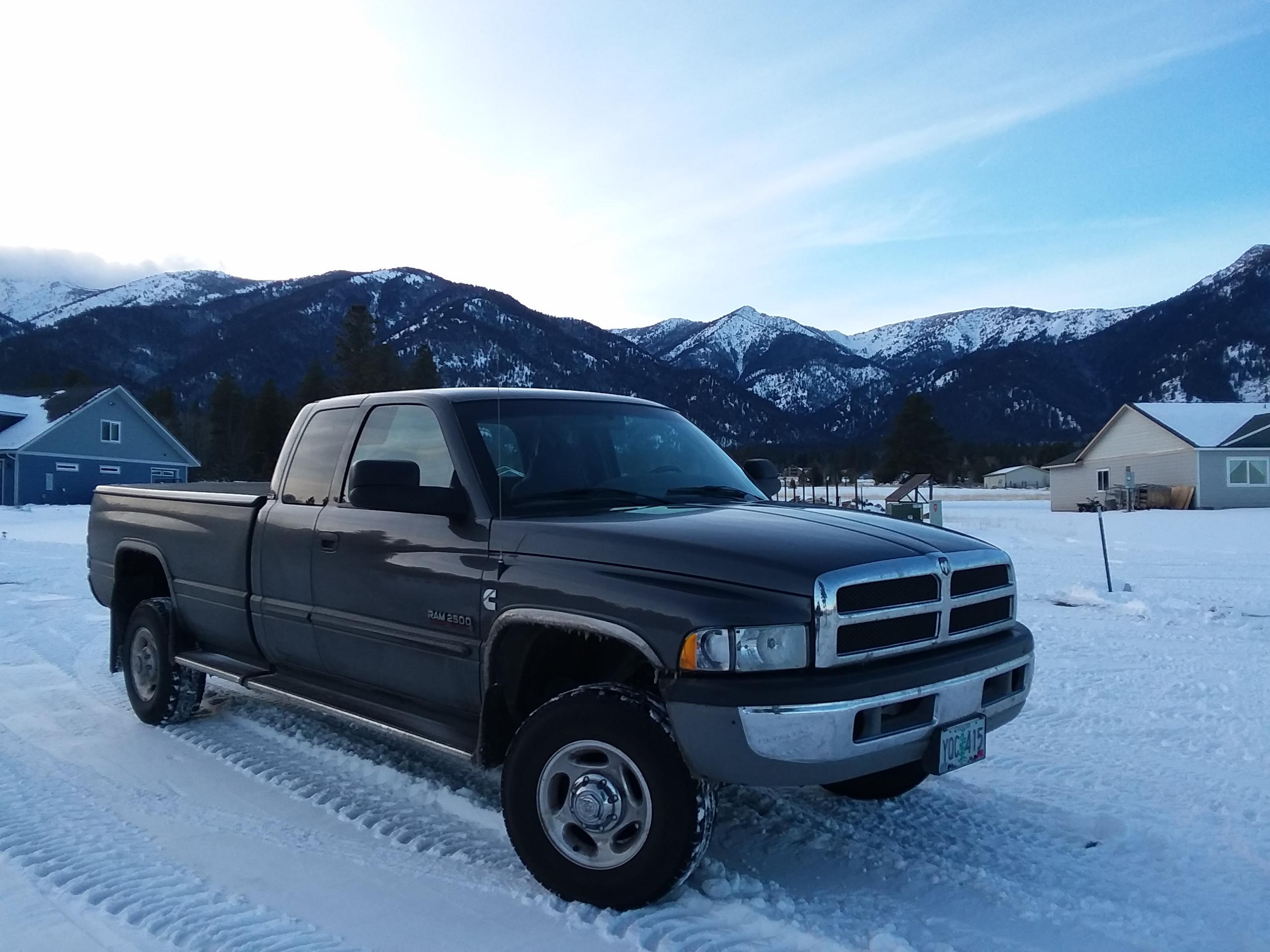
Everything posted by Tractorman
-
Road trip to Denmark..... wednesday 1st June
Probably just looking at you makes her tired. One thing about your part of the world - buildings that are hundreds of years old. Simply amazing! - John
-
Road trip to Denmark..... wednesday 1st June
The things we take for granted in the USA. I couldn't imagine crossing a border and having to drive on the other side of the road in a vehicle that wasn't designed to drive on the other side of the road. I added Sittensen to the map. - John
-
Road trip to Denmark..... wednesday 1st June
So, I placed some yellow pins on the map. Does this resemble your trip? If it does, it looks like it would be a fun trip. Enjoy! - John
-
2nd Brand New Redhead Popping
I believe he is referring to the upper and lower control arms. At this point I would have someone operate the steering wheel to repeatedly make the noise. I would crawl under the truck and with use of a stethoscope I would start checking every possible place that steering linkage or suspension components are connected to the frame or another component. Don't rule out a frame crack in another location. Components that are fastened by bolts, nuts, or rivets can leave a tell-tale sign of component movement. If there is a well defined dark line where components mate, this could indicate movement. Usually, a thin layer of road grime will cover this area if there is no movement. Keep in mind that you may be certain that a sound is coming from a specific location, but in reality the source of the sound could be from an entirely different location. Once, I had a Ford 1/2 ton truck that had a popping sound coming from the front passenger side. I could turn the steering wheel from stop to stop and make it pop. I spent lots of hours trying to figure it out. A few months later during a routine maintenance inspection, I noticed that a rivet on the transmission crossmember had a dark line where the crossmember joined the frame - turns out the rivet had lost its full clamping force. I had my wife operate the steering wheel and I could feel movement between the crossmember and frame when the popping sound occurred. I replaced the rivet with a hardened bolt, washer and nut. The popping sound from the front passenger side was gone and never came back. You'll find it... - John
-
2nd Brand New Redhead Popping
With the engine running and truck parked, can you operate the steering wheel back and forth to make the popping sound occur? - John
-
2nd Brand New Redhead Popping
@YeaImDylan, excellent job providing information! I would inspect that steering shaft closely, especially since your are feeling the pop toward the top of the steering box and especially after it would fix itself for awhile after being worked on. Years ago I replaced my original steering shaft with a Borgeson steering shaft. A thousand miles or so later the steering developed a popping noise that I could feel in the steering wheel. The feel was very subtle. It took me 25,000 miles of driving to figure out the problem. It turned out to be the slip yoke (sliding portion) on the new steering shaft. Each time I would work on the steering, the problem would go away for a few days or a few hundred miles, but it always came back. You can see in the photo below the arced spring that was used. That spring (even well lubed) intermittently would stick and not allow for axial movement of the shaft. That was the source of the popping sound. I had to removed that spring. The steering has performed flawlessly for over 120,000 miles since. This may not be your problem, but it clearly shows that some steering problem symptoms can be very hard to diagnose. Take some time to diagnose and pay close attention to cause and effect, don't just change out parts. - John
