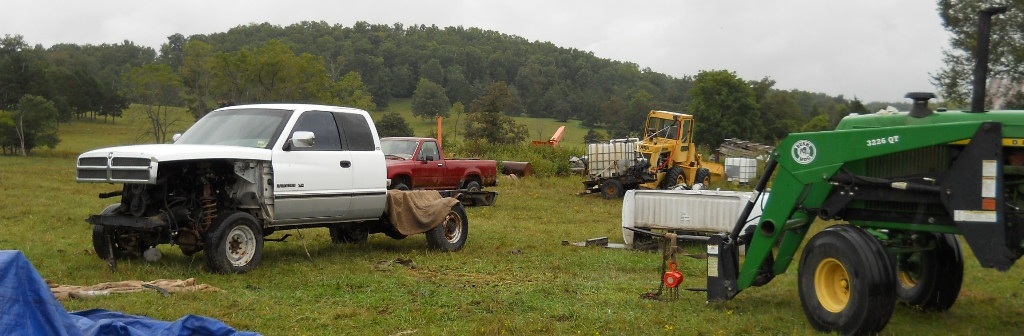
Everything posted by Cowboy
-
HX35 VS HY35-D
That is correct, the HY35, HE341, and HE351 all have the same turbine. However the HY35 has a 54/76.5 and the HE341 has a 56/76.5. These are measurements I personally took and compiled here. I don't have an updated thread on the boost governor, but here's an old one, but the internals have changed considerably. If you're thinking about building one, let me know, I'm pretty sure I can make one and ship it to you for cheaper.
-
HX35 VS HY35-D
Again, remember, this is a HY35 but with a HX35 compressor wheel, otherwise known as a HE341. On the wastegate I understand 100%! With the HX35 I made my own wastegate actuator that put a "banks bighead" plumb to shame, and I also designed a boost governor, which basically plugged the wastegate until my set pressure is reached then opens it as needed to maintain your desired boost. So if it's set at 35 psi, the wastegate will be closed and no pressure in it at 34 psi, and fully open at 36 psi. The plate that goes over the wastegate had a dent from the wastegate opening all the way and hitting it. If you can rig up a way to run a boost line from compressor to wastegate that you can hook a boost governor into, I'll make you one and you can have it at cost, just let me know what you think of it. On this HY35-D I enlarged the wastegate to 29mm and am running a spring gate. I need to measure everything again, but I'm pretty sure that it doesn't open till at least 20 psi. Maybe I'm misunderstanding you, but you said that boost:drive is 1:1 till 12 psi? The charts below are easier to read, they are actually 1:1 till about 25-26 psi. One thing to remember though, boost:drive ratio, especially on these smaller turbo's/turbines are largely dependent on RPM. With the HX35 I got 10 psi boost and 6 psi drive pressure at 1200 RPM. But at 2800 RPM, boost is 24, and drive pressure is 35. 1800-2100 RPM was the happy spot for the HX35, it ran about 1:1 regardless of boost, but spooling was still very fast. Is this easier to read, the X axis is RPM. If you would like me to format it differently let me know. Also, you can enlarge my pictures by clicking them. HY35-D (HE341) HX35
-
Boost Elbow
Try a fuel tank petcock. Have you considered a spring gate? I'm really warming up to them.
-
HX35 VS HY35-D
One thing to keep in mind. The stock HY35 on 2nd gen has a 54/76.5mm compressor wheel, this one has a 56/76.5mm compressor wheel. So it's not quite apples to apples. From the limited testing I've done, this turbo is great for automatics. Because you rarely spend time under 1600 RPM, and if you try to get into it to hard the TC will unlock. The spooling on this turbo above say 2000 RPM is very good, it just doesn't do as well below ~1600ish. I don't have a whole lot of data collected, I do plan on doing more testing at a later date, but I need to makes some fueling changes in the mean time. On the boost:drive pressure ratio, you can see the middle chart above, it shows the boost and drive pressure. I did data-log the way back from my runs so here is some of the info I got. Cruising ~35 MPH, 1350 RPM. Boost: 3.6 psi, Drive: 4.5 psi. Pulling a Hill 32 MPH, 1275 RPM. Boost 5 psi, Drive 5 psi. Pulling a Hill 40 MPH,1500 RPM, Boost 12.9 psi, Drive 12.1 psi. Cruising 40 MPH, 1500 RPM, Boost 4.2 psi, Drive 5.1 psi. Also, I do have a wastegate, due to the larger compressor wheel I set it to 35 psi.
