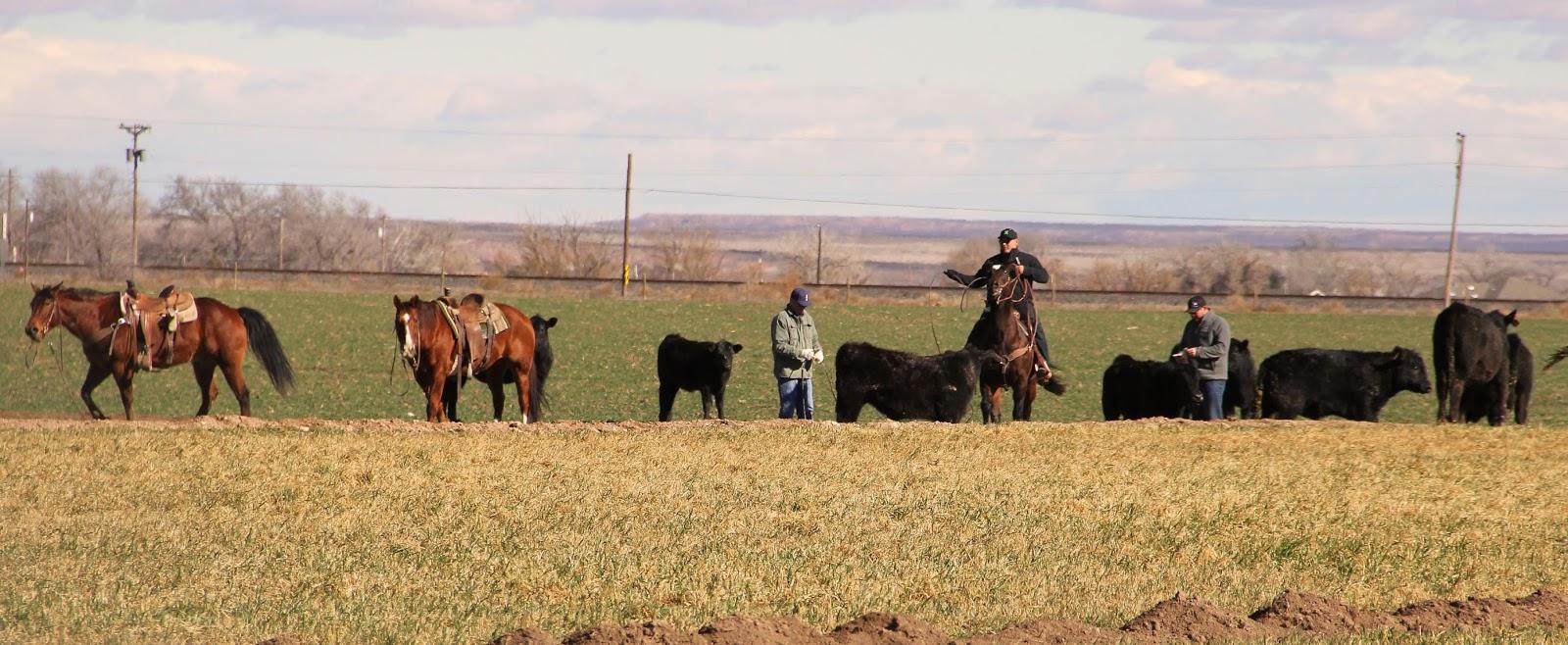
Everything posted by Rogan
-
Compressor Efficiency and Temperature
The author of this article is a turbo engineer for Garrett. I'm submitting it because it is an informative read and therefore is beneficial to the community. Enjoy. Compressor Efficiency and More by Khiem Dinh Compressor efficiency is a term thrown around whenever people mention forced induction, but what does it really mean? How does it affect an engine's performance? And what role does air temperature play in all of this? The cool thing about thermodynamics is that we can explain effects with equations. Using basic compressor equations, we'll put some numbers to the affects of air temperature and compressor efficiency on compressor power requirements and air temperature increase. Some fundamental compressor equations are below. I like working in SI units because doing calculations with English units sucks! So, mass flow rate is in kg/sec, the average constant specific heat value for air I used is 1.007 kJ/kg*k, and k for air is 1.4. The specific heat of air actually varies with temperature, but the change is basically nothing within the range of temperatures we're using, so I'm assuming a constant value. After calculating all the values in SI units, it is a simple conversion to English units. The table and chart I generated assumes: air inlet temperature of 298K/24.85C/76.7F, and 100% compressor efficiency (isentropic compression). Looking at the chart and table above, it becomes very obvious that increases in mass flow rate and pressure ratio require more power. Also, the graph shows lines of constant power. For a given compressor power, you can get a lot of flow and little pressure ratio, a lot of pressure ratio and little flow, or somewhere in the middle. To get a feel for what the numbers mean in the real world, we'll use 2.0L 4-cylinder engine as an example. Automotive engines of this displacement and cylinder count will make roughly 500hp with a mass flow rate of 50lbs/min and a pressure ratio of 2.75, or about 25psi of boost. Looking at the table, a 100% efficient compressor would require 51.1hp! Looking at the compressor map for a GT3076, it shows a compressor efficiency of ~72% at this point. So the actual power requirement becomes 71hp. A GTX3582 has a compressor efficiency of 77% resulting in a power requirement of 66.4hp. That extra hp required over a 100% efficient compressor ends up as extra heat in the air. More efficient is better! The other variable in the equation that's very important, but many people seem to neglect in the practice of building turbo cars, is the temperature of the air going into the compressor. Many people have the misconception that performance is unaffected because the intercooler will cool the air enough regardless of the air temp going into the turbo. What they are neglecting is the fact that compressor performance improves with cooler air. Said another way, it gets worse with taking in hotter air. Using values of 50lbs/min and a PR of 2.75, the table below shows compressor power required, change in temperature of the air (Delta T), and the exit temperature of the air based on the inlet temperature of the air. Hotter air in equals mo' hotta air out! Takes more power too. Translation? Laggy turbo. Notice that the hotter the air going into the compressor, the more power is required to compress it. Also, the increase in the air temperature