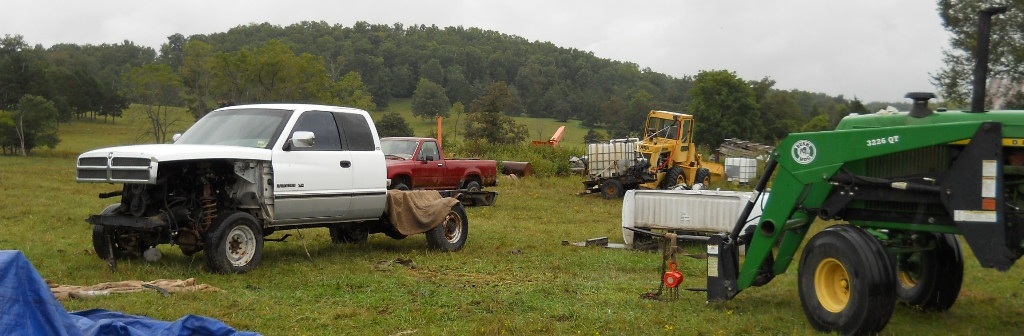
Everything posted by Cowboy
-
Is it worth adding 2-cycle oil to a P7100 truck?
http://www.walmart.com/ip/Super-Tech-TC-W3-Outboard-2-Cycle-Oil-1-Gallon/16795065 Buy 4 gallons get free shipping. I don't like walmart either, I don't think I've been in one for at least a year now.
-
He351ve stand alone Arduino controller code for 2nd Gen Cummins
My trans is the only thing keeping me from throwing more power at it, I am currently pretty impressed with how much my stock clutch is taking... hehe. But even after a clutch, I would still be worried about it. I'm not sure if I want to shell $600 for a clutch, or G56 it. From my experience with an exhaust brake, I don't think pre-loading it would work, it really bogs the turbo down.
-
He351ve stand alone Arduino controller code for 2nd Gen Cummins
It would be different alright... But.... IDK. That's a lot of air. I know a guy that did triple 351VE's, though he controlled them mechanically. It may be something I play with, but it would be a long while down the road. Right now I'm at the point of just wanting it running. lol
-
Is it worth adding 2-cycle oil to a P7100 truck?
I did a quick search for a more recent document, and found this. http://house.mo.gov/content.aspx?info=/bills091/bilsum/intro/sHB1068I.htm It does say that distributors can purchase straight ULSD, but must mix it with bio-diesel themselves.... If I'm reading that right. Next time I get the farm tanks filled, I'll have to ask the guy. From the conversations we've had in the past, he seems well versed in this stuff.
-
Is it worth adding 2-cycle oil to a P7100 truck?
I guess I'll have to look into this more. I have a feeling if I ask my local station, they're just going to look at me sideways.
-
Is it worth adding 2-cycle oil to a P7100 truck?
I'm heavily considering getting a jug for the VP44's, I don't visit Walmart often other wise I would have already. On the P7100's.... It it was plain ulsd then I would be more worried. But according to this, I should be fine. http://www.house.mo.gov/content.aspx?info=/bills071/bills/SB204.htm Couple other links I found interesting. http://web.cals.uidaho.edu/biodiesel/files/2013/08/Applied-21_2_149.pdf http://web.cals.uidaho.edu/biodiesel/files/2013/08/ASABE-036036.pdf One is with a 96 P7100, the other was a 98 VP44.
-
Radiator drain plug fix.
After fixing it, I haven't touched it since. I use a chunk of tubing and siphon it out the top. And yeah, I just grabbed a random O-ring that looked about right.
-
How to Replace a Power Steering Gear Box
How to Replace a Power Steering Gear Box OK first, when removing the pitman arm, don't worry about marking it so you can put it on the same way. It's splined and can only go on 4 ways. First step, remove the pitman arm nut, it's a 32mm if I remember correctly. Then install your puller, make sure to grease it up plenty. I made my own but I'm pretty sure Harbor Freight has one for a decent price. Just make sure to use it within 89 days of buying it! After soaking it for a week in PB blaster, giving it a fresh shot every day. And then fighting that thing for a few hours putting over 2500lb's of pressure trying to get it off, I found a simple trick. I removed the 4 15mm bolts holding the sway bar in place, torqued the puller to 135lb's, and gave it 3 good whacks in this spot with a BFH. Then it came right off. Just be careful not to hit the box, so maybe a BFH's little cousin would be a better choice. Then to remove the steering shaft. If you turn the steering wheel so the top is facing the passengers door, the bolt (13mm) should be fairly easy to get to. After you get that, remove the power steering fluid lines from the box, they are 18mm, If you're anything like me and wait for the box to blow up and loose all it's oil, then you don't have to worry about any oil wanting to leak out! otherwise, just put an oil pan under it and open both lines up and let it drain. I was able to go from the bottom and get the lines off fairly easily. But I've heard of some waiting to take them off til after the mounting bolts, and then just use a jack stand to suport the box until you get them off. Then for the 3 mounting bolts, super simple, don't know what metric size they are, but a 13/16" is nice and snug so I just used it. To ensure no mistakes were made, this was all done under the supervision of a highly trained professional! Also, if you're like me and don't jack up the front end, when you reinstall the box, hook everything up, except the pitman arm, fill it with oil and turn it from lock to lock, top off the oil, lock to lock, top off the oil, lock to lock, and then hook it up, that way you don't have to drag the tires across the ground with manual steering to fill the new box with oil. But I would still take it for a short drive and top it off again once it cools down. If you have any further questions, please feel welcome to ask them on the Mopar1973Man Forum.
