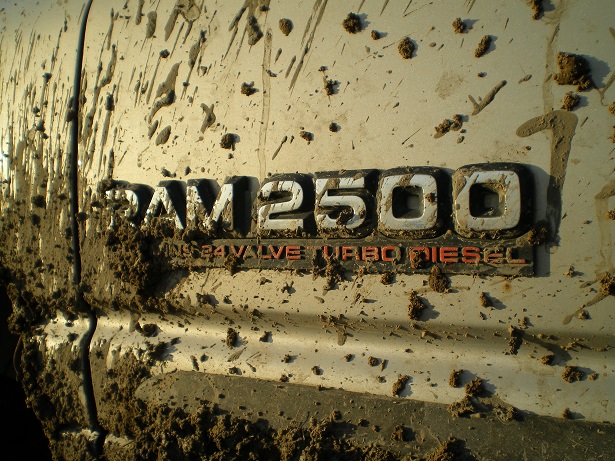
Everything posted by CUMMINSDIESELPWR
-
relay board and accessory power feed
just picked up a tackle box bin to house it in then mount it. pics sometime soon, can only do so much at on time still from injuries
-
relay board and accessory power feed
so i have lights and radios to power and needed to make my own power distro board. here it is. Took 3 hours to build from raw materials and it has 5 fused relays that will be switch operated along with 3 direct fused power links for my two radios and an accessory if needed. $350 to buy prebuilt but not designed perfect $125 was my cost of materials. it is better in my eyes with how i made it. when i have everything installed ill take pics (this eliminates the rats nest of wires to battery)
-
Front Crank Seal Help .... and show and tell of what the dealer did
i installed mine by hand on original oem cover on a workbench. started it with fingers and tapping with deadblow to get it in, then with a 2x4 i whacked it till it was flush with lip, then used the install tool which set it into the housing about 1/4" (from front) and it has worked fine. strange you have so many issues with yours
-
Front Crank Seal Help .... and show and tell of what the dealer did
you MUST install the seal from the front. using the tool from the front drive it all the way home till the lip of the tool if flush with the cover housing lip. The part of the tool that goes down into the cover is what evenly seats the seal. its a PITA to start but once started (using a 2x4 to get even impact pressure) work your way around the tool lip and seat the seal. Dont be afraid to put some punch into it, i used a 6lb deadblow and was hammering pretty good to seat it. and congrats on installing the speedy sleeve! here for example using the cummins install tool on the rear seal by seating it from the "front" of the seal housing. first picture shows the seal seated all the way with the tool resting on the face of the seal housing, and second pic is where the seal sits in the housing from the rear. the tool sets the depth perfect so go in from the front, set it and forget it. DONT pound on it from the rear you will damage it.
-
Front Crank Seal Help .... and show and tell of what the dealer did
mine didnt, thus why i tapped gently to seat it without ruining it. went well actually, but i do recommend the tool if possible.
-
Front Crank Seal Help .... and show and tell of what the dealer did
found this and it might help you, they make a sleeve install tool! i installed with hammer as my crank was sitting on the workbench.
-
Front Crank Seal Help .... and show and tell of what the dealer did
the sleeve i didnt use a 2x4. and i dont suggest using a 2x4. the sleeve will best go on one way and basically gently tap it in a circle to seat it. using a 2x4 will get it off center and ruin it etc etc. it took me about 25-30 minutes of gently tapping it on the crank all the way till its flush on the front. then install front seal onto cover and install cover. iirc the speedy sleeve will have a beveled side and that side goes on first then gently tap it in circles to seat. if it doesnt go on just a tad at first by hand, flip it over and try to push it on by hand, it should start itself slightly on its own. oh and locktite on the speedy sleeve, never heard it. its a interference fit (sleeve fits tight on its own) and i have over 3-4000 miles on my rebuild no issues. Also the damper will keep it from walking forward. I highly doubt the steel on steel friction fit will come loose due to the slight friction of the seal. zoom in on the crank and you will see the thickness of the speedy sleeve. it was about 1/8" thick. the shop installed a speedy sleeve that was paper thin and i removed it and installed the cummins thicker speedy sleeve with matching seal. i also recommend test fitting the seal onto the speedy sleeve before hand to ensure it all is properly fitting then install everything. "measure twice cut once thing"
-
Front Crank Seal Help .... and show and tell of what the dealer did
i did a genuine cummins speedy sleeve myself on my rebuild as the crank had a groove in it. i used the cummins seal install tool and pounded away to get the seal started and after a bit of finesse it went in. The tool will bottom out on the cover and thats when its seated all the way. Install was easy, with the plastic install tool in the seal, slip it over the crankand push the cover on. Note the seal goes on dry and dust free. I have had no issues with mine since rebuild. It was weeping a little as the groove was pronounced and the original seal was worn. oh and it looks like the seal is installed correct, but how it was installed (from the rear or with improper tool) could have caused the seal to become warped or damaged allowing leakage. Plus that RTV is not helping...