-
Injector Pump Operation Vidoes
I was thinking on it, but was hoping others possibly had more info and such, and I'll throw that together to put into an article.
-
Injector Pump Operation Vidoes
I found these videos very helpful for understanding the operation of different designs. P-Pump VE-Pump Governor Operation: This is not an automotive governor but instead a marine one. On automotive governors it has basically the same thing, but the governor operates at all RPM's to help maintain speed when load is applied. This one shows two types neither automotive. The "Regulating Governor" is found on farm machinery and generators, where a constant RPM is desired without having to physically pushing the throttle further. There are different versions of the rotary pump, does anyone know which the 1st gen VE's is, and which the VP44 is? Anyone got any others? Or more info to add, in other forms such a Words, Pictures or Links?
-
HX35 VS HY35-D
It's hard to explain my 'low-traction-pulling-others-out' method. It's like a mix between Jeremy Clarkson and a Sled Puller.
-
HX35 VS HY35-D
I would drive myself nuts trying to get the right tune. I like trying different things and see how they work. I may end up with one, at some point, who know. What would be really cool is if someone let me 'baby sit' there truck for a little while, and didn't mind if it was making 800hp and if there bank account was a little less full then before.
-
HX35 VS HY35-D
Did some turbo swapping on the '96. Went from the older 8 blade HX35 to the HY35-D found on 03-04 dodges. To make the swap easy, I used a HY35 turbine housing off a 2nd gen. This turbo is a 56/58/9W instead of the HX35's 56/60/12WD. I expected faster spooling, and possibly a less restrictive top end... I was wrong. The top end pulls a little harder and spooling is amazing, but down low just doesn't cut it. Here are the runs: RPM, Here you can see the HX35 took off much faster. Pressures, Again, spool-up on the HY was noticeably slower, but the top end did well. 60psi Drive pressure all the way to 3400RPM. For anyone wondering about the funky drive pressure curve, the peak happens about 27-2900RPM, and does that on all 3 runs. EGT's were slightly higher with the HY35, but I believe that was because the extra time the run took. Because they were actually climbing at a slower rate. Obviously, with tuning you could get better, but for a back to back comparison, this shows it pretty well. So if you live above 1800 RPM like with an auto, this would be a good upgrade, better power up top, and spool above 2000 RPM is to die for (or from). However I miss my sub 1400 RPM boost, it was definitely much torqueir down there. So I'll play with other turbo options and see what I can get.
-
From 24 valve to 12 valve
The stock TC is very loose and inefficient. A upgraded one will help a lot, it will: Keep the Tranny Cooler. Improve Acceleration. Improve MPG. Hold More Power then Stock Just because you have a shift kit doesn't mean you need a aftermarket TC, but it will still help. Before you throw to much power at the tranny, you may want to talk to your tranny guy about what he suggests. Auto tranny upgrades is not my strong suit, but I believe there are a couple other small items that you can add to help it hold power. http://www.cumminsforum.com/forum/94-98-drivetrain-except-engine/452157-proper-upgrade-list-transmission.html
-
Higher amp alternator recomendations ?
http://www.dieseltruckresource.com/forums/1st-gen-ram-all-topics-93/leece-neville-alternator-6bt-cummins-247286/
-
Having Line X Applied to Hood
Pictures are stupid easy on this forum. Just go to the folder that has your picture in it, click and drag the picture into the grey box below where you type that says "Drag files here to attach, or choose files...". Then it will upload your pic, once done, but your cursor where you want the picture to be, then click the little '+' button on the image and it includes it into your post!
