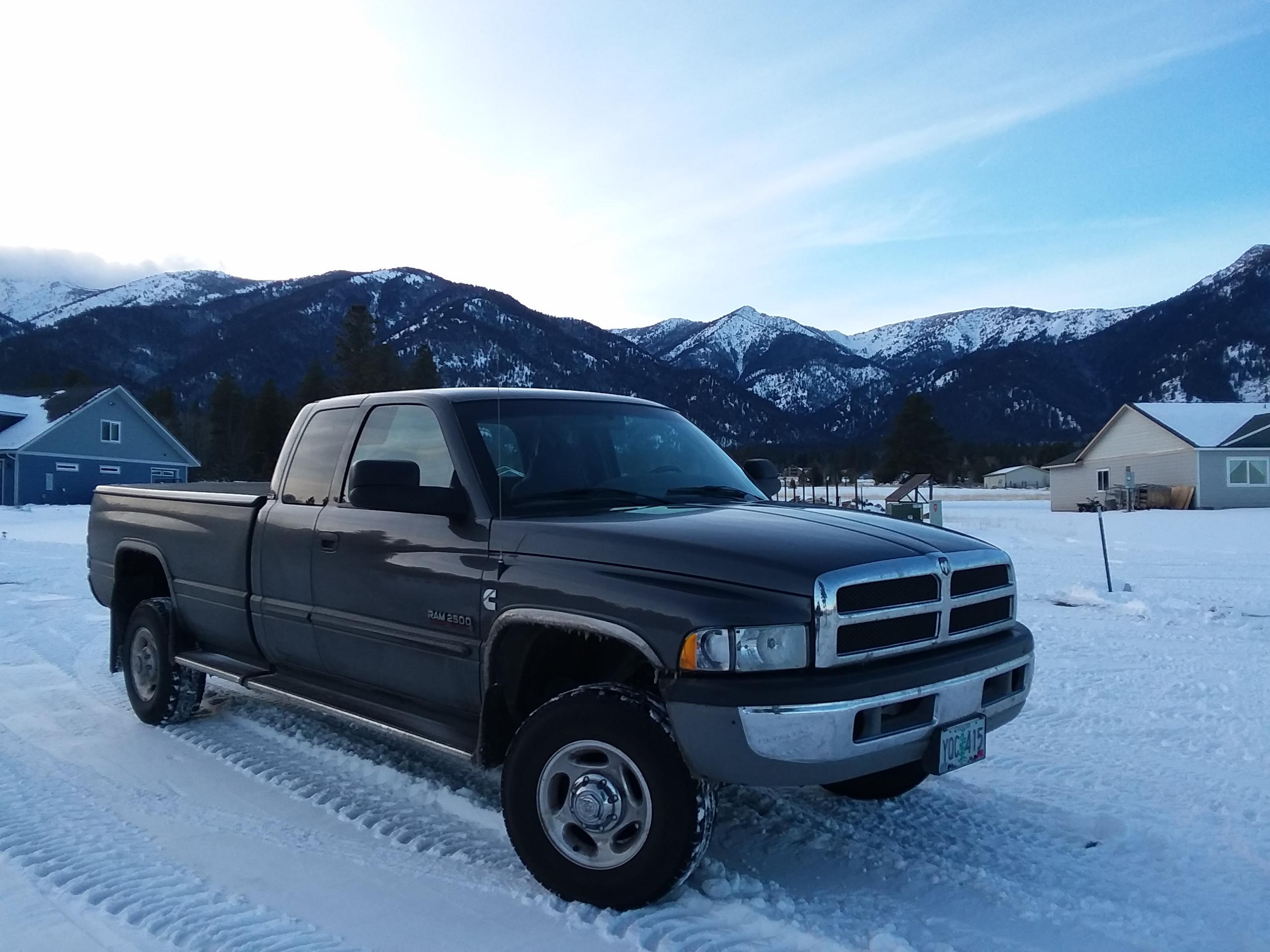
Everything posted by Tractorman
-
Does the VP44 completely shut off fueling when truck is coasting in gear on a downgrade (manual transmission)?
