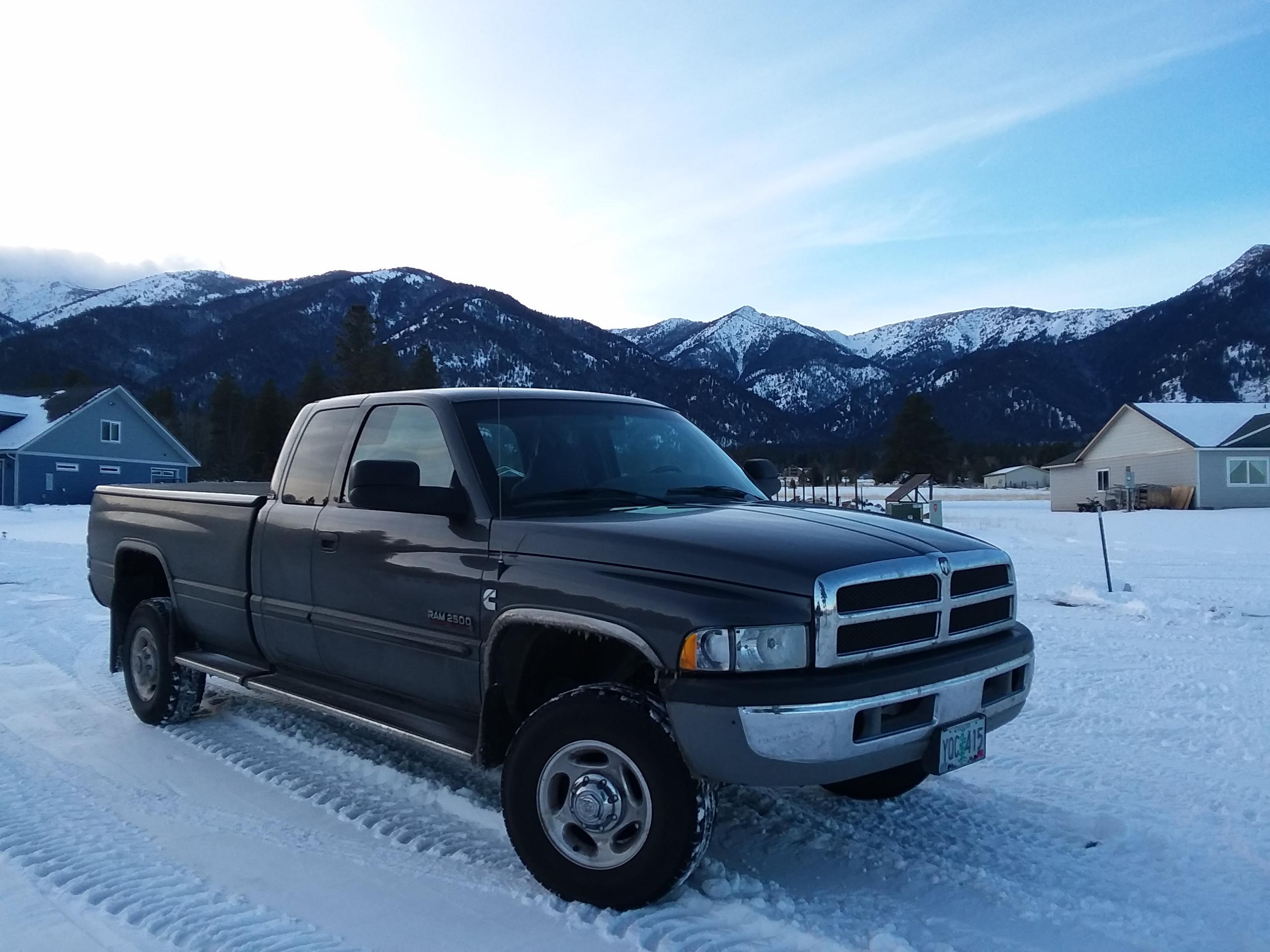
Everything posted by Tractorman
-
Dreaded P0216 code, help/advice
I posted this information on another thread a while back. The credit goes to Mopar-muscle and his helpers in performing a VP44 return flow test using a flowmeter back in April of 2001. I am not familiar with the tuners used back then, but that really doesn't matter. The documented results clearly show that lift pump pressure has no bearing on fuel volume that passes over the 14 psi overflow valve and returns to the fuel tank from the VP44. I am amazed that this kind of testing was done back in 2001, but here we are today with lots of folks still convinced that if lift pump pressure is below 14 psi, there is no fuel returning to the tank from the VP44. I think it is interesting that when I performed a return flow test using a measured container on my truck last summer, both of my test results at engine idle with lift pump operating and at engine idle with lift pump bypassed and not operating were both 19 gph. This compares closely to Mopar-muscle's 18 gph using a flowmeter. His flowmeter is probably a bit more accurate. I appreciate the comments of those who are participating in this topic. - John What Mopar-muscle has to say, Test # 1 well some of you guys ain't gonna like this , especially those led to believe (and those that believe it) ... the bigger is a MUST theory . spent a couple minutes running some tests with a DIGITAL/mechnical flow meter and a MECHNICAL fuel pressure gauge , items under test ... 2000 RAM , DD2's , DD TTPM on level 2 (??) and a HOT PE , ( all levels tested the same at WOT)factory pickup , factory lift pump , factory fuel filter housing unmodified , all banjo bolts intact and unmodified except the banjo to the input of the lift pump is replaced with a 90* swept areoquip type -6AN hose end , the bolt at the lift pump had the schrader cut off and drilled and tapped to a 1/8 npt ( for the gauge) and the banjo fittings between the lift pump and the fitler housing have been drilled to 9/32nd . again all banjo bolts are not drilled out as i have on my ram ( test conducted on the DTT RAM ) . we installed ( LaserBob is helping me and getting #2 fuel poured on his head ) a Sonnex digital flow meter ( inside ID is 5/16") in the return line back to the tank , cut in right at the trans crossmember . gph numbers are fuel returned to the tank . DD2 , DD TTPM (True Torque Power Module) FP volume idle 11 psi 18gph cruise 8 psi 24gph WOT 2 psi 30gph DD2 , TTPM , HOT PE ANY LEVEL FP volume idle 11 psi 18gph cruise 8psi 24gph WOT 0 psi 30gph yes you read that correctly , fuel pressure went to 0 and the fuel volume back to the tank did not change from WOT with 2 psi . the truck did NOT stumble , buck , spit , fart , fall on it's face , nothing , ran like all heck at 0 psi , i will note , my truck ran the same at 0 psi with the DD3's , EZ and a HOT PE . tomorrow we will install -8 lines and an HP carter pump , take flow readings in exact same spot and see what the results are . Mopar-muscle, Apr 24, 2001 Report Test # 2 well , here we go again , todays test was interesting to say the least , and we believe we have it figured out . added the carter HP 15psi 110gph pump on the frame rail next to the tank , -8 bulkhead in the bottom center of the tank , -8 line to the pump , -6 line from this pump to the inlet of an unmodified factory 2000 fuel filter housing , the rest of the system is as delievered from the factory except for a banjo bolt that had the schrader cut off and tapped to 1/8 npt for the gauge , the digital flow meter in the exact same location reading flow back to tank after the tee on the engine . with DD2 , DDTM (True Torque Power Module) psi volume idle 11. 5psi 18gph cruise 9psi 24gph WOT 6 psi 30gph with the HOT PE on any level idle 11. 5psi 18gph cruise 9psi 24gph WOT 4psi 30gph with the addition of the new pump and larger gravity fed pickup point the flow to the tank did not change , though pressure was up , the carter having an internal bypass is living with the backpressure on its output . the concenus is the VP44 is the restriction . the return line from the pump is only returning the excess fuel from the VP44's own internal pump , the more you feed it the higher the backpressure on the line to the pump . the guys with the large pumps , bigger lines and regulator mounted as close to the VP44 as possible have a large amount of the excess flow returned directly to the tank , this is not a bad thing ,( except that at a low fuel level it is possible to foam the fuel in the tank with the large amount of fuel dumping back into it from 2 sources ) but is really overkill as the vp44 uses a set amount of fuel and this is proved by the higher pressure seen with no increase in flow back to the tank . [This message has been edited by Mopar-muscle (edited 04-26-2001). ] Mopar-muscle, Apr 25, 2001 Report