-
P7100 Timing With Dial Indicator
How to pin time your pump from ground zero with a dial indicator. If you're using a dial indicator, you'll need the plunger lift charts, I've supplied them at the bottum of the article! One's metric and the other is inches, otherwise they're identical. OK, well first things first is you'll need to find #1 TDC. TDC (Top Dead Center) is where #1 piston is at the absolute top of it's stroke. We also need to make sure that's it's the compression stroke, both are very important for a successful timing job. Always double check your TDC and make sure it's the compression stroke, remember, if it's not, you need to spin the engine 360°. Place engine at approximate TDC Compression. Remove DV and Install Dial Indicator into Plunger. Rotate the engine BACKWARDS (CCW when standing in front) until the dial indicator stops dropping. Check the Dial indicator to make sure it's still contacting the plunger and hasn't maxed out, if it's still riding on the plunger continue. Zero the Dial Indicator Rotate the engine FORWARD until your set lift is achieved, lets say it's a 215 pump and we're shooting for 17°, so that's 5.73mm. Pop the injection pump gear off, careful to do it evenly as to not rotate the pump. Once the gear is off, rotate the engine to exact #1 TDC Compression. Clean the shaft thoroughly with brake cleaner or electrical contact cleaner (do not use carb cleaner). Torque Injection Pump gear to 20 ft/lb's and let sit to seat the gear on the shaft. Tighten down the Injection Pump gear nut to 144ft/lbs as specified in the FSM. Recheck your TDC and plunger lift to ensure nothing slipped while tightening the gear.
-
Lift Pump/ Fuel Supply Question
- From 24 valve to 12 valve
Your builders way to check transmission oil is correct, any other way won't read right. Yeah, Your automatic problem sounds electrical. Could also be the TPS The smoke on startup, does the engine sputter a lot? Or just grey smoke a bit? If you feel like pulling the injectors I can pop test them for you and set them to whatever pressure you wish for my cost.- This is fixable, right?
Lol, Prevention. I tore the last one up by looping it over the oil filler for OFV access, but forgot to take it off. The electrical tape/PVC pipe glue makes for a fan resistant coolant line, it works.- This is fixable, right?
It's the rubber strip that runs across the top of the firewall.- The official Good Deal thread! Post good deals on truck and non related stuff.
https://www.jbtoolsales.com/equus-31603-abs-srs-obdii-scan-tool/- DIY Cruise Control High Idle
DIY High Idle using the Stock Cruise Control Servo. First off, before being able to modify the system for high idle, we must understand what we are working with. How the cruise control servo works: Pin 4 (black) is permanently grounded. Pin 3 (blue/red) gets 12 volts from the PCM, through the brake switch when enabled. This is the main feed for the system, it supplies power to all 3 solenoid valves within the servo. Suppling this pin with power closes the "Dump" valve. Without power to this pin, nothing happens. Pin 2 (green/red) gets grounded selectively by the PCM, By grounding this pin, it closes the "vent" valve, thus allowing the servo to hold vacuum. By ungrounding the pin, it will allow vacuum out of the servo decreasing throttle. Pin 1 (tan/red) gets grounded selectively by the PCM. By grounding this pin, it opens the 'vacuum' valve allowing vacuum into the servo increasing the throttle. With our new found knowledge, it has become obvious what needs to be done. But there is something else that we need to remember, if we plan on having cruise control still, we must modify the system in a way that the PCM can still function correctly. So what do we need to accomplish: First things first, we need to make sure be don't back feed the PCM which can cause damage, for this we'll use diodes. Diodes only let current flow in one direction, they're the check valve of the electronics world. By placing diodes in the circuit, it will let the PCM feed the servo as normal, but won't let us back feed it. Perfect! We need to supply Pin 