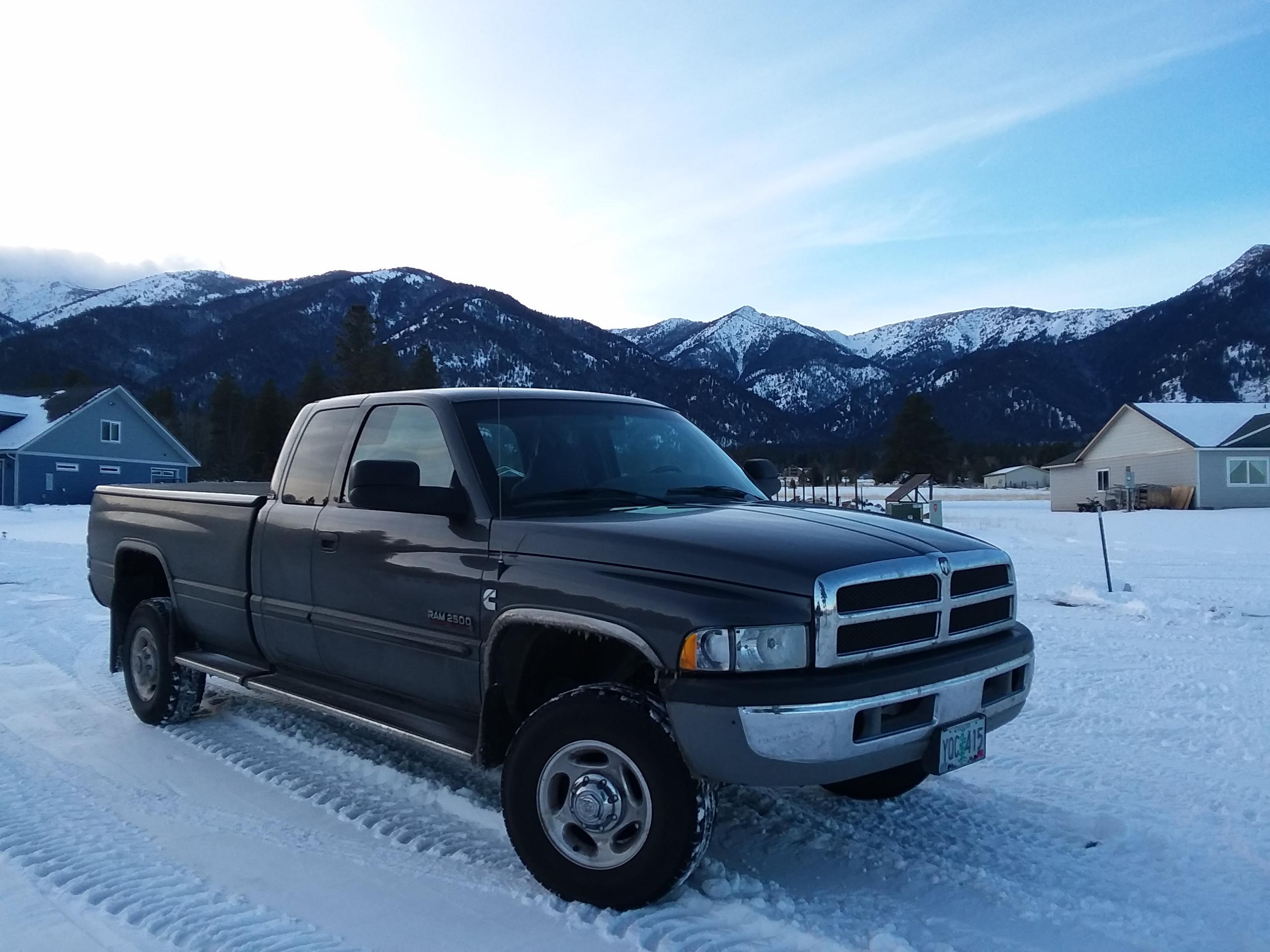
Everything posted by Tractorman
-
Rear Pinion Seal (re-lash?)
Possibly a 1" drive breaker bar accompanied with a cheater and the proper size socket. Of course, a large pipe wrench will also be needed to hold the yoke from turning. Torque could be guesstimated by calculating the lever length and calculating the force applied in pounds. - John
-
Rear Pinion Seal (re-lash?)