-
DIY Hotrod Power Steering Pump
DIY Hotrod Power Steering Pump First off this can all easily be done in the truck, took me about 30 minutes the first time. Unscrew the output line, this will also empty the resivoir, so flushing the system at the same time would be a good idea. Then unscrew the fitting the output line screws into. Here you can see the order of the things coming out, and should go back in. In the picture the pressure relief valve is dissasembled, so it will only be one piece. To mod the pump, drill the hole through the center of the plug out larger, stock is about .125" if I remember correctly. I drilled mine out to .2" and it made a very noticable difference in the ease of steering. There is also a hole out the side, I drilled another .125" hole on the oposite side. And then as the second picture shows, there is a small hole in the side of the fitting, don't plug it when you drill through the hole it leads too. There is also a pressure relief valve inside the pump, I would not recommend monkeying with it as it only comes into effect at full lock, or when you can hear the PS pump working hard to turn the wheels. If you still want to adjust the valve, DO NOT shim it. Stock the plug in the valve isn't totally seated, so you can just take it out, clean it up, and then seat the plug. Seating the plug will increase the max pressure. Increasing the pressure only effects the max steering/braking assist. Increasing the pressure unneeded only raises the chance of carnage. To take apart the valve, here's a handy trick I found, take care not to ruin the machined surfaces! Here's the plug taken apart, notice the shim in the picture, this shim is not stock, and after testing, would render the pressure relief valve useless. There is also a screen in the end of the pressure relief valve, if the screen gets plugged, it can cause weak power steering. Even if you arn't going to mod the pump, cleaning the screen is a good idea if the pump is already drained. And for those curious of the pressure relief valves operation, this is my own personal opinion after staring at it for an hour, could be way off. Crude sketch When the pressure relief valve relieves pressure from beneath the piston, as the fluid goes through the small tube, there is a pressure loss, once the pressure difference between the top and bottom are 9psi, then the plunger gets pushed down and compresses the spring, opening the big bypass port.
-
Oversized Wastegate and Regrinding
Oversized Wastegate and Regrinding When we're trying to get as much out of our turbo as possible, it is very common to port the the wastegate out to help keep drive pressure in check. However, we are limited to how much we can port the wastegate out by the size of the wastegate flapper. The size of the little HX35's flapper could use some serious help, and it wouldn't hurt to give a HE351 a little love as well. So what we're going to do is install a larger flapper, so we can make the hole even bigger, without having to worry about how much sealing surface is left. The stock wastegate port diameter on both HX35 and HE351 are right around 21.75mm (just shy of 7/8). While the stock wastegate flapper is considerably larger on the HE351, where you can take it out to 1” without much issue. The HX35’s flapper is considerably smaller, so 15/16” is the largest I would consider without upgrading the flapper to a larger diameter. Lucky for us, making a new flapper is a simple job, and takes all of 15 minutes. Here is a Stock HX35 wastegate flapper. And here is a Stock HE351CW wastegate flapper. To make a new flapper, I used an old exhaust valve, but this is as great of place as any to get creative. First we’ll need to remove the old wastegate flapper. Just drill out the center of the “rivet” holding the flapper to the wastegate arm. To grind the exhaust valve to the correct size, I installed the valve into a drill press, did the rough grinding with a hand grinder, and then did the finishing touches with a hand file. Here’s our new HX35 wastegate flapper, after I got it to the dimensions I wanted. I then cut the stem off the valve, and installed it to make sure there was a nice fit. On the HX35 I used a ¼” nut and hammered it onto the shaft, to hold the wastegate flapper on. We’ll weld it on in a second, first we need make sure the wastegate has enough “slop” in it to make full contact with the housing, for a positive seal. A little extra slop is a good thing. Here is our wastegate at this point. After making sure everything will work, weld the nut onto the shaft. Make sure no weld gets in the way of being able to put a socket on the nut, this will help for later. Now lets go to the HE351CW, we already made a new flapper for it, and welded it on (for the HE351CW, a 5/16” nut worked best) Now we’re going to “lap” the wastegate, to insure that everything sits together well and there are no leaks. Remember! Leaks mean slower spooling! Even if you don’t upgrade the flapper, I would recommend doing this if the wastegate has ever been ported, as porting can create a lip, and when porting. Even if it was sealing before, you may have removed the sealing surface for the wastegate. For lapping the wastegate, we’re going to use Valve Grinding Compound, last time I got some it was about $6 from Napa, you should be able to get it from most any auto parts store. Then we need to apply it on the flapper, make sure to put more on the flapper then you think you’ll need, as we use the compound, the grit becomes finer and finer, so by reusing the compound that goes to the edges, we can get a progressively finer finish. Now we need to be able to spin the flapper, to grind away at the high spots in the housing. When doing this, I would recommend going in circles instead of back and forth, that way the whole valve gets ground evenly. Also make sure to apply the pressure to the flapper by the wastegate arm, same as it would in the truck, otherwise the pressure won’t be the same when you hook the wastegate actuator up, and can grind away one side of the hole more than the other. Now here is where the nut welded to the top comes in handy! Just take a screw driver, or a drill and spin the flapper. Remember not to get carried away if using a drill, and don’t spin it to fast. Make sure to check the progress repeatedly along the way, make sure that the compound never gets dry, as it will start to scor the surface. Before: After: So there you have it, a wastegate that will seal wonderfully, but can flow enough for you performance needs!