is greater. Of course, this results in the final temperature being even hotter. I think comparing air inlet temps of 77F and 122F is reasonable; 77F being ambient air temp and 122F being the temp if you ingest air from the engine bay. So by sucking up the hotter engine bay air instead of cooler air from the front of the car, the compressor power required increases by 4.3hp, or about 8%. The difference in the temperature coming out of the compressor is a toasty 60.1F making the intercooler work that much harder. Of course, there's no such thing as a perfect compressor, so let's see what happens with a 60% efficient compressor; this is often where the tuner industry operates as they try to squeeze as much power as possible out of turbos. Looking again at 77F and 122F inlet temps, the power and temperature differences are now 7.1hp and 70.2F! Crappy compressor efficiency means supa dupa hotta air! You could boil an egg on it. Mo' laggy too. So now we know how crappy compressor efficiency and sucking in hot air increase the power required of a compressor to move and squeeze air. But where does that power come from? A supercharger gets it off the crankshaft of the engine and a turbocharger uses a turbine wheel in the exhaust. If you go by old school nomenclature, what we call a turbocharger was referred to as a turbo supercharger. So basically a special type of supercharger with a turbine wheel to get work out of the exhaust. Anyways, we like turbos because they use otherwise wasted energy. Going back to the very first chart, a perfect compressor doing 100lbs/min at a pressure ratio of 4 would need almost 150hp. Given the option of taking that from the engine crankshaft or the exhaust energy, we'll take the exhaust energy. That's the reason why pretty much every diesel engine and the majority of gasoline engines use turbos instead of superchargers. So does the turbo engine make 150hp more than the supercharged engine? The answer is no because the turbine wheel and turbine housing create back pressure in the engine reducing its volumetric efficiency. But a turbo engine will still make significantly more power than a supercharged engine given the turbo is properly sized. Sizing of the turbine wheel is important so as to get the maximum efficiency from it. Our worst case scenario of the 2.0L engine, 60% efficient compressor, 50lbs/min mass flow rate, 2.75 PR, and 122F air inlet temperature requires 92.4 hp of shaft power from the turbine to drive the compressor wheel. A 100% efficient turbine wheel would need to get 92.4 hp worth of energy out of the exhaust. However, like compressor wheels, there’s no such thing as a 100% efficient turbine wheel. Throw in some moderate turbine efficiency and you end up needing a lot of exhaust power to spin a compressor. Plugging in a value of 60% for turbine efficiency, we can see how much energy needs to be pulled from the exhaust based on the temperature of the air going into the turbo. The difference in power required going from 77F and 122F is a lag inducing 11.9 hp, or about 8%. So what have we learned? Maximizing compressor and turbine efficiencies reduces the exhaust energy required to get a turbo going. Sucking in colder air instead of hot air also makes compressors happy. The final conclusion to all of this is that math is cool, stay in school!
-
G56 rattles horribly after switching to a dual disk clutch and SMF
LOL Stroke ain't killed me, yet..
