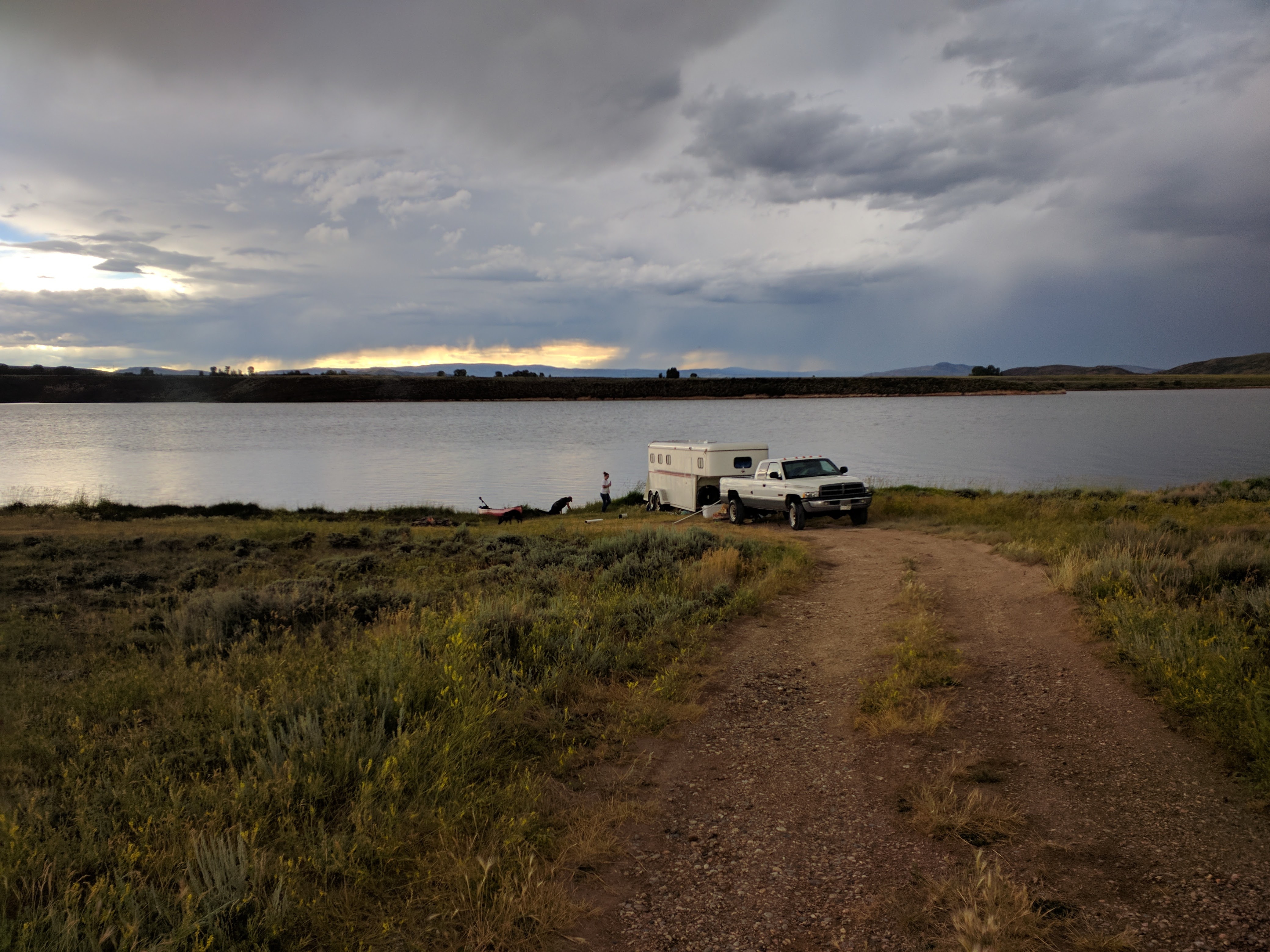
Everything posted by Me78569
-
No high pressure at vp when cold unless hotwired
Ecm on the block controls fueling
-
No high pressure at vp when cold unless hotwired
haha I have done that before to recover a file needed for a client off of a failing harddisk.
-
4x4 light not operating
exactly what I am thinking. Verify the switch is working first then figure out why you aren't getting full throw in your vacuum actuator.
-
4x4 light not operating
Yea have someone sit in the cab and watch the light on the dash then you climb under and remove the switch from the actuator and cycle it with your finger and see if the light comes on.
-
VP44 Troubleshooting
1. No 2. not sure what your question is 3. I supposed you could , but I REALLY doubt you will find the solenoid 4. Typical failues at timing piston failures Does the truck smoke white when it stumbles? White smoke typically means a timing piston failure, but you would almost always see a po216 code. Does the p0122 code still show? Have you cleared codes and driven it? Does the code come back? Why don't you think it is the apps? Dead pedal + a Apps code makes me really think the apps is dead.
