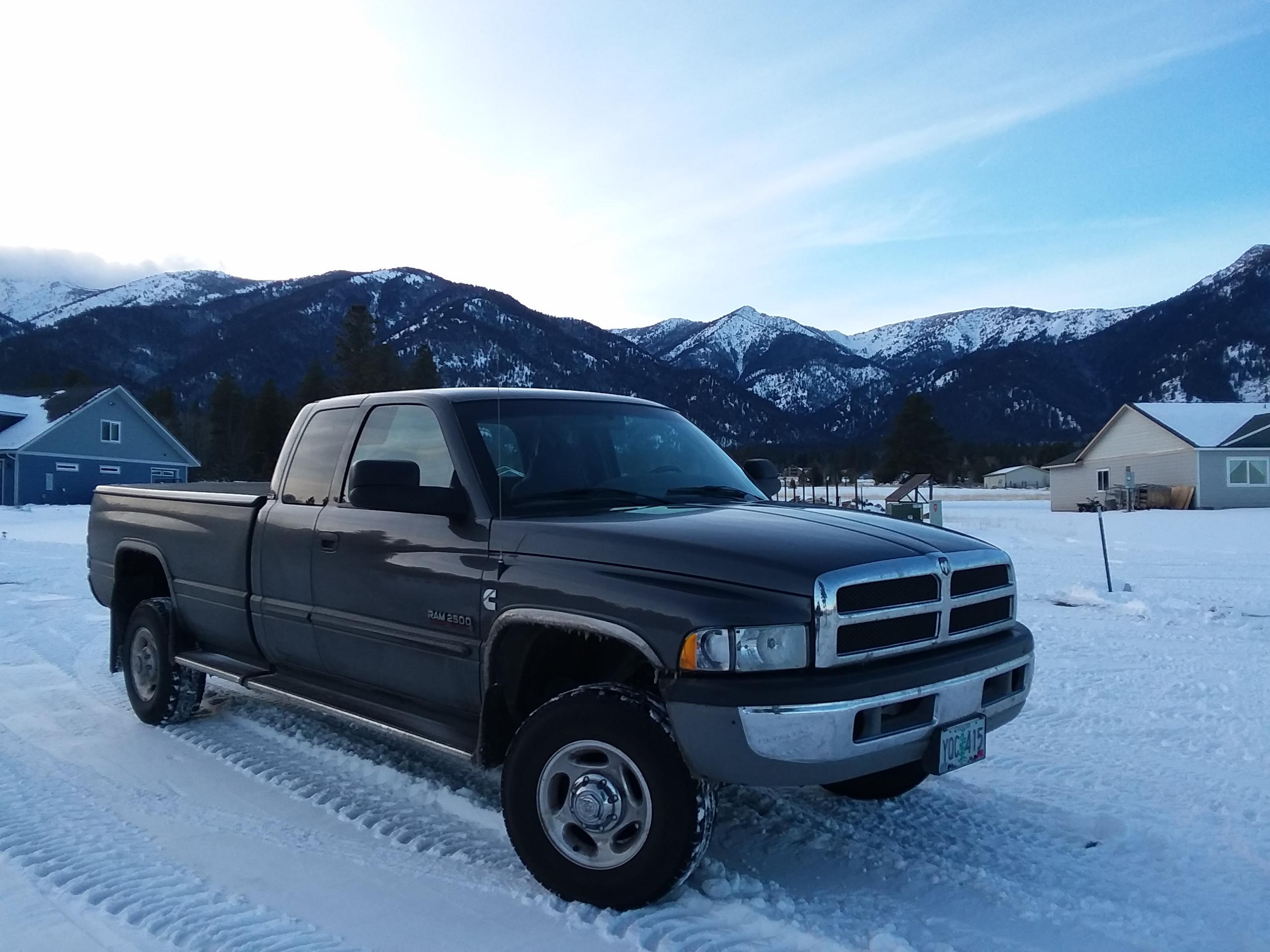
Everything posted by Tractorman
-
2nd Gen Cummins heater temp differences between trucks
My mom lived in a cabin north of the Arctic Circle for years. She used a single raisin for mouse bait. She had it down - one raisin used over and over will take out many mice for several weeks. The mouse has to tug fairly hard on the raisin and then..., well, you know. Sometimes, because of all the commotion, you would have to search for the raisin so that you could reuse it. - John
-
2nd Gen Cummins heater temp differences between trucks
I think you won. - John
-
Truck runs great but P0252 P0253
From my 2002 FSM - no P0252 code shown. Can you confirm that you are seeing a P0252 code? - John When you say "truck seems to run great", does that mean you have driven the truck and the engine performs normal? - John
-
Not starting straight away every time
Thanks for the photos. The break looks like it is located in an almost impossible place to inspect. Who was the manufacturer? Do you know how long and how many miles it had been installed on your truck? It is amazing how fortunate you were when that event happened. - John
-
2nd Gen Cummins heater temp differences between trucks
"The DIode" must be like "The Surgeon General". It's just there, somewhere. - John
-
Not starting straight away every time
Holy cow! You were very fortunate with the end results. Glad to hear that you and no one else got hurt. So, was it the ball joint that joined the Pitman arm to the drag link? I would like to see a photo of that failure. Always like to learn from experiences like you had. - John
-
Curse of the 5th gear nut!