-
Could really use some help - Engine knock
you can always do studs later on without removing the head. just gotta do them one at a time then torque, drive for a bit then torque again or whatever the procedure is for arp studs
-
Could really use some help - Engine knock
my truck has rv275 sticks and drives real nice, plenty o power on stock everything. but i mostly use a low setting on the juice to keep from smoking. i have it set to defuel at 30psi as well and 1250F to keep everything reliable and happy
-
Could really use some help - Engine knock
here is a place in florida that sells used engines at good prices. http://www.mylittlesalesman.com/find/cummins-59l-engines-i4c235f575m166280?maxyear=2001
-
cummins 24v/Valve seal/spring/valve replacement 24v head
Below is a video of replacing the valve seals on a 24 valve cummins engine. first get a valve compression tool that is for the 24v head. remove injector hold down bolt bolt base of tool to the injector hold down bolt holes snug is fine place top of tool on springs centering over valve stems with the greased nut, tighten tool down until all the valve stem keepers are retrievable many times the valve seat will stick to the keepers and will need to be broken loose with a socket and hammer to free them (see in video) pull keepers keys (2 halves) with a magnet and place on a template for each valve (do not mix any parts to other valves) loosen tool and remove plate take springs and keeper seats off and place in there designated holder with pliers, grip and twist and pull the old seals off clean seal seats as there will be crud under them from oil and soot yellow seals are intake14mm deepwell socket to drive these green seals are exhaust 13mm deepwell socket to drive these replace yellow for yellow and green for green after cleaning seal seats on head place each spring and keeper seats back to original positions and ensure they are seated in the head properly (not sitting on a machined lip) then pull on each valve stem to make sure they are all the way up place tool plate back on and centered place nut back on the tool and torque down to where you are able to place the keepers back in once keepers are put into the "keeper pocket" push the valve down a little to get the keepers to grab the valve stem (may need to elevate the head a bit to get clearance to do this) when all keepers are preset, untorque the tool and watch the springs to ensure they grab the keepers and they sit in the pocket properly when pressure is off remove top of tool and remove bottom of tool re-install injector hold down bolt with a dab of BLUE loctite inspect all 4 valves for proper re-installation done if valves are to be replaced or different springs are to be replaced it is the same steps outlined above. for more details please watch video below. http://youtu.be/BpSH_BzKq6k
-
Could really use some help - Engine knock
thats pretty darn good!
-
The time has come to produce the Mopar1973Man High Idle & MPG fooler switches again.
thank you sir
-
The time has come to produce the Mopar1973Man High Idle & MPG fooler switches again.
Mike, when is the next batch of switches going to be available? also do you have the new link to this tsb? id like to print it out and get my truck flashed to enable high idle etc...
-
Could really use some help - Engine knock
swapping an engine with 2 people will take at most 4 days or less if someone knows what all needs to be disconnected and reconnected. I put mine in with a helper in one day and had it running. the next day i put all the accessories back on and had it on the road.