-
4x4 light not operating
Pull out the switch on the front axle. Have someone sit in the cab, then manually push the switch in and out and verify that it is showing on the dash. I would guess that your vacuum actuator is getting weak or the shaft is bent, preventing full movement of the fork.
-
No high pressure at vp when cold unless hotwired
I would assume it is cheaper to have them fix it. all edge boxes that wiretap have the same programming so the screen is the only difference.
-
No high pressure at vp when cold unless hotwired
That is up to you. If you don't want to spend the money and like how the truck drives without it, then I would say you not get it fixed, if you miss the power and have the money then I would say you fix it.
-
No high pressure at vp when cold unless hotwired
Very interesting. I would remove the edge %100 and drive it around a bit and see if it is fixed.
-
Aux input 2nd Gen Dodge Ram Radio DIY p04704383ah
A few weeks ago I ordered some 3.5mm headphone jacks to try and wire up an AUX input into my radio. I did see a write-up on here for the Infinity system, but not the cd/cassette Chrysler radio with the number p04704383ah on the top cover. Finally got the parts in today to start in on this. Spent a bit of time looking and didn't find anything in regards to this radio. This image has been resized. Click this bar to view the full image. Report this image You will need - Radio - Headphone jack with internal Switch - Soldering iron - Heat Shrink - 5 pieces of wire (3x6") (2x3") - Phillips Screw Driver - Multimeter - SuperGlue - Needle Nose - Small Flat head screw driver The headphone jacks I ordered have a left / Right / Ground / and a 2 pole single throw switch. This allows for you to route a signal, such as the radio, though the head phone jack when not in use and disable the signal coming for the radio when you put the headphone jack in. HERE is the jack I used. or searching on EBAY for "3.5 headphone jack switch". I am sure Radioshack has something similar, but I didn't have a chance to look. You will be responsible for understanding how the jack you ended up with works. Since different jacks will have different prongs etc I cannot tell you which prongs go where. Use a multimeter to determine what prongs do what when there is nothing plugged in and when there is something plugged in. The jack I bought has a clear cover which made it easy to see how it worked. This image has been resized. Click this bar to view the full image. Report this image I ended up using a larger wire and heat shrink but you get the idea behind the wiring. First you need to disassemble the radio. Ensure to take note of how things go together because you will have to put it back together. If you are unsure about something take a picture of it. This DIY isn't meant to be a ste by step guide to disassemble the radio. There are two screws holding the top cover on towards the top back left and right of the radio. Once those are removing you can pull off the cover. Next you need to remove the cd player. Do this by removing the phillips head screws holding the cd player in place. They are located towards the front of the unit on the left and right hand side on top. You can pull the cd player section straight up, take care to disconnect the ribbon cable under the cd player. Picture shows the approx location of the screws holding in the CD player This image has been resized. Click this bar to view the full image. Report this image Next remove the faceplate of the radio. There are 2 screws on both the left and right hand side of the radio holding the plastic faceplate on. You will need to remove the volume knob and equalizer slider knobs. There are also 4 clips hold the bottom and top of the faceplate to the rest of the radio. Gently pop them loose. This image has been resized. Click this bar to view the full image. Report this image You will end up with this. This image has been resized. Click this bar to view the full image. Report this image the middle board is the next to come out. It is what you will be altering to make the AUX input work. There are 4 bent metal fingers holding this board into place. They are locked in place with solder so you will need to use the soldering gun to melt the solder and bend the metal fingers straight. Take care to not pull it too hard. There are 5 different connections on this board that you need to pop loose to remove the board and one ribbon cable that connects to the tape deck. The red dots on the above picture around the edge of board #3 are the bent metal Fingers you need to straighten. You will also need to remove/bend out slightly the tuner module from the passenger side of the radio. It connects to the board you need to remove, but can't unless the tuner is swung out of the way. The Front case section and board will come out as one piece This image has been resized. Click this bar to view the full image. Report this image This image has been resized. Click this bar to view the full image. Report this image The main connections you will be working with are the Tuner input and the Amp input Once you get this board out use a small flat head to scratch off a section on the two circuits shown. You will need to ensure that there is no continuity between the amp input and tuner input connectors. Using the wire you will effectively put the headphone jack in place of that circuit. You can find the circuit in the back right hand side of the board, You can see brown marks from a sharpie in the above images. Don't scratch the ground circuit between the one