All four strokes of the four stroke cycle engine must be considered for engine braking effectiveness - not just the compression stroke Since all engines have internal friction of varying degrees, this friction is not considered in the examples below for holding a vehicle back on a downgrade. For simplicity, consider the following operation on a single cylinder engine: Diesel engine without throttle plate intake stroke - intake valve open, no holdback compression stroke - all valves closed, air is compressed, holdback power stroke - all valves closed, compressed air expands, cancels compression stroke holdback exhaust stroke - exhaust valve open, no holdback Net results - no engine holdback Gasoline engine with throttle plate intake stroke - intake valve open, throttle plate closed, negative pressure produced, holdback compression stroke - all valves closed, throttle plate closed, air is compressed, holdback power stroke - all valves closed, throttle plate closed, compressed air expands, cancels compression stroke holdback exhaust stroke - exhaust valve open, no holdback Net results - engine holdback on intake stroke. If a closed throttle plate introduced a negative pressure of 25 inches of mercury (approximately 12 psi), then 12 psi would be working on each piston surface area to aid in holdback. Available atmospheric pressure is the limiting factor for engine braking. Diesel engine without throttle plate, with exhaust brake actuated intake stroke - intake valve open, exhaust brake closed, no holdback compression stroke - all valves closed, exhaust brake closed, air is compressed, holdback power stroke - all valves closed, exhaust brake closed, compressed air expands, cancels compression stroke holdback exhaust stroke - exhaust valve open, exhaust brake closed, holdback Net results - engine holdback on exhaust stroke. Diesel engine without throttle plate, with engine brake actuated (a real Jake brake) intake stroke - intake valve open, engine brake turned on, no holdback compression stroke - all valves closed, engine brake turned on, air is compressed, holdback (major) power stroke - all valves closed, engine brake pops exhaust valves open briefly at TDC, compressed air suddenly released, negative air pressure during stroke, holdback (minor) exhaust stroke - exhaust valve open, engine brake turned on, no holdback Net results - major engine holdback on compression stroke, minor engine holdback on power stroke. Please let me know if there are any errors or if something doesn't make sense in the above examples. - John
-
Does the VP44 completely shut off fueling when truck is coasting in gear on a downgrade (manual transmission)?
No hydro-lock would occur. The small amounts of fuel would be injected at regular commanded timing. Since you mentioned the phrase "throttle closed", that could be inferring there is a throttle plate - which there is not on a 5.9 liter Cummins diesel engine. Just mentioning this for clarity. Diesel engines without a throttle plate will not hold back the truck on downgrades with foot removed from throttle. The energy generated on the compression stroke without fuel is immediately released on the following power stroke , so any engine braking is cancelled. @Great work!, thank you for that explanation! That is the answer I was looking for. - John -
-
Does the VP44 completely shut off fueling when truck is coasting in gear on a downgrade (manual transmission)?
Thanks for the quick response. Just for clarification, are you saying that there is no fueling happening when canbus command is 3 or 13 with throttle position at 0% and engine rpm well above idle? Just making sure I understand correctly. - John
-
Me78569 Datalog repository
You did a lot of work to post this information and hopefully others are using it. I very much appreciate your work. I occasionally use your graphs and charts to help me understand what is going on under different driving conditions. The information your charts and graphs provide allows one to see how the engine performs under various operating conditions simulating real world driving. Great job! - John
- 1 review
-
-
- 1
-
-
Does the VP44 completely shut off fueling when truck is coasting in gear on a downgrade (manual transmission)?
Actually, before I posed my question I reviewed some of @Me78569's data logs. I looked at several of them and they all showed very similar recordings. The one posted below is titled "Stock". Note when the throttle position goes to zero (engine rpm 1977 and vehicle speed 51 mph), the CanBus fuel goes to zero followed by an occasional bump of fueling even though the throttle position remains at zero and engine rpm remains well above idle. This kind of supports what @Silverwolf2691is saying. - John
-
Does the VP44 completely shut off fueling when truck is coasting in gear on a downgrade (manual transmission)?
I can't seem to find a source that has a conclusive answer to the question, "Does the VP44 completely shut off fueling when truck is coasting in gear on a downgrade?" It would seem to me that the VP44's high pressure solenoid valve would stop receiving signals under this condition if the APPS signal was at 0% (foot off throttle). Does anyone know if this is true with certainty? An example would be: truck with a manual transmission coasting along on a down grade at 1700 rpm with foot off of throttle. - John
-
Allow us to reintroduce ourselves!
It is nice to see a vendor take the time to let potential customers know where they can get professional help when it comes to replacing very expensive electronic components. You will probably hear from me one day when my high mileage truck needs a PCM or an ECM replaced. I am sure it's only a matter of time. Thank you, - John
-
Squirrels Got Me Good
Good job!
-
Squirrels Got Me Good
@LorenS, I would suggest disconnecting the grid heaters while performing the test if the engine is cold. If the grid heaters are cycling, it would be hard to determine if the alternator began charging for a moment or so. - John
-
Squirrels Got Me Good
Kind of like you started to do. I would use a multimeter on the voltage setting and hook it to one of the batteries in a hands-free manner. Then I would perform the "wiggle test" at the wiring locations you suspect varmints have visited. Do the wiggle tests slowly so you have time to a see a response with the multimeter. - John
-
Fuel pressure issue, works but doesn't.
Okay. Does the FASS lift pump use a relay that is operated by the ECM, or is the lift pump directly wired to the ECM? - John
-
Fuel pressure issue, works but doesn't.
Another thought - is the lift pump fuel pressure gauge electric or mechanical? If it is electric, does it have power when the bump start mode is used? - John
-
Fuel pressure issue, works but doesn't.