-
Dreaded P0216 code, help/advice
Looking forward to hearing the results. - John
-
Dreaded P0216 code, help/advice
Yes, I am afraid it does. Hopefully, people who read this thread will be prompted to ask questions about the complete operation of the VP44 system and not just be focused on one item, that item being lift pump pressure. I have researched the VP44 injection pump operation for years and I wanted to get some miles on my own remanufactured VP44 that has never seen lift pump pressures any higher than 12 psi before I began posting this information. I am grateful for the 270,000 plus miles this VP44 has provided me, and I know that it could fail at any time. When it does fail, I will not be disappointed - it has given me great performance for a long life. Also worth noting is that all of the fuel lines and fuel filter housing are OEM stock on my truck. The only fuel line modification that has been done is the fuel return line that carries the VP44 return fuel and the return fuel from the head is now routed to the fuel tank filler neck. I really appreciate your comments. - John
-
Dreaded P0216 code, help/advice
I would have never done this test back in 2005 when my OEM VP44 failed. I didn't know anything about the VP44 system back then. But, with what I have learned since, I am confident the risk was very low or even non-existent. I did not figure this out by myself. I have read detailed posts from forums where people had done extensive VP44 return flow volume tests with a flowmeter under all kinds of driving conditions with different lift pumps pressures. All testing results concluded that fuel volume returning to the tank from the VP44 never changed under specific driving condition regardless of lift pump pressure, even when the lift pump pressure was pulled down to zero psi. During the testing, engine performance never faltered, even under heavy loads. These tests were done as early as 2001, so there were some people who were clearly not satisfied with some of the myths associated with the VP44 fuel system. I, for one, am very happy that these people went to great extents to help us better understand the VP44 fuel system. After my testing, I left the lift pump bypass circuit in place. If I ever have a lift pump stop working on a road trip, fuel will still be drawn into the VP44 by the internal vane pump. The fuel will simply flow around the dead lift pump. My low fuel pressure light on the dash will illuminate, but my truck will still be able to be driven home without harming the VP44 injection pump. Without the lift pump bypass, the non-working lift pump could cause a significant restriction that could harm the VP44 and could also require that truck be towed. There are many, many applications where a lift pump is not even used with VP44 fuel injection systems - fuel is just gravity fed from a fuel tank. Typically, the VP44 fuel systems that do not use a lift pump are in a very stable environment, so the lift pumps are not necessary. We need to have lift pumps on our engines, otherwise we would have a less reliable fuel system. A couple of good examples would be: * After a fuel filter change it could be very difficult to start the engine without a lift pump, especially if the fuel filter wasn't prefilled. Bleeding air from the injectors would probably be a necessity and could take a long time. A lift pump that can be cycled for 20 seconds at a time (without the engine running) will slowly purge air the through the small hole on the upstream side on the 14 psi overflow valve. Consequently, the engine will start easily. * Just the smallest air leaking into the fuel system could and would cause roadside breakdowns. Just imagine going to the store and your truck won't start when you are ready to leave because there is a little air in the fuel system. There you would be with the hood raised trying to bleed injectors without the aid of a lift pump - the truck may have to be towed. With a lift pump in the fuel system, you might notice a stumble on start up when leaving the store, but you truck would not be disabled. You would be able to get the truck home to diagnose the problem. I apologize for the long posts, but I really want people to have the best possible chance to understand the VP44 fuel system to help make sound decisions regarding the fuel system on their trucks. - John