you did scratch. This image has been resized. Click this bar to view the full image. Report this image Next you will need to solder in the two short sections of the wires from your supplies to the Radio Tuner board input. The connector is located on the front of the radio to the right hand side if the radioface is pointed towards you. This image has been resized. Click this bar to view the full image. Report this image Here are the pins you want to connect your wires to. First is the Tuner input section on the front of the Radio. This image has been resized. Click this bar to view the full image. Report this image These short sections of the wire go to the switch poles on the headphone jack. Left and Right don't really matter as the amp controls which signals go to what speakers. At this point if you have a quality radioshack soldering iron you will need to sand off the grime This image has been resized. Click this bar to view the full image. Report this image Next you need to connect the input prongs of the headphone jack and ground to the Amp input connector. to do this flip over the above board and solder on the L/R/G from the headphone jack. These prongs on the jack will be the ones that make direct connection to the actual jack. This image has been resized. Click this bar to view the full image. Report this image Once the poles in the headphone jack and the input for the headphone jack are wires onto the board test the amp input and tuner input for continuity between the two on both the right and left channels. There shouldn't be any continuity when something is plugged into the headphone jack. When the headphone jack is empty however there should be continuity, effectively passing the tuner signal through the headphone jack and into the amp. Once you verify that the jack is working as it should then you can move on. Next reinstall the board into the Radio case. Take care to line up all the connectors. This takes a little time, but isn't too tough. Rebend the metal fingers holding the board down. once the board is back in place route the jack and wires through the hole in the case for the tape deck. This image has been resized. Click this bar to view the full image. Report this image Once that is done you just have to drill a hole into the faceplate of the radio and mount your headphone jack. I chose to mount it in the tape deck flap since I don't think I own a tape anymore. If you choose this method you will need to superglue the tape deckflap closed. From my looking I couldn't find a location that my jack would actually fit, you might find a better place. This image has been resized. Click this bar to view the full image. Report this image Run the wires for the switch through the opening in the case for the tape deck. Insert your headphone jack into the hole you created and tighten it down. At this point you will want to reinstall the cd player on top of the board you were working with. Take care to ensure that the wires you soldered into place are not being pinched. Once that is done reinstall the faceplate and the volume knob and equalizer knobs and the screws holding it in place. Reinstall the top to the radio and any remaining screws and test. Mine sounds great. plug in my phone when the radio is in tuner mode and it switches to Aux-in from my phone. Let me know if there is any confusing bits.
-
The time has come to produce the Mopar1973Man High Idle & MPG fooler switches again.
We have one more switch for sale in the store. Harness is new and was only used to spec out the next run of switches. Now that we have spec'd out the next harnesses this one can be sold. Fully tested and working.
-
Would You Invest in My Truck or A Newer Truck
I wouldn't give me 7 for it, Been watching over the last couple months to see if the price comes down. A non running truck is work just above scrap value. Heck I only Paid $1000 for my 2nd gen. Pretty sure I can drop the cr head on my block.
-
98-99 HD steering upgrade
Interesting.
-
Would You Invest in My Truck or A Newer Truck
This did catch my eye http://cosprings.craigslist.org/cto/5313550511.html Pretty basic, but it is what I want. I could prob make some money back by selling the injectors and block..... Shove my motor into it and call it a day.
-
98-99 HD steering upgrade
Great article!!! How was the process of creating it in the new article section? easy? Thanks a ton
-
98-99 Heavy Duty Steering Conversion
Great Write-up
-
99 dakota 44re tranny problems
are you %100 sure it is shifting in and out of OD and not locking and unlocking the Torque Converter? Do you have good lockup?
-
Effect of Altitude on a Turbo Diesel
Effect of Altitude on a Turbo Diesel This Article covers the effect of being at higher altitude in a Turbo Diesel powered vehicle. The princples work the same on a Cummins 24v vs common rail and powerstroke or duramax. First thing we need to look at why altitude plays a role. We need to remember that at sea level there is about 14.7 psi of pressure in the air you breath. You can figure out this number by doing some basic math seen below. I am gonna quote some wiki info from https://en.wikipedia.org/wiki/Pounds_per_square_inch to show how PSIA is caluclated " The pound per square inch or, more accurately, pound-force per square inch (abbreviations: psi, lbf/in2, lbf/in2,lbf/sq in, lbf/sq in) is a unit of pressure or of stress based on avoirdupois units. It is the pressure resulting from a force of one pound-force applied to an area of one square inch: 1 psi = = ≈ 6894.757293168 N/m² Therefore, one pound per square inch is approximately 6894.757 Pa. Now converting the psi to standard atmospheres: 1 atm = = ≈ 14.69594877551 psi Therefore, 1 atmosphere is approximately 14.696 pounds per square inch. Pounds per square inch absolute (psia) is used to make it clear that the pressure is relative to a vacuum rather than the ambient atmospheric pressure. Since atmospheric pressure at sea level is around 14.7 psi, this will be added to any pressure reading made in air at sea level. The converse is pounds per square inch gauge or pounds per square inch gage (psig), indicating that the pressure is relative to atmospheric pressure. For example a bicycle tire pumped up to 65 psi above local atmospheric pressure (say, 14.7 psia locally), will have a pressure of 65 + 14.7 = 79.7 psia or 65 psig.