Overflow valve operation has little effect on lift pump operation. In the bump start mode the lift pump output flow is basically deadheaded against a non-rotating vane pump in the VP44. This is why lift pump pressure is usually the highest in this mode. Also, overflow valves rarely fail - they get misdiagnosed many times - but rarely fail. Since it is not mentioned, I will asked the question. Can you hear the lift pump running each time the bump start mode is used? While pumping into the bucket in the bump start mode, did you try restricting the flow to build pressure? If not, that may be worth a try. Is the lift pump being operated by the ECM directly, or has a relay been wired with the ECM operating the relay coil? I agree with @LorenS, it does not sound like a lift pump problem. - John
-
What shocks are you running and why?
I installed Bilstein 4600's front and rear about 140,000 miles ago. I have no complaints and the truck still handles well. I installed a Rare Parts track bar about 130,000 miles ago and so far it is doing what it is supposed to do. I have never experienced the death wobble or anything close to it. - John
-
Anybody Else Experiencing Global Warming?
Happened again this morning. This the third 5 inch-plus snowfall this week. I think this might be the last one - but, that is what I thought about the other two. - John
-
Holy crap moment!
I am thinking the same. The safety factor (working pressure versus bursting pressure) would be significantly higher with a steel line. - John
-
Fel Pro head gasket gave up in 4k miles
The first 106,000 miles was OEM coolant. Coolant was replaced with whatever Oil Can Henry's was using. The second coolant change was at 216,000 miles (Napa Long Life). Third coolant change was at 283,000 miles (Napa Long Life). Currently running that coolant at 363,000 miles. At 283,000 miles I installed a coolant filter. When I replaced the water pump at 216,000, I only did it as a preventative maintenance procedure - it was working fine. Personally, I think the quality of the water pump's bearing and seal diminished significantly in the early third generation trucks which led to failures of what had previously been a bullet proof product. I don't think the water pump failures were due to coolant change intervals. - John
-
Fel Pro head gasket gave up in 4k miles
Highly unlikely. Unfortunately, when the third generation trucks came out, quality control on some parts went down the tube - water pumps was one of those parts. I have three relatives that bought 03 and 04 trucks new. The OEM water pump failed (bearing failure) at just over 30,000 miles on one truck and well under 100,000 miles on the other two trucks - all bearing and seal failures on OEM water pumps. Sad. After-market replacement water pump quality is a gamble, as well. The second generation trucks never seemed to have that problem. I replaced my OEM water at 216,000 miles with a Geno's Gates water pump in 2014. The OEM water pump was still working fine - I just thought it was time. It is now my spare. The Gates water pump has logged just under 150,000 miles and is working fine. - John
-
Anybody Else Experiencing Global Warming?
-
Axle Wrap?
I agree. At least not on dry pavement. - John
-
Replacing head gasket
How long did you run the engine? Sometimes it takes a couple of minutes to remove the remaining air from the rest of the injector lines while it is running. Before I would pull any injectors or perform any time consuming work, I would remove the valve cover and start the engine. Don't worry, it will not make a mess. I would then observe every intake valve and every exhaust valve for full travel of operation. If any valve is not opening or only partially opening then you have narrowed down the problem. If everything is normal in the valve train, then I would crack each injector line individually while the engine is idling. If the engine rpm does not drop when an injector line is cracked, then that cylinder is not performing its share of the work. Test all six cylinders in this manner. Note which cylinders are not performing. This will not tell you exactly what the problem is, but it will tell you which cylinders are affected. This will save you some troubleshooting time and narrow down the cause of the problem. Sometimes the art of troubleshooting is not picking something that could be the problem and jumping into it, but instead, it is to methodically eliminate potential sources of the problem that are easy to perform with results that are conclusive. - John
-
Muffler - When to Replace
Now, that's funny!
-
Muffler - When to Replace
So I guess, "Don't fix it, if it ain't broke." approach? - John
-
Muffler - When to Replace
I am still running the OEM muffler on my '02. Just wondering when and if it should be replaced. It has logged 363,000 miles and has been in operation for over 20 years. It still seems to perform fine, but maybe it is one of those things that can slowly deteriorate internally and cause increasing back pressure without knowing it. Should I just keep running it or replace it as a maintenance item? Any thoughts? - John
-
No A/C after winter (worked last year)
Good, you answered all of the questions well. It is likely that the refrigerant charge is low. A rapidly cycling compressor would match the symptoms shown in your video. There is nothing wrong with recharging your AC system yourself. But, if you have never done this before, take time to watch lots of videos to get your best understanding of filling the system and the safety precautions to observe when doing so. Wear gloves. Liquid refrigerant vaporizes at atmospheric pressure at around 20° below zero F. It instantly extracts the heat from of whatever it touches. Also, understand that you do not know how much refrigerant or oil is currently in the system , Since you do not know that, it means that you do not know how much to add. The proper way to charge an AC system is to recover the refrigerant in the system, pull a strong vacuum on the system for a determined amount of time, and then check for leaks. If all is well, then the proper weight of refrigerant with the proper amount oil will be added to fill the system. I only mention this because when a person decides to add refrigerant themselves, that person assumes all of the risks associated with it. Before recharging, I would inspect the all of the components of the AC system that are visible for any oil residue surrounding them A particular candidate is the AC compressor dynamic seal. Let us know what you decide. - John