-
Max boost only with WG hose pinched
The drilled hole is a vent and it is needed to make the boost elbow work. If there is no vent, the boost flow can be restricted, but air will eventually fill the wastegate actuator chamber resulting in no change of wastegate operation, other than the wastegate will take a bit longer to open. The drilled orifice is downstream of the adjustable restrictor. The orifice will also act as a restriction, but as pressure builds the flow leaving orifice to atmosphere will match the flow passing through the adjustable restrictor at some point. When this happens, the new pressure value acting on the the wastegate actuator will now be lower than the actual boost pressure value of the air entering the boost elbow. The wastegate will not open. Yes, this is true. Exhaust flow that enters the turbine housing is exposed to some of the area of the closed wastegate valve. That area can be calculated by measuring the diameter of the exposed area. Example: Formula to calculate force. Diameter squared times .7854. (D2 x .7854) Let's say the exposed diameter of the closed wastegate valve is one-half inch. .5 x .5 x .7854 = .19635 square inches. I will round that to .20 square inches. Multiplying .20 square inches by 50 psi (turbine drive pressure) will equal 10 lbs of force pushing against a mechanical spring. The same method can be used to calculate the force of the wastegate actuator rod under a specific boost pressure. - John
-
Max boost only with WG hose pinched
I am interested to hear the results. - John
-
2nd Brand New Redhead Popping
More questions than answers... What front end parts were replaced and why? What was wrong with the old steering gearbox? So, two steering boxes were installed? When did the popping sound begin occurring (relative to repairs)? Before? After? in the middle? How many miles on the truck? on the steering parts? Has the steering shaft ever been replaced? I doubt that the steering gearbox is making the popping sound. - John
-
Max boost only with WG hose pinched
This is not surprising as marine engines have a lot more constants than truck engines have regarding air supply. For example, an ocean going vessel's engine has atmospheric pressure and air temperature surrounding it that is relatively constant. The engine is designed to move a load that will allow the engine to operate efficiently in a constant rpm range because the engine load is relatively constant. Consequently, the turbocharger can easily be sized for a marine application that will keep the turbocharger in its efficiency range without risk of over speeding the shaft - so, no wastegate needed. Truck engines on the other hand operate in more extremes of atmospheric pressure and air temperature - atmospheric pressure from sea level to over 11,000 feet in altitude, temperature from lower than minus 50°F to over 120°F. They also operate under load within a wide engine rpm band - from just off idle to a high rpm repeatedly during each gear change in the transmission. With tighter automotive emission standards, smaller turbochargers were introduced because they could supply more air into the engine's cylinders at much lower engine rpm's. This made diesel engines perform better throughout the rpm range, thus improving engine performance as well as improving emissions. To control a smaller turbocharger from over-boosting or over-speeding, a wastegate was added. I think you would be okay to use any of the methods mentioned in previous posts. I don't think there would be a significant difference in EGT's or drive pressure at 40 psi boost whether the wastegate was open or not. There are only so many oxygen molecules available to use in a given parcel of air at a given pressure and temperature to aid in the combustion process. And, of course, this whole post is just my opinion. - John