3 with 12 volts, I originally thought I could just turn on the stock cruise control system, however it became obvious that the PCM monitors the system closely, and can detect our fooling around and will shut the power back off, not letting us turn it back one again until the next start up. We need a way of normally having pin 2 open (not grounded), then ground it when the 'enable' switch is on, but then unground it when the 'lower idle' switch is pressed. And then lastely, we need to be able to ground pin 1, very simple, any NO (Normally Open) Switch will do. (Optional) When the 'Enable' Switch is off, disable both the other switches. Keeping that in mind we'll need 4 modes: Hold Idle Mode (High Idle Enabled): Pin 3 - 12 Volts, Pin 2 - Ground, Pin 1 - Open. Increase Idle Mode: Pin 3 - 12 Volts, Pin 2 - Ground, Pin 1 - Ground. Decrease Idle Mode: Pin 3 - 12 Volts, Pin 2 - Open, Pin 1 - Open. Stealth Mode(Makes the PCM think nothings changed): Pin 3 - Open, Pin 2 Open, Pin 1 - Open. With all that in mind, here's what I came up with: Parts List: (This is for my setup, if you wish to change it around, the sky is the limit.) 2 X Push Button Momentary SPST NO Green Black Red 1 X Latching On-Off Switch (lots of options here) 1 X Mini Relay SPDT 6V DC. 1 X 100 ohm 1 watt Resistor 6 X 1N4007 Diodes 1 X 4 Wire Cable 1 X Assortment of Heat Shrink Tubing -> Great Value Yes it is a little complex, but if you have one each of NO and NC momentary switches, and a DPST switch as your 'enable' switch, you can eliminate the resister and relay. I did it the way I did for a couple reasons specific to my setup. If you wish to play around with this circuit, here it is plugged into a circuit simulator, just click the switches, the LED color corresponds with the wire color, and them being on just means they are getting power. CC High Idle Simulation On to actually getting our hands dirty: Before we get started, I'm making a new acronym 'RYHST' (Remember Your Heat Shrink Tubing). First things first we need to be able to get to the cruise control servo's plug for soldering. You can also solder this in up top where the wires run along the firewall, but I liked doing down there where it's out of the way. To get to it I removed the drivers side battery, which also gives us more room for soldering. After removing a little electrical tape: Moment of no return.... Not really, Solder, Duct Tape and WD40 can fix about anything. Now for the diodes, I personally went with the 1N4007's as I had a pack of them, they're about as generic as they come. The only difference between these and the 1N4001-6 is the voltage rating, the larger the last number, the higher the voltage rating, for this system any of them will work. The way I figure it, if we're going to protect the PCM with these, might as well protect it all the way to 1000 Volts! When selecting a diode, anything over 100V should be fine. Now for amperage rating, each solenoid has a resistance of 44 ohms, we'll be feeding them 14.5 Volts, minus the voltage drop of the diodes which is ~.6V each, 14.5V-.6V-.6V = 13.3 Volts. Using that info we can calculate the amp draw, 13.3V/44Ω = .3 Amps. Now that is for a single solenoid, the diodes on pin 3 will be powering 2 solenoids (.6Amp) constantly, and all 3 (.9Amp) for a short period of time. These Diodes are rated for continues 1Amp. Normally I would shoot for a larger margin for error, however a higher rated diode will be physically bigger, and because we're soldering relatively thick wires straight to the diode it will have more heat dissipation abilities allowing it to handle more amperage. Voltage Rating - 100V minimum (overkill is good) - Check! Current Rating - 0.9 Amp Minimum - Check! Lastly, Make sure these are just a general diode, not a fancy zener diode or something - Check! Remember, the diodes are getting soldered to the PCM side of the plug. Now to reach into the cab for our switches we'll need a 4 wire cable, I picked a chunk of phone cable, even had good wire colors. Again, solder the diodes on. Also, remember diodes are directional, so notice the orientation of all the diodes