[1][2] When gauge pressure is referenced to something other than ambient atmospheric pressure, then the units would be pounds per square inch differential (psid). " and a pretty graph Now as we all know there is less air the higher in altitude you go. But the real question is how much does it really matter? I mean the turbo compresses air anyways so does a little less atmospheric pressure really matter? Well the answer is yes absolutely it matters. A lot of people say that when you have a NA engine it matters a ton but on a turbo engine it isn't as big of a deal. While that is somewhat true we can see below that turbo engines also suffer a good deal. So using the below you can see in the "PSIA" column the atmospheric pressure at a given altitude. As expected we see about 14.7 PSIA at 0 feet. If we look down the chart we can see at 3000' altitude you should have 13.17 psia or about 1.5 psi less than at sea level ( 14.7 - 13.17 = 1.53 psi). Now lets step up to 7000' were a lot of us Rocky Mountian guys live. The PSIA at 7000' is ~11.34 or about 3.5 psi less than at sea level ( 14.7 - 11.34 = 3.36 PSI) Well those numbers are all fine and dandy, but what does that actually mean? So lets think of this in laymens terms and just add the PSIA to the overall boost on the gauge IE: if your gauge reads 30 PSI you actually have 44.7psi at sea level ( 30 Psi + 14.7 psia = 44.7 psi). Lets say now that you are sitting idle at a stop light. At sea level sitting at a stop light you have a total boost of 14.7 psi ( 0 psi from the turbo + 14.7 psia = 14.7 psi). Lets do the same with 3000' At idle you now only have 13.17 psia at idle. And at 7000' you have a whooping 11.34 psia at idle. So in order for the guy at 7000's to have the same boost as the guy at sea level the turbo will need to create that extra 3.5 psi. So to sum it up the guy at sea level has the same amount of boost going into the engine at idle as the guy at 7000' when his gauge is reading 3.5psi. So you can think about this all in terms of, How long does your truck take to make 3.5 psi worth of boost? The time it takes for your truck to make that boost is how much quicker the guy at Sea Level will spool. Right off the line the guy at sea level is already "spooling" 3.5psi worth of boost compared the the guy at 7000's altitude. You could also think of it as if you lined 2 trucks up and told them to drag race, but told one driver that he could brake boost to 3.5psi while the other truck had to leave the line at idle. It is easy to see which truck will leave the line quicker. As we can see this means that the turbo will have to work harder when it is at a higher altitude. From a stop the turbo at 7000' is automatically at a 3.5psi disavantage to the guy at sea level. Not only does altitude have an effect on Off idle performance, but it also has an effect on the upper end of the turbo map. The turbo has a map that shows how much air it will flow. How To Read Turbo Map So we need to consider that the in order for the turbo at 7000' to make 30 psi on the boost gauge it will actually have to make 33.5psi of boost. Fine and dandy right? What's another 3.5 psi worth of boost on a diesel right? Well if we consider that each turbo has it's limits that it flows air, we know that while the turbo at sea level might be efficent at 30 psi of boost, the turbo at 7000' might be out of it's map when the gauge hits 30psi as it actually has to create 33.5 psi total pressure. The turbo at 7000' altitude will become inefficent 3.5psi sooner than the turbo at sea level. If we use the rule of thumb and say every 10psi of boost is worth 100 hp at the crank we say say that a truck at 7000' will make roughly 35 hp / 70tw less than the same truck at sea level if the turbo is kept within the same map both times. Numbers are fine and dandy, but lets see some proof to back all of this up. First the spec's on the truck. - 2000 ram 2500 24v Cummins - 3.55 rear end 47re tranny - 7x.009 DFI vco injectors - 235/85/16 tires - Quadzilla tuner ( turned off for the videos) Here are some Videos. 0' altitude I was unable to ge ta video of this, but I can say that smoke output was pretty much 0 at sea level I would say the DFI 7x.009 injectors were Less than a stock truck with a timing box with no canbus fueling. You can see the difference between 2000' and 7000' so keep that in mind. 2000' Altitude 7000' Altitude As you can see the difference is HUGE. So to sum up everything. Altitude plays a HUGE role in how your turbo diesel runs. A truck at Altitude will smoke more, build boost slower, run out of boost faster AKA It's map. So what can we do about it? Truthfully, Nothing. You need to build your truck with this in mind. If you live at high altitude you might not want the same turbo that you would at sea level.
