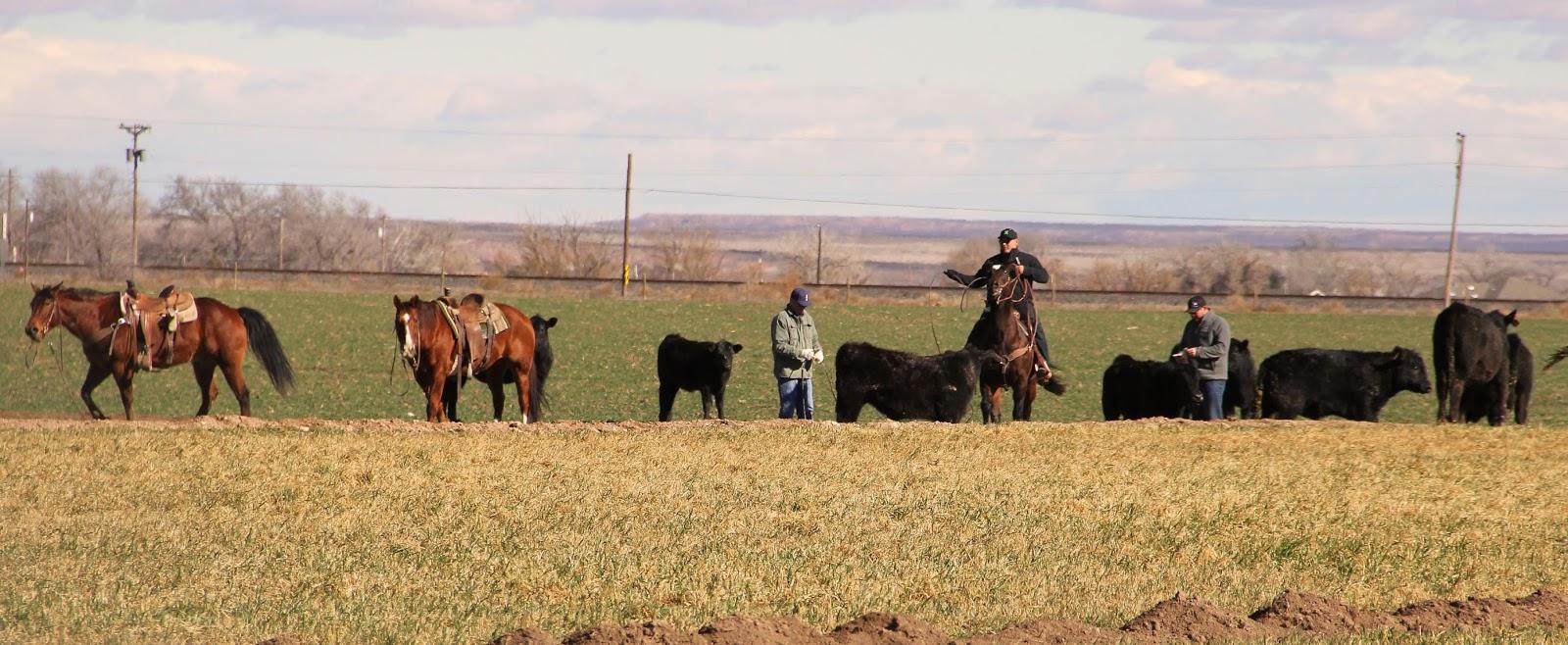
Everything posted by Rogan
-
2001 24V charging issues
This truck is in need of a lot of catch-up care.. LOL It leaks oil out of orifices I didn't even know it had. So far, the running diags are as follows: ECM repair/replace AC noise check Rear main seal Front main seal Oil pan gasket Tappet cover reseal Full Exhaust replacement Clutch assembly (original has 382K miles) rocker adjustment Valve cover gasket Gonna be a fun one...
-
Understanding your stock turbo!
I thought the HYs were only on the autos.. I had 2 01s, one auto , one 6 speed. Auto had HY35, the 6 speed had the HX..