-
Don's Head Porting Extravaganza
Don's Head Porting Extravaganza Special Thanks to Don (Drothgeb) For the Time, Information and Pictures present in this article. Thanks Don! There are different stages of porting, as Don describes below. Stage 1, is removing the collar in the bowls just below the valve seat. It's pretty easy to see the area I'm talking about in the pictures below. Just removing that without removing anything around the valve guide or runners is a huge improvement. It will actually increase low end performance. Just doing that minimal amount of work, helped spooling a touch, dropped my maximum boost more than 10lb, and knocked .3-.4 sec off my quarter mile times. I ran this level of porting for more than a year, and was finally able to get the truck into the 10s with no other head work. As a comment toward cams... Adding a popular cam to this configuration actually cost me more than .2 sec. Like my earlier comment, the cam was costing me more on one end than it could make up for on the other end. Basically, the head was still holding me back. You really need at least this amount of work to take advantage of compound turbos Here's a stock head. As you can see there's a lot of excess material just under the valve seat. Everything inside the red circle is protruding into the air stream, simply removing this on each cylinder achieves what Don refers to as a “Stage 1 Port Job” Stage 2, is a Stage 1, as well as removing the material around the valve guides, smoothing out and enlarging the bowls and swirl ramps, plus some work to the intake runners. This level really increases flow, and as long as you're careful with the bowls and swirl ramps, has very little if any negative effects. Any performance configuration is going to spool better and produce more power. This is also the minimum level that you are going to see much benefit from a cam. Although, that's still a tough call for a moderate hp truck that doesn't see much higher than the mid 3000 rpm range. Here you can see a Stage 2 Port Job. You can compare this to the stock picture above. And the material required to take off. Stage 3, is when you modify the head to gain access to the intake runners through milling off the intake plenum or the npt plug trick (shown below). This level still spools and drives well and works with stock or moderate cams. I have this configuration on my street truck and see 10psi of boost at 1700-1800rpm. To me that's not bad for a 66/91 combo. Here's a couple of slices through the intake. They are not in exactly the same location, but it gives you a good idea of the metal that needs to be removed. Here's a good view of the intake after porting. Again, this still needs to be hit with a sanding wheel to smooth it out. Now the stock exhaust runner is pretty open, so it just needs some cleaning up. But the stock intake runner is pretty tight. Looking through the plenum here, you can see what I mean. Before: Here's after a little work (still needs some more though) Here's a side by side before and after exhaust port. This head actually had a "stage 1 porting" from a couple of years ago, so a stock head is even tighter than the before one here. Above this is competition level. More extensive runner work, larger valves, swirl ramps are removed. The Hamilton Head starts at this level. At this level low end performance definitely takes a hit. Not going to spool well below 2000rpm, but it will flow on the top end. At this level you definitely need a performance cam to run in the rpm range that suits the head. Not suited to small turbo(s) either, needs air to make it work. NPT Plug Trick Now some of you are thinking that's great on the 4 runners you can reach. But what about the 2 on the ends. Well, I drill 2 holes in the top of the plenum that let you reach where you need to get to. I then tap the head for a 3/4"npt plug to seal the openings. You just need to get one of these carbide bits with a 6" shank. With one of those I can reach every surface in the intake runner without milling it off. And once a couple of the humps and bumps are cleaned out of the stock plenum, I think it works as good or better than the runner type intakes. Well, that's the basics. Just remember, a lot of the runner walls are only a little over a 1/4" thick, so don't get carried away without knowing what's behind it. I've got this old head that I sliced up and, I drilled a bunch of holes in the slices too. It's pretty handy to have around for reference.