-
Dreaded P0216 code, help/advice
Under Fuel Injection Pump Description, The FSM states, "A greater quantity of fuel is required for cooling the VP44 than what is necessary for engine operation. Because of this, approximately 70 percent of fuel entering the pump is returned to the fuel tank through the overflow valve and fuel return line." So, your 60% is close enough, but you mention, "as long and the pressure behind the overflow valve is above 14 PSI and then the fuel is return below that the value is close and nothing is returned." Why do you mention this? Any time the engine is at idle or being fueled above idle, there is ALWAYS plenty of fuel flowing over the 14 psi overflow volve. This flow is provided by the internal fixed displacement vane pump - not the lift pump. So, return fuel flow is always happening - regardless of lift pump pressure. An idling engine returns about 18 gph to the fuel tank. As engine rpm's are increased, the volume of fuel retuning to the fuel tank will also increase because of the increased revolutions of the VP44's internal fixed displacement vane pump. I am fine with your math here, but again you mention, "this means the remain volume is returned again only if the pressure is above 14 PSI behind the overflow valve." I ask again, why do you mention this? The internal vane pump will ALWAYS be flowing plenty of fuel over the 14 psi overflow valve under this condition - even if the lift pump pressure is only 10 psi, for example. I can understand people wanting higher volume lift pumps for high volume injectors that would be operated near their maximum flow at high engine rpm's, but the majority of the people who own these trucks do not operate their engine in this manner, including @Doubletrouble. He basically has a stock setup. I'm a little late here, but since you mentioned that you are on a budget, a 100 gph lift pump would have easily accommodated your fuel needs for your application. A stock VP44 fuel system will consume a maximum of well under 50 gph under the most demanding conditions. This includes returned fuel from the VP44 and fuel burned by the injectors. This is why the OEM lift pumps were rated at about 60 gph. Remember, the lift pump only ensures that there is a positive pressure at all times at the VP44 inlet which is also the inlet of the VP44's internal fixed displacement vane pump. It is only this internal vane that supplies fuel to all of the internal components of the VP44, including the fuel flow over the 14 psi overflow valve that returns fuel to the fuel tank. The lift pump is there only to ensure that fuel is readily available at the VP44 inlet under all adverse driving conditions - such as pulling a heavy load up a long steep grade with an almost empty fuel tank. You said, " Here's the issue. We run 1/2" line to carry this fuel, the return line is what? 5/16 coming out if the VP? There is a restriction. Which doesn't allow the fuel (150gph) to move fast enough" You are sort of on the right track here. The 5/16" return line leaving the VP44 is not a restriction. The VP44's internal vane pump is a fixed displacement pump driven by the engine's camshaft. This means the volume of fuel from this vane pump is determined by engine rpm only. Nothing else. This vane pump is the restriction in the VP44 - the VP44's fuel return lines are not the restriction. The lift pump cannot push more fuel through the vane than the vane pump can displace, under any circumstances. This is why the lift pump has to return so much fuel back to its suction side. As an example, if your engine was using near maximum horsepower and the VP44 was returning 30 gph and the injectors were using 8 gph, this would mean that your lift pump would be delivering 38 gph to the VP44. If the lift pump was displacing 138 gph at a specific psi at this moment, then the