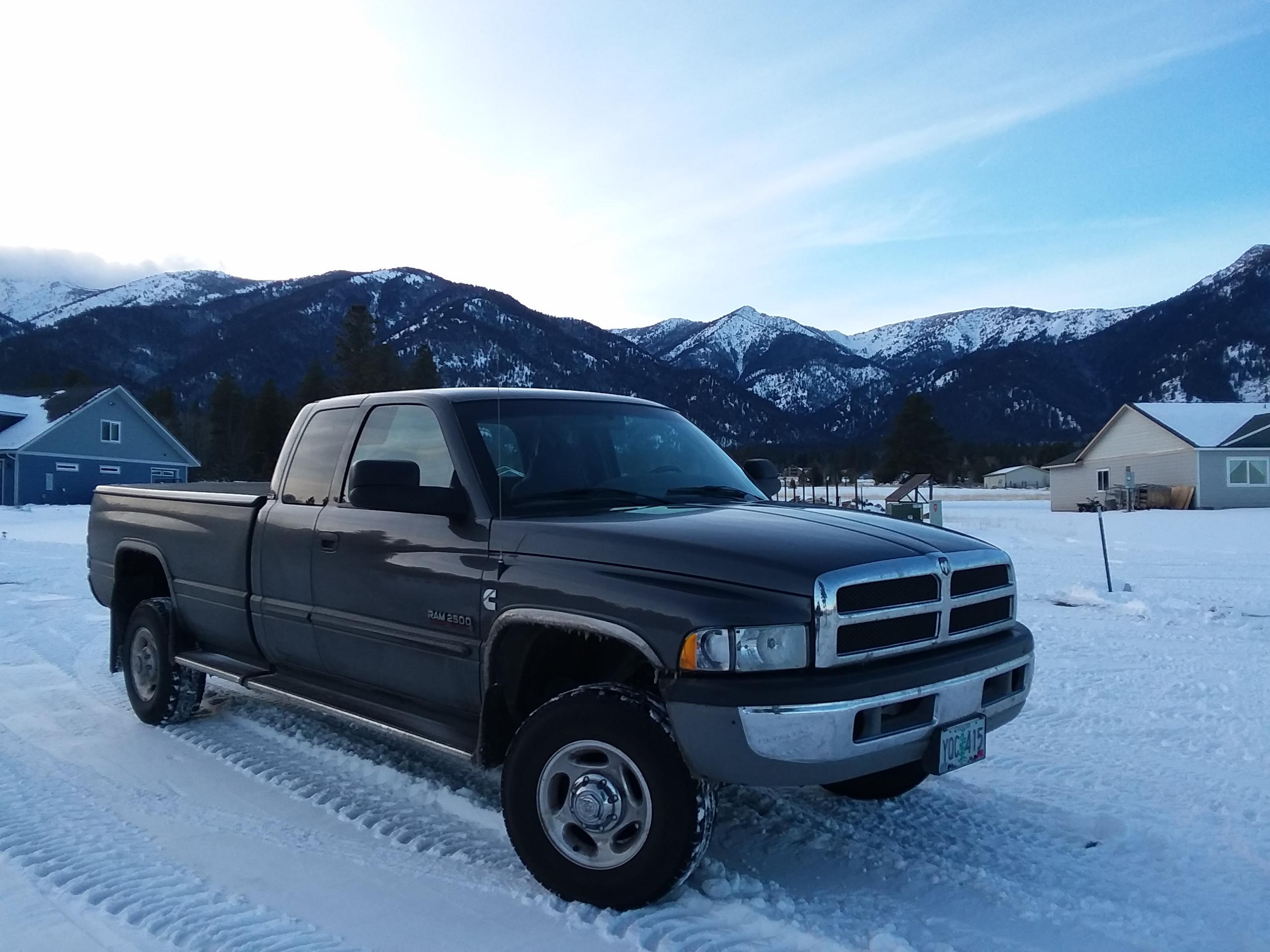
Everything posted by Tractorman
-
A/c compressor help
I would not assume anything. Did you inspect the first compressor that was suspect for failure? Was there any metal debris present at the outlet port? It would probably be best to remove and inspect this compressor for damage before deciding your next step. Earlier I asked if the engine cooling fan was turning (assuming it is an engine fan that pulls air across the condenser). This answer is important. If there is no air flowing across the condenser, then compressor output pressure can rise rapidly to a destructive level and will / may activate the the pressure relief valve. Without gauges (especially a high pressure gauge) you are only guessing at what is going on in the system when the compressor is running. I would definitely install quality gauges on both the low and high pressure ports before doing any further testing. - John
-
A/c compressor help
What were the high and low pressure readings when the failure occurred the first time? the second time? What was the ambient temperature for each time? I am assuming there is an engine clutch fan. Was it turning? From information you have posted, it seems like the system pressure is excessive on the high side. - John
-
Serpentine Drive Belt - What is the best
I always use my old belt as the backup because I know it works. On rare occasions a new belt can fail or come off right away, OR it might even be the wrong belt. So, if one waits for the old belt to fail and then replaces it with the new "backup" belt and Murphy's Law strikes - well, that's what Murphy's Law does, here you will be sitting alongside the road..., - John
-
Dodge 2500 OEM Hitch Receiver Failure
About a month ago I experienced a hitch receiver failure on my 2002 2500 4WD Long Bed truck equipped with a Cummins engine and a manual 6 spd transmission. Although I have inspected the hitch many times over the years, I overlooked a critical area during those inspections. The hitch-to-frame fasteners (four on each side) were always tight. However, a couple of inches away from the fasteners (at the first 90 bend in the hitch receiver flange) is where the separation occurred. It started on the left rear side of the hitch receiver (a long time ago) and continued forward until the hitch receiver dropped away from the truck frame as I was pulling off to the side the road. Only the right side of the hitch receiver stayed connected to the frame while I finished pulling off to the side of the road. There are several things that attributed to this hitch receiver failure - most of which is on me. Closer detailed hitch inspections and using the hitch within its rated capacity would have gone a long way toward this event never happening. The OEM hitch receiver is rated as follows (a sticker is located on the hitch receiver). These are maximum ratings: With Weight Distribution …..... 10,000 lbs trailer weight, 1,000 lbs tongue weight Weight Carrying …………………. 