-
Boost Controller Designs
Boost Controller Designs For simplicity's sake, we'll say the wastegate opens at 20 psi and regulates the boost pressure to 20 psi. The way any mechanical boost controller works is fool the wastegate into thinking you are are making less boost then you actually are. So if you want to build 40psi, you need to make the wastegate think that you are only building 20psi at your set pressure, so in this case, you want it to think the boost is half of what it actually is. There are a couple designs. The Needle Valve This is simple and cheap, and works OK for people that use there trucks for fun. How it works is it delays the pressure going to the wastegate, so when you floor it, the boost has time to build up to your set pressure before the wastegate realizes it. The problem is when you're towing, or at/above 20psi for extended periods, the wastegate will get the full boost pressure you are making and will open way up to try and get boost back down. And because of the restriction, when you let of the skinny pedal to shift (with a manual) and you boost goes down, the wastegate will take a while to close again, making it harder to re-spool the turbo once you're done shifting. Boost Elbow The boost elbow is basically like a needle valve, but it has a small orifice after the needle valve that bleeds pressure to the atmosphere, if anyone here is familiar with a "resistor devider" (electronic circuit) it works in exactly the same way. By bleeding pressure after the valve you lower the pressure that the wastegate sees, making it so it will always see lower pressure then what you're actually making. Using the valve, you can change the amount of pressure drop. This is a step above the plain needle valve, and works very well for many, however there is still one issue. In order to wastegate the boost to 20 psi, the wastegate has to start to open around 10 psi. So if you set your pressure to 40 psi with the boost elbow, then it will start to open around 20 psi. And because of the orifice, you will always have a small boost leak, nothing huge, but it is there. Ball & Spring Boost Controller Learn how to make one HERE. This is another step above the boost elbow. The Spring pushes the ball into a seat, sealing off the passage to the wastegate. The spring is on one side of the ball, and on the other side, there is the boost from the engine pushing the ball open. Once the boost pressure is enough to overcome the pressure given from the spring, the ball unseats and lets air into the waste gate opening it. On paper it looks like it will keep the wastegate closed until you your set pressure, however that's not quite the case. Because once some air pressure goes around the ball, it is now applying pressure trying to close the ball again. So in reality this design makes the wastegate think your at X less pressure then you actually are. So if you have it open at 40 psi, it will think you are at 20, and at 30 psi, it will think you are at 10. This design works very well, and should be good for all but the biggest perfectionists out there. The only real downside to this design is it still has a pressure spread between starting to open, and open enough to regulate the boost to that pressure. Boost Governor This design's only advantage over the "Ball & Spring" design is that it fixes the "problem" of the pressure difference between starting to open, and open enough to regulate the boost. This controller works by doing it's best to keep the pressure exactly where it's set to, so fully closed @ 38 psi, and fully open by 42 psi. There are some "over shooting" issues with ones I've played with though, due to the issue that the wastegate has only the time it takes to build ~2 psi to go from fully closed to open enough to regulate the pressure. This is a much rarer design that only a few I know of have, this works extremely well for those who use there truck for towing, as they never really "punch" the throttle, giving the wastegate plenty of time to open. Note: "Boost Governor" is a name I came up with, as I'm not sure what this type is actually called.
-
KDP (Killer Dowel Pin)
Killer Dowel Pin Big Thanks to Illflem for some of the information precent in this article Dowel Pin Repair Kit for 94-98 If you have heard of “dowel pin issues” on the 12 valve Cummins 5.9 with the P7100 Bosch injection pump then you may already have taken care of your truck. This dowel pin issue applies to all ’89-’98 12 valve Rams with Cummins engines and many other non-Dodge Cummins 12 valve engines. If you have not heard of the issue, or you heard yet have done nothing and you are the owner of one of these vehicles, listen up. A dowel pin failure could destroy your engine completely or do no damage at all. The aluminum front gear housing on the 5.9 Cummins is precisely located on the front of the cast iron engine block using dowel pins. The dowel pin is about 3/8 inch diameter by 3/4inch length made of steel. During engine assembly the dowel pins are driven into holes drilled in the block such that about half their length protrudes. Matching holes in the gear housing permit a precise fit of the housing the block. Several cap screws are used to hold the housing to the block. The problem with the dowel pin occurs because the hole in the aluminum gear housing was drilled through. During engine operation vibration could cause the dowel pin to work its way out of the hole and fall into the gear case. When the dowel pin falls, it can drop right to the oil pan or land in the gear housing, causing no damage at all. On the other hand, the pin can be caught in the camshaft gear and forced into the aluminum gear housing, breaking out a big chunk of the housing which would cause a huge oil leak and an expensive, time consuming failure. Worst-case failure is when the dowel pin goes between the cam and crank gears, or cam and injection pump gears, breaking the gear off the camshaft. The camshaft stops rotating instantly causing valves to stop operating, leaving some valves open and some closed. The crankshaft continues to rotate for a few seconds, slamming pistons into valves, and possibly ruining block, crank, rods, cylinder head, and valve train. Almost no reusable parts in this case, a complete engine swap could be required. If you are the owner of one of these 12 valve 5.9 engines and you haven’t taken preventive action, we suggest you take action before the vehicle strands you in a bad location and sticks you with an expensive repair bill. TST offers a “Dowel Pin Kit” that includes the parts you need to access the dowel pin, positively lock it in place so that it does not come out. Installing this kit requires removal of the engine fan shroud, fan, damper, and front gear cover to gain access to the dowel pin. Once the dowel pin is secured, a new crankshaft seal included in the kit is installed in the gear cover and all parts are reinstalled. This kit sells for $65 and takes about 4 hours to install. See http://www.tstproducts.com/DowelPina.pdf for complete installation instructions. Cummins also has all the parts you need: Blocking tab # CM3958017 (Or Make your own) Front seal # CM3804899 Timing cover gasket # CM3918673 Stock KDP Tabbed KDP. Finding something to make the tab out of is a good place to get creative. strength isn't a big deal, you can even use a pop can. Typical KDP caused case crack and pin with cover removed View from the top, fan bearing housing almost always needs to be removed to see More severe but common damage Even more severe, cracked gear Side view of cracked gear If you have any further questions, please feel welcome to ask them on the Mopar1973Man Forum.