-
Air & Exhaust Article - Holset HE351 VE VGT Standalone Turbo Arduino Controller Tuner
HE351ve Holset VGT Controller This article is for the standalone controller / tuner needed to control a Holset HE351 ve He351 VGT turbo from a 6.7 Cummins. This controller will help you tune the holset he351ve vgt turbo for your truck. It is is %100 open source you can tune the turbo in any manner you like. It will take some trial and error to tune the holet he351vgt, but the pay off is worth it. The he351ve really shines when it comes to low end power and having a flat torque curve. He351ve Airflow Specs The reason for wanting this turbo comparted to another aftermarket turbo are, Increased flow over a hx35 turbo ( 60lb/min to 69 lb/min) built in Exhaust Brake functions, Cheap turbo cost, fast spooling, and good mpg's if you have it tuned right. For a 5.9 Cummins the he351ve makes a great towing turbo for hp levels up to 500. It will be hot at 500hp but it is possible, not recommended, but possible. This should also work for He451 ve vgt or other Holset variable Geometery turbos. 551 431 turbos There is a certain amount of DIY needed to get this setup on your truck. You will need to learn the arduino system, how to wire it, power it, etc etc etc. Basic Video Here is a Video of the basic code and how it works with the VGT turbo If you read through this and have ANY questions, feel free to Post to the Ongoing thread covering the progress on this project You can Find the Forum Link HERE Parts: Here are the list of parts that are used. you can void the code to use one or all of the sensors, but this list is for everything. Arduino uno: http://www.amazon.com/Arduino-Board-Module-With-ATmega328P/dp/B008GRTSV6 $25 Canbus Shield: http://www.amazon.com/CAN-BUS-Shield-Compatible-Arduino-Seeeduino/dp/B00NQVH666 $40 Exhaust/boost sensor 0-100 psi: http://www.auberins....products_id=271x2 if you want to control the turbo on both exhaust and boost. $56 a piece and they come with 3 wire pigtails. Potentiometer push pull 10k linear: Mouser Link $15 Momentary on button switch: havent picked one up yet that I like. Currently using a computer button. Wire: 16 gauge should be fine 100' should be enough, ensure to get good quality wire Connectors: I used 2x DT06-12SA and 2 x DT06-12PA along with all hardware, ebay link LCD Screen: I used a 4x20 screen with a I2C adapter. Searching EBAY should find you one. Click link to see search. Turbo Connector 4 pin: Mouser Connector Link 54200410-B Pins 10762770 Turbo RPM Connector: Mouser Connector Link PN: 282087-1 Software: You will need to download the Arduino program: Arduino - Software You will need the libraries that I use. You can Download them all from My Google Drive Download the Canbus library: Dropbox - CANLibrarymaster.zip (thanks to Farm828) download the LCD Library: Dropbox - LiquidCrystal.zip Download the Freqmeasure library https://www.dropbox.com/s/yv98sgdllckc9z4/FreqMeasure.zip?dl=0 Download the Timer library https://www.dropbox.com/s/xa0lxny0pftdi6h/Timer-master.zip?dl=0 Basic starter Code downloaded here: Dropbox - HE351VE_Control.ino (thanks to Farm828) This is the code from CF without my changes You can edit the code by voiding the sensors "//" you are using in the right section, defined. My code has changed significantly from the above. How to Connect everything I will go into some detail here. First basics of the arduino uno and cabus_ shield. Arduino boards allow you to "stack" shields onto it via the pins on the outside edge of the board. Each Pin on the arduino and shield correlate to the Pins the code below. You can think of the Arduino as a Small computer and the Shield as a device to perform another specific task, like WIFI or Audio or in this Case Communicate on a Canbus Network. Stacking the shield onto the Arduino allows the arduino to talk in Canbus. First is the Arduino Uno Next is the Can bus Shield that you stack on top Together they should look like this. notice how they are connected, stacked on top of each other with the pins from the shield extending into the Arduino board. Each Shield will use some pins so your code must take that into consideration. Just as an example the can bus shield might use pin 10 and 11 ( I dont remember off the top of my head) so in your code you can't address those pins outside of the canbus shield use. Next you will need to connect all the wires to the sensors. I used some weather proof plugs to make my arduino detachable from the rest of the wiring harness. You will need to figure out a way to connect your harness to the arduino. I used a shield to do this like this. Now for actually connecting the wires from the sensor to the board you will need 3 wires for boost -5v -Sensor return ( pin A0) -Ground 3 wires for Drive -5v -Sensor return ( pinA1) -Ground 3 wires for Pot -5v -Sensor return ( pin A2) -Ground 1 wire for TPS -Sensor return ( pin A3) 2 wires for PotSwitch -Ground return ( pin D2) -Ground 2 wires for EBSwitch -Ground return ( pin D9) -Ground 4 wires for LCD screen -5v -Ground -SCL ( Pin A5) -SDA ( Pin A4) 2 wires for The turbo Shaft speed input -positive signal ( goes to the 9924 chip) -Neg signal ( goes to the 9924 Chip) -Output from pin 7 of 9924 chip to pin 8 of the arduino. Here is an example from www.Arduino.cc of how to wire a simple pot/sensor. you can see 5v. ground, and the sense return going to pin 2 Keep in mind some shields provide more 5v outputs and grounds than others. You can splice the grounds together and run them into one or a couple grounds on the arduino. The Code He351ve Boost/Drive Controlled My basic code is as follows for controlling the he351ve using boost and