-
Derale 15870 Install Under 3rd Gen
On 2G trucks, I tend to mount them behind the front bumper on the left side, tucked up by the outer bracket; tends to work well there. Very nice job on the 3G, @Dynamic
-
AC blower motor somtimes not working
Yeah, I'm sure you know, but the 2002 1/2 tons were new body style (3G). It always confused me, for the longest time. I've got a 2001 at the house that needs a resistor and blower right now.
-
What are the best headlight packages?
Yeah, I can buy a lot of additional lights for 1000$. lol $1000 my be like: or
-
Waited a long time for this
Wow, you couldn't find a black zip tie? haha!! what gauge pod is that, on the dash? I like it.
-
CR Injector failures and upset owners
This 08 3500 6.7 I've been working on, got a new set of injectors last spring at 108k mile mark. I will warn those that have CRs and are looking to buy injectors.. STICK WITH BOSCH OEM/REMAN buy REPUTABLE builders (I solely use Antrim Diesel in PA for all injector and pump repairs/replacements.) $25-2800 for a set of injectors is outrageous, even from my perspective. Built a 5.9 CR for a guy's 05 2500, $6000 build and installation. He bought Advance Auto replacement injectors after being suggested not to.. 685 miles on the engine, and BOOF... Injector failure wiped #2 piston and cylinder and valves.. AAP warrantied the faulty injector only. $3500 more to the shop so we could fix his engine.. So in 3 weeks, a poor decision cost him a little better than $12K.
-
NV273D to NV271F (hybrid) swap in MY08 3500
So, I finished the transfer case swap in my friend's 08 3500 MC this past weekend. Basically, the reason for it was I replaced the chain, gears, seals and bearings in it a year or so ago, due to what we thought was slippage of the chain. Problem disappeared for about 3 months, then returned. Only this time, it came back with a vengeance. What was actually occurring was the electronic shift motor was attempting to engage 4WD at whenever it felt like it. Last time, it was at about 70mph when it tried to switch to 4WD, all but grenading the tcase into dust. So I Got my hands on a really good priced NV271F (Yes, Ford). Ripped it apart, freshened the bearings, seals and chains, etc, then started determining what I needed to change for it to work in the Dodge G56/5600. Dodge mainshaft is longer in the nose than the Ford. Input stub shaft (that sits in the planetary gearset) needs swapped (dodge one has a longer nose and a deeper bearing race.). Rear output shaft housing needs swapped; Dodge uses slip-yoke, Ford uses flanged rear output. Front shaft output flange needs swapped to the Dodge one; the Ford one bolts to the front driveshaft the opposite direction, so it won't work. Aside from that, you could swap the shift fork carrier, but I didn't as the Dodge one was destroyed, so I went with the Ford selector shaft. The Swap works great, But there's a couple of oversights.. I used a Dodge 2004 1500 tcase shifter (it's same as all 3G trucks) and 2004 shifter boot; the boot fits perfect and is same as 2007; just pop the pocket out of the console and the boot snaps right into place. HOWEVER, the Ford's shift (top to bottom) is 2H-4H-N-4L. Dodge is 4H-2H-N-4L. So the pattern on the knob is wrong, and I can't find anything else to show the proper pattern. If I owned a 3D printer, I'd make one, but I dont. The Ford knob is a slip-on splined knob, where Dodge is a thread-on. I also need to figure out the shifter motor wiring for the 2008. It's an 8-pin plug, but uses 5 pins. The Ford uses a standard 2-pin 4WD switch. Current issue is that "SERV 4WD" is illuminated on the dash, and the 4WD light does 'not' work (for obvious reasons). I think they are controlled by the PCM/ECM, so with the motor no longer present, I have to see if I can find out/figure out how to 'fool' it. Thanks! Rogan
-
My dually
Good lookin truck. You’re askin a lot out of those skinny tailgate cables ?
