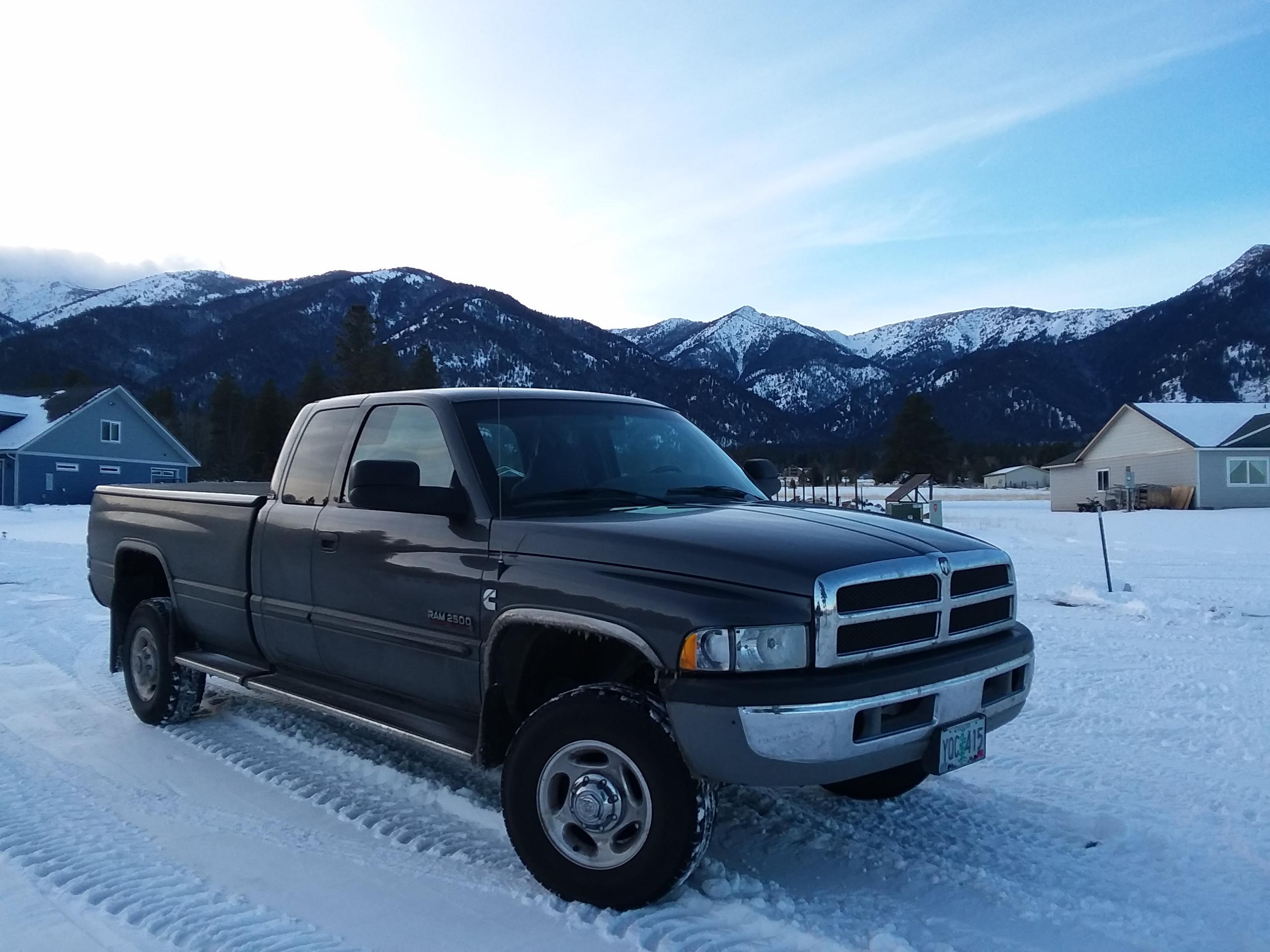
Everything posted by Tractorman
-
98 12 valve cummins no bus, need help please
You can use dielectric grease, but I don't think it will help your situation. The dielectric grease primarily helps keep out moisture and reduces the likelihood of oxidation on the pins. I would carefully inspect the multi-pin connectors for any spreading of the the female terminal and inspect for any wires that may be partially pushed back inside the connector. - John
-
Poor fuel MPG
The two photos below show my setup using a 0-5,000 ohm variable resistor (potentiometer). I have it set to display a constant 143° when checking with my OBLink scanner. The temperature never varies. There are lots of resistors (fixed and variable) to choose on Amazon or other sites. Here are some excerpts from Michael Nelson (Mopar1973Man) from a few years ago. They should be helpful for understanding how cold intake air / warm intake air affect engine performance and fuel economy. - John
-
Poor fuel MPG
Mine has been on my truck for about 8 years. I will take a photo of it tomorrow and post it here. From what I remember, it is a 5,000 ohm 1/4 watt variable resistor. I mounted it in the engine compartment near the driver side hood hinge. Essentially, the IAT sensor is disconnected and sealed off. A two-pin Deutsch male electrical connector with a six inch lead can be purchased from Amazon and used to lengthen the wiring to the the mounted potentiometer. It is a relatively simple process. I can post more detail tomorrow. Also, I forgot to mention that I use a homemade winter front during the winter months for faster engine warmup and improved driveability. This also helps improve fuel economy. - John
-
Poor fuel MPG
The speed was quite variable. On the way to Cresecent City, the roads were snowpacked for about 350 miles, so speed was about 45-50 mph with a lot of time in 4WD. On the return trip, speeds were about 60-65 mph where the roads were clear which was most of the way. The speeds were slower through the mountain passes (7 passes each way). - John
-
Poor fuel MPG