-
Max boost only with WG hose pinched
Or, just disconnect and plug the boost line to the actuator. Put a cap on the actuator side to keep out dirt. Use the tuner to set maximum boost. - John
-
Odd ABS & AC Issue
A hand operated vacuum pump is a great tool for diagnosing vacuum leaks. You should find a small vacuum manifold with many connections just above and nearby the top of the valve cover. Locate the line that goes to HVAC unit. Unplug that line and connect the vacuum pump to it. Operate the vacuum pump. After several pumps the vacuum should easily rise to 20" HG or more and hold when you stop pumping. If you cannot make this happens, you probably have found your problem. All vacuum operated HVAC systems default to defrost (for safety) when the vacuum supply is lost. As I am writing I just realized that in my first post I mentioned there could be an electrical problem as well, but after thinking about that - it is not the case. All door functions are controlled by vacuum actuators. The only exception is the blend door actuator; it is controlled electrically. - John
-
Odd ABS & AC Issue
More questions than answers. When and under what conditions did you first notice the ABS and brake warning light? the abnormal AC operation? How many times has this happened? Are the symptoms consistent? Noting that when the trailer was disconnected and the truck was driven and the ABS and brake light went out may not have any value. When an ABS lamp is lit, it will not reset until the truck is driven a certain distance above a certain speed (usually a short distance and less than 25 mph). If this problem is intermittent, the light could go out on its own, regardless of the trailer wiring connection. This condition could occur from a moderate vacuum leak or a lack of an electrical signal to carry out the command. If you turn of the engine and restart the engine two or three times, do the symptoms repeat? Thoroughly check for vacuum leaks. If possible, use a vacuum pump to supply the HVAC vacuum line only and see if the problem persists. - John
-
Replacing head gasket
Just curious, you didn't mention checking cylinder # 2, #5 and #6 - did you check them? Or, maybe you did check them and just didn't post the results. Checking all cylinders by loosening the fuel line and then documenting the results would be more conclusive than just checking some of them. The more specific relevant information you provide will likely lead to resolving the problem sooner. I have mentioned performing this test on all six cylinders in a previous post, but I have not seen any posts from you stating that you performed the complete test. If you did check all of the cylinders, let us know what the results were. - John
-
Where'd Everybody Go?
-
Okay I’ll admit it I need assistance. Post WT mod issues.
I agree. Guaranteed to cause you grief down the road. The connector damages the wire being connected into (usually breaking one or two strands) and exposes both wires to the elements which allows for further corrosion and high resistance. These trucks came with enough electrical challenges - no need to add more. - John
-
Where'd Everybody Go?