lift pump would be returning 100 gph to its suction side. As a side note, I am going to say that your lift pump would not be cavitating. The pump would be delivering 138 gph - 38 gph to the VP44 and 100 gph back to its suction side. 38 gph would be drawn from the fuel tank accompanied with the 100 gph being returned from the lift pump outlet, so there would be 138 gph always passing through the lift impeller. I stand behind what I say here using my own truck as an example. My OEM VP44 failed (0216 code) and was replaced at 87,000 miles in 2005. Back then, the lift pump was always blamed. I strapped a fuel gauge to my windshield and drove back and forth to work for five days for a total of 250 miles. The lift pump easily stayed within specs for the whole duration. Under warranty the VP44 was replaced with a remanufactured unit and the OEM lift pump was removed and an in-tank lift pump was installed. I checked the new lift pump pressure, and it was far lower than the OEM lift pump. The new lift pump was 6 psi at idle and 3 psi at wide open throttle. I really didn't care because there was still a positve pressure at the VP44 inlet. What wasn't known back then was that the VP44 had serious issues with material quality - timing pistons and bores made with poor material, an under designed rubber diaphragm to absorb pressure spikes, rotors that weren't deburred and would seize, poor soldered joints in the processor piggy backed onto the pump - just to mention a few. The professionally remanufactured VP44 pumps addressed these concerns and now the VP44 is much more reliable. So, fast forward a few years and the replaced VP44 now has logged over 270,000 miles and is still running strong. I ran the in-tank lift pump for just over 160,000 miles. I removed it and installed a used FASS DRP-02 (about 65 gph) on the frame rail. It operates at 12 psi at idle and 6 psi at wide open throttle. That pump is still on the truck and has logged over 110,00 miles. So, my point here is that the remanufactured VP44 on my truck has never seen over 12 psi and most of the time is running under 10 psi; however, the life of the VP44 does not seem to have been impacted. This is also with a Smarty S03 tuner on a mild tune with RV275 injectors for the last 110,000 miles and 60,000 miles respectively. @Doubletrouble, you ask a lot of good questions. Last summer I took things one step further. A friand and I carefully measured return flow from the VP44 by letting the return fuel flow into a measuring container. I also rigged a fuel bypass around the lift pump with a one-way check valve allowing flow to the VP44 when I disabled the electrical connection to the lift pump. Results: Lift pump operating: Test #1: engine at idle - .5 gallons pumped in 92 seconds Test #2: engine at idle - .5 gallons pumped in 94 seconds Average fuel pumped is .5 gallons in 93 seconds = .3225 gpm rounded to .32 gpm or 19.35 gph Lift pump disabled and bypassed Test #3: engine at idle - .5 gallons pumped in 93 seconds Test #4: engine at idle - .5 gallons pumped in 95 seconds Average fuel pumped is .5 gallons in 94 seconds = .3191 gpm rounded to .32 gpm or 19.35 gph These results clearly show that the lift pump has very little to do with how much return fuel flows from the VP44. I performed one other test. Since I am convinced that it is the internal vane pump that does all of the work, I disabled the lift pump and drove my truck to town and back – a 25 mile round trip - using the lift pump bypass circuit, so the VP44's internal vane pump was drawing fuel from the tank around the lift pump. I drove the truck hard. I accelerated and held 30 psi boost several times. I restarted the truck several times while running errands. The engine never stumbled and continued to deliver the power it always does. It ran as I expected it would. - John I will probably be editing as I will likely find mistakes in this post....
-
Dreaded P0216 code, help/advice
Okay, that makes sense about what the guy from DAP told you regarding staying with OEM fuel line sizes from the tank to the lift pump. Just wanted to clarify that even though you will now have a 150 gph lift pump and a 1/2" line to the VP44, no more fuel will be flowing through the VP44 and returning to the fuel tank than when you had the lower gph lift pump. The VP44's internal fixed displacement vane pump and the VP44's internal fuel routing determines how much fuel will return to the fuel tank. - John