Have you done the IAT sensor fooler with a resistor yet? I use a varaiable resistor that sets the IAT sensor reading at 143° all the time. This really helps for winter performance and fuel economy. Plus, the engine runs quieter when cold. I use a Smarty S03 on a mild tune with stock timing - RV275 hp injectors. About a month ago, I made a trip from Baker City, Or to Crescent City, Ca (a 1,000 mile round trip) carrying about 800 lbs in the bed for traction. I averaged just over 20 mpg with ambient temperatures ranging from 5° below zero to 40° above. Most of the time the temperature was in the 20's. - John
-
Surging
How about when the engine is at idle. Does the APPS stay at zero percent when the engine rpm's vary? - John
-
Surging
I use an OBDLink LX OBD2 Bluetooth Scanner through my Android phone to read live APPS signal data with the engine running. Do you have this capability? It would be good to verify that there is a 0 percent APPS signal commanded when the engine is at idle. What exactly do you mean when you say, "I can watch my throttle on my adrenaline and its fluctuating up and down when using accelerator."? Are you talking about the per cent of throttle commanded? A steady throttle should result in a steady per cent value for the commanded APPS signal. - John
-
Surging
Since the W-T wiring mod essentially shortens and improves electrical grounds for the ECM and PCM and alternator, I would think it would be less likely for electrical interference to be a source of your problem. Not sure if you have done the mod and also not sure if your question was referenced to after the W-T wiring mod, or before the mod. - John
-
Surging
Interesting that the surging goes away while using cruise control. With manual transmission trucks, the ECM controls throttle while using cruise control - the APPS is completely out of the loop. It seems like you are getting an unwanted signal through the APPS when driving without using cruise control. I think you need to physically disconnect the Adrenaline completely and then test drive. If possible, use a scanner to observe the APPS signal with the engine running and while driving the truck. With the engine at idle, the APPS signal should be 0 percent. This is controlled by the idle validation switch in the APPS. I recall someone having a similar problem and it turned out to be that the throttle low limit set screw was loose and the APPS couldn't set the idle validation switch. - John
-
Finally decided to add cupholders! We shall see.
I was wondering if there was a latch adjustment of some kind. Thanks for the tip. - John
-
Finally decided to add cupholders! We shall see.