This site has been a great source for information on second generation trucks - especially VP44 trucks., but considering the newest second generation truck is now 20 years old, most of problems have been figured out. And, of course, as time goes by there will be fewer of these trucks on the road. I do think the subscription price is too high to encourage long term membership. I understand the reasons behind the price increase, but even I have considered dropping my subscription a couple of times. The main reason I stay on the site is because I have invested much time already and I have met some very knowledgeable people here. I also have turned wrenches most of my life and I like to help anyone learn a little more about their truck to be able to repair it and have the satisfaction of doing a great job performing the repairs. I am a member of the Turbo Diesel Register (since 2004). The annual subscription is $35.00, much less than the $100 annual subscription for this site. Again, I understand about this site's operational costs, but nevertheless, people are likely to shop around. - John
-
Steering questions
As you drive your truck for the next few days, make sure the steering wheel movement is very free in the straight ahead position. If steering feels like it is hanging or sticky in the straight ahead position, the adjustment is too tight. Too tight can also stress the worm gear drive assembly that interfaces with the ball nut. The adjustment you made sets a minimal clearance between the sector shaft and the ball nut and this adjustment must be done with the steering gear centered - not necessarily the steering wheel centered. When done properly, a preload will be established between the sector shaft and the ball nut with steering gear centered. When the steering gear is turned either left or right from center the preload will disappear and the clearance will grow. This is normal. Usually, this adjustment is done on the bench and the drag is measured with an inch-pound torque wrench on the steering input shaft to establish the correct preload as the steering gear passes over center. It is fine to make the adjustment on the truck, but one must remember there is no real feel for the proper setting because the steering wheel input and the pitman arm output (with associated steering linkage) will mask the feel of the expected drag when the steering gear is passing over the center position. You may already know this..., but, just in case you don't. - John
-
Does the VP44 completely shut off fueling when truck is coasting in gear on a downgrade (manual transmission)?
You made my day! - John
-
Does the VP44 completely shut off fueling when truck is coasting in gear on a downgrade (manual transmission)?
Neil, I have been thinking about how to put in words what I have enjoyed most about this conversation, but I think you nailed it in another thread you started this morning. Referring to this thread, you said, "As many would have noticed myself and @Tractorman have had what you would call a really interesting debate/aurgument in another thread, no crossed words, no fisticuffs, no nukes just different opinions, doesn't matter the outcome". I could not have said it any better. It is how you wrote that made this conversation worthwhile. Anyone who reads this conversation can easily take away what they want without having to filter through irrelevant words or thoughts, regardless of opinion. This is what I believe this forum is about - to put out the best information possible from forum members to help readers make informed decisions regarding maintenance and repairs of their Cummins powered trucks. This has been worth hijacking my own thread. - John
-
Steering questions
Have you ever had alignment checked and recorded? A positive caster of 3° to 4.5° would be a good setting for the steering to return to center well and keeping the truck tracking straight on its own. What are the miles on the truck? Is the steering gearbox original? Have you always had the death wobble, or did it just start? Check steering gearbox mounting bolts for tightness and recheck your newly installed track bar for tightness, especially where it attaches to the axle. Sometimes the bolt is not tightened enough to clamp the metal ears to the inner steel bushing inside the track bar end. Can you give details of your method of checking steering components and upper / lower ball joints? How new are the tires? Are they wearing evenly? Has the death wobble occurred before and after scheduled tire rotation? Lots of question, I know, but the more information you post, the more likely for you to get some good information from other members. - John
-
Steering questions
First, I will say that I have never experienced death wobble, nor do I know of anyone who has. However, I have done much reading on the topic over the years just because it interests me. It seems that there is no absolute cause and effect which can make diagnosing the problem very difficult. One thing that seems to stand out is that trucks with larger than stock tires and wheels favor getting the death wobble compared to trucks with stock tires and wheels. I am not in any way suggesting that larger tires / wheels are the cause, but larger tires / wheels do carry a lot more rotating mass, so when the death wobble is triggered, that energy can keep it going if conditions are right. Many have done a single repair and said, "It's cured!", only to find out that it was just masked and returned a few months later. If I were in your shoes, I would post all relevant information regarding the history of your truck such as, total miles on truck, total miles you have driven it, tire size and wheel size, when and what steering / suspension repairs have been done, etc. When did your death wobble first occur? The first thing I would is get an alignment check from a reputable shop and get a printout of the measurements for caster, camber, and toe. I would especially be interested in the caster setting. I personally don't think it would be the cause, but it could definitely be a contributor. The cause for death wobble (coming from some in-depth sources) seems to be when a specific resonance is generated by a trigger, usually a certain type of bump in the roadway. When this resonance is set in motion, it is sustained by using the energy released from dynamic suspension components and the rotating mass of the wheels / tires. The resonance has to change amplitude / frequency before it will stop. This is usually done by slowing the vehicle. Another consensus is that several slightly worn steering / suspension parts can also cause the death wobble. I would think it through thoroughly before I would start changing out components. - John
-
Does the VP44 completely shut off fueling when truck is coasting in gear on a downgrade (manual transmission)?