I just reviewed the FSM for pinion seal replacement and rear wheel bearing adjustment. * Pinion Seal * Rear of truck on jack stands. Remove rear wheels and brake pads. Park brake released Use inch-pound torque wrench and record torque required to turn the pinion nut 3 revolutions. * After installing new seal, tighten pinion nut to 440 ft/lbs. Use inch-pound torque wrench and record torque required to turn the pinion nut 3 revolutions. Compare to previous readings. Should be the same or slightly higher (new seal). So, that is technically how it should be done. * Rear Wheel Bearing Adjustment * tighten wheel bearing nut to 120-140 ft/lbs, then back off 1/8 turn. - John
-
Rear Pinion Seal (re-lash?)
Yes, it sounds like his experience has been with 1/2 ton vehicles. I don't think he's had experience with full-floating axles. I am familiar with the C-clips he is talking about in order to pull some semi-floating axles. Also, many of those differentials used crush sleeves for setting the torque on the pinion bearing. Tightening the pinion nut does not set a preload on the pinion bearing on the differentials on our trucks. I think the pinion nut has a torque of about 450 ft/lbs. - John
-
Rear Pinion Seal (re-lash?)
I replaced the pinion seal on my truck at 206,000 miles. I couldn't get the nut off. Broke big sockets trying. I took the truck to a recommended shop and it took two of us over an hour to get the nut off. After installing the new seal, the nut was re-tightened with a 3/4 inch drive air gun - no torque wrench. That was over 160,000 miles ago. No leaks or problems. - John
-
endless NV5600 problems.
Actually, I use a compromise between a single-clutch action and a double-clutch action that gives the performance and benefits of a double-clutch action. Performing a single-clutch action during a shift is easier and works well with small and light duty transmissions, but, the synchronizer is doing all of the work - especially if the road speed and engine rpm are not matched for the gear being selected. Single-clutching during an upshift will usually be fairly smooth because the engine rpm is falling during the upshift and the next higher gear needs lower engine rpm. So, with a little practiced timing, the shifting is generally smooth, unless, of course, there is a problem with a transmission and / or clutch component that interferes with this timing. I use the following technique for both upshifting and downshifting. Here is an example upshifting from 3rd gear to 4th gear. As the tach approaches 2000 rpm, I ease off of the throttle until there is no load on the drivetrain (nether forward nor reverse loading) and I slip the shifter into neutral without depressing the clutch pedal. While the transmission is in neutral (engine now driving the transmission input shaft), I allow the throttle to drop to the rpm needed for 4th gear. At this moment, I depress the clutch pedal and shift into 4th gear. The result is a smooth shift with virtually no wear on the synchronizer, gears, or clutch facing. I use the same technique for a downshift, but while the transmission is in neutral I raise the engine rpm to match the road speed of the next lower gear. Cars and small pickups with light duty manual transmissions work well with synchronizers because the transmission's internal components don't have much weight, therefore a synchronizer can quickly bring a gear to speed without generating much heat. Transmissions used for heavy duty applications (NV4500 and NV5600) have much heavier components, thus much more rotating mass in terms of weight. Synchronizers have to work much harder for any mismatch of road speed / engine rpm during a shift. Of course, any shifting technique being used will be more difficult to perform if there are malfunctioning parts involved. I think first step regarding clutch hydraulics is to measure the distance the clutch pedal travels from the floor to beginning of clutch engagement (engine loading) as I mentioned previously. In the case of my truck, the clutch pedal travel is at least 6 inches before engine loading. If yours is similar, then there is no need to bleed the system. If there is hardly any pedal travel, then bleeding the system would be a good place to start. - John
-
endless NV5600 problems.
The reason it shifts better when you double-clutch during upshifts is because the transmission input shaft is engaged to the engine when the clutch pedal is released as the shifter is passing though neutral. This matches engine rpm to the road speed of the next selected gear. When this happens, the synchronizer is barely used and the shift is smooth. This is why I mention that driving style can contribute to the cause of a transmission that may seem to be hard to shift at times. South Bend Clutch Products can provide you with a heavy duty master / slave cylinder system - even a system that increases the length of travel of the slave cylinder pushrod. If you decide to go this route, be careful to adjust the additional length for only what is needed to make the clutch perform correctly. Over-extending the slave cylinder push rod could damage the pressure plate. - John
-
endless NV5600 problems.
