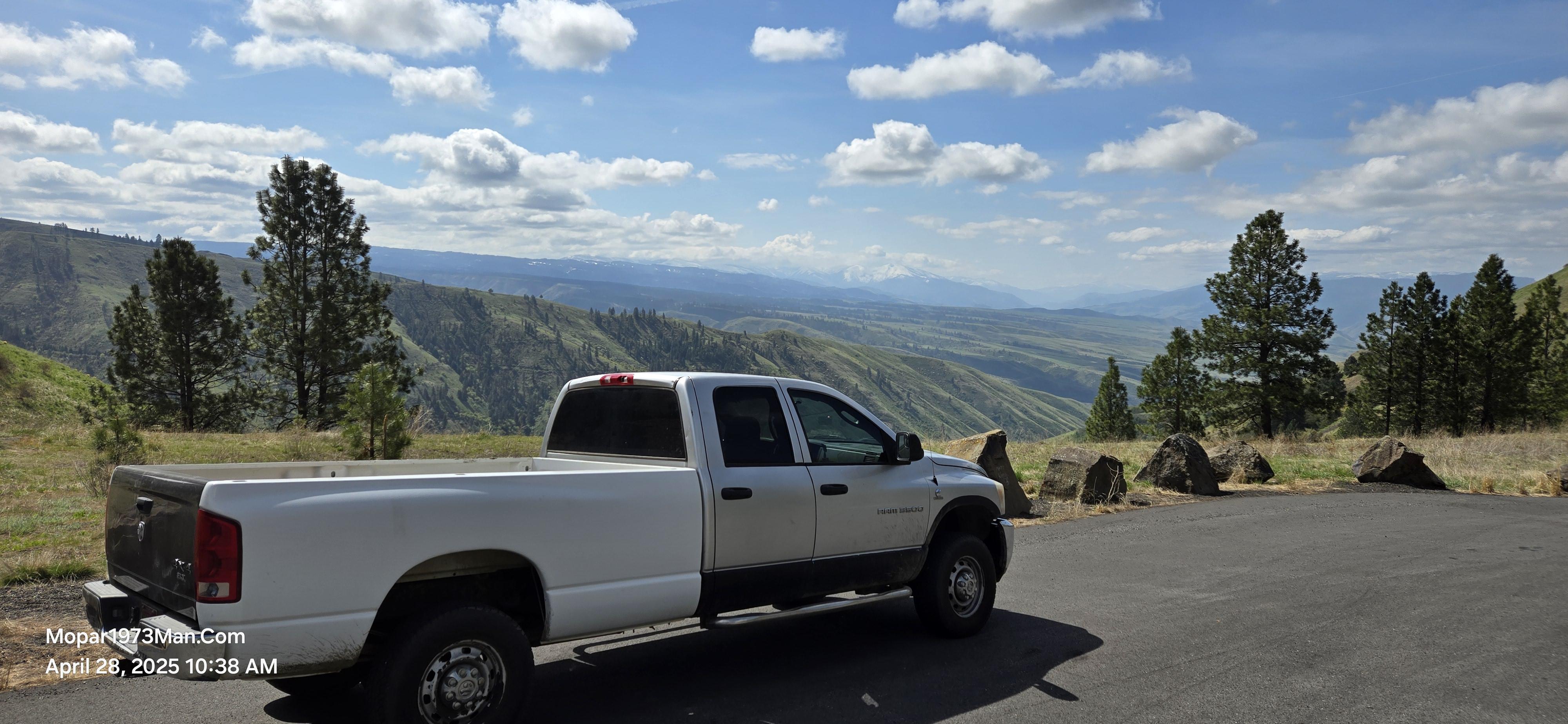
Everything posted by Mopar1973Man
-
20250521_182544.jpg
From the album: Thor
-
20250521_182537.jpg
From the album: Thor
-
20250521_182511.jpg
From the album: Thor
-
20250521_182432.jpg
From the album: Thor
-
20250521_150756.jpg
From the album: Thor
-
20250521_150737.jpg
From the album: Thor
-
20250521_150707.jpg
From the album: Thor
-
2000 Cummins Surge/Dead Pedal
This is one of the few reasons I would typically suggest to have the alternator bench tested for AC ripple at the time of the w-T ground wire mod install. Kind of hard to fix a noise issue if the alternator is still screaming into the charge wire. The ground mod helps with the noise not hoping back on the ground strap to the ECM and VP44.