5,000 lbs trailer weight, 500 lbs tongue weight I never paid attention to the Weight Carrying maximum - a serious oversight. The first few years of the truck’s life I occasionally hauled a 6,000 lb equipment trailer and a 10,000 lb dump trailer without the use of a weight distribution hitch. Since 2013, I have always used a weight distribution hitch. The gross combined weight when the hitch receiver failure occurred was just under 20,000 lbs with 11,300 lbs on the trailer. The weight on the tongue was set to 1,200 lbs while loading the trailer. The next day I removed the hitch receiver and laid it out on the tailgate. In the photo below you can see the broken flanges (all on the left side) and one broken mounting flange on the right side. On the left side only one mounting tab showed a fresh tear, the rest had rust on them for some time. The right rear tab was also rusted, so it had been broken for a long time as well. This incident prompted me research hitch receiver ratings and hitch terminology in general. I was not impressed with the research results. Basically, what I found was that OEM hitch receivers on Dodge Ram 2500 trucks up to around year 2013 are rated as follows. These are maximum ratings: With Weight Distribution …..... 12,000 lbs trailer weight, 1,200 lbs tongue weight Weight Carrying …………………. 5,000 lbs trailer weight, 500 lbs tongue weight My neighbor and I used his 2011 Dodge Ram Cummins 2500 to rescue my trailer on top of the pass. We couldn’t use my weight distribution hitch because his hitch pin was frozen in place. It wasn’t until the next day that I realized that we had seriously abused his hitch receiver (maximum weight carrying - 5,000 lbs, maximum tongue weight - 500 lbs). However, after close inspection, all is well. One thing that sticks with me through all of this is that there is no safety margin with the OEM hitch receiver ratings on the years of trucks mentioned. The sticker on the hitch receiver is the only place where I found weight carrying information on my truck. There was no sticker on my neighbor’s 2011 truck. My owner’s manual had information about maximum load capacities with use of a weight distribution hitch, but no weight carrying information. The owner’s manual for the 2011 truck had no towing information and referred to the “ramtrucks.com” site for towing information. I have since installed a Curt 16,000 lb bolt-in hitch receiver which allows for 16,000 lbs towing and 2,400 lbs weight carrying (with or without weight distribution). May be a bit overkill since my trailer load maximum weights won’t change, but there certainly will be a greater margin of safety. My neighbor has ordered a 15,000 lb hitch receiver for his truck. Just thought I would share my towing experience and maybe trigger some hitch receiver inspections on some older trucks. - John
-
Serpentine Drive Belt - What is the best
The last serpentine belt I installed was in 2014, approximately 170,000 miles ago. Still on the truck and wearing well. Never has made any noise. Can't tell you the brand, but it came from Geno's. - John
-
Hilary's coming to your place Mike...