-
2001 24V charging issues
Understood. The pcm (from a regulation standpoint) is completely out of the circuit. The evr is located by the airbox on the firewall, next to the hood hinge. I’ll get him to drop the truck off maybe next week so i can get a closer look at what’s really going on. This megacab im swapping to a manual tcase is also his, so when it’s done I'll get his other truck. I’ll test the AC noise too, but it may just be the evr took a dump. I’d love to go back to the pcm regulation but that may require a new pcm; not 100% sure yet.
-
2001 24V charging issues
Mornin' fellas. Out of curiosity, how would AC voltage cause an overcharge issue? I totally get how it can affect signal issues for things such as TCC, and all, but to cause overcharging? Not disputing it, just curious of the thought process as to 'why' it would..
-
2001 24V charging issues
Truck belongs to a good friend of mine. A couple years ago, he had an overcharging problem. Since the PCM (I think) controls the charging, he wanted me to throw an external voltage regulator (EVR) on it to 'get by for awhile'.. Well, it worked fine for a year or so, and now he told me yesterday that it'll peg the voltage gauge and ding the check engine chime. the fuel gauge, he said, will often drop to empty for a few seconds, then return to normal, but doesn't seem consistent with anything else.. Are we at a point where he should look for another PCM? Or has anyone seen this type of issue before? Thanks, all.. Rogan
-
My dually
that welder must be heavy AF. truck looks like it's bowed in the middle. Possibly just camera angle. Nice looking non-dually, though. I'm here for the dually.
-
Exhaust system info
Exactly my point on you gaining any benefits from a larger diameter exhaust. 65K mi a year? and that truck only has 350k on it?
-
Exhaust system info
I agree with Mike 100%. However, a fuel-miser like himself would not see benefit of a larger diameter exhaust, other than for audible tone gains. However, in a high-boost situation (here's where thermodynamics come into play), this is where you'd see the difference in stock 3" vs larger exhaust sizes. As your boost levels increase, so does your IATs, cylinder pressures, and EGTs. With the much hotter air leaving your engine, the molecules are greatly expanded. The stock 3" piping doesn't allow for the added expansion of the gasses and slows down the flow through the system. As they travel down the pipe, they cool and contract, requiring less 'volume'.So even a 4" downpipe into a 3" exhaust would still help a bit. Bear in mind, though. The choke point on the HY/HX is the 3" turbine outlet in a high-boost situation. The faster you can get the exhaust gasses out and away from the engine, the less heat-soak you encounter. But if you are a mileage chaser, you'll get no gains in anything, other than loudness and tone.
-
Power lost intermetant
I had a similar issue with an 01 automatic. From initial startup to about 140-145*F coolant temp, it would not go above about 17-1800 and had no power. As soon as it reached 140+F, it ran like normal. Come to find out, it was an issue with the circuit board inside the VP44; this is considered a non-serviceable part, requiring VP44 replacement. What was occurring was than when the engine was cool, there was a 'break' in the board's circuit, causing the VP to limp, basically. Once the engine reached a certain temp range, the expansion of parts regained circuit contact, closing the circuit, and boom! Rand normally.. I never fixed it, just drove it accordingly. Just food for thought...
-
Exhaust system info
I agree. I've had mufflered 4" DE and MBRP, as well as 5" mufflered DE on previous trucks. As M73M stated, they'll growl when you're on the skinny pedal, but nice and quiet when cruising. Turbo-whine is also increased a little with the bigger pipe, and stainless seems to even produce a little greater whine and throatiness over aluminized steel.
-
G56 rattles horribly after switching to a dual disk clutch and SMF
When I go out to the farm tomorrow, I'll take a picture of it.. I'm SO GLAD it's over. Also, converted the truck (in process) from NV273 Electric to NV271 manual. The shifter motor kept trying to randomly engage 4WD until is destroyed the 273.