-
Problem with idle cut off
Basic wire test is to ohm from end to end (unplugged) you should see less than 5 ohms for good wire. Above 5 ohms there is a problem. Another test. Still both ends unplugged then measure connector pin to ground. This should show OL or infinite resistance. This means no wire shorted to ground. If any ohms show then it could have a rubbed jacket or wire damage. Remember both ends need to be unplugged or unhooked.
-
Problem with idle cut off
Remember Bosch stock injectors are NOT made as a set. You could have low end of 293 bar you the high end of 327 bar. This can affect idle performance. I high suggest AGAINST using stock injectors. Buy +50 HP from any good injector shop and they are balanced as a set within 2% of flow rate. Like my custom 7 x 0.010 is popped at 320 bar and custom tuned by the Quadzilla. Remember low pop will advance timing, high pop will retard timing.
-
Problem with idle cut off
Possible tight torque converter in the transmission?
-
Requirements for small compounds
Sadly I've never done twins yet. 7x0.010 injectors can be ran on a stock turbo if you have Quadzilla tuner. Beast is my 30+ MPG truck.
-
Different thickness injector washers?
Good point
-
High idle when hot out
3 CYL 15°F IAT 6 CYL 32°F IAT Remember this is with grid heaters running. Cancels 170°F ECT This is all listed in the tsb by Dodge in the article database
-
Intermitten P1689
Thanks for marking the thread solved. 😊
-
Bad intermittent drive line vibration at highway speed
I'm going to have to say tire-related issues. That is the only material that with change as the tires warms up the rubber softens and the deformity will get worse. I've got to ask what brand of tires, what size of tires, are they on factory rims or aftermarket rims?
-
High idle when hot out
IAT sets the mode. ECT cancels the high idle.
-
Pilothouse/RAM3500 build
It needs paint. OMG! I'm dying to see this custom truck is done. Wow
-
1689 with HVAC
Ouch I would of got a pigtail for it and kept the plug.
-
Cracked bodywork at hood hinge
I would love to do a product review for you. PM going to be sent.
-
Terms Of Use and Policies
@Tweety Bird And I have been busy rewriting the terms of use and policies for the website. This is all new website software, and more features now than in the past. We felt that it was time to review the dated policies and realize we need to totally rebuild everything. Here, shortly, there will be a full database of policies for everything on the website for the usage policy. This is being built in a database so that when other issues develop, we can append to the current policies easily. This will be broke down in a modular design so there will be a policy for each division of the website. Then I've been digging through the site. I'm trying to get everything working right when I've got time at the keyboard. I know the event calendar is currently broken. I need to grab a few days at home and be able to do tag team with the software manufacturer so I can get this resolved. The event module needs to be repaired. I want to post Zoom Meeting schedules. Yup! I'm going to push forward. I'm getting tired of social media and the censoring of speech. Since I have the website, I need to build up a few more features, like face-to-face Zoom meetings to help you fix your trucks. Yeah, I just leaked an idea... 😱😁
-
1689 with HVAC
Did you leave the key on for a long period to wait for the CCD Bus to quit talking?