@Doubletrouble, I received and installed my cup holder. It works well with my 6 spd. I think the truck has just a little more power now, too. At this point, I didn't use any hardware to fasten the cup holder. I did notice that the console lid doesn't latch anymore with the added material of the cup holder. Did you have the same issue? - John
-
Lift Pump Suction
Something else you may be interested in..., After dropping my fuel tank twice over the last 20 years, I decided to make an access door through the truck bed. One of the best mods I ever did. The actual time it takes to do the mod is about the same as dropping the fuel tank, replacing the basket, and re-installing the fuel tank. With the modification completed, I can now remove the fuel basket in about 10 minutes. Easy access to electrical and fuel connections, easy to remove the large threaded nut, easy to remove and install the fuel basket. Also, the job can be done regardless of the level of fuel in the tank. - John
-
Lift Pump Suction
There is another option without modifying your new fuel basket plumbing. On my truck with an OEM fuel sender basket (no pump), I installed the basket and hooked up the fuel lines in an OEM fashion. Along the frame I cut the return fuel line and installed a three-way valve and added a fuel line and a tee to the fuel tank filler neck. With the newly added three-way valve in one position, fuel returns to the basket - a good option during winter months when warm fuel is desirable. With the valve in the other position, fuel returns to the fuel tank via the tank filler neck. This is a good option during the hot summer when cooler fuel is desirable. Just be aware that whichever method you use, more fuel will flow through the one-way check valve in the bottom of the fuel basket when the fuel is returned outside of the basket. This will result in running out of fuel sooner as the fuel tank nears empty. When fuel is returned directly to the basket (about 70% of the volume drawn from the basket), then the fuel level can be drawn down a little farther before running out of fuel. Here is the filler neck T. - John
-
Finally decided to add cupholders! We shall see.
Thanks for the photos and the followup. I think I'm going to do it Is this the correct cup holder? - John
-
Finally decided to add cupholders! We shall see.
I am curious to hear back after you drive the truck using the cup holder. I may have to do the same mod. - John
-
Anyone close have a smarty I can borrow?
I have a Smarty S03 and the high idle is enabled on my truck. I was not impressed with it at all. First, there are many times I wished the high idle would come on in the 6 cyl mode, but it never did. Then, when it did operate, it ramped up to the 6 cyl high idle and then switched to the 3 cyl high idle. OBNOXIOUS!! HORRIBLE!! The first time it activated, I was in the house. I thought the oil drain plug must have fallen out and all the rods were knocking. Not for me. These trucks are already noisy enough - especially when they are cold. So, last summer I decided to install my own mechanical high idle. It works very well and I get to be the boss and turn it on whenever I want. It is also nice to have on a 100° day in a parking lot. I posted what I did on this site. Here's a link. - John
-
Is there a foolproof way to tell if I need a heater treater?
For the second generation Dodge Ram ('95-'02), this is about the blend door actuator. It is the only electronically operated ventilation door on our trucks. The rest of the doors are vacuum operated. The blend door's OEM "interposer" is plastic and prone to cracking or just wearing out. The replacement interposer is steel. - John
-
No crank No go.
I wrote this post almost 24 hours ago, but an ice storm nearby shut off the internet service, so I could not post. Even though it appears that you have solved your problem, I am posting now anyway. I would use a test light with an incandescent bulb for all my tests. This test light will place a small electrical load on the circuit being tested and clearly show whether or not the circuit is working properly. The tests are simple and reliable. For part of the testing I would use a jumper wire. For the following tests, use the wiring diagram to follow along for each test to help you understand the test and the test results. Make sure the transmission is in "Park" and the park brake is set. Ignition key "Off". First test. This test will check continuity between the starter relay terminal #87 and the starter solenoid. Remove the starter relay. Use a jumper wire and connect one end to terminal #87 of the relay base and the other end to the positive battery post. The starter should operate. If it doe not, then continuity between terminal #87 and the starter relay has been lost. Second test. This test will check continuity between the starter relay and ground via the transmission neutral safety switch. Connect a test light clamp to the the positive battery post. Touch the other end to the #85 terminal of the relay base. The lamp should glow. If the lamp does not glow, then have a helper move the transmission selector around during the test. If the lamp occasionally glows, then the transmission linkage needs adjustment or the neutral safety switch needs be replaced. Third test. The test will check continuity between the battery, through Fuse #9 (30 amp), and terminal #30 in the relay base. Use a jumper wire and connect one end to terminal #30 and the other end to terminal #87 in the relay base. The starter should operate. If it does not, then check the condition of the 30 amp fuse and wiring between terminal #30 and the battery. Fourth and last test. This test will check continuity between terminal #85 and the ignition switch "start" terminal. Connect a test light clamp to the negative battery post. Touch the other end to terminal #86 in the relay base. Have a helper turn the ignition switch to the "start " position. The test lamp should glow. If it does not, then continuity has been lost between terminal #85 and the start terminal on the ignition switch. Performing these tests should find the problem. - John
-
No crank No go.