drive.. You can change it / use it / do whatever you like. You can download the tab'd version of the boost controlled code HERE Keep in mind that it is VERY easy to overspeed the he351ve turbo. Holset rates the turbo to 130,000 rpm. Using the code below I was seeing speeds of up to 160,000 rpm. ENSURE you tune the turbo for your fueling. I found that it is nearly impossible to manage the turbo efficently without using shaft speed so I do not recommend driving the turbo on this code. You will run into egt issues, you will run into shaft speed issues. the boost map code is no longer updated so the version that is hosted is what you get. I have noted in the code as much as I could,. The basic run down for what this code allows is. - During normal driving it will allow you to choose from 3 different boost maps, performance, daily, and Economy by using the pot, with the switch off, to have low/mid/high input from the pot. Vein position is managed by the boostmap until 30 psi is hit. after 30 psi boost the program will switch over to DPmanage and it will attempt to keep drive pressure at 50psi ( defined by code "maxexhaustpressure") which keeps drive to boost ratio within check, 40psi boost theory max 50 theory max drive 40psi/50psi gives a ratio 1.25:1. the HE351 turbo seems to like a high ratio on the lower end. I see ratio of 2:1 all the time until boost is above 20psi, then it starts to level off and come down closer to 1:1. - Turning the pot switch on allows you to manually set the vein position as long as throttle input is below %25. If you turn the pot all the way to 1000 value ( turbo is limited to positions 40-970) it will lock the turbo %100 open regardless of throttle input. You can use the pot to set the turbo position to small and allow for fast warmup. - Exhaust brake will work provided pot switch is off and throttle input is below %5 it will try and keep EB pressure at 45psi per the code. If pressure increases to above 45 psi it will slowly open the veins. He351ve TURBO RPM based Controller Code Thanks to hakcenter at lilbb.com I have edited my code to include his turbo shaft speed controller for the turbo. It is smoother and more refined than using the boost/drive to control the vanes. You will not run into EGT issues or shaft speed issues using this code. You can download the code in the attached zip ** versions after 1.11 are for the arduino mega so if you are using an arduino uno ensure you use version 1.11 This requries you add a 9924 chip to your controller to count rpms. I highly suggest you visit www.lilbb.com and look at his controller shield for the arduino if you want a more out of the box controller. Additional Parts Umax 9924 Chip: Mouser link Pullup Resistors 10k: SparkFun Link You can find the documentation for the 9924 HERE, Click "Data Sheet" Chip: Pins: Basics on wiring for A2 Mode: 1 vr+ ( turbo +) 2 vr- ( turbo -) 3 NC ( not connected) 4 GND 5 GND 10 +5v 9 GND 8 NC 7 IO8 + 10k + 5v pullup 6 GND Top left is 1, Top right is 10 Bottom left is 5, Bottom right is 6 He351ve Shaft speed Controller with ODB interface In my quest for a better controlled turbo I have decided to interface with a pretty cool OBDII interface. It is $39.99 shipped and should plug and play into your arduino. It converts the Canbus info into serial signal that can be read by the arduino via the library that was created for the device. You can find it Arduino OBD2 reader You will plug this into your vcc, gnd, tx, and rx pins of the arduino. Due to the age of the cummins there is a limited amount of info that can be used, but it does read RPM, TPS, Coolant, and IAT ( I think) maybe some other stuff, but I am not sure. The biggest perk to this is you can now use Engine RPM in your code to increase the vane size at higher RPMS while keeping the turbo responsive down low. You can download the code in the attached zip This code is still Beta so use at your own risk. Spool speed with the He351vgt. I went to about %35 throttle at about 8-9 seconds into the video. If you found this helpful please shoot a donation my way. Everything I do is to help support the community. Thanks -Me78569 he351.zip View full Cummins article
-
Holset HE351 VE VGT Standalone Turbo Arduino Controller Tuner
HE351ve Holset VGT Controller This article is for the standalone controller / tuner needed to control a Holset HE351 ve He351 VGT turbo from a 6.7 Cummins. This controller will help you tune the holset he351ve vgt turbo for your truck. It is is %100 open source you can tune the turbo in any manner you like. It will take some trial and error to tune the holet he351vgt, but the pay off is worth it. The he351ve really shines when it comes to low end power and having a flat torque curve. He351ve Airflow Specs The reason for wanting this turbo comparted to another aftermarket turbo are, Increased flow over a hx35 turbo ( 60lb/min to 69 lb/min) built in Exhaust Brake functions, Cheap turbo cost, fast spooling, and good mpg's if you have it tuned right. For a 5.9 Cummins the he351ve makes a great towing turbo for hp levels up to 500. It will be hot at 500hp but it is possible, not recommended, but possible. This should also work for He451 ve vgt or other Holset variable Geometery turbos. 