Yes, the four stroke cycle engine does take two crankshaft revolutions to complete one cycle. I believe I allowed for this in the first step of my calculation, "If a vehicle is decelerating with an engine speed of 1800 rpm, that would mean a camshaft speed of 900 rpm." The rest of my calculations are based on the number of camshaft revolutions, not crankshaft revolutions, so I think my numbers are correct. Maybe you can give me another double check. You wrote, "so compression and power stroke would take 0.66 seconds for one revolution and exhaust and intake take the same, 180deg per stroke for a total of 720. In your example one stroke would take 0.33 seconds ?" I am guessing just a typo error here - should be ".066" and ".033". I also did one other test the same day that really supports your "engine compression holdback" theory. As mentioned in my previous post, my testing was done in 3rd gear. I did another test at the same location using 4th gear. Here are the results: Truck stopped, engine off, 4th gear selected, park brake released, foot on brake pedal - upon releasing brake pedal truck would creep forward very slowly, slightly gaining sped, then in a few feet the truck would suddenly completely stop. This event repeated itself in lurches endlessly. In this scenario I believe the weight of the truck used gravity to push though engine friction to get the truck in motion and then the effect of engine compression definitely took over to repeatedly stop the truck. While the truck was stopped, engine compression would bleed off, thus allowing for truck movement again continuously repeating the cycle. I also think that under this condition whichever cylinder is in the power stroke would provide resistance as well, This cylinder would start to pull a vacuum while truck is in motion and then bleed off when truck is stopped. A person feels the same events when hand barring an engine over. In conclusion, I would agree that there can be significant engine compression braking, but at only extremely low engine rpm. I believe that as soon as engine rpm increases, cylinder compression efficiency increases greatly and very rapidly, becoming very efficient at higher rpm's. Consequently, the work being done by the compression stroke would be undone by the expansion of air in the following power stroke. The operation of a compression release engine brake supports this concept. I perused the internet as well and found sites supporting both of our theories. Here is some information from Wiipedia - which everyone knows is Gospel (it's as good as "I saw it on TV."). Engine Braking Gasoline engines The term "engine braking" refers to the braking effect that occurs in gasoline engines when the accelerator pedal is released. This causes fuel injection to cease and the throttle valve to close almost completely, greatly restricting forced airflow from, for example, a turbocharger. The restriction causes a strong manifold vacuum which the cylinders have to work against, sapping much of the potential energy out of the system over time and producing the majority of the engine-braking effect.[1] This vacuum manifold effect can often be amplified by a down-shift, which induces a faster spinning drivechain to engage with the engine. Engine braking is a viable method of controlling the speed at which a vehicle travels downhill. By shifting to a lower gear in a manual transmission, or selecting the "low" mode on an automatic transmission, engine braking reduces the need to repeatedly apply the foot brake, lowering the risk of the brakes overheating.[2] While some of the braking force is produced due to friction in the drive train, this is negligible compared to the effect from the manifold vacuum caused by the air-flow restriction. On an automatic transmission, engine braking often spontaneously increases the engine RPM, causing a sudden revving to occur even without applying the accelerator pedal. Diesel engines Diesel engines in personal cars provide little engine braking as they are not equipped with a throttle body and thus cannot draw a vacuum in the intake manifold. In heavy vehicles the engine is often made to provide extra braking power to take some strain off the vehicle's regular brake system and to help avoid overheating the brakes. In its simplest form this consists of a butterfly valve that stops the exhaust flow. This is referred to as an exhaust brake and mostly found on older trucks. It has a limited effect, and more advanced systems as described below are near universal on newer heavy vehicles. Compression release brake A compression release brake (also known as a Jacobs brake or "jake brake"), is the type of brake most commonly confused with real engine braking; it is used mainly in large diesel trucks and works by opening the exhaust valves at the top of the compression stroke, so the large amount of energy stored in that compressed air is not returned to the crankshaft, but is released into the atmosphere. Normally, during the compression stroke, energy is used as the upward-traveling piston compresses air in the cylinder; the compressed air then acts as a compressed spring and pushes the piston back down. However, with the jake brake in operation, the compressed air is suddenly released just before the piston begins its downward travel. Having lost the energy stored within the compressed air, there is no "spring back" so the engine must expend yet more energy pulling the piston back down again. It is very effective, however, and creates immense amounts of braking force which significantly extends friction brake life – a 565 hp (421 kW) diesel engine can produce up to 600 hp (450 kW) of braking power at 2,100 RPM.