-
Hi, I'm Rogan
HAH! Hiya Mike. It was thanking me for NOT being here, I suppose ;)
-
G56 rattles horribly after switching to a dual disk clutch and SMF
Let's dig up an old thread. Found the source of the problem, and only recently (as in, last week). When you remove the DMFW, there's a small spacer plate thingy that goes between the DMFW and crank end. If you aren't looking for it, it's VERY easy to miss (was on this one). For S&Gs, I dropped the clutch assembly off the truck as there it was! Embedded itself (pressed in, basically) into the back of the flywheel. Pried it out, cleaned it up, BAM! Vibration and about 70% of the rollover noise was gone. The issue is that the chamferred edge is not exactly the same profile as the stock flywheel, but extremely close. Close enough to feel right, but different enough to actually not allow the flywheel to sit completely flush.
-
Hi, I'm Rogan
I'd like to introduce mysel-... oh wait. I've been here before, it's just been a really long time. :)
-
Article: Compressors and Turbines Explained - Part 1
Turbochargers while simple in design, can get very complex in theory. From deciding what compressor trim is desired, to what turbine housing to be used is confusing to most who enter the field of forced induction. This article will hopefully take away all the confusion in turbocharger selection. Terminology Before I can begin writing an article explaining turbochargers, terminology must be learned. Here is a list of the more commonly used turbocharger terms: Compressor - Essentially a fan that spins and compresses air within an enclosed area (compressor housing). In order to allow the air to compress and build pressure within the housing, the fan must be spun at certain rpm levels. Compressor Housing - Housing that encloses the compressor. Pictured is a compressor housing. Compressor Map – A map that allows the ability to plot compressor pressure ratio vs. engine airflow. An “island” shape is created on the plot showing where the compressor is efficient. Compressor Efficiency – Compressors efficiency is the ability to produce lowest possible temperature from the compressor air. When air is compressed heat is generated, at certain range of speeds of the compressor rotation the heat can be keep to a minimum. This is what is known as “being in the efficiency range of a compressor” Higher efficiency, lower outlet temperatures. Highest possible efficiency of compressors are 78~82%. Lower outlet temperature=lower intake air temperature. Lower intake air temperature=more dense mixture of air=more oxygen available in the combustion to burn. The greater amount of oxygen present with fuel provides more energy. More energy=more heat=more torque=more power. Compressor Trim – The trim of the compressor refers to the squared ratio of the smaller diameter divided by the larger diameter multiplied by 100 of the compressor wheel. The smaller diameter of the wheel is known as the inducer, and the larger diameter of the wheel is known as the exducer. Compressor Families – Beyond compressor trim levels there is compressor family of wheels. In the Garret turbo line of older technology compressors there is T22, T25, T3, T350, T04b, T04e, T04s and T04r families. In each family there is trim levels to the family. Although there is a 60 trim in both the t3 and to4e family wheels, the main difference is the inducer diameter of the wheels. The trim is only a ratio of the exducer/inducer, so while the inducer size of the compressor wheels are vastly different, the ratio between the exducer/inducer remains constant since it’s the comparison between the exducer to inducer size. Turbine – A fan that uses exhaust energy to rotate. The rotation of the turbine is transmitted through a shaft that is connected to the compressor. Faster the turbine spins, faster the compressor spins. Compressor uses the rpm translation through the turbine/compressor-connecting shaft to compress air at the rpm level that dictates compressor flow. Turbine Housing – Housing that encloses the turbine wheel. Turbine housing size affects the ability of the turbine to transmit rpm to the compressor wheel. Smaller turbine housing, quicker spool up due to quicker translation of rpm’s to compressor. Trade-off is increased low-end response for less high-end response from turbocharger. Picture below is a turbine housing. Turbine Trim – The trim of the turbine refers to the squared ratio of the smaller diameter divided by the larger diameter multiplied by 100 of the compressor wheel. The smaller diameter