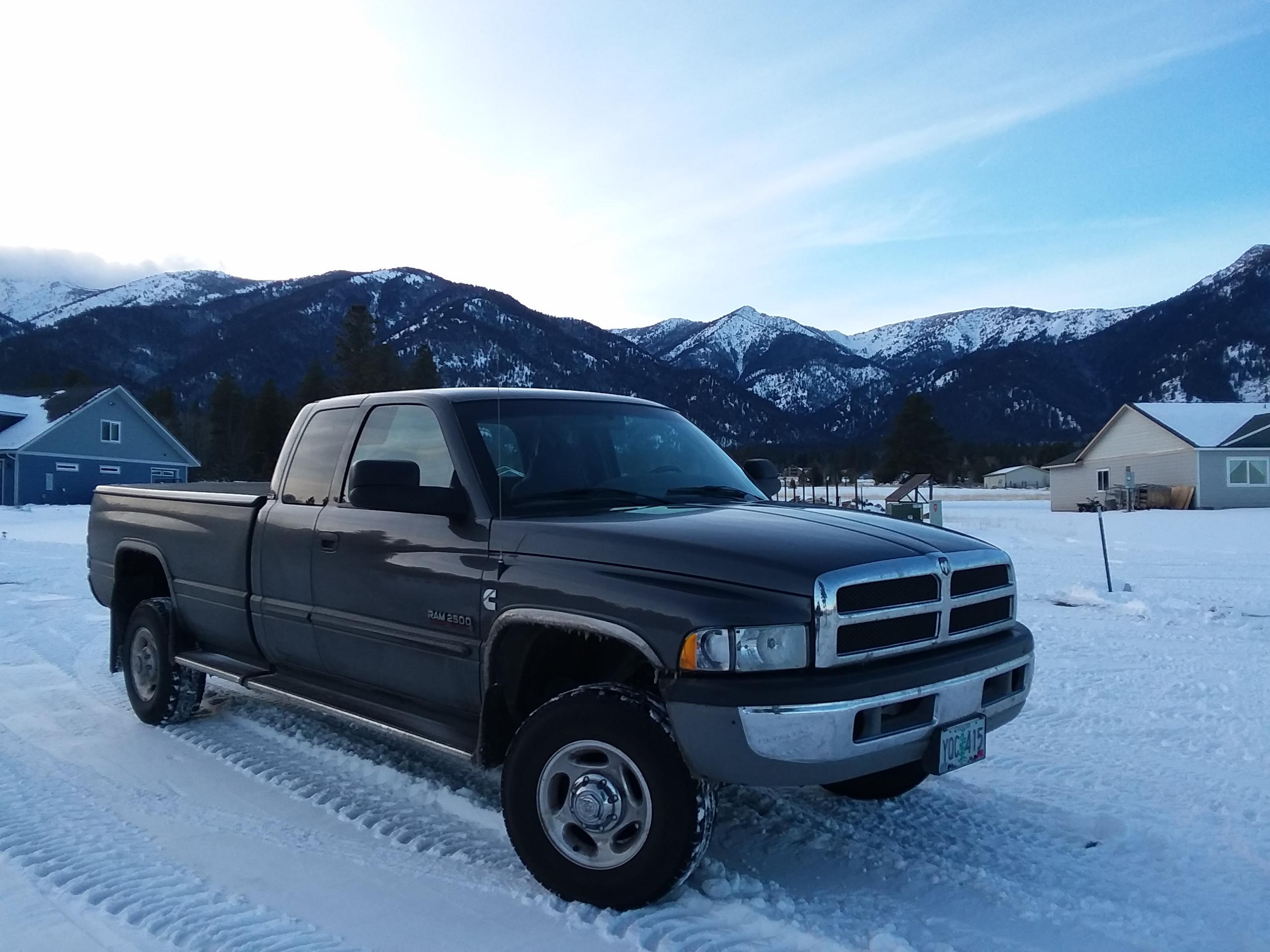
Everything posted by Tractorman
-
Smarty s03 today :)
What ? Are you saying my truck's retarded? (attempt at humor). I understand what you are saying about the limitations of the Smarty S03. On a different subject, is the screenshot in your photo the actual display you are looking at while driving down the road? If so, what is the size of the screen? - John
-
Smarty s03 today :)
@Evan, it is good that you have read @pepsi71ocean's Smarty S03 article. Another good read, if you haven't already done so, is @Tittle Diesel Performance's posts regarding what a Smart S03 representative told him. Two important items: 1. He lists the default Revo settings (torque management, timing, and fuel duration) for each software setting (SW1 through SW9). This makes for a good reference point when deciding which Revo settings you want to change, which direction you want to go, and which settings you will leave default. 2. If all Revo settings are left to default, the software in general increases torque, advances timing, and increases fuel duration progressively from SW1 through SW9. But, if you select a Revo number in either Torque Management, Timing, or Duration that is not Default (0), then those parameters stay the same regardless of software number (SW1 through SW9). My truck has a manual 6 speed transmission and the engine has RV275 injectors, so tuning for me is much more simplified and using the information from @Tittle Diesel Performance's posts, the software settings I have tried seem to agree with that information - at least for my truck. I believe @pepsi71ocean has had a different experience. Your truck seems to be a closer match to @pepsi71ocean's truck. It seems that with automatic transmissions and large injectors, the transmission shift points can be greatly affected with different Smarty settings which masks what is really going on at a particular setting. This would definitely make it harder to tune the truck. These are only observations from my point of view from reading different posts, as I have never tried to tune a truck with an automatic transmission. - John
-
Fuel transfer pump relocation
A few years ago I bought a used FASS lift pump and mounted it onto one of the rear cab mounts right at the front of the fuel tank. I just stayed with the factory lines and it was easy to tap into the fuel lines on the inside of the frame. I also installed an in-line fuel strainer (Napa 3270) on the inside of the frame between the tank and the lift pump. - John
-
PDC
@dripley, I checked where the power for the lift pump relay contacts come from on my truck. As you suggested, it comes from the battery connection at the PDC. A short distance away is a 15 amp in-line fuse. @Daleb, I can't remember if you mentioned where your lift pump gets its power, so if you haven't checked, it would be a good thing to verify. If the power for the lift pump is tapped into an existing circuit, the additional lift pump current could easily overload that circuit. Ideally, the lift pump should be fused and relayed from the PDC and the coil portion of the relay triggered by the ECM. - John