-
Dreaded P0216 code, help/advice
Does this lift pump have a separate return line for fuel not used? - John
-
Towing-new injectors and quad
I see two issues that could help you/ 1. Go down on tire size - 245's would probably put the engine at about 1700 rpm at 65 mph. 2. You mentioned, " I’ve never even pushed it past 20 psi.". That sounds like a stock waste gate setting to me. If the wastegate isn't clamped or a boost elbow is not installed, then the Smarty S03 can't do much for you. You should be able to attain 28-30 psi boost above 1700 rpm. So, just as long as your transmission is up to the job and since you already have a Smarty S03, I don't see why you can't do what you are trying to do. The engine will pull hard at 1700 rpm and still keep EGT's in check with the right tune. I have been running the Smarty S03 for over 110,000 miles, with the first 50,000 miles on OEM injectors with 250,000 miles on them - changed them out at 303,000 miles. If I were in your shoes, I would get the wastegate operating properly and use the Smarty with a proper tune. Since you already have the Smarty, it would be easy to experiment to see if it would work for you. - John
-
Dreaded P0216 code, help/advice
@ddmk6, I very much appreciate your remarks. Thank you, - John
-
Dreaded P0216 code, help/advice
Since the word “cavitation” has been used a few times in this thread, I thought I would clarify the meaning of “cavitation”, specifically “pump cavitation”. When the suction pressure of a pump becomes so low (usually far below atmospheric pressure), a condition can exist in which part of the fluid being pumped will change from a liquid state to a vapor state where the extremely low pressure exists. When this vapor is carried to the discharge side of the pump, the pressure will instantly rise above atmospheric pressure and the sudden collapse of the fluid from the vapor state to a liquid state will be so severe that an implosion will occur at a precise and repetitive location. If the cavitation condition continues, then the implosions will continue to hammer the internal pump parts at that specific location and this repetition will likely cause damage to the internal metal surfaces of the pump at that location. @ddmk6posted, “Pre-filters can and will effect flow and possibly cause cavitation. Just my opinion but something to think about.” I think his concern is very valid, especially for the lift pump that uses a separate fuel line to return to the fuel tank. The higher volume of fuel flowing through the suction circuit of this type of lift pump makes it more susceptible to cavitation. The illustration below represents my estimation of how the VP44 lift pump system is working under a specific engine load. I think it is a reasonable evaluation based on what I have learned and testing I have done over many years. The following is worth noting about two different lift pump circuits that have identical flow rates, but each has a different return flow circuit design, thus making each pump perform differently in the suction side circuit: · Lift pump A flows28 gph from the fuel tank through the 140 micron strainer to the lift pump inlet. · Lift pump B flows 100 gph from the fuel tank through the 140 micron strainer to the lift pump inlet. If both lift pump A and B have a partially plugged strainer, then lift pump B has a higher potential for cavitation than lift pump A, simply because there is almost 4 times the fuel flow through the fuel strainer for the same engine operating conditions. Also, lift pump A circuit doesn't really need larger suction lines, but lift pump B circuit does need larger suction lines. @Mopar1973Man stated, “Pumps without a return line are very common for cavitation especially when the pump is dead headed.” I am not sure that I agree with this, mainly because I am not sure that “cavitation” is really occurring under this condition. Many times, the word “cavitation” is misused when describing pump operation – even by professionals. For example, there are many conditions that can cause aeration in the fuel system. A lift pump that is passing aerated fuel will likely be noisy, but pump cavitation is not occurring. The air does not change state from a vapor to a liquid. The air will compress and decompress, but these events will be relatively harmless to the fuel system. Even if cavitation was occurring under conditions @Mopar1973Manstated, the electric lift pump is never deadheaded under normal starting and operating conditions. The only time it has a chance of being deadheaded is after a fuel filter change and the lift pump is being used to prime the filters. Even then, the lift pump is operating at a reduced voltage and is still flowing fuel until the filters are full. If I made any errors with my numbers, please let me know. - John