-
12V Engine Specs
12 Valve Engine Specs Horse Power (SAE net) 215 bhp @ 2600 RPM - 1996-98 49 State Manual Transmissions 180 bhp @ 2500 RPM - 1996-98 All Auto Transmissions 180 bhp @ 2500 RPM - 1996-98 CA Manual Transmissions 175 bhp @ 2500 RPM - 1994-95 Manual Transmissions 160 bhp @ 2500 RPM - 1994-95 Auto Transmissions Torque (SAE net) 440 lb-ft @ 1600 RPM - 1996-98 49 State Manual Transmissions 420 lb-ft @ 1500 RPM - 1996-98 All Auto Transmissions 420 lb-ft @ 1500 RPM - 1996-98 CA Manual Transmissions 420 lb-ft @ 1500 RPM - 1994-95 Manual Transmissions 400 lb-ft @ 1500 RPM - 1994-95 Auto Transmissions Engine: 5.9-Liter, OHV, Diesel Six-Cylinder Type & Description: Six cylinder, in line, liquid cooled, turbocharged, intercooled Displacement: 359 cu. in. (5.9 L) Bore x Stroke: 4.02 x 4.72 (102.1 x 119.9) Construction: Cast iron block & head Compression 17.5:1 Oil Flow Rate: 20 GPM Coolant Capacity: 24 qt. (22.7 L) Emission Controls: Engine modifications, oxidation catalyst (after 1/1/94) Oil Capacity: 1994: 10 qt. (9.5 L) with filter 11 quarts using Cummins p/n 3928740 or Dodge p/n 4796874 dipstick 11 qts by marking the dipstick 1 3/16" above the "ADD" mark 1995-98: 11 qt. (10.4 L) with filter Valve System: OHV, 12 valves, solid sliding tappet lifter/followers Valve Adjustment (engine cold) Intake = 0.010" Exhaust = 0.020" Adjustment interval - 24,000 miles Fuel System: Fuel Injection: P7100 High-pressure direct injection, mechanical Fuel Pressure: 18-24 psi at idle, 28-36 at 2000 rpm with no load. Max Pressure across Filter: 5 psi Max fuel return line restriction: 20.4" Hg Max Inlet Restriction 4" Hg Fuel Requirement: Diesel #1 or #2 Alternator: 94-95 - 120 Amp 96-98 - 136 Amp Battery: Maintenance-free, dual 750 CCA Valve Specs seat angle:(degree) = 30 face angle:(degree) = 45 spring test pressure:(lbs.@in.) = 81@1.64 spring installed height:(in.) = 2.36 stem-to-guide clearance:(in) intake = 0.002 exhaust = 0.006 stem diameter:(in.) intake = 0.313 - 0.314 exhaust = 0.313 - 0.314 Turbocharger specifications: TurboCharger Model: 1994 - Holset WH1C, 12 sq sm Turbine Housing, 8 Blade Compressor Wheel. 1995-1998 - Holset HX35W 12 sq cm Turbine Housing, 8 Blade Compressor Wheel. Turbo Boost Rating (Engine in stock form) 1994-95: 15-18 psi 1996-98 Auto: 15-18 psi 1996-98 Manual: 21-23 psi Max Exhaust Gas Temperature (EGT): Temperature Probe in Manifold: 1250 Degrees F Temperature Probe post Turbo: 950 Degrees F If you have any further questions, please feel welcome to ask them on the Mopar1973Man Forum.