of the wheel is known as the inducer, and the larger diameter of the wheel is known as the exducer. Turbine Families – As with compressor families, there is turbine families. The most common evidence of the turbine families is the t31, t350 and t04 wheel used in the t3, t3/t4 turbos sold on the market. Precision offers the t31, aka stage 3 blade in their smaller line of sport compact series turbochargers. The t31 comes in two different trim levels the 69 and 76 trim. The t350, aka stage 5 blade comes in two different trim levels as well, 69 and 76 trim. The t31 will spool faster than the t350 due to the physical size differences (t31 being smaller). The smaller the trim level the quicker spool, but less top end. Essentially you are changing the turbine pressure ratio when you are selecting the family and trim level of the turbine wheel you are using. The larger family and trim level you choose the more power the turbocharger will produce at the expense of lag. As with the compressor trim levels both the t31 and t350 have the 69 and 76 trim levels, which are not the same. The turbine trim is the ratio of the exducer compared to the inducer size of the turbine wheel, since its only a ratio the size of the inducer/exducers are completely different. Turbine Map – A map that allows the ability to plot turbine expansion ratio vs. engine airflow. An “island” shape is created on the plot showing where the turbine is efficient. A/R – Ratio of the area of the compressor/turbine housing to the radius of the compressor/turbine wheel. In order to find out the A/R of the compressor or turbine housing select a point where the compressor/turbine housing begins and measure the cross-sectional area at that point. Cross sectional area is A=P*(Radius)2. Next step is to measure the distance between the center of the area and the center of the compressor/turbine wheel, this is the radius measurement. If you choose a different point on the compressor/turbine housing and remeasure the area and radius, you’ll find that it stays constant. This is due to the housing getting constantly smaller in diameter as it gets closer and closer to the compressor/turbine wheel. When you upgrade from a .48 to a .63, or .63 to a .82 A/R you are essentially increasing the area of the housing. Increasing the area increases the amount airflow to the turbine wheel. The smaller area of the smaller turbine housing builds pressure quickly and transmits this pressure to the turbine. The pressure gives the turbine enough rpm’s to allow the compressor to compress air at lower engine speeds (less engine speed, less airflow from engine). The trade off is that pressure builds up quickly in the housing to obtain quick spool up, but the pressure quickly becomes to great and backpressure builds up. The backpressure is the restriction that limits shaft speed of the compressor, and as the rpm increase (engine airflow increases) the torque curve begins to drop off due to the volumetric efficiency of the engine decreasing. Think of the turbine housing sizing as increasing/decreasing inlet pressure to the housing in order to gain low end, midrange or top-end response from the turbocharger. The smaller turbine housing wont carry the torque curve to a high rpm, limiting the amount of peak whp. Excellent low-end and midrange gains are felt through smaller housings. Compressor/Turbine Mismatch – When “matching” a compressor and a turbine you are seeking to balance the turbine characteristics to the compressor characteristics. When you increase the size of the turbine wheel you are decreasing the pressure ratio of the turbine, essentially decreasing the shaft speed connecting the compressor/turbine. When pairing a larger turbine wheel to a small compressor wheel, the smaller the compressor wheel the higher the rpm the wheel has to be spun at to compress the air. This becomes a problem in that the smaller compressor cannot generate adequate shaft speed to compress air. The same can hold true when pairing a huge compressor to a small turbine wheel. The larger compressor needs less shaft speed to compressor airflow, but the smaller turbine wheel will spin at a much higher rpm level that is what is necessary. The result is crossing over the choke or surge line on the compressor map (this will be explained in part 2 of this article). Note the two different compressor maps, one of a 60 trim t3 compressor wheel, the other a t64 compressor wheel. Part 2 will explain compressor and turbine maps, and all the terminology that goes along with topics.
