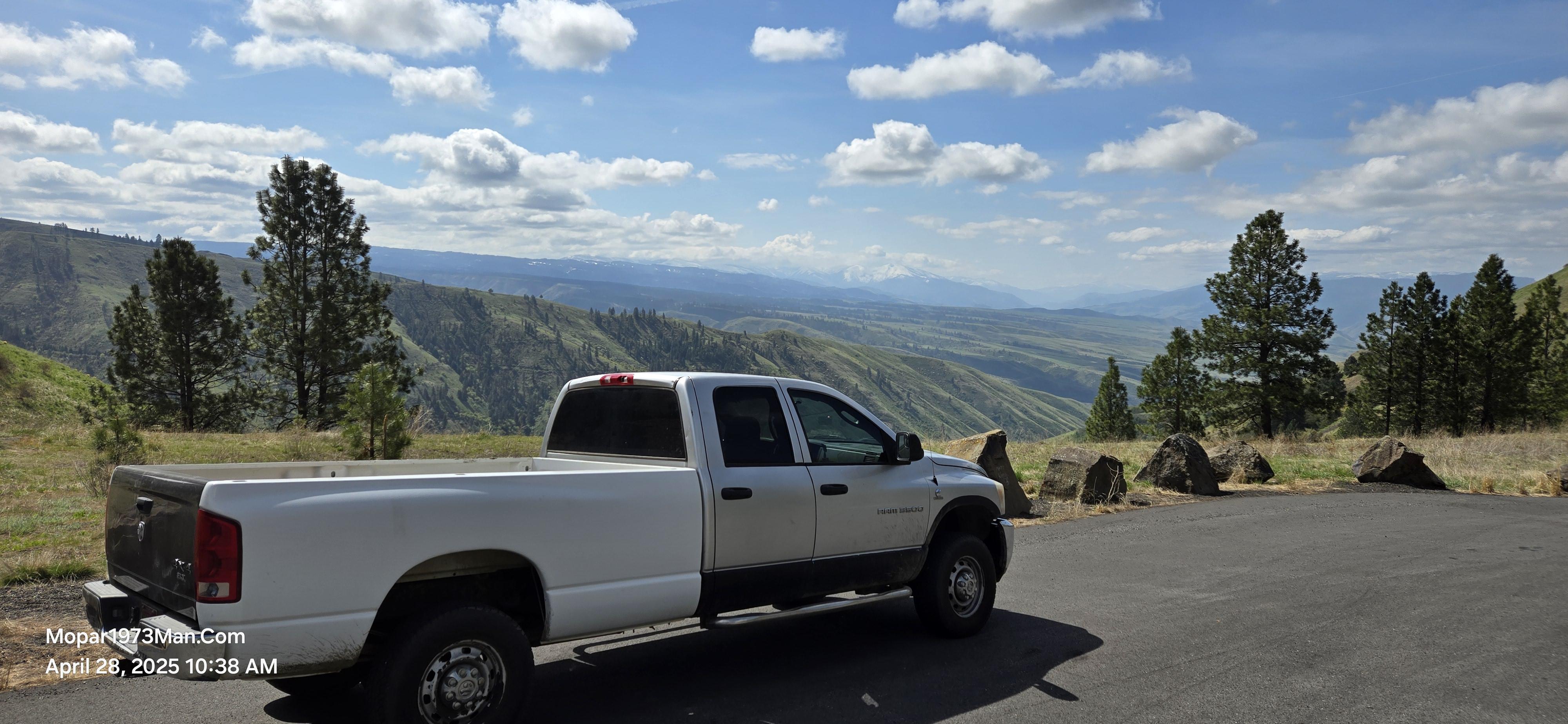
Mopar1973Man
Owner
-
Joined
-
Last visited
-
Currently
Viewing Topic: Flashing WTS light
Everything posted by Mopar1973Man
-
Ford 6.7L issues
https://www.tiktok.com/t/ZT2HEpJHN/ https://www.tiktok.com/t/ZT2HEt7QF/
-
ECM failure
Thank you for the kind words. Personally I'm looking for people that are willing to write articles about repairs and information on repairing these trucks. Im going to move forward into 3rd Gen to put Thor at the top of the focus. I need to expand knowledge into newer generations. A lot of info is trapped in my head and needs to get put into HTML5 code for all to see and learn from. Thanks for the comment.
-
Internet speeds
Mopar1973Man replied to Mopar1973Man's topic in Linux Computers, Networks, and Servers's Linux Computer SupportInteresting, I found that my network is viewable directly over the Omada App. Like today, I'm down in Boise with @Tweety Bird and I started playing with my phone. Sure enough, my network is viewable from my cellphone. I'm going to do some experiments on this and see if i could bind a URL to my home server; and port forward to the world wide web, possibly. At this point, I could very well create a Private Cloud for our own use as I travel for medical reasons and be able to handle all the website needs without being home. Still wondering if I could complete a port forward say 22 and 80 out to the web. Time to get crafty.