-
Leaky Dodge Radiator Drain Plug Fix
How to fix a leaking Cummins radiator drain plug. This is a super simple fix. Anyone with some needle nose pliers and a flat screwdriver can do it! First thing you need to do is locate it, which, if you found this article, you likely have already done. If not, it's on the bottom, drivers side of the radiator. Now you'll want to drain the radiator of all the coolant, If your fancy automatic drain valve didn't already. You can drain it into a couple jugs so you can reuse it (prepare for up to 5 gallons). I would suggest getting used to using a syphon hose out of the fill cap. The plastic drain valves are a joke. OK Now that you're ready to take it apart. Take your needle nose pliers and open the drain valve just shy of 180*. fully open is about 225*. Now wiggle it about and pull it straight out, you may need to use your screwdriver to help pry it out a little while you wiggle. OK, now it's out! you'll see an O-Ring, it is likely nicked or cut. Now you got a few options, you can buy a hole new valve (NAPA P#605-1372, AutoZone P#61134 ). Or you can just pull an O-ring out of a kit that looks about right and hope it doesn't leak... you can guess which I did! Fingers crossed! Like with any O-Ring, it's a good idea to put a little lube on to help it go in. I use petroleum jelly, but I'm sure soap would work aswell. Not to sound like a haynes repair manual, but installation really is just opposite as removal. Just make sure the "handle" on the plug is facing straight up and down. Then press into place, refill the radiator, and you're good to go! One leak free radiator drain valve coming right up! If you have any further questions, please feel welcome to ask them on the Mopar1973Man Forum.
-
How to Adjust your Idle RPM
How to Adjust your Idle RPM Big thanks to: Illflem, and Rumbus528 on youtube. Adjusting the idle speed on the diesel engine is not difficult. The adjustment is located on the driver side of the injector pump near the rear of the pump. You will need a 10 mm wrench. Correct speed is: 1994-1998 with AT - in drive with AC on 750 -800 RPM 1994-1998 with manual in neutral with AC on 750-800 RPM NOTE: These speeds may cause stalling when the engine is cold. If this is a problem for you, bump the idle speed to 900 RPM. See TSB 18-07-98, which warns that the dash tachometer is not accurate enough for proper adjustment. If you have adjusted the idle using the tachometer and have any of the problems listed in the TSB, you may use your tachometer to get the idle speed in the ballpark and then use your judgment to fine tune the idle adjustment. Idle Speed Adjustment There are several ways to reach the idle adjustment. Go in from the front of the truck - Lay over on the radiator and snake the right arm back and down to the adjustment. From a short stepladder beside the driver side tire - Reach down from behind the injector pump to the adjustment. Stand on 5-gallon bucket by the drivers wheel, lean in under the hood and put the back of your head against the hood insulation - reach your right hand under the brake master AND under the ABS lines to the back of the pump. From any of the positions above, you can easily feel a vertical bolt with the extra threads on the bottom. The locknut is on the bolt threads below the boss on the pump housing. An open end wrench will usually loosen the locknut, it is difficult to get a box end wrench to fit onto the locknut. Loosen the 10 mm Locknut on the low idle adjusting screw at the rear of the injector pump. Take the left hand and gently push the linkage rearward to take the pressure off and with the right hand. Look at the RPM and repeat to get the results you're after. turn the idle screw counter clockwise (up) to increase idle speed turn the idle screw clockwise (down) to decrease idle speed Tighten the 10 mm locknut when the idle speed is correct. Another version from Jeff Hammaker: Question> How do I adjust the idle speed on my Ram diesel? The idle speed seems too high. First, trace the accelerator linkage to the connection on the fuel pump. With the ENGINE OFF have someone floor the accelerator and watch the fuel arm move. The best position I can describe is that it is under and to the left of the fuel filter on the rear of the fuel pump. A Flashlight and a mechanics telescoping inspection mirror would best serve as your visual aids as there is little room to move around and get a view of this area. Once you have located the fuel arm the idle adjustment bolt is where the fuel arm normally rests on. It is easier to see and adjust if you have someone hold the accelerator down. The 10mm bolt that the fuel arm rests on threads into the bracket that you see and has a 10mm lock nut on the underside of the bolt. Loosen the lock nut and adjust the bolt on top in for a lower idle speed and out to raise the idle. I have found that the truck works well with the idle set at 750 rpms and this is the first white line below the 1000 rpm mark on the tach. Start the engine and observe the idle speed and put the truck in gear (if automatic) and turn the AC on. If the truck doesn't try to stall then you are set. Make sure that you tighten the locknut good when you get your desired idle speed. An observation I have made. With the idle speed set below the factory set point it is easier to start the truck when you gently put some slight pressure on the accelerator while cranking the engine. Applying to much pedal will generate a a real smoke cloud so its an experimental thing that you need adjust by feel until you get it just right. Any confusion let me know. Video; If you have any further questions, please feel welcome to ask them on the Mopar1973Man Forum!
-
From 24 valve to 12 valve
Glad you like my avatar! Here's a couple links I've got saved. http://www.cumminsforum.com/forum/94-98-non-powertrain/23378-fuel-gauge-stuck-full.html http://www.cumminsforum.com/forum/98-5-02-non-powertrain/387473-fuel-sending-unit-repair-under-1-a.html
-
Straightening out wiring harness.
The Fuel Heater and FSS both get 16ga fusible links. I don't know what the grids get. The starter I'm not sure about, if it does, it's under the insulation. I'm with Nick on this one.
-
He351ve stand alone Arduino controller code for 2nd Gen Cummins
Very Impressive! Does the HE351VE have a 60 or 62mm compressor wheel?