551 431 turbos There is a certain amount of DIY needed to get this setup on your truck. You will need to learn the arduino system, how to wire it, power it, etc etc etc. Basic Video Here is a Video of the basic code and how it works with the VGT turbo If you read through this and have ANY questions, feel free to Post to the Ongoing thread covering the progress on this project You can Find the Forum Link HERE Parts: Here are the list of parts that are used. you can void the code to use one or all of the sensors, but this list is for everything. Arduino uno: http://www.amazon.com/Arduino-Board-Module-With-ATmega328P/dp/B008GRTSV6 $25 Canbus Shield: http://www.amazon.com/CAN-BUS-Shield-Compatible-Arduino-Seeeduino/dp/B00NQVH666 $40 Exhaust/boost sensor 0-100 psi: http://www.auberins....products_id=271x2 if you want to control the turbo on both exhaust and boost. $56 a piece and they come with 3 wire pigtails. Potentiometer push pull 10k linear: Mouser Link $15 Momentary on button switch: havent picked one up yet that I like. Currently using a computer button. Wire: 16 gauge should be fine 100' should be enough, ensure to get good quality wire Connectors: I used 2x DT06-12SA and 2 x DT06-12PA along with all hardware, ebay link LCD Screen: I used a 4x20 screen with a I2C adapter. Searching EBAY should find you one. Click link to see search. Turbo Connector 4 pin: Mouser Connector Link 54200410-B Pins 10762770 Turbo RPM Connector: Mouser Connector Link PN: 282087-1 Software: You will need to download the Arduino program: Arduino - Software You will need the libraries that I use. You can Download them all from My Google Drive Download the Canbus library: Dropbox - CANLibrarymaster.zip (thanks to Farm828) download the LCD Library: Dropbox - LiquidCrystal.zip Download the Freqmeasure library https://www.dropbox.com/s/yv98sgdllckc9z4/FreqMeasure.zip?dl=0 Download the Timer library https://www.dropbox.com/s/xa0lxny0pftdi6h/Timer-master.zip?dl=0 Basic starter Code downloaded here: Dropbox - HE351VE_Control.ino (thanks to Farm828) This is the code from CF without my changes You can edit the code by voiding the sensors "//" you are using in the right section, defined. My code has changed significantly from the above. How to Connect everything I will go into some detail here. First basics of the arduino uno and cabus_ shield. Arduino boards allow you to "stack" shields onto it via the pins on the outside edge of the board. Each Pin on the arduino and shield correlate to the Pins the code below. You can think of the Arduino as a Small computer and the Shield as a device to perform another specific task, like WIFI or Audio or in this Case Communicate on a Canbus Network. Stacking the shield onto the Arduino allows the arduino to talk in Canbus. First is the Arduino Uno Next is the Can bus Shield that you stack on top Together they should look like this. notice how they are connected, stacked on top of each other with the pins from the shield extending into the Arduino board. Each Shield will use some pins so your code must take that into consideration. Just as an example the can bus shield might use pin 10 and 11 ( I dont remember off the top of my head) so in your code you can't address those pins outside of the canbus shield use. Next you will need to connect all the wires to the sensors. I used some weather proof plugs to make my arduino detachable from the rest of the wiring harness. You will need to figure out a way to connect your harness to the arduino. I used a shield to do this like this. Now for actually connecting the wires from the sensor to the board you will need 3 wires for boost -5v -Sensor return ( pin A0) -Ground 3 wires for Drive -5v -Sensor return ( pinA1) -Ground 3 wires for Pot -5v -Sensor return ( pin A2) -Ground 1 wire for TPS -Sensor return ( pin A3) 2 wires for PotSwitch -Ground return ( pin D2) -Ground 2 wires for EBSwitch -Ground return ( pin D9) -Ground 4 wires for LCD screen -5v -Ground -SCL ( Pin A5) -SDA ( Pin A4) 2 wires for The turbo Shaft speed input -positive signal ( goes to the 9924 chip) -Neg signal ( goes to the 9924 Chip) -Output from pin 7 of 9924 chip to pin 8 of the arduino. Here is an example from www.Arduino.cc of how to wire a simple pot/sensor. you can see 5v. ground, and the sense return going to pin 2 Keep in mind some shields provide more 5v outputs and grounds than others. You can splice the grounds together and run them into one or a couple grounds on the arduino. The Code He351ve Boost/Drive Controlled My basic code is as follows for controlling the he351ve using boost and drive.. You can change it / use it / do whatever you like. You can download the tab'd version of the boost controlled code HERE Keep in mind that it is VERY easy to overspeed the he351ve turbo. Holset rates the turbo to 130,000 rpm. Using the code below I was seeing speeds of up to 160,000 rpm. ENSURE you tune the turbo for your fueling. I found that it is nearly impossible to manage the turbo efficently without using shaft speed so I do not recommend driving the turbo on this code. You will run into egt issues, you will run into shaft speed issues. the boost map code is no longer updated so the version that is hosted is what you get. I have noted in the code as much as I could,. The basic run down for what this code allows is. - During normal driving it will allow you to choose from 3 different boost maps, performance, daily, and Economy by using the pot, with the switch off, to have low/mid/high input from the pot. Vein position is managed by the boostmap until 30 psi is hit. after 30 psi boost the program will switch over to DPmanage and it will attempt to keep drive pressure at 50psi ( defined by code "maxexhaustpressure") which keeps drive to boost ratio within check, 40psi boost theory max 50 theory max drive 40psi/50psi gives a ratio 1.25:1. the HE351 turbo seems to like a high ratio on the lower end. I see ratio of 2:1 all the time until boost is above 20psi, then it starts to level off and come down closer to 1:1. - Turning the pot switch on allows you to manually set the vein position