-
Cookies
CookiesNotice on Use of Cookies and Similar TechnologiesBy continuing to use our website and online services, you consent to using cookies and similar technologies described in this Cookie Notice and our privacy notice. Use of Cookies and Similar TechnologiesOur website and online services use cookies and similar technologies to collect and store certain non-personal data (such as log data, location data, and cookie data) when you visit or interact with our website and online services to help us secure our website and online services, as well as the information processed by our website and online services; monitor and enhance the performance of our website and online services; better understand user behavior; and facilitate and measure the effectiveness of advertisements and website features. These cookies and similar technologies include: CookiesCookies are small text files that are sent to and stored by your browser when you visit or interact with our website and online services. These cookies are then sent back unchanged to the party that served the cookie each time you visit or interact with our website and online services (which includes our ads on third-party sites) for the party that served the cookie to recognize your browser or device. Cookies are either first-party cookies or third-party cookies. "First-party cookies" are sent to your browser by the party that operates the site you are visiting (g., cookies served by Mopar1973Man.Com when you visit our website). "Third-party cookies" are sent to your browser by any party other than the party that operates the site you are visiting (e.g., cookies sent by our online partners, such as Google Analytics, when you visit our website). Further, when we use cookies, we may use "session" cookies (that last until you close your browser) or "persistent" cookies (that last until you or your browser delete them). Some of the cookies we use on our website and online services may be associated with your personal data (such as your email address), and other cookies are not. However, if we associate non-personal data (such as cookie data) with personal data, the combined information will be treated as personal data for as long as it remains combined. Pixel TagsPixel tags (also known as web beacons) are small blocks of code installed on our website and online services which enable our online partners to serve cookies when you visit our website and online services and are generally used in combination with cookies to track activity user on our website and online services, receive relevant log data and cookie data, and perform other activities relating to the monitoring and analysis of the use and performance of our website and online services. Software Development KitsSoftware development kits (also called SDKs) function like third-party cookies and pixel tags, but operate in the mobile app environment where cookies and pixel tags cannot function as effectively. Instead of using cookies and pixel tags, we may install pieces of code (the SDK) provided by our online partners (such as advertising companies, ad networks, and analytics providers) in our mobile apps for these online partners to monitor and analyze the use and performance of our mobile apps and services. Statistical IdentifiersStatistical identifiers refer to identifiers created using certain device information and log data. Collectively, this information makes your browser or device sufficiently distinct for a server or similar system to reasonably determine that it is encountering the same browser or device over time. Statistical identifiers enable us and our partners to uniquely identify your browser or device for the same purposes as cookies. Statistical identifiers may be associated with your personal data (such as your email address). However, if we associate non-personal data with personal data, the combined information will be treated as personal data for as long as it remains combined. How Cookies and Similar Technologies are UsedCookies and similar technologies used on our website and online services (including the information obtained through such use) fall into four categories: EssentialOur website and online services utilize first- and third-party cookies and similar technologies that are necessary to operate our business and maintain our website and online services, including verifying and authenticating website users; preventing fraud and securing our website and online services and databases; payment processing; enabling users to move around our website and online services and use their features; and complying with applicable laws and industry standards. These cookies and similar technologies do not gather information about you that could be used for marketing or tracking your browsing activity. This category of cookies generally cannot be disabled. PerformanceOur website and online services may utilize first- and third-party cookies and similar technologies to provide enhanced features and remember user preferences, including identifying return users when visiting our website (e.g., to remember your login credentials); keeping track of user preferences, interests, and past items viewed or utilized (e.g., preferred language or past purchases); and providing social features that allow users to interact with social media services through our website and online services (e.g., Facebook or Twitter, as further described below). AnalyticsOur website and online services may utilize first- and third-party cookies and similar technologies for analytics, product development, and market research purposes, including analyzing how users arrive at and engage with our website and online services; tracking and measuring the performance and effectiveness of our website and online services; optimizing the location of ads, website features, and other content on our website and online services; statistical reporting in connection with website activity; analyzing user preferences and behaviors and market characteristics and trends in order to develop