-
He351ve stand alone Arduino controller code for 2nd Gen Cummins
Looking good! What's the delay between data logs? And what's your drive pressure at when you're at 3000 RPM? My HX35 hates me to no end. But we've both got similar turbine wheels.
-
Injector Disassembly, Cleaning & Inspection
Injector Disassembly, Cleaning & Inspection Cleanliness is very important, any dirt or debris that get inside the injector will wear on the tight tolerance parts. Injector Diagram: Torque Specs 15mm Nozzle Retaining Nut - 22 ftlb's 10mm Injector Bleed-off bolt - 6 ftlb's 24mm Injector Retaining Nut - 44 ftlb's Things we'll need. 19MM Open end wrench (For Pop Tester). 15MM Open end/box end wrench (For Injector Disassembly and Pop Tester). Torque Wrench with 15mm Deep Socket. Vice, Preferably Smooth Jaw. Lubrication Oil (I use 50% Diesel, 50% engine oil). Pen Magnet for Shim Removal. Small pick (I like a 5/64 hex key, it fits tight into the shim for easy removal). Adjustment Shims (For Adjusting Pop Pressure). Caliper (For measuring Shim packs for easier pressure adjustment). Pop Tester (For checking Pop Pressure) Fluid for Pop Tester (I use 95% Diesel, 5% 2-Stroke Oil) Clean the injectors thoroughly before disassembly. I Highly recommend you only work on one injector at a time to prevent mixing parts between them. Clamp Injector in the Vice. Do not Clamp onto the Injector Return Outlet Port. Use 15MM Wrench to loosen Nozzle Clamping Nut until Hand Tight. Remove the injector from the vise, put the injector close to your work bench before finish removal of the Nozzle Retaining Nut. This will prevent small parts from falling and disappearing. Disassemble the injector further, note the orientation of everything, it should come apart like this. Clean All Parts Thoroughly. Use Brake Cleaner/Carb Cleaner and Compressed Air to blow backwards through the Feed Passage in the Injector Body to clean the Edge Filter. Carefully remove the Needle from the Nozzle, if necessary use some pliers and carefully pull the needle out, make sure not to scratch the nozzle mating surface. If the needle still won't come out (very unlikely for a used nozzle in good shape) then reassemble the injector and install it into the injector Pop tester and use it to pop the needle loose. And then once again disassemble the injector and continue cleaning. Use Brake Cleaner/Carb Cleaner and Compressed air to clean out the nozzle, blowing into the needle hole, and the feed passage. Inspect the injector needle for wear or pitting at the tip. Here is a video showing a good and bad needle. If the injector needle is damaged, both it and the nozzle must be replaced. If this is the case, it is highly recommended that you replace the whole set. Once clean, use your lubricating oil and put a couple drops on the injector needle before inserting it into the nozzle. Make sure to lube both the needle tip, and the largest diameter portion of the needle. Well used nozzles aren't picky about the type of oil, you could even get away with straight engine oil. However new nozzle have much tighter clearances so are very picky about oil thickness, Use a maximum of 50% oil and 50% diesel. To thick will warrant inaccurate readings with the Pop Tester. If the injector isn't working correctly on the Pop Tester, Disassemble the injector, clean the nozzle thoroughly, and make sure you're using a thin enough lubricating oil. Once done, insert the Needle back into the Nozzle. Back to the injector body. Install all the shims back into the hole, if you are installing extra shims to raise the Pop Pressure, install them under the main thick shim. As a general rule, .01mm of shim will raise the pop pressure 1.5-2 Bar. Once the shims are in place, insert the spring, if the spring does not sit approximately flush with the injector body, the shims are not seated correctly. Carefully use the spring as a ram-rod to seat the springs. Here is the shims and spring inserted correctly. Then install the spring seat, note the orientation. Now install the Valve Stop Plate. Once again, note the orientation, the conical side should face the injector body. When installing, make sure to line up the Feed passages. Once installed Dribble a little Lubricating Oil onto the Valve Stop Plate, This will lube many key things, most importantly the injector body threads. Also dribble some oil into the Injector Nozzle Nut, this will again lube the threads, as well as where it seats against the nozzle. Once done, install the nozzle, again make sure to line up the Feed Passage. Install the nozzle, then the nut. Tighten the nut until you start to feel spring tension, then back it off a turn or two. Grab the nozzle tip with your fingers and pull up and down on it, there should be play, if not, loosen the Nozzle retaining nut further until there is some play. Then try and spin the nozzle tip, while pulling in and out. The nozzle should not spin. If it does then you do not have the aligning dowels in incorrectly. Disassemble and re-check your work. if the nozzle does not spin, everything is good to go and you can tighten the Nozzle retaining nut down to 22 ftlb's. If you are changing the pop pressure, or installing new nozzles, it is highly recommended that you Pop test the injectors once down. This will let you know if you should shim the injectors, or if some nozzles aren't spraying correctly. I highly recommend you do your pop testing outdoors, or in a very well ventilated area (Due to the fact that it was raining, I had to take these pictures indoors). Good spray pattern: 5x.010 VCO @ 280 Bar 7x.0105 SAC @ 320 Bar 7x.0105 SAC @ 260 Bar 5x.013 SAC @ 260 Bar 7x.0105 SAC With Bad Spray pattern, it may look like it's just injecting less fuel, but it's actually the same amount.