-
High Beam Indicator Stuck On
Since you said that you just purchased this truck, do you know any history about the truck - particularly the headlight system. * Are the headlights still OEM? * Is there one 9004 bulb for each side? (one bulb per side system) * Is it a sport headlight system? (t2 bulbs per side system - 9007 bulbs for 2 outside lamps and 9004 bulbs for 2 inside lamps) * Does the truck have fog lights? If anyone has modified the headlight system, I would start my troubleshooting there. - John
-
PDC
@dripley, when my first VP44 failed 64,000 miles and was replaced at 87,000 miles, it was replaced under warranty along with the lift pump and the associated wiring. At that time the factory fix was to install an in-tank lift pump and to relay that lift pump. The coil portion of the new relay was triggered by the ECM, but I don't know where the power source comes from for the relay portion that actually operates the lift pump. I was wondering if you might know. I think I might have to do some investigating - John
-
PDC
If the headlight wiring is OEM with a factory one bulb per side system, then all of the headlight controls (headlight switch and dimmer switch) use the ground wiring side of the bulbs to switch the headlights on and off. The headlights are fed by a hot lead. Does your truck have fog lights? I am assuming your headlights were working normally before your problems with Joint Connector #2. Try the following: * Leave the key switch off and operate the headlight switch. The low beams and high beams should operate normally. If they don't, operate normally, then I would start my troubleshooting here. * If the headlights do operate normally with key switch off, then I would be looking for something powered by the ignition switch circuit that is switching the ground side wiring for the headlights to ground. Sometimes when I am troubleshooting electrical problems I like to prove what is working correctly rather than trying to come to a conclusion that I can't prove. For me, it is a process of elimination. - John
-
Head gasket replacement
Good thinkin'! - John
-
Oil from breather tube
The two times over the life of my truck that I noticed the breather tube was messier and leaked more oil than normal, I had a vacuum leak. Neither time was the vacuum leak large enough to noticeably affect vacuum operated controls, but the excessive air flow showed up through the breather and added to the mess. Each time I repaired the vacuum leak the breather began venting normally again. - John
-
How do you clean your engine bay?
