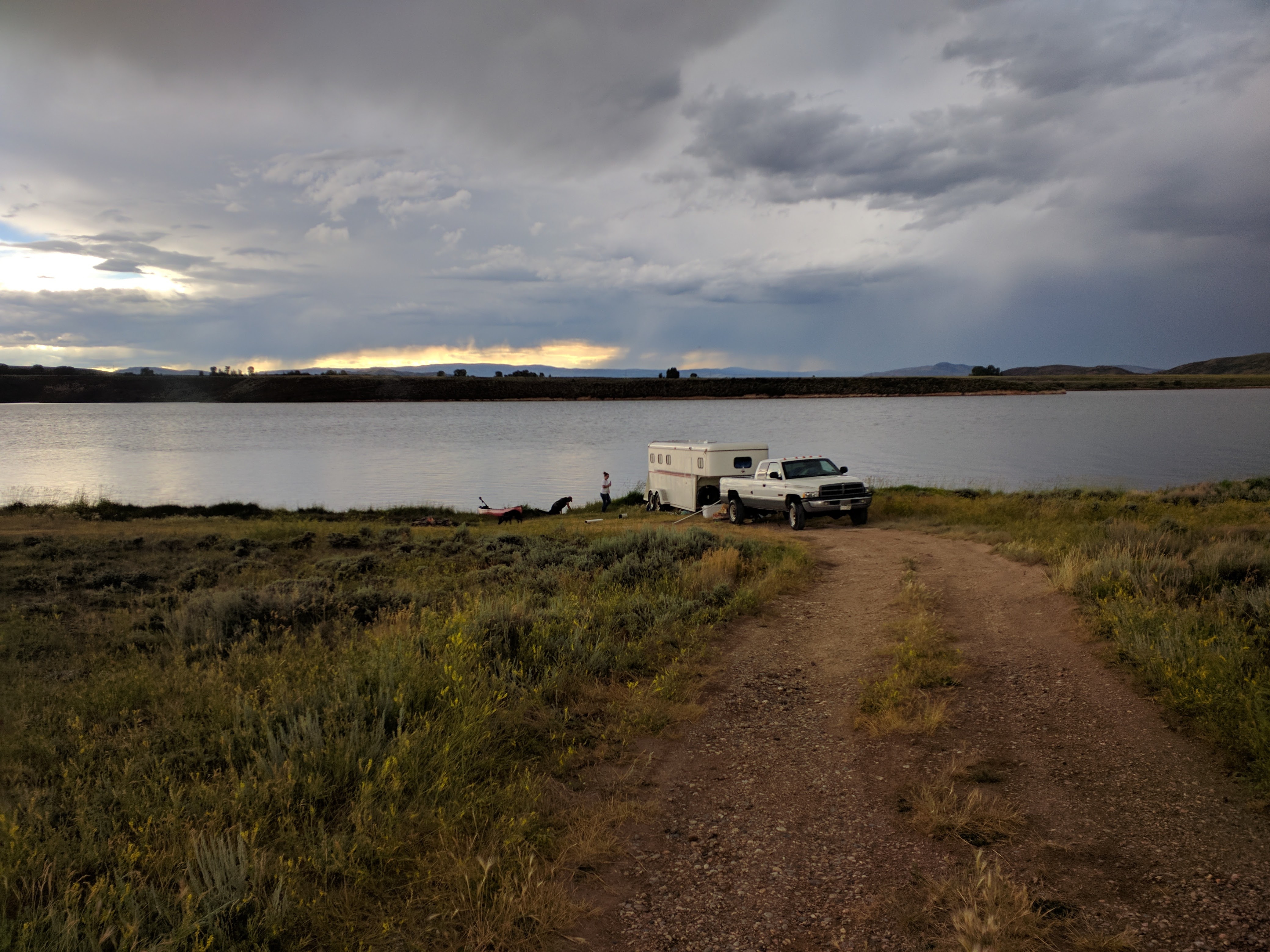
Everything posted by Me78569
-
He351ve stand alone Arduino controller code for 2nd Gen Cummins
I seem to have some bidirectional communication going on now between my arduino canbus shield the the underhood plug. It is much less complex than trying to talk through the Obd, at least for me. Not sure what it means yet, but at least I have some data. I can't say that it is much faster than the obd however. More digging is required.
-
Edge comp question
I like to yell sometimes
-
Knocking sound.
haha I have actually heard this before actually. I dunno if it is valid or not.
-
Fuel problem?
If the lift pump does not remain on after cranking that it is likely ECM. Any WTS light issue? You might have them supply lift pump power directly and see if the issue goes away. if it does it points back to the ecm.
-
Another Arduino Project being dreamed up...Smoke output throttle reducer
DAC is in and the code is adjusted to work on a 12 bit scale. Seems to be working very well during the bench testing. I still have to test the %100 TPS voltage to ensure I am writing a high enough V. I think it was 3.6 volt for %100 throttle, but I have not messed with it in a week or so.
-
loss of overdrive when ac is turned on
Test the new alternator for AC noise. AC noise tends to burn up computers, longer you have it the worse off the computers are. I would get some dielectric grease and check and lube every plug under the hood with it. Apply it, then cycle the plug 5 or 6 times. Look for any signs of corrosion on the pins and wires.