as long as throttle input is below %25. If you turn the pot all the way to 1000 value ( turbo is limited to positions 40-970) it will lock the turbo %100 open regardless of throttle input. You can use the pot to set the turbo position to small and allow for fast warmup. - Exhaust brake will work provided pot switch is off and throttle input is below %5 it will try and keep EB pressure at 45psi per the code. If pressure increases to above 45 psi it will slowly open the veins. He351ve TURBO RPM based Controller Code Thanks to hakcenter at lilbb.com I have edited my code to include his turbo shaft speed controller for the turbo. It is smoother and more refined than using the boost/drive to control the vanes. You will not run into EGT issues or shaft speed issues using this code. You can download the code in the attached zip ** versions after 1.11 are for the arduino mega so if you are using an arduino uno ensure you use version 1.11 This requries you add a 9924 chip to your controller to count rpms. I highly suggest you visit www.lilbb.com and look at his controller shield for the arduino if you want a more out of the box controller. Additional Parts Umax 9924 Chip: Mouser link Pullup Resistors 10k: SparkFun Link You can find the documentation for the 9924 HERE, Click "Data Sheet" Chip: Pins: Basics on wiring for A2 Mode: 1 vr+ ( turbo +) 2 vr- ( turbo -) 3 NC ( not connected) 4 GND 5 GND 10 +5v 9 GND 8 NC 7 IO8 + 10k + 5v pullup 6 GND Top left is 1, Top right is 10 Bottom left is 5, Bottom right is 6 He351ve Shaft speed Controller with ODB interface In my quest for a better controlled turbo I have decided to interface with a pretty cool OBDII interface. It is $39.99 shipped and should plug and play into your arduino. It converts the Canbus info into serial signal that can be read by the arduino via the library that was created for the device. You can find it Arduino OBD2 reader You will plug this into your vcc, gnd, tx, and rx pins of the arduino. Due to the age of the cummins there is a limited amount of info that can be used, but it does read RPM, TPS, Coolant, and IAT ( I think) maybe some other stuff, but I am not sure. The biggest perk to this is you can now use Engine RPM in your code to increase the vane size at higher RPMS while keeping the turbo responsive down low. You can download the code in the attached zip This code is still Beta so use at your own risk. Spool speed with the He351vgt. I went to about %35 throttle at about 8-9 seconds into the video. If you found this helpful please shoot a donation my way. Everything I do is to help support the community. Thanks -Me78569 he351.zip
-
Would You Invest in My Truck or A Newer Truck
I have been eye balling some 3rd gens lately, because my truck is tired. Can't argue that, but I cannot bring myself to spend so much money on a 10+ year old truck with 100,000 + miles. I cannot understand how people pay for their new trucks as of late. My mortgage is less than most of the payments for the new trucks out there. so in the end I just keep driving the junker, I fix what is badly broken and ignore the 2nd gen rattles. It always gets me where I need to go and even if I have to spend a hundred a month keeping it on the road that is better than a car payment, or even the full coverage that is required with a auto loan.
-
Ball joints
Thanks I'll give them a call.
-
Ball joints
alright, now that I am home I am trying to figure out what joints to put in. It seems that the spicer joints that are knurled are the cheapo ones. I can't remember if the ones I put in where knurled or now. I am not sure if the denny drive shaft ones are knurled or not, but they are sold out regardless. so my question now is where do I find the "good" dana spicer stuff? Any more thoughts on another brand I should do? Rock auto is very limited for what they have for 96-98 trucks, I think acdelco is the best they have. No Rayebeso, no DANA. I hate hate hate this.
-
He351ve stand alone Arduino controller code for 2nd Gen Cummins
Made a holiday trip to my moms house up in north minnesota, AKA sea level. I cannot say how much I hate living at 7000' in altitude. with my 100 injectors and my quadzilla turned up my truck is all but smoke free at 450 hp worth of fuel at sea level, at home my truck smokes like a train.I could EASILY pass emissions with the fuel turned up if I didn't live at 7000'I did notice that my boost and drive sensors were reading high at idle, due to more atmospheric pressure. I have added some to my code to adjust the boost and drive values by comparing idle state boost to recorded boost, IE: at idle boost should read 0 so if it is reading more or less I can adjust the readingsHere is the timer trigger Code: [Select] if (timer % 800){ //checks for idle state to run the barcalc section, which corrects the boost and drive sensor for altitude changes. if (ThrottlePosition = 0){ barcount ++; if (barcount = 10){ baroffset(); } } else { barcount = 0;} }Pretty much if TPS is 0 for 10 times through the timer section it will run baroffset(); Code: [Select] void baroffset (){ // compares idle state boost to 0 psi so altitude isn't causing miss readings. barcount = 0; barcalcb = 0 - BoostPressure; barcalcd = 0 - ExhaustPressure; }Then I adjust my boost and drive reads. Code: [Select] if (adc_roll_over == 1) { BoostPressure = ReadBoostPressure() + barcalcb; } if (adc_roll_over == 2) { ExhaustPressure = ReadExhaustPressure() + barcalcd; } Version 1.07 is now uploaded. It is beta, but should work as it is a simple adjustment.
-
Curious what others think of installing a blocking diode to prevent AC Noise
less than .05 ac. I think .02 is where most are happy.