-
ECM failure
Gotta ask where did you get the pedal assembly? Also would you be willing to write an article on how you did this?
-
47RE kicking out of O/D
Yeah band adjust should be done every 30k with filter and fluid change. Grab a FSM is going to have the torque specs and slack
-
Transfer case Oil
Note: All ATF+4 in all synthetic oil and brand name doesn't matter. All have the same specs minimum wise. NAPA ATF+4 is just the same and half the cost at times.
-
Transfer case Oil
I've ran both dextron and ATF+4 for transfer case fluids. Beast with 495k miles I've never had any issues including summer heat in Arizona. Only had to reseal the case once.
-
Internet speeds
Mopar1973Man replied to Mopar1973Man's topic in Linux Computers, Networks, and Servers's Linux Computer SupportJust completed hooking up a network switch for Mark to have in his place to plug in other network stuff to CAT5 Cable. We ran a test on his old computer running 24.04 Ubuntu Linux and... Feb. 22, 2025 SpaceX / Starlink speed test... Beauty of this network. Im firewall secure. Im also behind the firewall of Starlink (CGNAT). Then hooked up IPv6 internet address system. My WiFi is separate from the cabled network so people on WiFi can't see any of my PCs (cable driven). I've had several WiFi devices hoping on from neighbors wanting to get any signal. My neighbor to the south has no internet. So her kids jump on when visiting. Cat5 cable devices - 192.168.0.xxx Guest WiFi - 192.168.10.xxx Private WiFi - 192.168.20.xxx My guest users are limited to 10Mbits down and 5Mbits up. Private WiFi is unrestricted. Then Cat5 cable devices are even faster at a full 1Gbit up or down. All device are load balanced too so no one can horde the bandwidth. My guest account is without any password and fully open to any one to use even broke down people stuck along the highway. My outdoor WiFi is 1/4 watt and transmits over 700 feet. My indoor heads are also 1/4 watt too but 2.4GHz and 5 GHz frequencies biased towards 5GHz first for speed and auto-magically backs down to 2.4GHz for range when needed. Managed Controller TP-Link SG2428 and Gateway ER605 Starlink dish and my outdoor WiFi antenna.
-
ECM failure
Shoot the WIF plug with brake clean. Then bag the end and zip tie. Any moisture or oil will cause the light to come on. Typically I always leave the stock filter in place and get the big line kit from @dieselautopower. This way you don't have this issue, manifold coolant heat will warm the fuel up.
-
2006 Dodge Ram 3500 - Thor Project
Great minds think alike. I just filled Thor rim full with 98 dollars of fuel and got the bed off and its dry up top of the module and pump is drowning in the tank.
-
2006 Dodge Ram 3500 - Thor Project
No need when no fuel is leaking out. If you can remove the banjo bolt lightly tweak the line a little and fire it up and watch the PRV top for any changes. No leakage of fuel. Oh just fun to now have a 3 chime grid heater light. I WANNA KNOW WHAT THESE CHIMES MEAN. As for what I've done today. Mark was a huge help getting the a frame out and then getting the bed cut free from the frame. You have no idea how wild it was to keep lifting the bed and watch the weight transfer and seeing the natural rake of stance return. That bed is farking heavy! Those rear spring had alot of weight.
-
2006 Dodge Ram 3500 - Thor Project
Now on Thor i went through and for sure torqued all crossovers to Industrial injection specs of 44 ft/lbs and then added 4 more on a second pass on torque. Now... I need the chime list for sure. Drove the truck runs way better and more power. Still extremely long starting and loss of prime instantly. Turn off the engine and prime is gone instantly. Also my repaired injector #1 is now tossing P0301 code misfire cylinder one. Chime list - 1, 5, 7, 8, and 10 chimes with grid heater light. Every cycle I would either clear the light with my code reader or it would self reset just idling. I've call Industrial Injection only thing he's will do is sell me a entire fuel system for $4k. Nope not happening. Alligator performance was helpful but no clue on chimes or meanings. Again just would sell a full fuel system, injectors, cross over tubes, cp3, and rail pressure sensor with relief valve. I'm looking for that chime list. Now @dieselautopower I talked to Lenny and he's going to retest everything for me again being this is the 4th time pulling these injectors in under 1,000 miles.
-
Edit profile
Thank you sir. Wedding will happen in the spring time no hard date yet. Cancer wise yeah I'm clean but but fighting several other issues. Kidney functions etc.
-
New Life and New Body with issues...