-
Article: Turbine Housings, Exhaust Sizing, and Back Pressure
Everyone seems to grasp that a larger exhaust on a turbocharger vehicle will gain faster spool up, increased power and thus faster acceleration. Here is the theory behind the phenomenon: The turbine housing is merely a volume for which exhaust gas (energy) is transmitted from the engine, to the turbine blade, then dispelled into the atmosphere. In order to better understand how this works we need to take a look at pressure. Turbines in general work off of a pressure differential. A pressure differential in layman's terms is the ratio of pressure before the turbine blade, and after the turbine blade. The greater the pre-turbine pressure compared to the post-turbine pressure, the greater the amount of work can be transmitted through the turbine/compressor shaft. This is where some engineering comes into play. Work is defined as the integration of force and displacement, keeping force constant. Again in layman's terms this merely means work is the force exerted on an object while taking into account the change in displacement, or position of the object. In relation to turbines, the greater the pressure differential, the greater the amount of work is created. The greater the amount of work created, the greater the amount of energy transmitted through the turbine, into the compressor through the connecting shaft. To break this down into another small explanation, compressors work off of rpm. The amount of air the compressor is able to “flow”, or merely put the lbs/minute the compressor can flow is dictated by the amount compressor blades, angles of the blades, etc. What the compressor uses to “compress” the air through the inlet is based off of how fast the compressor wheel is spun. The rpm at which the compressor blade has to be spun to “compress” the air varies from turbo to turbo from the different compressor blade characteristics. Another critical aspect of the compressor is the physical size and weight of the blade. The larger the blade, more amount of energy must be transmitted to allow the shaft to spin to the rpm at which the compressor can compress the air. In engineering terms rotating mass is called inertia, so smaller turbos have smaller inertia demands, larger compressors have larger inertia demands. To bring the focus back on the turbine side of things, the increased inertia demands more energy to be supplied from the turbine. The greater the pressure differential discussed above, the greater the amount of work that be be supplied to overcome the inertia effects of the compressor. Now looking at the exhaust, or post turbine the larger the exhaust, the larger the pressure differential can become. The increase in area of the exhaust, gives the exhaust gas much more room to expand. Hot gas has only one goal, to expand as quickly as possible. The goal pre-turbine is to focus the energy into the turbine to carry as much energy as possible. As the exhaust expands the energy dissipates, so the goal post turbine (i.e exhaust) is to have the largest area possible for the gas to expand. Looking at the immediate exit of the turbine housing, the downpipe, the exhaust gas is traveling at a very high rate of speed. The exhaust gas is expanding rapidly, and is in a very turbulence state from being flung from the turbine. At this point having a 3″ down-pipe becomes critical since the exhaust gas is both in a turbulent state, and is expanding. In turbulence, the expansion of an area the turbulence is forced to become more laminar (although this doesn't happen very quickly). Also the increased area allows the gas to expand rapidly, allowing the energy in the exhaust gas to dissipate quickly and letting the pressure created by the exit from the turbine housing to drop. Essentially you are creating a greater pressure drop. Looking at the turbine housing the sizing becomes a critical part in how the pressure differential is created. Take for instance the .48 A/R housing. Changing turbine A/R has many effects. By going to a larger turbine A/R, the turbo comes up on boost at a higher engine speed, the flow capacity of the turbine is increased and less flow is wastegated, there is less engine back pressure, and engine volumetric efficiency is increased resulting in more overall power. The .48 A/R is able to create the pressure differential at a much lower engine rpm, giving the compressor ability to make its maximum rpm speed sooner. As the engine rpm climbs, the pressure differential is lowered due to the physical volume of the housing size becoming a restriction on the post turbine side. As the housing size is increased, it take greater engine rpm speed (greater exhaust energy) to spool up the turbine, but the pressure differential is less effected by the physical volume of the housing. If you are after maximum midrange gains smaller housings are essentially, if top end gains are essential larger housing are essential. Selecting the power band of the engine is essentially dictated through the housing size, and the turbine physical characteristics.
-
Article: Why Horsepower doesn't matter...