-
He351ve stand alone Arduino controller code for 2nd Gen Cummins
If you made graphs that look like mine, you should be ashamed of yourself. Either way, can't wait to see them!
-
Finding & Fixing your Air Leak
Finding & Fixing your air leak. So you found out that you have an air leak somewhere. In this article we’ll find it. In addition to this article, this is also a good read. Joe G's Fuel System Write-up The air leak can be anywhere from inside the fuel tank, to the lift pump. Finding the Air Leak If the leak is large enough, it may drip when the engine is not running. If you are not that lucky, you may have to persuade it to drip by taking an air compressor and pressurizing the fuel tank to 10 psi MAX. to pressurize the tank, take an air nozzle, wrap a rag around it, and insert the contraption into the tank fill-up spout. Now just watch for leaks! If no leaks are found, the issue may be in the fuel tank. Also, if the lift pump primer is leaking fuel, it will likely leak a little air as well. Fuel Module The fuel lines in the fuel module in the fuel tank can wear holes and suck air. The Fix: You will need to replace the lines in the tank, LarryB’s has a good kit. Or you can install a Draw Straw or Sump. Fuel Quick Connects at the tank. They are called “quick connects”, but really they are the least quick connect fittings imaginable, especially at the odd angles you will be forced to be in in order to even see it. The quick connect has an O-ring it in that can have a flat spot in them. The Fix: Replaced the quick-connect (3/8” Feed, 5/16” Return), or as many owners have done, replaced the rubber hose (3/8” Feed , 5/16” Return) that the quick connect is on, and just slide the hose over the male portion of the quick connect on the fuel module. This method has been used many times, and I have yet to hear of any failures. Fuel Lines along the Frame If your truck is somewhat of a rust bucket, the fuel lines are going to be one of the first things to go. The Fix: You will need to replace the lines, there is a large array of replacment options, including stainless steel lines, and the more popular and DIY friendly, Rubber hose option. If you use rubber hose, make sure it is Diesel Rated. Marine Grade would be recommended. Trident A-15 Marine Fuel Line is good stuff, at an affordable price. LarryB’s also has good kit. When re-doing the fuel system, if you bypass the pre-screen (I wouldn’t), make sure to use some form of screen before the lift pump. Avoid too much restriction as the lift pump doesn’t like having to pull through to fine of a filter. Fitting sizes are as follows: Lift pump inlet – ½” BSPT (NPT work fine), Pre-filter inlet/outlet – 3/8” NPT. Fuel Heater/Pre-screen unit The fuel heater is well known for its likability. The rest of the prescreen unit is very reliable. The Fix: Delete the pre-heater. Pre-Filter to Lift Pump Hose. It is common for this hose to leak air, it may look good on the outside, but the connections can leak air. The Fix: The cheapest place to get a new ones, surprisingly, is the Dodge dealer, Cummins Dealer is much more expensive. Or you can get one from here http://www.genosgarage.com/product/mop-04746638/hoses Lift Pump The Inlet Fitting may leak, along with the primer seal. The Fix: If the issue is the primer seal, some of the old pumps has a normal O-ring that sealed it off. If your is like that you can try replacing the O-ring. Otherwise if your pump in not like that, then you need to replace the Lift Pump. http://www.genosgarage.com/product/pump-4988747-kit/fuel-pumps
-
Engine Not Starting
94-98 12 Valve Cummins not Starting. In this article we’ll troubleshoot the mighty Cummins not wanting to breathe life. I’m going to assume that the engine is cranking over like it should, but isn’t firing. If you are having issues with the engine not cranking over, please wait patiently for me to write a “Starting System Diagnostics” article, Thank you. Things to check: FSS (Fuel Shutoff Solenoid). Symtoms: Engine Cranks with no hint of wanting to start, or starts but shuts off once you let go of the key The FSS is an electrical solenoid that lifts a lever on the injector pump. The injector pump will not inject fuel into the engine if the FSS lever is not in the raised position. For more information, Go to: Fuel Shutoff Selenoid (FSS) No Fuel to injector Pump Symtoms: Engine just cranks, possibility of white smoke out exhaust pipe. Common issue if the engine ran out of fuel, has sat a while, or a part in the fuel system has been removed/replaced. For troubleshooting and system bleeding procedures, Go to: Bleeding the Fuel System Slipped Injection Timing Symtoms: Engine just cranks, white smoke out exhaust pipe. Likely issue if Injector pump was just re-timed. To set the timing back to stock, go here: Confirming Stock Timing & Checking And Setting your Timing Back to Stock
-
Curious what others think of installing a blocking diode to prevent AC Noise
You may want to double check your understanding about them.