I'm ok with a full face mask through the night. I've experienced @Tweety Bird machine and started sleeping great. I'm in process of getting my own machine and setup. As for my new doctor he agrees with moving forward on getting a CPAP being I get slow to breathe or occasionally pause for long periods. Good O² levels actual retard my pain in my back and swelling. My back will never get better. Is just normal degeneration of my lower back. Getting old hurts and you gotta be tough. As for the kidneys my new doctor is scheduling all all kinds of labs, and procedures for me very soon. Wait and see time. Even got a kidney specialist diving in to attempt to wake my kidneys up.
-
Internet speeds
-
New Life and New Body with issues...
6 month check up done. Cancer free is the good news. Bad news my right kidney is taking damage and struggling. I've just switched over to a local doctor to look it over and he's setting me up with a kidney specialist to get this all figured out so I gain my full kidney function back. Then during all this I found why my back issues and my pain / blood pressure is from my L3 and L4 have been compressing my disc which now gives my that numb area for my kidneys but lower back pain. This isn't get better sadly. Final got a doctor to give me a 40 pound weight limit for lifting. Now ive got to relay this to my PT doctor my lifting limits. On top of all my issues now toss in sleep apnea so I'm currently working by video chat to get a sleep lab done to set me up on CPAP machine. My days are super busy most days.
-
Hello Everyone!
Yup it is true. Strange enough I was in full makeup when we met both times. She enjoys my artistry of my makeup and wigs which she continues to encourage me to learn more about the art. Yeah after I did give Suzanna my number it seemed like there was so many questions and so much to talk about most of our phone calls went till 2am most nights. Strange some night we still just talk till early hours. Yes it's true we plan on getting married in the spring of the year. Suzanna was amazed by what I've created with Beast. She enjoys good Cummins power. Now we both want to build into 3rd and 4th Gen lines hence why the active work on Thor to attempt to give me time to repair Beast which is nearly 500k miles now. There is a lot going on with software changes, server changes, and even things on the site. Suzanna and I are going to fix the website up and bring more newer generations to the article database. Right now I'm just cleaning up after moving servers to cut operational costs.
-
Edit profile
3 bar menu button at the top right. Then select account on the slide out menu. Then tap profile. Then up in the top area look for a Edit Pencil in the picture area up top. Then will open the edit window.
-
ECM or something else?
Might read here for more info... https://mopar1973man.com/cummins/articles.html/24-valve-2nd-generation_50/51_engine/swapping-vp44-cummins-engine-between-985-00-01-02-r429/?do=getNewComment&d=4&id=429
-
High boost error code
Boost fooler damaged on the Quadzilla module? Wiring issues to the Quadzilla module? Proper wiring used on the Quadzilla? (No hacking up the connector to fit a later series?) Since the boost number is high on the Quadzilla I would have both the module and the wiring checked.
-
47RE kicking out of O/D
What kind of mileage since the rebuild?
-
Subscription
Thank you for the wonderful comment. Truth yes it's still paying to keep the server alive and keep paying the bills. Remember Mopar1973Man.Com is the LAST PRIVATELY OWNED WEBSITE left. I'm not owned by a corporate clearing house like Cummins Forum which is owned by VerticalScope Inc. Or DieselBombers which is owned by Internet Brands. All these other websites are corporate owned groups.
-
2006 Dodge Ram 3500 - Thor Project
-
My personal network
Mopar1973Man replied to Mopar1973Man's topic in Linux Computers, Networks, and Servers's Linux Computer SupportReturning back to this topic and sharing more information. I've learned quite a bit more about my network and security. Boy can I show you all kinds of cool tricks. For example, I've managed to create a VLAN for my Mopar1973Man Guest WiFi. When you hook up to my guest account it moves from the default network and creates a new network with a totally different IP address. This hides my private network completely. Now the family here we have our own network to work together between people we can all see either other to be able to share information flawlessly. My basic network but all works so amazing. At the hub of it is the Starlink internet provider. This has been awesome for the internet speed and will handle quite a bit of network traffic. Then I've got a ER605 Gateway providing a firewall into the network here. Then my 28 port managed switch which is the brains of the network also the power supply for all PoE devices. As you can see there is 192.168.0.x, 192.168.10.x, and 192.168.20.x. The 192.168.0.x is all my hard wired stuff like PCs, cameras, etc. You must use a hard wired jack to gain access to this network. Then the 192.168.10.x is all my guest network which can't see anything but themselves in their pool but have zero access to the private network at all. Then the 192.168.20.x is all my stuff that uses WiFi like cellphones, TVs, game consoles like the Xbox.
-
2006 Dodge Ram 3500 - Thor Project
No problem grid heater light pops on it locks to 19k to 20k rail pressure cruising faster than 40 MPH. Everyone here is like nope stay in day too cold to mess around as well the sun is heading down, shadows are coming, temperature already failing. Try again tomorrow. Yes I know date and time are wrong.