-
G56 rattles horribly after switching to a dual disk clutch and SMF
I've been googling and found that A LOT of people have complained about this. Seems no one has found a 'fix' for it. $60+/gal fluid is a common theme, so I tried it.. Absolutely no real change. Maybe a decibel or two in reduction, but nothing all "OMG this is so much better" that such a costly fluid should bring to the table.. The removing of any slack (by pressing the shifter a little) is understandable, as it quietens it to nill, but that's not a fix.. By the way, @Mopar1973Man, you still , as I am?
-
G56 rattles horribly after switching to a dual disk clutch and SMF
Thanks, Mike. A lot has changed here, that's for sure... Well, the 06 would've had a NV5600, correct? The G56 is a different creature, but the principles are the same. I've read where 'gear rollover' noise increase is common in the G56, but this is nuts. Everything works fine, shifts fine, engagement is fine.. Just this horrible rollover. And like I said, slightly adding pressure to a shift-gate stops all of it. I know the G56 has brass or bronze fork pads, rather than Delrin or the likes.. I'r afraid I may end up going inside the G56 before too long..
-
G56 rattles horribly after switching to a dual disk clutch and SMF
Good morning, all, and hello old friends 2008 2500 with G56 trans. Changed to a SMF and DD clutch. After doing so, I get horrid "gear rollover" in neutral, as well as in gears. In neutral, no clutch depressed, it's quite noisy. If I slightly push the shift lever towards a gear, it immediately goes quiet. Does this at all gear positions. If I let the shifter rest, it's quite noisy again.. Anyone experienced this? I mean, I understand there'll be 'gear rollover' when going from DMFW to SMFW, as the vibration transmitted is increased a little, but this is nuts.. Thanks.
-
Ultra Low Sulfur Diesel 101
Ultra Low Sulfur Diesel 101 (ULSD Diesel) Emissions Standards Continue to Tighten You may have heard that The U.S. Environmental Protection Agency has adopted a tough set of diesel emissions standards aimed at drastically reducing the sulfur content of diesel fuel to improve air quality. A good thing indeed. To meet those standards, petroleum refiners are producing Ultra Low Sulfur Diesel (ULSD) or S15, a cleaner diesel fuel that has a maximum sulfur content of 15 parts per million (ppm). When the full retail phase-in is complete, this fuel will be a direct replacement for Low Sulfur Diesel or S500 (which has a sulfur content of 500 ppm) culminating in more than a 95% sulfur reduction. In a move similar to eliminating lead from gasoline to protect catalytic converters, sulfur reduction in diesel fuel is necessary to preserve the proper function of the advanced emissions control systems on new diesel engines. The combination of this cleaner burning fuel and the sophisticated emissions devices on the new engines will result in more than a 90% reduction in soot and oxides of nitrogen. Look for the Label Beware 2007 vehicle owners: Not all retail outlets (excluding California) are required to offer ULSD fuel until December 1, 2010. For a period of time, through this transition period, some fueling stations may not have ultra low sulfur diesel (ULSD) available. The pumps must have a label stating that they dispense ULSD, so if the label isn't on a pump, don't put the fuel in your 2007 vehicle—severe damage to the emissions control systems could result. Find a station that has ULSD to fill your 2007 vehicle. Please note, however, that all diesel fuel in California was transitioned to ULSD by September 1, 2006, and no labeling is required. But Can I Use ULSD in My Older Diesel vehicle? All 2007 and later diesel vehicles sold in the U.S. for on highway use will be required to use ULSD. No problem here, these engines are designed to run on this fuel. But what about older engines—engines that were designed to run on Low Sulfur Diesel (S500) or its very early brother, S5000? The argument here certainly isn’t in defense of higher sulfur fuel—its many drawbacks are quite evident. But sulfur in the fuel enhances lubricity, and older engines depend on it to protect their pumps and injectors from premature wear. To combat the loss of this lubrication, packages of additives that increase lubricity will be blended with the fuel prior to distribution. Biodiesel to the Rescue While synthetic additives will initially fill the role of lubricant, there is plenty of room for development of biodiesel blends that can easily handle the task. Because of its vegetable oil base, biodiesel contains no sulfur and has a very high lubricity factor. These two qualities make it an ideal candidate for blending with ULSD to solve the problem of lubricity while keeping the sulfur ratio intact. Stay tuned. Biodiesel started out as a niche fuel touted mainly by environmentalists and the agriculture industry, but it is proving to be quite useful as an additive as well as transitional fuel while cleaner alternatives continue to be developed. For it pure versatility—as a straight fuel, and as a multifaceted additive—biodiesel has certainly earned its stripes. Clearly the advantages are compelling, but as with any transition from one technology to another, there are hurdles to be cleared. Mainly it boils down to logistics. It will take time to develop the blends that perform well under various conditions (cold flow characteristics, adequate lubricity, fuel efficiency) and to get the blends into the infrastructure pipeline. Cold Weather Considerations The refining process used to attain the sulfur ratio of ULSD affects the naturally occurring paraffins (wax) inherent in diesel fuel in such a way that can cause the fuel to gel more readily in cold temperatures. Though most retail fuel should be properly winterized for your local climate, some testing and experimenting with additional treatment processes will probably be in order. Higher doses of anti-gel additives may be necessary for extremely low temperatures—and not all additives that have traditionally been used for treating conventional low sulfur diesel will be compatible with—or effective on—ULSD. Keep the Following Points In Mind: First look for packaging labels that indicate compatibility with ULSD. Secondly, be aware that mixing conventional low sulfur kerosene with ULSD as a flow enhancer will increase the sulfur ratio and could damage emissions control equipment. Finally, even in cases where it is available—cutting ULSD with ultra low sulfur kerosene may be ineffective as a flow enhancer.