I think @IBMobilehas it right. When the coil is energized, current will flow between terminal 30 and 87. - John
-
Time for new grid heaters.
Your readings could very well be correct. Heating elements can fail both ways - a shorted / partially shorted circuit or an open / partially open circuit. Either way, there will be little or no heat generated by the element. I would be curious for you to retest the old grid heater elements on the bench to verify your first test. Also, do you make a practice of setting a specific range on your multimeter? Do you first touch the leads together to ensure a "0" ohm reading with the leads before testing a component? Even if you checked the resistance value for an new one, the information would not be helpful. Using Ohm's Law one can calculate the approximate resistance value, but only for a heated element that is probably glowing. Under a load the applied voltage would be around 11 volts. The current flow would be approximately 90 amps. That would calculate to be around 1.22 ohms of resistance. But, since that is a heated resistance, that resistance value doesn't mean much. The resistance value would be much, much lower after the element cooled. Our meters do not have anywhere close to the capability to read accurate resistance values that low. Even if they could, an absolutely perfect electrical connection would be required at both meter connections and the resistance value for a cold element would have to be known. Another way to look at this would be to consider that only one wire strand of a 20 strand wire was connected and the rest of the wire strands were broken and not connected. The one connected strand would still give you the same almost "0" ohm reading, consequently, there would be no value to that reading. With one connected strand and 19 disconnected strands, an electrical load could not function properly, yet the ohm reading would indicate that the circuit is okay. - John
-
I know this is sudden but...
Today's weather forecast was to be partly sunny. No mention of snow. But we got 4 inches anyway. - John
-
Time for new grid heaters.
Make sure to verify that the ground terminal of the grid heaters is not problem before replacing the grid heaters. Probably not the case, but it shouldn't be overlooked. - John
-
I know this is sudden but...
@Doubletrouble, I apologize for my remark regarding not being ready for winter. It was meant as humor, but obviously it didn't come across that way. I know that you have some hardships come your way and it seems that you dedicating yourself to taking care of your parents. Very caring. You don't need any sarcastic remarks from me. Also, I thought I was quoting MoparMan - he lives in snow country. In fact, he is about 90 air miles to the east from me (across the Snake River). I think I should pay more attention to who I am quoting. - John
-
I know this is sudden but...
It's January..., How could you not be ready for it? There's more coming your way - looks like a snowy week ahead for us. - John
-
Truck is HORRIBLE in 2HI loose conditions
I can't offer any help regarding the transfer case, but i do have some thoughts about lack of traction in two-wheel drive. * What tire pressure are you running in the rear tires (looks like a dually according to your avatar)? I would run no higher than 40 psi, maybe even less. * Throw some weight in the bed over the rear axle. (500-700 lbs). I carry a 600 lb pallet of pavers during the winter month just for that reason. It works very well for traction, even in two-wheel drive with an open differential. * What material is the clutch made from? organic, ceramic, etc? Organic will have the smoothest engagement Ceramic encourages axle wrap. * What is the condition of your rear shocks? The rear shocks are mounted at an angle on the rear axle to help with forward / reverse torsional stability when putting power to the wheels or engaging the clutch. * Do you engage the clutch without throttle? As you know, these engine have lots of clutch engagement torque. No throttle should be applied until the clutch is fully engaged. Any or all of the above mentioned items can contribute to wheel hop / axle wrap and / or traction loss. - John