-
Dreaded P0216 code, help/advice
I am unable to follow the logic here. Can you offer an explanation? - John
-
Dreaded P0216 code, help/advice
If I am understanding correctly, you have about 168,000 miles on your truck? It is possible that you are running the original VP44. If that is the case, there are many inferior components inside that pump - including the timing piston assembly. My VP44 failed at 67,000 miles in 2004 with the 0216 code. I drove it that way for 20,000 more miles. Then Dodge replaced the VP44 and installed in-tank lift pump under warranty. Interestingly, Dodge provided a relay for the lift pump. I don't use any 2-stroke oil, but Oregon mandates 5% biodiesel. So far, my replacement VP44 has logged over 270,000 miles. Get your lift pump working properly and give your truck a test drive to see if you continue to go into limp mode with the 0216 code. It is possible that when your lift pump failed, the fuel path may have been severely restricted which would not allow the VP44's internal vane pump to do its job. One of its many duties is to supply fuel flow and to regulate fuel pressure for the timing piston assembly. - John
-
2nd Gen Cummins heater temp differences between trucks
I would try to rig up something to operate the blend door manually after removing the actuator motor. I would make sure to position the blend door so that all of the air is passing through the heater core. and then check to see if the heater core performance has improved. If there is nothing physically blocking the blend door travel, then theoretically, lots of hot air should come out of the vents. Since you are seeing an adequate temperature of the coolant, there can only really be two things wrong that would generate low heat output. * Blockage of coolant passing through the heater core. Or, * Blend door bypassing air round the heater core. You just have to figure out which one it is. - John
-
2nd Gen Cummins heater temp differences between trucks
The only way to do that without removing the dash is to remove the blend door motor and interposer. You can then manually operate the blend door to ensure it travels to its full extent in both directions. Have your engine to operating temperature so you can test the heat output manually. The video below will show you how to get to that point. - John
-
2nd Gen Cummins heater temp differences between trucks
No. The operator cannot control the cycling of the AC compressor. There are only three positions in the upper control switch that disable the AC compressor circuit. They are OFF, and the first two positions clockwise of the 12 O'clock position. All of the other five positions activate the AC compressor circuit. The lower knob (temperature control) controls the blend door position only. It knows nothing else. The blend door must be able to reach its full extent of travel in both directions. At its extent in one direction, the blend door seals so that all air flow bypasses around the heater core. At its extent in the other direction, the blend door seals the bypass and all airflow must travel through the heater core. Any setting of the lower knob (temperature control) between its extents will adjust the blend door to allow air to flow around and through the heater core relative to the control knob's position. The blend door operation is key and could very well be his problem. The heater core in these trucks have more than sufficient capacity to easily heat the cab, even in below zero weather - far below the approximate 35 degree evaporator core temperature when the AC compressor is operating. I run a 180° thermostat and I have no issues heating the cab. I live on the other side of the Blue Mountains from @01_Cummins_4x4. Much colder on this side. - John
-
PS Pump Replacement