-
Tire, Gears, MPH, and RPM
Tech: Tires, Gears, MPH and RPM A common 4x4 application is an upgrade to larger-than-stock tires. Once completed, this change immediately alters vehicle speed at a given rpm, rpm at a given speed, and effective gear ratio, which in turn affect both acceleration and fuel economy. Tire size, gear ratio, mph and rpm weave an intricate pattern of performance. Change one and all four are affected.; knowing any of the three, the fourth can be easily determined. The following four formulas illustrate the point: Tire diameter = ((MPH x Gear Ratio) x 336) / RPM Gear ratio = ( rpm x tire diameter) / (Mph x 336) Mph = (rpm x tire diameter) / (Gear ratio x 336) Rpm = ( (mph x gear ratio) x 336) / Tire diameter If you are contemplating a tire size upgrade and know your rear-end gear ratio, you can measure your tire size and observe rpm and mph, you can calculate what gears are in your axles. How To Calculate Actual Speed: With the change to taller tires, your speedometer will real "slower" than the actual vehicle speed. To determine the percentage of speedometer error, the formula is a simple relationship between old and new tire diameters. Actual Speed = (new tire diameter x indicated speed) / Old tire diameter Example: You’ve replaced your 30-inch OEM rubber with a new set of 35-inch all-terrains and you want to know your actual speed when the speedo reads 60 mph: (35 x 60) / 30 = 70 mph Speedometer ratio adjustment calculation Formula used (New Tire Diameter / Old Tire Diameter) * Speedometer MPH = Actual MPH Another way of looking at this relationship would be to figure what the indicated speed would be if you were actually going 60 mph. In this case, the tire diameter relationship is flip-flopped to: Indicated Speed = old tire diameter x actual speed / New tire diameter Using the previous example, your speedometer reading at an actual 60 mph is: 30 x 60 / 35 = 51 mph Gearing up: Using the above tire change as an example, lets say that your vehicle is currently running a 3.40:1 final-drive gear set. Now that you have changed to a taller tire, you want to determine the actual, or effective, final ratio. This can be figured by dividing the old tire diameter by the new, and multiplying by the current gear ratio (:1): 30 x 3.40 / 35 = 2.91:1 Dropping from a 3.40:1 to a 2.72:1 ratio will reduce off-the-line responsiveness and severely affect slow-speed trail capabilities. If your new 35-inch rubber is just what you want, but you now need to restore your vehicle’s low-end, the following formula will allow you to determine what gear set (equivalent) ratio should be installed to compensate: Equivalent ratio = new tire diameter x original ratio Old tire diameter Or, in this example: 35 x 3.40 / 30 = 3:85:1 By installing a gear set in the range of 4.25:1, you will not only restore your vehicle’s low-end responsiveness, you will likewise restore your speedometer’s accuracy. Figuring gear ratio: Knowing what gears are in a given axle is a must when considering that axle for a swap. The actual ratio or reference code, will normally be found on either a tag attached to a bolt, or will be stamped into the axle housing. If it cannot be found, there is a simple method for manually (and mathematically) determining the ratio for any axle installed on a vehicle. Raise both wheels of the axle, with the transmission in Neutral. (Make sure you support the vehicle with safety stands and block the front tires.) Make a reference mark on the driveshaft and on the differential housing. Next, without rotating them, make a mark on both tires and their respective fender wells. With a friend watching the driveshaft, carefully rotate both tires at the same time exactly one revolution. The number of turns the driveshaft makes will indicate the ratio. If the driveshaft rotates 4 ½ turns, for instance, the axle ratio is roughly 4.5:1. METRIC TIRE TO DIAMETER (INCHES) CALCULATION Formula used ((Section Width x Aspect Ratio x 2) / 25.4) + Rim Diameter = Tire Diameter Width in inches = section width / 25.4 Section Height in inches = Width in inches X Aspect Ratio (%) GEAR RATIO CALCULATION Calculating Gear Ratio For two standard round gears, the gear ratio is calculated by counting the number of teeth on each gear and dividing the number of teeth on the driver gear by the number of teeth on the driven gear. For example, a gear with 25 teeth drives a gear with 75 teeth. Dividing 25 by 75 gives you a ratio of 3/1, meaning