes * Resistance to electron flow (resistance) measured in ohms So you have pressure, flow, and resistance In fluids you have the following: * Pressure - usually measured in pounds per square inch (psi) * Flow - usually measured in gallons per minute (gpm) or gallons per hour (gph) * Resistance -something restricting the flow of fluid - also usually measured in pounds per square inch (psi) Again, you have pressure, flow, and resistance When working with electricity, we have relatively inexpensive meters to measure voltage, amperes, and ohms (electrical pressure, current, and resistance). We use these meters responsibly to measure the appropriate property of electricity to draw responsible conclusions. Would you modify an electrical system based on one gauge - a voltage gauge - and not consider the current flow or the resistance of electrical loads? Probably not. When working with fluids, the only inexpensive measuring device is a pressure gauge. Flow meters are very expensive and can be difficult to install. So, we usually end up with only a pressure gauge as a tool to diagnose a fluid flow problem. Without a solid understanding of the physics of fluid under pressure, flow, and resistance, diagnosing a fluid flow related problem with only a pressure gauge can be difficult. Misunderstandings of how things operate can easily occur. Now, we get to our VP44 fuel system with a pressure gauge and ONLY a pressure gauge. No flow meter in conjunction with other pressure gauges to evaluate a complex operating fuel system. Nope. Just one pressure gauge location for over 20 years of VP44 operation with many folks making decisions and drawing conclusions based on the reading from that pressure gauge without even considering fuel flow and the resistance to fuel flow. Even worse - not even considering that there is another fixed displacement feed pump in series within the same circuit (the fixed displacement vane pump inside the VP44). This is only my opinion, of course, but I completely disagree with the "it is imperative to monitor fuel pressure and prevent it from dropping below 15 PSI at all times." part of that statement. Similar statements have appeared over the years on this site stating that the VP44 could be harmed by having fuel pressure fall below 14 or 15 psi. This is simply not true. It has also been stated on this site that when fuel pressure falls below 14 psi, there is no fuel from the VP44 returning to the tank, so no VP44 cooling. Again, simply not true. W-T, my original VP44 failed at 64,000 miles and was replaced under warranty at 87,000 miles. The warranty also covered the "fix" at the time, which was to install a relayed in-tank lift pump modification. Before I took the truck in for repairs, I had already heard of the horror stories of faulty lift pumps taking out the VP44. Of course, at the time I believed them - why shouldn't I? So, I strapped a fuel gauge onto the driver side wiper arm and drove the truck back and forth to work for a week (250 miles). The lift pump pressure stayed between 12 psi (idle) and 7 psi (WOT) one hundred per cent of the time. Hmmm. After the repairs the truck drove much better. The very next day I strapped the same fuel gauge onto the wiper arm again and went for a drive. 6 psi at idle and 3 psi at 2000 rpm wide open throttle. Hmmmm..., again. I went back to the dealer and talked directly to the mechanic - a very knowledgeable guy. He said that those low readings are normal but he readily stated the he did not understand why this was the direction Chrysler decided to go. I told him not to worry about it because with my background in fluid power, I figured that as long as there was always a positive pressure at the inlet of the VP44, the VP44 would be happy, so I would be happy. I have currently logged 283,000 miles on this re-manufactured VP44. I used the in-tank lift pump for 160,000 miles (6 psi at idle, 3 psi WOT). According to a lot of information from this site, this VP44 should have been killed in short order. I elected to replace the in-tank lift pump (still working fine) with a used frame-mounted FASS (65 gph, I think) on the frame rail just in case of an in-tank lift pump failure. The used FASS lift pump shows 12 psi at idle and 6 psi at 2000 rpm WOT (with a mild tune on the Smarty S03). That lift pump is still being used and has logged over 120,000 miles. So, in conclusion my re-manufactured VP44 has never seen over 12 psi...., ever. Just for the record, I use no fuel additives nor any two-stroke oil. So...., @Basranabread, if I haven't bored you to death by now, the pressure switch in the photo can easily be adjusted to suit your needs. I adjusted mine to turn off the warning light quickly after the engine has started. I didn't set it at a specific pressure. In one way you can make it behave similar to a gauge. Set the gauge at a fuel pressure that would make the warning light come on under a heavy throttle at a specific rpm of your choice. Then when you drive your truck under those conditions, the light will begin to flicker when the fuel pressure nears your setting. @W-Tand @Mopar1973Man, I mean no disrespect to either of you. Both of you have provided information many times that has helped me resolve problems or, in many cases, has provided me information to make my truck a nicer vehicle to operate. So I thank you both for that. - John
-
New VP44 No Start! Codes P0382 , P1689
I understand. A question for you, even though it is not related to your starting issues. Does your lift pump normally keep running with the key in the run position and the engine not running? Hopefully, you have the engine started by now. - John