-
loss of overdrive when ac is turned on
Did you replace the alternator?
-
He351ve stand alone Arduino controller code for 2nd Gen Cummins
From a PM I got 1. PN for the turbo connector Turbo Connector 4 pin: Mouser Connector Link 54200410-B Pins 10762770 Turbo RPM Connector: Mouser Connector Link PN: 282087-1 If you want the EB then I would suggest getting a arduino 5v relay to control the grounding of the TC pin. of course assuming you have an auto and not a manual. http://www.resistorpark.com/5v-1-channel-relay-module-for-arduino/?gclid=Cj0KEQjw17i7BRC7toz5g5DM0tsBEiQAIt7nLDAtqtFkPWam-2Lse_pLChd45O9zfhXoaEVTgmr2Yl0aAmXq8P8HAQ Should be fine. I think you have everything you need other than a button to tell the arduino when you want to engage the EB. I recommend a momentary on off button. I am working towards retrofitting a chevy shifter with the built in buttons, but who knows when i will finish that up. 2. You need to have a button to tell the arduino when you want to engage the EB. You could do it off the brake pedal switch if you like, but I dont like having it always go into eb mode. 3. I have been trying to find a good way to read canbus data but I have yet to be able to get back info in a timely manner. I am actively working towards this as time allows. At this point I wouldn't wait on me getting the canbus going. It is pretty tricky on our trucks. You can read RPM directly from the sensor, it puts out a nice square wave.
-
anyone ever thought about retrofitting tapshifter in place of our autos?
already have. I would need to make volts on the solenoid through gear shifts vs tps. then bypass the pcm and adjust the solenoid pressure to make shifts happen. again I dunno if I want to do the R&D on that one, but in theory....
-
anyone ever thought about retrofitting tapshifter in place of our autos?
Depends on what you have. I could use the buttons for + / - to manually set vane position, or curve type, or EB or lockup. You may even be able to control shifts IF, BIG IF, you were able to control solenoid pressure somehow. not sure I want to R&D that one but it should be sorta possible.
-
anyone ever thought about retrofitting tapshifter in place of our autos?
I like nice OEM style buttons to control things, It could be EB or TC lockup or whatever. Or the dodge version I looks like it might be a pretty easy install. Anyone ever been down this road?
-
Reservations for Full Eclipse weekend
18th-22nd for Jen and I
-
Knocking sound.
Nope get new ones haha. I think 300k means that have lived their life. Injectors are cheap for the 12v and 24v
-
Beat my old high mark of MPG's.
time for 2wd springs and a roll of masking tape to tap all body joints.
-
Reservations for Full Eclipse weekend
I am sure we can hang a hammock between two campers at the very least
-
Leveling kit questions
humm
-
He351ve stand alone Arduino controller code for 2nd Gen Cummins
Lockup + EB is now tested and working with the current code. Using one of these https://www.sparkfun.com/products/13815 it is easy to control lockup. It is just a NO relay. to control it you just set a pin to low to engage the relay or high to disengage. Now if I can only figure out how to read shift points I could do an automated 2nd gear lockup. @dynamic said something about watching for a spike or something, I dunno. More reading and testing. this project is starting to get pretty specific to my truck now. I might break the code out into 2 different sections, one for my projects and one for controlling the turbo. Dunno who knows if anyone is actually using my code.
-
Quiet exhaust
Do you currently have a muffler on your MBRP?
-
Leveling kit questions
So in theory you should get 5x the use out of the joint? then you must get new oem style joints?
-
Leveling kit questions
What happens when the stud end plastic gets rounded out? I am confused as to how tight the stud end is held.
-
Leveling kit questions
Does the main ball still rest against the OEM plastic bushing in the head of the joint? or is there a replacement piece for that.
-
Leveling kit questions
I have only seen what was in the pictures so I am not an expert in it. It looked like the joint was pressed into the collar to prevent movement so I was put off by that. I would like to see one in person and take a closer look.
-
Leveling kit questions
I personally don't like the luke link setup. they pretty much take all the flex out of the steering system that typically is there due to the joints and rubber.
-
Reservations for Full Eclipse weekend
I didn't want to drain all the coolant haha. I just replaced the waterpump a few months ago and had to replace the coolant.
-
Reservations for Full Eclipse weekend
I was able to clean mine without pulling it front the truck 1. Pull the upper hose and tie it back to prevent loss of coolant 2. pull the fan 3. pull the fan shroud 4 Get a bottle of this http://www.shopwurthusa.com/wurthstorefront/Chemical-Product/Cleaning-and-Care/Degreasers/Citrus-Degreaser-18-Fl-Oz/p/0890924 Put it in a spray bottle 5. spray on radiator and let sit for 20 minutes. 6. wash off using semi high pressure from hose. 7. do 3-1 backwards 8.... 9. profit I went from overheating (220*f+ driving VERY easy to keep temp in check) with tuner off pulling up the pass to pulling the pass with tuner turned up with the same load at 200*f no issues.