-
Could really use some help - Engine knock
yeah i saw that, i need to open up a rebuild shop lol
-
Could really use some help - Engine knock
$10,000 to rebuild a 24v?????? I rebuilt mine with new pistons,rings,bearings,gaskets also with a polish on the crank and a .20 overbore for under $3500, runs strong and reliable. Just giving you a real estimate if you did it yourself. you will pay more for a used engine probably. I have a article on a poor mans garage rebuild in the database, lists the steps of putting it back together. hardest part was getting all the accessories off and putting them back on. I took my time and had the engine put together in a total of about 12 hours by myself. If you can find a garage for a couple weeks, order all the stuff you need, get the engine apart and order the rest of the stuff you need then slap it back together.
-
Driveshaft Center Carrier Bearing
So this thread is an illustration of me actually doing the work. What is not in the commentary in the photos is the axle center bearing has to be pressed off with a 12ton press. The new bearing and the bearing replacement was done at Englewood Driveshafts Inc (Denver). Bill was the one who replaced the bearing after i removed the driveshafts and brought the front portion to him. The new bearing,rubber damper,bearing removel and replacement was less than $100. He was very nice to tell me how it was put on, a few tricks next time and he let me watch most of the work in his shop. Total time to replace just the bearing appx 20 minutes. Total time from start to finish if done all at once appx 3 hours (drive time included in that). I was able to do this by myself, you just need to ensure not to let the parts come crashing down on you and injuring you. When after the bearing was replaced, assemblage of all the components is exactly backwards from the removal. start with inserting the front shaft into the transfer case,bolting the bearing carrier to the drop down hangar, bolt the hangar to the crossmember with the 4 bolts, slide on the rear portion of the shaft, crimp on the new strap on the boot, align the rear ujoint to the axle input yoke, ensure the cups are set into the yoke properly (you will see the clean pressure points on the cups, match these to the yoke). Then put a touch of loktite on the 4 small bolts, torque them per MFG specs (will update with torqe specs). Test drive to ensure no weird vibrations or issues. You are looking for PN: 04773014 Amazon http://www.amazon.com/Mopar-Drive-Center-Support-Bearing/dp/B00MJ2MMGW/ref=sr_1_1?ie=UTF8&qid=1458702477&sr=8-1&keywords=04773014. Ebay http://www.ebay.com/sch/i.html?_from=R40&_trksid=p2047675.m570.l1313.TR0.TRC0.A0.H0.X04773014..TRS5&_nkw=04773014.&_sacat=0 DONE!
- 1 review
-
-
- 2
-
-
Another one learn the cold truth of a fuel pressure gauge
highly recommend fuel boss. its mechanical and increases psi when more power is put to engine. the belts are $15 each (if they ever break) and ive had mine on for well over 15,000-20,000 miles and no issues so far. i dont worry about fuel psi anymore. yes i have a gauge lol
-
Could really use some help - Engine knock
this was my #6 from cold start from oil cooling starvation from metal being made by lugging the engine towing a load. at 9-10 sec you can hear the first hollow pong sound as the cylinder warms up enough to combust then knock. full engine rebuild this is an injector knock (after rebuild and before break-in). the time my injector pump sat in the engine bay during rebuild something got stuck in it and caused the injector knock. i drove it around later that day couple times around the block and it cleared. this is what it sounded like as soon as it cleared a few minutes later
-
Could really use some help - Engine knock
like wild and free stated, start on the easy stuff get it out of the way. crack the injector and if the knock goes away it is highly caused by fuel
-
Could really use some help - Engine knock
not to scare ya but i dont think its a fuel issue either. either a valve issue wristpin failure or conrod bearing failing (piston slap), i can hear the bang come after the compression/ignition stroke and it might be slapping the piston onto the head during the exhaust stroke just my $.02 hope you find the issue and its an easy fix
-
inexpensive borescope
check out the first page, i posted a pic of the scope looking at my motherboard from about 2" away. the light is coming from the borescope camera as well. im satisfied with it. for $7-12 you cant lose when using it to see the health of the piston or other uses that happen infrequently
-
inexpensive borescope
friend of mine is sending me a couple galaxy s3's to repair and ill put one together as a toolbox kit. ill also send screenshots of it in use when i get it all together.