Rain continues - up to 1.04 inches now. Moparman should be getting some of this rain. Our average monthly rainfall here for August is 0.75 inches. We were already well over an inch of rain before this morning's rainfall started. - John
-
Hilary's coming to your place Mike...
Rain started about 5:15 am. Received 0.61 inches so far. The forecast is for 1 to 2 inches today. - John This is what radar has looked like for the last 4 hours. Rainfall up to 0.74 inches now. - John
-
Hilary's coming to your place Mike...
It's all about percentages. You should take precautions. Your rainfall and wind speed could double or triple on a moment's notice. You need to be prepared. - John
-
Hilary's coming to your place Mike...
Showing signs of arrival here in Baker City. Two thunderstorms this afternoon and evening with .14 inches of rain. Flood watches in effect Sunday and Monday. - John
-
To display the Hour Meter on your 3rd Generation Cummins
Does that work for all 3rd generation trucks?
-
New A/C Compressor squeaking
Agree with @Max Tuneabout either of the valves leaking, especially the high pressure valve. Spray with soapy water to detect a leak and then blow the fitting dry with compressed air before installing the protective cap. Rapid compressor cycling strongly suggests a refrigerant leak. When you get back to the truck, don't forget to test the serpentine belt noise with WD40. - John
-
Fat tire e bike and bike rack 48 inches from the hitch...
My concern would not be the hitch rating. It would be the unweighting of the front axle. Your modified load may be 4 feet behind the hitch, but it is closer to 7 feet behind the rear axle. The rear axle is the fulcrum. This is why weighing the truck before and after the modification is important. Need to ensure that the proper weight is on the front axle. - John
-
Fat tire e bike and bike rack 48 inches from the hitch...
I have a feeling that he has considered that option, but doesn't want the bike mounted there. - John
-
Fat tire e bike and bike rack 48 inches from the hitch...
@JAG1, if you haven't done so already, I would independently weigh the front axle and rear axle of your truck empty. Record the weights and keep them somewhere accessible. Then load your camper and gear and weigh the truck again. Do this before you make any modifications to the rear of the truck / camper. If the front axle is too light / heavy, then redistribute your gear to get the front axle weight where it should be. If / when you make your modification, then re-weigh the truck with the camper and gear loaded. Figure out where to place gear to get the proper amount of weight back onto the front axle. Years ago, I used to own a slide-in truck camper. It weighed approximately 3,500 lbs with water, propane, and gear. My truck empty with driver and tonneau cover: FA - 4,400 lbs RA - 3,050 lbs 7,450 lbs total Truck with slide-in camper, water, propane, gear, and two people: FA - 4,850 lbs RA - 6,150 lbs 11,000 lbs total What was important to me was ensuring that I gained some weight on the front axle when the camper and gear were loaded. In my case the front axle gained 450 lbs. The gross weight rating for the front axle is 5,200 lbs. The 4,850 lbs on the front axle worked well for me and fell in about mid-way between the empty weight and the gross weight rating of the axle. Weighing the truck before and after is the only way to know how the weight is distributed on the axles. This is especially important to know for high center of gravity loads. - John
-
New A/C Compressor squeaking
Not sure of the belt brand, but I did buy it from Geno's in October of 2014. That belt has currently logged about 165,000 miles. Just inspected it and all of the pulleys about three days ago. All in good condition and the belt is still quiet. - John
-
New A/C Compressor squeaking
This condition indicates to me that the problem is not the compressor. There are two different bearings sets involved with the compressor / clutch assembly. When the compressor clutch is disengaged, the only bearing that is rotating is the clutch to input shaft bearing. When the compressor clutch is engaged the clutch to input shaft bearing stops rotating and the front bearing inside the compressor begins rotating. If one of these bearing is faulty, then the noise should disappear either when the compressor is engaged or disengaged. It sounds to me that the noise is coming from another component or the belt. The noise pitch changes when the AC compressor cycles on and off because the belt load is changed. Since the noise is also occurring at idle, I would spray some WD-40 onto the belt (carefully) while the engine is running. If the noise does not change significantly or go completely away, then I would think the belt is not the problem, but a belt driven component is the problem. In my experience over the years, belts can make horrendous noises that would make you look elsewhere, especially if any coolant has dripped onto the belt. I also think that it is worth removing the belt and try rotating and moving every pulley side-to-side and forward / backward to observe anything out of the ordinary. - John