we install. You can tell the orientation by the silver stripe, in the picture below, electrical flow can only go up, if it tries to go down the diodes will close and prevent it from doing so. RYHST and twist the two sets of diodes together. When soldering, once done, make sure there are no spikes that are sticking up waiting to puncture the heat shrink tubing. If you have a lot of issues with this, it may be a sign of using to much solder. Now solder that back to your plug (RYHST) Now the ground wire, just strip a portion of the insulation off, rap the new wire around it and apply solder. There is a small issue, doing it this way we can't get heat shrink tubing on the wire. Or maybe we can... Use a pick (or pocket knife) to pry this red plug out Now there are little fingers holding the pins in, again take your "pick" and pry the one up to get the pin out. Now for pin #3 (notice that the diodes are facing the opposite direction, that is because this is a power wire where as the others were ground). RYHST! All back together That's all ready, Time for the truck side, unfortunately I didn't get as many pictures as I would have liked, but they arn't really of use anyway, just a rats nest of wires everywhere. Just stick to the diagram above and you'll be fine! I'm going to be using 4 resisters instead of one... Why? It' simple, the design requires a 6 volt relay, so we must split the 12V in half. I measured the relays resistance and got 100 ohm's, so all we need is a 100 ohm resistor. However we need to make sure it is rated for our needs. we'll have half of 14 volts going through it, so 7 volts/100 ohms = .07 amps. .07 amps x 7 volts = .49 watts! So our resistor needs to be rated for at least 1/2 watt, 1 watt would be better. Easy Peizy, however I did not have one on hand... So my fix was to put four 470ohm 1/4watt resistors in parallel. What does that give us? The equivalent to one 117ohm 1watt resistor! That'll do donkey, that'll do. I had some clearance issues with the switches, so I had to cut the terminals short, but I was able to use some larger heat shrink tubing to protect them pretty well. Here's the rats nest all soldered up ready to go; Throw a little electrical tape at it and it's ready to call the dash it's home! And Installed:- Adjusting TPS & Throttle Linkage
THROTTLE POSITION SENSOR AUTOMATIC TRANSMISSION ONLY The throttle position sensor (TPS) is used on the diesel powered engine only when equipped with an automatic transmission. If the TPS is to be replaced on a diesel engine, it must be tested/ adjusted after replacement. REMOVAL (1) Disconnect the electrical connector on bottom of TPS (Fig. 34). (2) Remove the two TPS mounting bolts. (3) Remove the sensor from bracket. INSTALLATION (1) Position the TPS to the mounting bracket. The electrical connector should be facing downward. NOTE: The TPS is spring loaded. After positioning the TPS to its mounting bracket, rotate the TPS on the bracket in a counterclockwise direction until the two bolt holes align. (2) Install and tighten two bolts. (3) Connect the electrical connector on bottom of TPS. (4) Operate the throttle by hand to check for binding. (5) The TPS voltage must now be tested and (if necessary) adjusted. Refer to the following: Throttle Position Sensor Testing. THROTTLE POSITION SENSOR TESTING CAUTION: Before attempting to test the TPS, verify the linkage adjustment dimension (Fig. 35). This dimension MUST be 126.5 mm (5.0 inches) BEFORE testing. For linkage adjustment procedures, refer to Throttle Linkage Adjustment—Diesel Engine. This an be found in the Accelerator Pedal and Throttle Cable section of this group. CAUTION: Before testing the TPS, verify that the engine is set at correct low idle speed. Refer to Idle Speed Adjustment. (1) After confirming the correct linkage adjustment and idle speed, proceed to the following: (2) Attach a paper clip into the center terminal (Fig. 34) of the TPS electrical connector. Do not remove the connector from the TPS for this test. (3) Attach the positive lead of a voltmeter to this paper clip and the negative lead to a good ground. (4) Turn