and improve our products and services, websites, and ads; segmenting audiences to test features of our website and online services; and conducting research about our consumers, products, and online services. AdvertisingOur website and online services may utilize first- and third-party cookies and similar technologies to deliver, track, and measure ads both on and off our website and online services, including ads relevant to your interests (e.g., ads based on your past interaction with our website or based on predictions about your interests derived from your browsing activities on different websites over time); and ads based on your location, demographics, or device characteristics. Cookies are also used for tracking and measuring the reach and frequency of ads and regulating the delivery of such ads (e.g., capping the number of times you see a particular ad). Use of Cookies and Similar Technologies by Our Online PartnersWe may use vendors and other online partners to perform some of the Essential, Performance, Analytics, and Advertising activities described above, including to provide audience measurement and analytics services, to serve ads on our behalf on our website and online services and on third-party sites, and to track and report on the performance of such ads. These online partners may use third-party cookies and similar technologies to collect and store certain log data, location data, cookie data and other information when you visit or interact with our website and online services and other unaffiliated sites in order to identify your browser or device and provide their respective services. Further, these online partners may combine data collected on our website and online services with information collected on unaffiliated sites or with any other data maintained by these online partners. Their use of data collected on our website and online services and third-party sites will be subject to their own terms of use and privacy policies. For example, we may use third-party cookies to deliver our ads on third-party websites through a common form of online advertising known as "retargeting." Retargeting works by serving ads on one website based on an individual's activities on a different website (e.g., if you view a product or service on our website, you may later see ads for our products and services when you visit a third-party website). To do this, we allow our online partners (such as Google or other ad network vendors) to serve their own third-party cookies when users visit our website and online services, allowing these online partners to recognize users who have previously visited our website and online services. When these users visit a third-party website that includes features provided by our online partners (e.g., where our online partners have purchased ad space), our online partners can recognize the users' interest in our products and services and deliver one of our ads on the third-party website. Your Cookie ChoicesMost browsers are set to accept cookies by default. However, browsers typically allow individuals to remove or block browser cookies if they choose. For more information on blocking and removing browser cookies, please review your browser's Settings or Preferences tab. More information can be found here: Google Chrome Internet Explorer Mozilla Firefox Safari (Desktop) Opera Opera Mobile Android Browser Safari (Mobile) For other browsers, please consult the documentation that your browser manufacturer provides. In addition to removing and blocking browser cookies generally, the following opt-out mechanisms may be available if our website and online services utilize the third-party cookies listed below: Google AnalyticsOur website and online services may use Google Analytics, a web analytics service provided by Google. Google Analytics utilizes cookies and similar technologies to collect and analyze information about the performance and use of our website and online services. More information on Google Analytics can be found here. If you would like to opt-out of having your information collected and used as described, please use the Google Analytics opt-out available here. Google Remarketing. Our website and online services may use Google's Remarketing with Google Analytics to allow Google to use information about your visits to our website and online services and other unaffiliated websites to measure advertising effectiveness and serve ads about our products and services that may be of interest to you. As described above, Google places its own cookies when users visit our website and online services which enable Google to recognize users who have previously visited our website and online services when such users visit other unaffiliated sites that also use Google's services and cookies. More information on Google's Remarketing with Google Analytics can be found here. If you would like to opt-out of having your information collected and used as described, please use the Google Analytics opt-out available here. Mobile Apps For cookies and similar technologies used on mobile apps (such as software development kits) for certain targeted advertising activities, please follow the steps below to opt-out of having your information collected and used for such purposes (unless different instructions are provided by your mobile device manufacturer): iOS Users: Launch "Settings" > Tap on "Privacy" and scroll down and tap on "Advertising" > Toggle on "Limit Ad Tracking." You can also reset your Advertising Identifier from here by tapping "Reset Advertising Identifier". Android UsersOpen your app drawer and launch the Google Setting app > Tap "Ads" under Services and enable the "Opt out of interest-based ads" option. You can also reset your advertising ID from here by tapping "Reset advertising ID".
-
1689 with HVAC
Remember the PCM is the creator of the CCD Bus. Can you measure the voltages on the CCD Bus+ and CCD Bus- pins to ground and see if the 2.49 and 2.51 voltages can be seen after the modules all stop talking.
- Vendor Directory