-
New A/C Compressor squeaking
More questions than answers. Is the noise EXACTLY the same as before? How far is the drive home? 2 miles..., 30 miles? Did the noise occur right away? What are the engine rpms when the noise occurs? Does the noise still occur when the AC compressor is not running? When you had the serpentine belt removed, did you check the condition of the other pulleys? How about the belt condition? These details are needed to help eliminate possible sources of the noise. - John
-
code 2509 2127
P2509 ECM/PCM Power Input Signal Intermittent P2127 Pedal Validation Switch 2 Low I would stop changing parts. You may have good intentions, but new problems could easily be introduced and make it even more difficult to diagnose. I would start with P2509 code. If power to the ECM/PCM is intermittent (not sure if there is a PCM on a 2003), this could easily be the source of your problem. You have access to wiring diagrams on this site, if you don't have a factory service manual. The ECM/PCM power source needs to confirmed that it is in good working order. Double check that all positive and negative wires were reconnected when you installed the new batteries. - John
-
AC drain issues
Here's another tidbit of information. As has been noted, there is just a piece of straight pipe sticking out into the engine compartment. A few years ago my passenger side carpet was getting wet. Turned out that the seal between the HVAC housing and engine firewall had weathered enough to allow water leaving the end of the pipe to find a path back into the cabin. I inserted a rubber hose elbow on the end pipe - problem resolved. It took me awhile to figure out the problem as we were on vacation with our travel trailer east of the Rockies. Since it was raining every other day or so, I first thought it was rain water leaking into the cabin. - John
-
Tranny swap
I agree with @Mopar1973Man. Way too many gears that will never be used. Awhile back, I made a chart to compare some manual transmissions. I added the Eaton Fuller RTO 6610 (10 speed Overdrive) transmission. I think it could be a good option. 660 lb/ft input torque and transmission weighs in at 359 lbs. Very uniform close ratio transmission. - John
-
Tranny swap
The 1.24:1 is still an underdrive in 8th gear on the 613 transmission. The 613 had two choices - direct drive 1:1 or 1.24:1. No overdrive. - John
-
2006 Dodge - Thor - Track Bar issues
Good catch on your part. I think this happens more frequently than is ever mentioned. This type of bushing contains two parts. They each have their purpose. One part is a flexible bushing that is intended to flex and absorb energy. The other part is an internal steel sleeve that is slightly wider than the bushing. Its purpose is to ensure the assembly can be clamped with enough force between two steel ears that the steel sleeve will never move. This type of bushing is also used for leaf spring hangers and shackles as well as some shock absorber mounts. Proper torque for the fastener may be set correctly, but this does not guarantee that the ears (usually welded onto the frame or axle) are bending enough to reach their full clamping force on the inner steel sleeve of the bushing. For this reason I usually torque the fastener to a higher value to ensure good clamping force. I follow up with an inspection after a couple of thousand miles to check for tightness. @Mopar1973Man, since the track bar connection on your truck has been loose for awhile, the steel sleeve and / or ear mounts will wear some, possibly removing material. This will make it harder to attain the clamping force when the fastener is re-tightened. I recommend inspecting the connection again after a few hundred miles. - John
-
Tranny swap
@David E, I can't help you regarding the adapter, but I am interested in your project. Would that Roadranger be an 8 speed? I always thought that this transmission would be an excellent choice for a Dodge Cummins powered truck. - John
-
Anyone ever wonder what you would do if you find squatters in your house?
Can you give details as to what transpired here? Example: was the home unoccupied for a few months first? Or, were the owners gone for a couple of weeks (vacation)? Or, did the owners go to the grocery store and return to find people occupying their house? Could make a difference on how to prepare by knowing what you are up against. - John
-
VP 44 home made brains part 2 getting real now
@Great work!, you are a talented man!! I couldn't even begin to take on that task. - John