the ignition switch to the ON position. Do not start engine. (5) The voltage at the TPS center terminal should be 1.0 volt (± .2 volt) with linkage at idle position. Atwide open throttle (WOT), the output voltage must be 2.2-to-2.9 volts higher than at idle speed. I f voltage is not correct, proceed to adjusting linkage. (6) The linkage rod (Fig. 36) connecting the throttle lever to the fuel injection pump lever is adjustable. To prevent damage to the ends of linkage, attach locking-type pliers to the flat (Fig. 36) located on the linkage rod before loosening locknuts. (7) Loosen the right-hand-threaded nut (Fig. 36). (8) Loosen the left-hand-threaded nut (Fig. 36). (9) Slowly rotate the flat (Fig. 36) on the linkage rod (lengthen or shorten) to achieve 1.0 volt (± .2 volts) on the voltmeter with the linkage in the idle position. At wide open throttle (WOT), the output voltage must be 2.2-to-2.9 volts higher than at idle speed. DO NOT lengthen or shorten the linkage rod more than 1 mm from the dimension shown in (Fig. 35). I f voltage requirements cannot be met by linkage adjustment (125.6 to 127.6 mm), replace the TPS. (10) Tighten both nuts after adjustment. (11) With the engine OFF, operate the throttle from accelerator pedal and check for throttle lever action and binding. Be sure throttle lever stop is against the low idle speed screw after throttle is released. (12) Be sure of wide open throttle (WOT) when accelerator pedal is pressed to the floor. This is checked by observing throttle lever breakover position. Proceed to the following: (a) Key OFF and engine OFF for this test. (b) Two people are needed for this test. From inside of the vehicle, press the accelerator pedal about half-way to the floor. Movement of both the throttle lever and throttle lever-to-injection pump lever linkage rod (Fig. 36) should be observed. (c) Continue to press the accelerator pedal to the floor. I f throttle lever breakover is operating correctly, the throttle lever-to- injection pump lever linkage rod should have stopped moving while the throttle lever continues to move towards the rear of vehicle. (13) Again, check and verify low idle speed. Adjust if necessary. Fig. 34 Throttle Position Sensor—Diesel Fig. 35 Linkage Measurement—Diesel Fig. 36 Throttle Lever Linkage Adjustment—Diesel- When was the last time you lifted the hood?
I guess you could say that. I used it to jump another rig and haven't put it back yet. haha- From 24 valve to 12 valve
You got started with these monsters about the same way I did. Truck wasn't running right, ended up pulling the tank which was about 1/2 full. Finally found my air leak, fixed that. Ran it for a while, checked fuel pressure, 2 psi, OFV fixed that. Turned out to be a really good engine if you feed it good fuel. That's a Nice Welder! Can't wait to see how it goes. I got a stick welder that I'm getting better with, plus an old mig "miller sidekick". It doesn't run quite right, but can put out some decent welds if you manipulate it just right. I recently used it to redo the front bumper/grille/rack on one of the Honda rancher 350's because we tore it off. haha On the camera, I got a used one off eBay recently, it was $40 and does everything I need it to, you can get better, but for taking pictures/videos of truck parts, being shoved into a jungle of wires, hoses, and cables... It does fine.- New member introduction/reccomended maintenance
On the valve lash, I degree'd the cam in the 96, it was cool to see the difference a couple thou difference in valve lash makes. I'll probably be running .006"/.014" once I get a chance to set them.- When was the last time you lifted the hood?
Today. My drivers side battery is MIA.- Lift pump leak
Some of the older designs had a O-ring you could replace, but I don't think yours will. If yours looks like this, replacement is your best option. If you don't mind it being yellow. http://www.ebay.com/itm/NEW-TAKE-OFF-FUEL-LIFT-PUMP-4BT-390-CUMMINS-PART-3936316-/301747944699?hash=item4641943cfb:g:ZwkAAOxydlFS5M5- And yes, it has the possibility of leaking air in as well. - From 24 valve to 12 valve