I use the treated wipes the guy hands me at the car wash for interior cleaning. They are white so I can see when I wipe off a dirty spot on the engine. - John
-
PDC
If I understand correctly, that junction connecter supports a few fused circuits and some other circuits. I don't see anything stopping one from bypassing just one damaged circuit and leaving the rest intact, just as long as the new circuit has the proper size fuse and wire gauge. - John
-
Head gasket replacement
I figured you did know that, just thought it worth a mention. I am glad that the miss was something simple - you probably had all sorts of things going through your head on that test drive, and none of them good. When I was in my late twenties, I owned a mobile auto repair business for a few years and many times I found myself working in less than desirable weather conditions; so I hope you are feeling good about what you have accomplished working in the elements under the canopy. - John
-
Head gasket replacement
The pushrod absolutely needs to be straight, as it rotates constantly while in operation to ensure uniform wear on its mating surfaces on both ends. - John
-
PDC
Sounds like there might be a trend here - thanks for the heads up... - John
-
Head gasket replacement
It doesn't sound like the intake valves were held open - that's good. Were you able to rotate the afflicted pushrod to see if it is still straight? If the pushrod is straight I think you are good to go. The raw fuel symptom makes sense - no fresh air entering the combustion chamber. - John
-
Head gasket replacement
I don't know you that well, so I would never treat you like others do. When you are done, are you going to put the roof back on the chicken house? - John
-
PDC
I understand that you are very concerned that the event won't happen again - I would be concerned, too. A poor ground at a single connection that combine multiple circuits could cause electrical components to randomly not operate properly. Heat could build at the poor ground connection, but I don't think it would cause heat to build in joint connector #2. There could be two ways for heat to build in joint connector #2. 1. If the connection in joint connector #2 was corroded or cracked, then normal current flowing in that circuit could generate enough heat to damage the connection. 2. If higher than normal current was flowing in that circuit, but still less current than the properly rated fuse, then heat could be generated anywhere in the weakest part of the circuit, including joint connector #2. Since there are multiple connections in joint connector #2, you could re-inspect the damaged connector to find out exactly which wires were involved. Then you would only need to inspect the wiring and components downstream from the damaged connection. Also, you should make sure nobody has added an additional electrical load to that circuit. - John
-
PDC
The bad ground is a good find on your part - it definitely needs to be addressed. Can you expand on why you think this bad ground caused the meltdown in joint connector #2? - John
-
PDC
@Daleb, I am not sure of what you are trying to accomplish and I think that you may be chasing your tail here. Are you still trying to find a short to ground? I ask because I don't think a short to ground exists. Are you trying to figure out why joint connector #2 failed due to heat? If you are, I think I covered that in my previous post - basically, that a poor connection (in this case, joint connector #2) in a properly operating circuit can cause enough heat to destroy that connection. A test light can be a valuable tool for troubleshooting. But, if the circuit being tested is not fully understood and / or if the testing tool limitations are not fully understood, then the test results can be useless. Most test lights draw very little current, probably about 250 milliamps on average. There are control modules on your truck that draw more than 250 milliamps (combined) after the ignition switch is turned off. These modules will continue to draw power that will easily make a test light glow for a up to a few minutes after the ignition switch is turned off. Even when the modules finally go to sleep they can still draw up to a combined total of 35 milliamps, enough to make a test light glow dimly. Different levels of trim on a truck can affect the number of control modules a truck has, as well - for example, a truck with a security system and a premium sound system will have more control modules than a base model truck (like mine). Electrical problems can be frustrating, but sometimes I get so involved that I can be my own worst enemy. - John
-
Head gasket replacement
Looks like you might be one of those one million mile guys not to far in the future. I don't know if I will live long enough to accomplish that with my truck - I just recently cleared 300,000 miles. - John