I have never owned a vehicle with an NV4500. But, with what I have learned about the NV4500, if I would have owned one that failed, I would have immediately replaced it with a NV5600. In my opinion the NV4500 transmission is too light duty for a high torque, low rpm Cummins diesel engine. There is no fix. The nut loosens or the shaft breaks because the nut loses its clamping force, It loses its clamping force because it is under-designed for the clamp load. Locktite / set screws / Loctited set screws do NOT maintain clamping force. Welding the nut will cause a properly torqued nut to immediately reduce its clamping force. For all of these mentioned conditions, when the clamping force is lost the nut will always come loose or the shaft will break. Every time. I am sorry you are having to go through this. - John
-
Not starting straight away every time
Well, I'll be gobsmacked! Isn't it rather obvious what is the matter with your truck? The ECM on your truck not only communicates with various sensors and the VP44, but also communicates with diesel truck forums, so it knows what you are thinking and saying about your truck at all times. And you have been saying plenty. Things like, "I've bought a AM General M50A2 so pretty sure the ram is going...". Wow!! How is the ECM going to take that profound statement? Maybe give you a little trouble next time you try to start the engine? Duh! I always wanted to use that word "gobsmacked". - John
-
Now vs Later?
I am in a similar situation. I am at 382,000 miles on my truck. New RV275 injectors at 303,000 miles. Rebuilt VP44 at 87,000 miles, currently 295,000 miles on the replacement VP44 with no issues. Turbo is still original. Personally, I would never replace injectors at 100,000 miles, but at 300,000 miles your injectors have served you well, so it is time to replace them. On my truck before replacing injectors at 303,000 miles, the engine still idled smooth, power was good and fuel economy was good - probably like yours. I plan on running my VP44 until I start seeing something that warrants replacing it. Same goes for the turbo. Usually, symptoms will show if a problem is starts occurring with either the VP44 or turbo - not likely to leave you stranded. And, the turbo is easy to inspect for any rubbing that may begin to occur. I have plenty of oil leaks to find and I am just going to tackle them one by one. I have already replaced the tappet cover gasket - good to follow MoparMan's advice regarding no sealants. As far as the head gasket, I will wait until I can schedule some down time, so I am not rushed. A couple of years ago when I was performing fuel return flow tests from the VP44, I installed a fuel line bypass (with a one-way check valve) around the frame-mounted lift pump. After testing was completed, I kept that bypass in place in case of a future lift pump failure. With the bypass in operation I would still be able to drive the truck home without a functional e lift pump. - John
-
Just out of curiosity
Now, for sure, he will never come back. - John
-
Just out of curiosity
W-T is doing okay. He is going through long processes of collecting insurance money and other resources so he can rebuild to some degree. At this point, I believe he wants to stay in Paradise if everything works out. As far as "chicken man" (DRipley) goes, I think you guys picked on him so much that it caused his disappearance. I only picked on him a little. - John
-
Website is going to get busy again.