I agree. I am inclined to believe that surface metal hardness was more of a factor. I ended up running the power steering pump to 215,000 miles and then replaced it. - John
-
Radiator leak
Rather rude to change the subject like that. What's up with that? Oh, that's right, the subject is Radiator Leak. Good to hear you got your radiator in. - John
-
PS Pump Replacement
I had the same issue with the drive tangs on my OEM pump during the same repair (mine at 176,000 miles) on the vacuum pump. Like you, I thought that kind of wear was excessive and premature. At that time the steering gearbox was a 4 1/4 turn from stop to stop and the tires were stock, so there was no additional stress on the power steering pump. - John
-
rear brakes adjusting to tight
@Nekkedbob, it seems that you have a unique situation. I don't think anyone here is challenging your knowledge - I know that I'm not. But, I also know that when very unusual problems occur, sometimes I have to sit back and rethink things, kind of start over. By starting over, I mean set the brake adjustment as it should be. Then monitor the performance regularly as I mentioned in my previous post. At least then you should be able to find out which is the problem side (if it is only one side). If it turns out to be both sides happening simultaneously, that will be good information to know. This would be another strong reason to start over with diagnosing without changing anything first. You need to know which brake assembly is the problem or if both brake assemblies are having the problem at the same time. That information alone would be of great help to move ahead diagnosing the problem. You have provided a lot of information, but you haven't given much detail. For example, you said, "And yes it has been checked for residual pressure and none has been found." What were the conditions when this residual pressure check was done? If the check was done when the brakes were hanging up, the results of the check would have value. If the check was done hours or days later, then the check would have absolutely no value. Like you, I have done a countless number of rear drum brake repair work. One of the most overlooked things I have observed (even by qualified brake specialists) is the parking brake actuator not being backed off enough to allow both brake shoes on both sides to set firmly against the anchor pin. They may mount the brake shoes correctly on one side, but when the brake shoes are installed and compressed to set on the anchor pin on the other side, energy is transferred through the park brake equalizer, consequently energizing the park brake lever on the previous side which will promptly move the brakes shoes away from the anchor pin. That action usually does not get observed. The park brake cables must be relaxed considerably for this not to happen. I don't think this is contributing to your problem, but it is still worthy of mention. I am really interested to hear what the final fix is going to be. - John
-
rear brakes adjusting to tight
If the cable is removed, there nothing to stop the adjuster from backing off and reducing brake performance. A manual brake adjuster should be used. It has a much coarser, rounded tooth pattern with a spring clip that locks the adjuster in place. I agree. Personally, I don't think it is a self-adjuster issue, but I could be wrong. If it was my truck, I would figure out what is actually causing the problem before making an assumption it is the self-adjusters and then modifying the braking system based on that assumption. I would start by adjusting the rear brakes in a normal manner. Then I would just drive the truck. I would frequently check the brake drum temperature carefully by hand so that I would be aware of the heating of the brake drum / drums before it got out of hand. - John
-
Throttle linkage stuck at idle - cannot accelerate
@01_Cummins_4x4, I have had a Timbo APPS on my truck for over 70,000 miles now. I have also removed the plastic shield. So far, I have not experienced your situation. Plenty cold over here in Baker City but, I haven't started the truck outside in below zero weather, just driven the truck into areas of below zero weather after the engine is warm. I would suspect the throttle cable. It could be that throttle cable housing is shrinking enough in the extreme cold to clamp down on the cable. - John
-
rear brakes adjusting to tight