[3] Exhaust brake An exhaust brake works by causing a restriction in the exhaust, much like the intake throttle causes in a gasoline engine. In simple terms, it works by increasing the back-pressure of the exhaust. Nearly all of these brakes are butterfly valves similar to a throttle valve, mounted downstream of the turbocharger if there is one. Once again, you have forced me to "think" and consume more coffee..., - John
-
Does the VP44 completely shut off fueling when truck is coasting in gear on a downgrade (manual transmission)?
I agree with your statement, but I think the amount of energy lost would be insignificant at higher engine rpm's. If a vehicle is decelerating with an engine speed of 1800 rpm, that would mean a camshaft speed of 900 rpm. Dividing 900 rpm by 60 seconds equals 15 revolutions per second. Dividing one second by 15 revolutions equals .066 seconds to complete one revolution. This means that four strokes of the four stroke cycle are completed in .066 seconds. This would also mean the time to complete the compression and power stroke (two strokes) would be .033 seconds, or the time to complete the power stoke only, would be about .017 seconds. I just can't visualize that much energy being lost in 17 micro seconds. Feel free to double check my math. Not necessary to perform the test because you and I would agree with the results - yes, first gear would be slower. But, I am saying it would be slower for a different reason. That reason would be resistance from friction (overcoming engine internal resistance by forcing the engine to rotate) which applies to all engines. I did perform a test that I think demonstrates this. I have a level tool that allows me to measure percent of a grade. I found a down grade that averaged just over 3 percent and performed the following tests. Test #1. With truck stopped, engine off, transmission in 3rd gear, park brake released - truck did not move (observed this condition for over a minute). This indicates to me that engine friction in combination with gear reduction is holding the truck from moving. Any compressed air in a cylinder on compression stroke would have long been bled off. Test #2. Started engine and brought truck up to 20 mph in 3rd gear, then shut off engine. Truck speed very slowly began to increase. This indicates to me that engine compression is not doing much to hold the truck back. This testing may not be very scientific, but it supports how I think it should work. I think I hijacked my own thread...., - John P.S. I posted this late so you would have something to look forward to in the morning.
-
Does the VP44 completely shut off fueling when truck is coasting in gear on a downgrade (manual transmission)?
Not arguing this point. but it seems that your focus is on the compression stroke only with no consideration of what happens on the next stroke (the power stroke) which is key. At the beginning of the power stroke the cylinder is filled with stored energy in the from of highly compressed air just generated by the previous compression stroke. That stored energy will now drive the piston downward with the same force that was used to compress the air in the first place. Compression stroke - stores energy in the form of highly compressed air by resisting and slowing the upward speed of the piston - results in momentary engine braking . Power stroke - releases energy of same parcel of highly compressed air driving the piston downward and accelerating the downward speed of the piston - results in no engine braking and piston acceleration is momentary. The actions of the compression stroke and power stroke cancel each other which nets zero engine braking. The number of cylinders in an engine is not relevant as each cylinder operates independently in the four stroke cycle process. This is why I simplified my explanation using a single cylinder engine. The only thing individual cylinders have in common are air intake, exhaust outlet, and crankshaft connection. If this is true, then can you offer an explanation of what is happening with energy from the highly compressed air during the power stroke? Just want you to know that I have always respected your point of view and continue to do so - you have clearly shown that you are a knowledgeable person through many posts on this forum. In the end we may have to agree to disagree, which is okay with me - John