Thanks for answering the questions and sorry I missed your truck mileage in your signature. I would try a process of elimination. First I would operate all of the gears with the vehicle not moving and the engine not running. See if anything feels amiss. Occasionally you might hit gear teeth head on - that would be normal. Do the gates align properly? Without you hand on the shifter, 3rd and 4th should align by default. Move the shifter to the left and 1st and 2nd should align. Move the shifter to the right of default position (against a heavy spring for reverse) and 5th and 6th should align. One more push to the right and reverse should align. Do the synchronizers feels about same in each gear? First gear and reverse can sometimes hit gear teeth head on and be difficult to engage. Out of habit I always select 4th gear before selecting reverse for that reason. Probably the most important item to address is to ensure there is no air in the clutch hydraulic system. The first step would be to measure the distance the clutch pedal travels after it is pushed to the floor and clutch engagement begins. Start the engine and depress the clutch pedal to the floor and select second gear. Slowly begin to release the pedal until you hear the engine begin to load. What is that distance? It should be at least 3 or 4 inches of pedal travel. Something to keep in mind is that when a new clutch, pressure plate, and flywheel are installed, the clutch may engage with the clutch pedal closer to the floor than normal until all of the components wear in. I replaced my clutch at 297,000 miles and during the first three or four weeks of driving I noticed that clutch engagement was right off of the floor and I had to pay attention to fully depressing the clutch pedal when engaging a gear. I don't think there is a problem with the oil you are using nor a problem with any of the internal clutch parts you installed. - John
-
endless NV5600 problems.
How about some history on your truck. How many owners, how many miles on the truck, any transmission / clutch related problems before you bought the truck? How has the truck been treated by previous owner / owners? When the transmission / clutch is giving you problems, how far from the floor is the pedal when clutch begins to engage? I am assuming that when you replaced the clutch that you also replaced the pilot bearing. Here are a few things that can cause your symptoms of gears grinding, hard shifting, or hard to shift into reverse. * a dragging pilot bearing * air trapped in the hydraulic master / slave cylinder * worn clutch fork / fulcrum * worn synchronizers / gates in the transmission * wrong transmission fluid * driving style Any one of the above conditions or any combination of the above conditions could cause the symptoms you are describing. This is why more detail is needed. - John
-
How hot are you?
I called and told them to turn off the wind farms east of The Dalles, so your wind speed should be dying down. - John
-
A/C getting warm after two recharges
The AC compressor shaft seal is a likely cause of the leak, especially if the compressor has lots of miles on it. Just inspect the shaft seal area. If there is an oily mess around it, you have found your leak. If it is dry, it is not leaking. The condenser, evaporator, and accumulator are non-moving parts and will only leak if damaged. Most connections are double-oring sealed and rarely leak, and if they did, the leak would have to present for a long time to affect AC performance. Also, check the high pressure connection for the high pressure gauge. They are notorious for leaking after removing a high pressure gauge. Even a new connector leaked on my truck. The leak is masked by the plastic protector cap. Remove the plastic cap and use a soapy water solution for the test. I am the original owner of my truck. The only leak I have ever had is the compressor shaft seal and it was obvious. I replaced the compressor (about 100,000 miles ago). All of the other AC components are original. - John
-
No start after Pac Brake install/Now VP electrical issue
Congratulation are in order for your perseverance! - John
-
Fass 150 question I shouldn't be asking.
I had to look up the meaning of "quiet quitting" as I had never heard the term before. I thought it was the event that happens when I start the engine in my truck. - John
-
No start after Pac Brake install/Now VP electrical issue
I am assuming the truck was running fine before you started the turbo and PacBrake project. If that is the case, you probably inadvertently did something along the way to trigger this new problem. Is it possible that there is something blocking the intake or exhaust ports? Like a rag or anything that may have been used to protect the intake and exhaust while everything was apart. Just throwing out ideas. - John
-
02 Intermittent dead pedal
Good information from you. It is not a dead pedal or limp mode symptom. It sounds like a direct engine miss, as if the signal to the fuel solenoid valve (inside the VP44) is being interrupted. I recommend that you recheck the work you performed when you did the W-T wiring modification - especially the ground circuit for the ECM and the VP44. You could also swap out the fuel pump relay in the PDC (power distribution panel) with another relay in the PDC. The fuel pump relay supplies power to the the fuel solenoid in the VP44. - John
-
02 Intermittent dead pedal
Just want to clarify a "dead pedal" occurrence. This is a a condition in which the engine falls to and stays at idle speed for 30 seconds or so and then corrects itself on its own. The transition is smooth and no engine miss is involved. This condition can occur with a faulty APPS, but not limited to a faulty APPS. Another condition that can occur is a reduced power mode (sometimes call "limp mode"). This condition will last approximately 30 seconds or so and then correct itself. The transition will also be smooth and no engine miss will be involved. This does not sound like a "dead pedal" condition nor a "limp mode" condition. Have you done the W-T ground wiring modification recommended on this site? A bit more history on your truck will be helpful - total mileage, mods, how many owners, other related problems / repairs, etc. - John
-
What doing tonight? Spark plugs on 5.9L Cummins
As Hank would say, "That engine runs on propane and propane accessories." - John
-
How hot are you?