If it was a color photo, you would see the blue hair. - John
-
AM General M50 6x6
-
AM General M50 6x6
Well, it looks like you have your work cut out for you. If you are going to go to the trouble of taking the truck to London, you should install a large green environmental decal that says, "FLex Fuel Vehicle" Then, in smaller hard to read print, "Meets 1959 Emissions" That way you won't feel bad making all those people mad. One important thing to check is whether you have a hydraulic braking system with a single or a dual master cylinder. Here, in the U.S., dual master cylinders didn't come out until around 1965. Driving with an aged single master cylinder braking system could be inviting disaster. By the way, -40°C is the same as -40°F - but, you probably already knew that. - John
-
Weird rough idle
All alternator wires need to be connected for the AC voltage test. The test is not valid if the alternator is not working. I suggested disconnecting the alternator output wire to check if your rough idle disappears - not to check for AC voltage. The factory installed in-tank lift pump is fine - I had one installed under warranty for over 150,000 miles. It was still working fine when I replaced it with a frame-mounted lift pump for easier access. If you end up replacing the VP44, be sure to purchase one that gets a new (not rebuilt) PSG and that the PSG is calibrated to the pump on Bosch 815 test stand. Don't know the quality of your current VP44, but it may be sub-standard, especially considering the 1688 code set. I do not recommend two lift pumps in series. It will work fine, but it complicates the system and there is no benefit. Plus, it is another component that can fail. I would either continue to use the in-tank lift pump or remove it and install a frame-mounted lift pump. I think the frame-mounted lift pump is the best option because it becomes a pusher pump and its location is easy to service. - John
-
AM General M50 6x6
Great pictures. When I was living in Alaska in the early 60's, my dad had a 4x4 version of that truck. He just ran it on gasoline. But, I do remember late one November it was about -40° (Celsius or Fahrenheit, doesn't matter) and the truck hadn't been run for a couple of weeks. Standard procedure - take battery into house for an overnight warmup, build a small bonfire underneath the engine for about three hours to liquify the oil (no mulit-viscosity oil back then). Wait for the outside temperature to warm to - 30°F and then start the engine. Works great. Do you know what year your truck is? - John
-
Weird rough idle
When it begins to act up, turn off the engine and disconnect the alternator output cable. Restart the truck to see if the problem is still there. You can perform an AC voltage test on the alternator output with everything connected and engine idling. The test should be done after the grid heaters have finished post-cycling and there are no heavy electrical loads present. The reading should be around .05 volts AC or less. Double check your work regarding the W-T ground wiring mod. Make sure all connection points are clean and tight. Make sure you didn't miss a ground connection. How is the condition of the cross-over cable? - John
-
Weird rough idle
You are not the only one to have this problem after installing a circuit breaker. Likely that you have a weak 150 circuit breaker. Prior to the W-T ground wiring mod, there was a 145 amp heavy duty fuse in the distribution center. Try a better quality 150 amp circuit breaker or fuse. I use a 150 amp fuse and I have never had a problem, but I also have a manual grid heater switch control, which means there is no post-cycling of the grid heaters - a lot less work for the alternator after the engine is running. The 1688 code is more serious: - John
-
She's dead. And I'm done with it.
