- Replies 20
- Views 3.6k
- Created
- Last Reply
Top Posters In This Topic
-
Silverwolf2691 6 posts
-
Great work! 6 posts
-
Mopar1973Man 5 posts
-
Dieselfuture 1 post
Most Popular Posts
-
Man this is some in depth stuff here!!! Gosh I wish I knew all this; or what you were even talking about
I am working on a home made PSG unit and needed to know the min and max absolute timing.
So I improvised a degree wheel and blew back into the #1 port with the pump shaft key way centered
with the mark on the front of the pump by the seal. I could blow back about 30 deg before and 30 deg after
which is +60 and - 60 at the crankshaft. I noticed that the port starts to close up about 3 degrees sooner
because of the port hole width. There is also about 1 degree of overlap where two ports are very slightly exposed.
I then measured the rotor, slot and ports then did the math and it confirmed my findings. So never try to inject past ~54 degrees either before or after top dead center.
o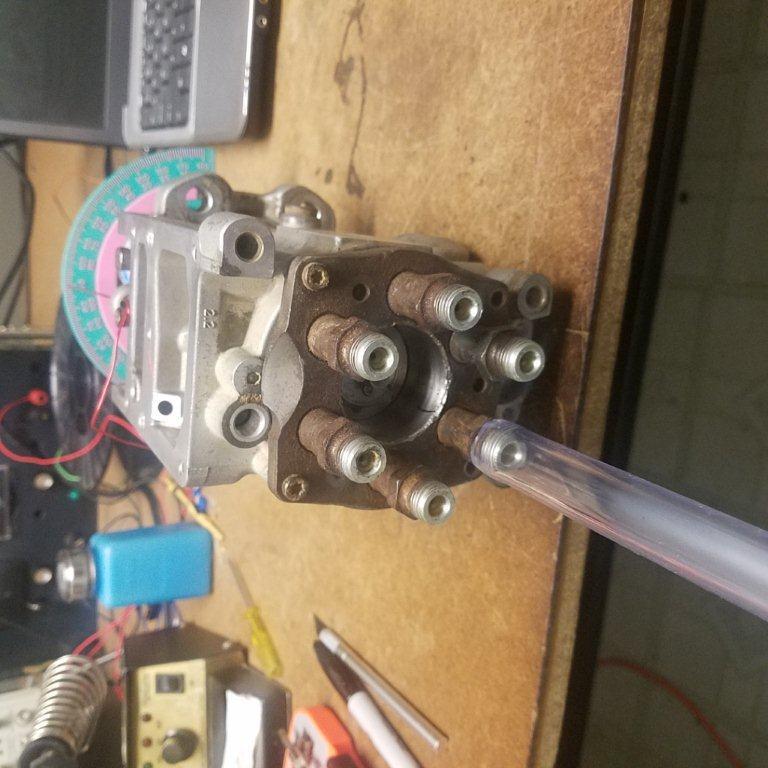