Overnight low of 43° here in Baker City. Also, the coldest night for over two months. - John
-
Traction Bars for short box 2wd
Under what conditions is your axle wrap occurring? and which gear? Details matter. What clutch did you install when you swapped to the G-56? Why not go back to the OEM rear spring setup? There are plenty of OEM 2WD pickup trucks with 6 speed manual transmissions out there that don't have any drive-ability problems. - John
-
thermostat help !!!
@Nekkedbob, I apologize for my part in hijacking your thread. - John
-
thermostat help !!!
@JAG1, I appreciate your response. I strongly agree with most of what you are saying. But, I am not challenging any of those things. In fact, I have done some of the things that you mention - mounting my lift pump on the frame rail, modifying the suction line inside the fuel tank, adding a serviceable coarse suction strainer just upstream of the the lift pump, and rerouting the return fuel flow to the fuel tank filler tube. What I am challenging is the long-lived belief that somehow the lift pump pressure determines how much return fuel (cooling for the VP44) comes from the VP44 via the 14 psi overflow valve. Over the years I have read many posts from the leader / leaders of this site who have referenced that if lift pump pressure is less than 14 psi, then there is no return fuel flowing over the 14 psi overflow valve, thus no cooling for the VP44 injection pump. I have also read many posts that say the VP44 will be damaged if the if lift pump pressure is less than 14 psi. It is my opinion that this is simply not true. I have never seen any documentation to support these beliefs. I have performed fuel return flow tests that dispute this concept. Others have also performed this same test using flowmeters and driving their trucks for real-time documentation. Some of the tests were performed and results were posted over 15 years ago. In fact, one of the testing events involved a vendor that was going to market improved lift pump systems, but dropped the idea when the fuel return flow test results were documented. One of my goals for posting this information is to help the readers decide what fuel system is best for their truck and to help the readers diagnose any fuel related problems. Years ago I attended a truck driving school. The school was taught by veteran truck drivers, each with over 30 years of safe driving experience. Toward the end of the training I was talking with one of the instructors. I was thanking him for the knowledge he shared. One thing that stuck in my mind was something that he said. It was something to the effect of, "You can learn a lot from a veteran truck driver - including any bad habits or misconceptions of the trade. So, don't be afraid to challenge what you hear" That has always stuck with me. I am hoping that my challenge will be addressed. - John
-
thermostat help !!!