-
Head gasket replacement
We will be looking forward to hearing it run... How many miles on your truck? You may have already said and I just don't recall. - John
-
Head gasket replacement
Actually by just following the procedure, you have already reduced compression on the head gasket on the first fasteners when you have completed the first round of torqueing to 77 ft/lbs. - John
-
Head gasket replacement
Back to @dripley's first post regarding the head bolt torque procedure. I am sure he wants to know the correct procedure - I would, too. Although service manuals are a great resource for making a quality repair, sometimes clarity is lacking in instruction, or sometimes words or phrases are used that have different meanings for different people. When I am in doubt, I like to approach things from a fundamental point of view - in this case, the point of view of a fastener. The purpose for applying a specified torque value to a fastener is to make sure the fastener maintains its designed clamping force for a long time during normal operations when vibrations and thermal expansions / contractions are occurring. A fastener can be brought to 77 ft/lbs of torque in a dynamic state. If a person wanted to increase this torque to 82 ft/lbs of torque from a static state, then the person may find that the fastener does not move when 82 ft/lbs of torque is applied. This is the result of static friction. If the fastener does not move with 82 ft/lbs of torque applied, it is still holding a clamping force of 77 ft/lbs . It is kind of like trying to slide a heavy box on a smooth floor. It takes more force to get it moving than to keep it moving - static vs. dynamic. The following example is hypothetical and I make certain assumptions for clarity: In the case of installing a head, the fastener is to be clean and lightly oiled to ensure a uniform clamping force for each of the fasteners when tightening the fastener to a specified torque. * First, all fasteners are brought to 77 ft/lbs of torque using the proper torque sequence. At this point, the first fasteners that were torqued will have lost some of their clamping force. These fasteners will not be "loose", but for sure, their clamping force will have been reduced somewhat at this point. Procedure A: If the same 77 ft/lbs of torque is re-applied in the same sequence order, the first two or three fasteners may turn because the static friction is overcome by the 77 ft/ lbs of torque being applied. These fasteners will torque properly because they are in a dynamic state when 77 ft/lbs is reached. The next fastener may not move when the torque of at 77 ft/ lbs is applied. It could very well be that this fastener's real clamping force value has been reduced to 70 ft/lbs of torque, but static friction will not allow the fastener to turn with 77 ft/lbs of torque applied. This fastener will maintain its clamping force of 70 ft/lbs of torque. Procedure B: Starting in the same torque sequencing order, if each fastener (one at a time) is loosened only enough to allow for a dynamic torque to 77 ft/lbs to be applied, then each fastener will have a more uniform clamping force. Procedure B will have a more uniform clamping force for each of the fasteners before the final 90 degree turn of the fastener. I am sure that either procedure will work fine, but I just wanted to show that the results will be different and why the results will be different. One of the great benefits of this forum is that we can gather valuable information and use that information to suit our specific needs. @dripley, what I would do in your situation is just use a cordless drill on the maximum torque setting and run all of the bolts down and call it good. And be sure to re-check them. - John
-
Head gasket replacement
The FSM is not clear as to exactly how to perform this particular procedure, but I understand what @AH64ID is saying. If you truly want to have the most uniform clamping force throughout the head, then backing off each bolt and re-torqueing to 77 ft/lb will achieve that. From the FSM for my 2002 truck: (a) Torque bolts to 80 N·m (59 ft. lbs.) (b) Torque bolts to 105 N·m (77 ft. lbs.) (c) Re-check all bolts to 105 N·m (77 ft. lbs.) (d) Tighten all bolts an additional ¼ turn (90°) - John
-
New Injectors?
I just switched to RV275's about 6,000 miles ago (303,000 miles on the OEM injectors). They perform well for me. I have never heard of any negative comments about the RV275 injectors. I think there are others on this forum who have run the RV275's and different injectors on the same truck, as well. You will probably be hearing from them soon. I use the SO3 Smarty programmer - the RV275's and the programmer work well together. My truck is a daily driver and is used for towing. - John