This is an excellent idea and an easy step that will have informative results. I was going write that in my original post, but I forgot to do so. I seems that I forget many things, but I don't worry too much because shortly I will forget that I forgot. - John
-
rear brakes adjusting to tight
In the first quote you mention "brakes" as in plural. In the second quote you mention "they", which indicates plural again. So, I am understanding that both brakes on the rear axles are overheating. It is highly unlikely that a self-adjuster will cause this - especially in both drums simultaneously. By nature, a self-adjuster can only move the adjuster when there is enough movement in the brake shoes. Even if the brakes are initially adjusted too tight, the self-adjuster cannot grab a tooth on the star wheel until the brake lining has worn enough to allow for enough brake shoe travel for the self-adjuster to grab the next tooth on the star wheel. I highly recommend to not do this. There is something wrong with the brake system. The problem needs to be resolved, not skirted around. When I have situations that are very difficult to resolve, I go back to fundamentals to help arrive at good conclusions. I seek help from people who understand and can explain the fundamentals well. Unfortunately, there are fewer and fewer people around who know drum brake systems well, since the drum brake system is becoming obsolete. That being said, the thing that I see being repeated in your posts is that both rear brakes are overheating at the same time. You also mentioned, "and the pedal has moved up to the top of the travel". This could indicate a hydraulic problem - specifically, brake fluid is not making its way back to the reservoir when the brake pedal is released. A possible source could be brake master cylinder. The first 1/8" forward movement of the dual piston in the master cylinder covers up the compensating port of each piston bore. These compensating ports allow for thermal expansion and contraction of brake fluid when brakes are not applied. If the pistons do not return to their home positions, then brake fluid can be trapped in the brake lines which would not allow for the full return travel of the brake shoes. Over time the brake shoes creep toward the drum surfaces and finally begin to drag. If the hydroboost unit has been replaced at some point in the past, then the pushrod length adjustment could cause this anomaly. Also, there should be some sort of a proportioning valve in the rear brake hydraulic system as well as the anti-lock brakes for the rear axle. These are potential sources of the problem. I am not saying that these things are the cause of your problem, but a possible hydraulic lock would match the symptoms you are having, including the inconsistent time intervals between events. Backing off the brake adjustment and starting over would just mask the problem. - John
-
Replaced batteries, Quadzilla no longer works.
A trickle charger is going to void the warranty!? If I would have bought a programmer that stated that in the manual, I wouldn't install the programmer. I would put it back into the box, send it back, and get a refund. If I were in your shoes, I would challenge the manufacturer regarding that statement. By the way (just my opinion), but you are much more likely to damage an electronic component when operating the said component during an abnormally low voltage condition, such as when you were trying to start your truck with low batteries, which everybody in the world has done at one time or another. Also, the normal large voltage fluctuations from using the starter motor and / or grid heaters are far more disruptive than the fluctuations that could ever come from a trickle charger. Really..., a trickle charger will void the warranty?! - John
-
Grid Heater Delete
Here's my theory for here in the United States. Sometime back in the '70's, the big wigs of the Big Three (Ford, GM, and Chrlysler/Dodge) were having trouble deciding which direction to go - "metric" or "imperial". First one says, "Let's go with metric. It is much simpler and actually makes sense." The second one says, "I think we should stay with imperial. Everyone already knows it and to change tooling would cost a lot of money." After much discussion, the third one says, "Let's do both!" They all agreed unanimously, and it became law. - John