@Max Tune, I really appreciate your response. You ask many good questions. The VP44 fuel system is made up of several series and parallel circuits, especially inside the VP44. That's where the complexity begins. Over the years many observations and decisions about how the VP44 works and how it is cooled have been based upon the only two pressures readings available - lift pump pressure and overflow valve pressure (14 psi). Nothing has been based on flow, mainly because no one really seems to know what the flow is in the various parts of the circuit. The 14 psi overflow valve ensures an even distribution of charge pressure to the fill chamber of the high pressure pump (radial piston design) when the fuel solenoid valve is de-energized. The 14 psi is also a low enough pressure that it easily accommodates returning fuel back to the tank without adding excessive heat to the fuel. This is where some of the confusion lies. The workings of the inside of the VP44 are no different than a sophisticated hydraulic system. All hydraulic systems have calibrated internal leakage for lubrication for every component used inside the system. The inside of the VP44 is no different - it just uses fuel instead of hydraulic oil. Some of those internal components are: positive displacement vane pump, timing piston, timing piston control valve, high pressure injection pump, etc. All of those components are designed with a specific amount of internal leakage for lubrication. With that said, if the VP44 pump is not turning and lift pump pressure is applied, flow will eventually get to the overflow valve. BUT, the overflow valve will not open. The fuel will exit through the tiny orifice just below the overflow valve, acting as a vent. There will only be a continuous dribble. The dribble will be smaller if there is only 10 psi lift pump pressure. It will be larger if there is 20 psi lift pump pressure, BUT, AGAIN, the overflow valve will not open. The most important thing to note here is, the fuel is NOT being pushed through the internal vane pump. It is leaking through all of the internal components at the calibrated leakage rate. The total leakage rate flow is what will be passing through the orifice vent. Knowing how this works will help in understanding how air is vented from the VP44 after a fuel filter change. This part is the hardest part for me to explain, partly because I don't fully understand it myself and partly because it is complex. Refer to the photo below as I try to get through this. You will note that when the fuel first enters the VP44, it goes right to the inlet of the internal vane pump (Bosch calls this pump the "feed pump"). Note that the fuel leaving the feed pump has three paths to take. All of these path see the regulated pressure. 1. directly to the feed pump pressure regulator (120 psi approximately) 2. to the accumulator (to the far right (rectangle symbol shown with spring) 3. to the timing piston control valve and timing piston (to the right and down) Now focus on the path after the fuel leaves the accumulator. Here's is where things get complicated. The following is my interpretation of how this system works. The fuel has to pass through the rotor shaft (a small passageway) in order to get to the fill chamber of the high pressure pump. This restriction is why the feed pump pressure falls considerably at this location and the fuel will be subjected to the 14 psi overflow valve pressure as the fuel enters the fill chamber when the fuel solenoid is de-energized. As soon as the fuel solenoid valve energizes, the fill chamber and overflow valve will be isolated from the feed pump / accumulator circuit. When the fuel solenoid de-energizes, the accumulator will absorb the energy left over from high pressure injection and the 14 psi overflow valve will ensure a uniform fill pressure for the next event. Feel free to pick this apart. - John
-
She's dead. And I'm done with it.
I will never know. The VP44 was replaced in June of 2005 (at 87,000 miles) under warranty. At that time I didn't know much about the VP44 fuel system, so I never asked any questions about the pump. Ironically, initially I was disappointed that it was a re-manufactured pump. I wanted a new one. However, over the next few months I learned a lot about the VP44 pump and about some of the inferior components inside the pump. It was then I was glad to have received a re-manufactured pump, mainly because of the many improvements done as time went on. As far as filter, I just use the stock filter housing and usually a Napa filter. I have added a 140 micron strainer at the suction of the frame-mounted lift pump. - John
-
She's dead. And I'm done with it.