In my opinion, there is a lot of incorrect information being posted here. I am assuming you are referring to the 14 psi overflow valve in the VP44, The moment the engine starts and idles, there is approximately 19 gph of fuel instantly flowing through the 14 psi overflow valve and returning to the fuel tank. This flow is provided by the VP44 internal fixed displacement vane pump - NOT the lift pump. If the lift pump pressure is 5 psi or 20 psi, the 19 gph return flow will remain the same while the engine idles. If there was no lift pump and the internal vane pump was drawing directly from the fuel tank, there will still be 19 gph fuel return flow from the VP44. The internal vane pump pressure regulator is set to around 135 psi - certainly more than enough pressure and flow to ensure that the high pressure pump chambers fill and that fuel flows through the 14 psi overflow valve. At 2000 rpm there will be about 28 gph of fuel returning to the fuel tank via the overflow valve. That is certainly much more than the 2.5 gph injector consumption. It is also likely that if the lift pump pressure is around 15 psi, then the lift pump flow will be much less than rated 150 gph. The lift pump manufacturers do not provide flow vs pressure performance charts. The most information that I could ever find was from FASS - which stated that the rated flow was at 0 psi. So, I would not be surprised if that 150 gph rated lift pump is only flowing half of that rating at 15 psi. If this were the case, 75 gph minus 2.5 gph minus 28 gph equals 44.5 gph returning from the lift pump to its own inlet, or returning to tank by separate line. Not true if you are referring to 10 psi lift pump pressure. At 10 psi (or 5 psi, or 20 psi), 19 gph of fuel will be passing through the 14 psi overflow valve and returning to tank with the engine at idle. The only time the 14 psi overflow valve is closed is when the engine is shut off. I made these charts below to illustrate the combined series and parallel fuel circuits involved in the VP44 fuel system. The 19 gallons / hour of fuel returning to the fuel tank from the VP44 is based on return flow tests that I and others have performed. The test is at engine idle. The circuit on the left uses a 60 gph / 6 psi lift pump that returns fuel to its own suction. The circuit on the right uses a 100 gph / 17 psi lift pump that uses a separate line to return fuel to the tank. Compare the different flow rates in some parts of the two circuits. Note that the return flow rate from the VP44 does not change in either circuit. - John
-
Swapped out some 50hp injectors for some 100's today
@Caleb Hardy, I like what you wrote. I think the words "effective ratio" are a better choice of words to present a case of how different tire diameters affect engine performance. Earlier today I was writing about this subject, but I wasn't ready to post. I am now posting below what my thoughts are. I changed the words "final drive ratio" to "effective ratio" as a result of reading your post. Thank you. I think the intent is to say, for example, "When a smaller diameter tire is installed on a truck with a 3.55:1 rear axle ratio, then the "effective ratio" at the ground would make the truck behave like it was closer to a 3.73:1 rear axle ratio." I think that in order to make a fair comparison, the only time "effective ratios" should be compared between different vehicles is when the vehicles that are being compared are using a transmission gear that provides a direct 1:1 gear ratio. There is only one gear in each of the three available transmissions for 2nd generation trucks that meets this requirement and that gear is a different gear in each transmission. Direct 1:1 ratio gear are: * 5th gear (NV5600) * 4lth gear (NV4500) * 3rd gear (47RE) Over drive gears ore: * 6th gear (NV5600) 0.73:1 * 5th gear (NV4500) 0.75:1 * 4th gear (47RE) 0.69:1 - John
-
Swapped out some 50hp injectors for some 100's today
For your truck, tire size, transmission, and 3.55 gears - sounds like you are right where you should be to me. - John
-
Any helpful tips on doing injectors / valve lash adjustment?
I apologize for any confusion with my instructions. Please disregard my initial instructions. As I recall now, I used the method for installing injectors from the service manual for a common rail fuel system. I have more confidence that this method will provide a more reliable leak-free connection at the intersection of the connector tube and the injector opening. The injector hold down torque is the same for both fuel systems. It's just how you get there is different. The connector tube nut torque is 28 ft/lb on the VP44 fuel system, versus 37 ft/lb on the common rail fuel system. While I am writing this, I see that @Doubletroublehas posted. His explanation works well, too. From the 2004 FSM (installing injectors): (a) Install fuel injector holdown clamp (mount- ing flange) bolts. Do a preliminary tightening of these bolts to 5 N·m (44 in. lbs.) torque. This preliminary tightening insures the fuel injector is seated and centered. (b) After tightening, relieve bolt torque, but leave both bolts threaded in place. (c) Install high-pressure connector and retaining nut. Do a preliminary tightening to 15 N·m (11 ft. lbs.) torque. (d) Alternately tighten injector holdown bolts to 10 N·m (89 in. lbs.) torque. (e) Do a final tightening of the high-pressure connector and retaining nut. Tighten to 50 N·m (37 ft. lbs.) torque (28 ft/lb for VP44 injectors). - John
-
Any helpful tips on doing injectors / valve lash adjustment?
It has been awhile since that repair, but if I recall correctly, the nut that is torqued for the fuel line connection is also the same nut that pushes the crossover tube (connector tube) into the injector inlet port, so, yes, it is necessary to torque all of the fuel lines. If there is a leak at a fuel line connection, it is usually because there is a small piece of foreign material or a scratch / burr on the mating surfaces. This is a fairly common problem, but usually loosening the fitting and slightly moving the tubing as the fitting is retightened usually will stop the leak. If a leak occurs, it is likely to be just a weep. Sometimes, the weep will disappear on its own. - John