For the last century, horsepower has been used to describe the power output of the internal combustion engine. The horsepower unit was created by James Watt in the 18th century. Its origin is based from how much power a horse could lift in foot pounds, 33,000 ft-lbs to be exact in one minute. The unit is derived from torque, which is the true measurement of the engine physical power production. What is strange about the units of horsepower is that it has no physical meaning. Its an arbitrary unit that has no real significance in describing the characteristic of the engine. For those that are curious to calculate horsepower: horsepower = (rpm/5252) * torque From this equation you can see that horsepower is nothing more than a contrived unit that is based purely from torque and rpm. You’ll notice the number 5252 in the equation, this represents the point at which every dyno graph must intersect horsepower and torque. Its a mathematical relationship, both strange and interesting since horsepower is a function of torque and rpm. There has been much confusion and rumors across the internet about gaining more horsepower. In essence, gaining more horsepower is gaining torque. If you are after “peak” horsepower, you are interesting in carrying the torque curve as high in the rpm range without falling as possible. You can see from the equation that as the rpm’s increase, and the torque remains the same you get a higher horsepower number. What physically is happening is that the engine is able to produce enough torque to overcome frictional forces through the air, tires, etc. As you are able to keep the torque from falling off on the top end, you are able to maintain a steady torque curve that will “pull” the car through the mph you are trying to reach. So people who are after “peak” horsepower really want to extend their torque curves as far towards redline as possible, without letting the torque fall off. Check out some dyno graphs and see what I mean. Horsepower doesn't describe the true nature of how the engine performs, its the torque curve. From a tuners perspective, I don't tune off of the horsepower curves. The physical relevance towards the engine performance is arbitrary, since the torque is truly what is effected by the fuel, timing, breathing, etc of the engine. The horsepower is merely a concocted unit of measure, showing no true characteristics of the engine power output. A good tuner will only make changes from the torque curves, see what increase/decrease the curves show from the changes. So next time you are thinking horsepower, think “what would I want my torque curve to be”?
-
Article: Turbochargers - A/R, Trim, and Flanges
What is an A/R ratio and how is it calculated?: The A/R in a relationship that is obtained when dividing the interior area of the turbine where the inner walls are found, through the turbine housing radio from the center to the tongue as the illustration indicates. A/R values are expressed as .35, .47, .68, .84, 1.00, 1.15, etc. A small A/R indicates a small interior volume in the small turbine and a large A/R indicates a greater volume. At a minimum A/R the motor's response is produced at small revolutions per minute but at high revolutions we will not achieve an adequate caudal. We should always find a compromise between achieving the lowest response possible and have enough caudal at high revolutions. The picture below is for reference: As stated, the turbine housing A/R is the cross sectional area of the turbine housing divided by the distance from the center of that cross section to the center of the wheel. This makes sense if you look at the graphic. If you take for example, the area in A1 and divide it by R1, you will have found the A/R for this turbine housing. Each cross section and radius have the same proportions so the A/R will be found by using any cross section/radius. What is the Trim of a turbo and how is it calculated? Each turbine wheel y compressor wheel model generally have the same turbine diameter (highest diameter), but different steps (lowest diameter). Each type of step (trim), has different blowing characteristics. [*]TRIM values are expressed as 45, 50, 55, etc... and can only go from 0 to 100. A value of 100 means Dp = Dg [*]A large TRIM indicates a large turbine diameter. [*]A TRIM of 55, gives 10% more caudal than a TRIM of 50. [*]TRIM is used in the same way for turbine wheels as for compressor wheels. [*]TRIM is calculated through the following formula. TRIM = ( Dp / Dg )² x 100 Si Dg = 50 mm y Dp = 35 mm TRIM = ( 35/50 )² x 100 = 49 What are the different flanges and what are the sizes? [*]All most all of your turbo head units come with the flanges described below. The T3 housing is the smallest and flows the least, with the T6/Thumper flange being the biggest and flowing the most. The flange plays a role in spool up, backpressure...etc. The rule of thumb here is use the largest flange you can possibly fit. Of course this will be limited by what headers you use, since most are pre-fabbed and come with a flange already, and under hood space will also be a limitation. [*]Basic T3 [*]Basic T4 [*]Basic T6