"The lift pump has no say in when the overflow valve is open." I stand behind that statement. Rarely, does anyone talk about the role of the internal vane pump inside the VP44. Its role is far more important than the role of the lift pump. The only job required of the lift is to always provide a positive pressure at the VP44 injection pump inlet under all operating conditions. The role of the internal vane pump is to supply a flow of fuel (based on engine rpm) to all internal injection pump working components, to the injectors, and to the fuel tank via flowing fuel through the 14 psi overflow valve. The minimum pressure for the internal vane pump regulating valve is 120 psi. The internal vane pump is a fixed displacement pump. When a fixed displacement pump is operating, it is ALWAYS displacing the SAME volume of liquid at a specific rpm, regardless of whether its inlet is being charged with a lift pump, or it is drawing directly from a fuel tank. This volume cannot be changed without changing the rpm of the engine. It's physically impossible. All fuel must pass through the internal vane pump; there is no path around it. The rpm of the vane pump determines the volume of fuel flow. As soon as the engine starts and idles, fuel immediately begins to flow at about 18 gph through the 14 psi overflow valve, regardless of lift pump pressure. As engine rpm is increased, fuel flow through the overflow valve increases immediately. I disagree. If an engine at idle is sending 18 gph through the overflow valve (returning to tank) and the injectors are consuming 1 gph, then 19 gph are entering the inlet of the VP44's internal vane pump, regardless of lift pump pressure. If a 100 gph lift pump is providing fuel to the VP44 inlet, this means that 81 gph are being returned to the inlet of the lift pump (or to the fuel tank from the lift pump, if a dedicated return line is being used), and the other 19 gph are flowing into the VP44 injection pump. If a 150 gph lift pump is being used, then 131 gph are being returned from the lift pump and the same 19 gph are flowing into the VP44 injection pump. In both cases , fuel volume flowing into the VP44, fuel volume consumed by the injectors, and fuel volume returning to the fuel tank via the overflow valve remain unchanged. Back in April of 2001, some members of the TDR performed some extensive testing with the use of a flow meter in the fuel return line circuit from the VP44. Many tests were done - all tests were done at engine idle, cruising speed, and wide open throttle. Tests were done with different lift pumps and different tuning levels. EVERY test showed the same results - 18 gph at idle, 24 gph at cruising speed, 30 gph at wide open throttle. One of the tests even had 0 psi lift pump pressure at wide open throttle, but the fuel return flow remained unchanged. By the way, the maximum lift pump pressure recorded for ALL of the testing was 11 psi - and that was at idle. Three years ago I performed some fuel return flow tests on my truck. I didn't have access to a flow meter, so I used a container that showed graduated volume measurements. At idle ....... lift pump pressure 12 psi, return flow from VP44 - 19 gph A 2000 rpm.... lift pump pressure 8 psi, return flow from VP44 - 28 gph I repeated the tesst with VP44 pulling directly from the fuel tank (no lift pump). Fuel return flows were exactly the same. I even drove a 28 mile round trip to town without the lift pump in operation. No performance issues whatsoever. My replacement VP44 has now logged just over 294,000 miles - all of the miles with 12 psi or less lift pump pressure. Most of the miles with less than 6 psi. So, yes, I stand behind what I am saying here. I don't expect others to accept this information at face value. But, so far, I have yet to hear of any documentation that shows that lift pump pressure must always be over 14 psi in order for fuel to return to the tank from the VP44. - John
-
Power Steering Pump bad after flush?
Maybe this will help. The photo below shows a simplified drawing of a recirculating ball type power steering gearbox. Your objective is to achieve zero clearance with the slightest preload between the ball nut rack and the sector gear when the steering gearbox is centered (tires in straight ahead position). Normally, this adjustment is done on a work bench using an inch-pound torque wrench, so there is no friction interference from other steering components. Note the adjusting screw and lock nut on top of the Pitman shaft (also called sector shaft). This is what you are adjusting. Raising the Pitman shaft increases clearance - lowering decreases clearance. Because you are making this adjustment in the vehicle, it is better to have a very slight clearance than no clearance. I use a different method than Moparman. I note the position of the adjusting screw before loosening the jam nut. I loosen the jam nut and then tighten the screw 1/8 turn (clockwise from top view). I tighten the jam nut. Without starting the engine, I just barely move the steering wheel left and right - there should be virtually no friction. I then test drive the truck. I will continue to make 1/8 turn adjustments until I think it is right. If, when you are driving straight ahead, the steering becomes sticky (this can be very subtle), then the adjustment is too tight. Back off the adjusting screw 1/8 - 1/4 turn. Again, better too loose than too tight. Hope this helps. - John
-
Power Steering Pump bad after flush?
The front tires can be on the ground. What does matter is that the tires must be pointed straight ahead with the steering wheel centered. This is the position where the steering gear lash clearance is the tightest. This is important. I will let @Mopar1973Mananswer your first question. - John
-
P0121, P0237, P0234, P1689,p0236 all at once.
Wow! Same thing happened to me, and I have a manual transmission! What are the odds?! - John
-
P0121, P0237, P0234, P1689,p0236 all at once.
Glad to hearing everything is working properly and no codes. Would have been interesting to know if the W-T ground wiring mod would have corrected the old alternator high AC voltage. - John