that for every three rotations the driver gear makes, the larger gear turns once. Formulas used (RPM x Tire diameter) / (Diff Ratio x Trans Ratio x TCase Ratio x 336) = MPH and (Trans Ratio x TCase Ratio x Axle Ratio) = Crawl Ratio Definition of Gearing Ratios In the automotive industry, gear ratio refers to the difference between the input and output speed of a differential or trans-axle. The purpose of the gear ratio is to give the best combination of performance and economy for a given engine size and vehicle weight. Some gear ratios are designed to operate outside of this condition, such as those used by hot rods in drag racing. Function 1. In the simplest terms, a gear ratio is the difference in size between two gears that have the same tooth spacing. One common ratio is the 4.10 gear ratio used in heavy-duty pickup trucks and drag-racing cars. This ratio is considered "low-geared"; for every revolution the larger gear (attached to the axles and wheels) makes, the small gear (attached to the drive shaft) makes 4.10 turns. This gear reduction gives increased power at the expense of top speed and fuel economy. An example of a "high-geared" ratio would be 2.62, where the large gear that drives the wheels turns once every time the drive shaft gear turns 2.62 times. Effects 2. The effect of the gear ratio is to convert rotational energy--in this case coming from the drive shaft--to a desired level of energy at the wheels. The gear ratio does not increase horsepower; it merely changes how it is used. A lower ratio offers greater power while sacrificing top speed, whereas a higher ratio offers greater top speed with less power. Gear ratios also affect the vehicle's fuel economy. A higher gear ratio offers greater fuel economy on the highway, and a lower ratio will be less efficient. This is because the higher a gear ratio is, the fewer revolutions the engine has to make to achieve a desired speed. Since one of the things that affect fuel economy is engine RPM, fewer revolutions per minute use less fuel. History 3. Gear ratios have existed since the first wooden gears were created. They were in use in applications such as windmills, where the weak rotational energy from the blades of the windmill was made usable by through slower speeds that turned a large grinding stone. Some uses predate even this. One of the simplest ancient gear ratios involves the well-bucket winch. A wooden cylinder with a handle was used to wind a rope and pull the bucket full of water up to the operator. This is an example of gear reduction, where ease of use was preferred to speed. Considerations 4. Gear ratio changes to a vehicle can change seemingly-unrelated aspects of vehicle operation. For example, changing the gear ratio of most vehicles will cause the speedometer to register inaccurately. The gear that drives the speedometer cable is sized according to the gear ratio. This gear must be replaced to ensure accuracy of the speedometer. One of the most frequently overlooked gear ratio changes occurs with changes to tire size. While a tire is not a gear, changes to its diameter have the same effect. Putting larger tires on a car effectively increases its gear ratio, costing power and gaining fuel economy, whereas smaller tires increase power but reduce fuel economy. Tire size changes also affect speedometer accuracy. Benefits 5. Changing the existing gear ratio can be highly beneficial if done to meet specific needs. For example, a large farm truck, or a truck used to pull a boat or trailer, can benefit from a lower gear ratio. The increased performance when stopping and starting, or going up hills, may easily outweigh the loss of fuel economy. The same is true for sports cars used in drag racing. A lower gear ratio gives more power to the wheels, at the cost of top speed; occasionally drag racers will benefit from a higher ratio, trading excessive wheel power for rotational speed. This depends on the weight of the car and the horsepower available. Many times the ideal ratio for a particular race car is not the ratio that the differential came with. As a 'general' rule of thumb, choose green to stay close to factory gear ratios, yellow for better economy and highway usage and red for better off road capabilities. What's in a Ratio? An automobile uses gear ratios in both the transmission and the drive axle to multiply power. The two ratios multiplied together equal the final drive ratio. Spend a few minutes in any bench-racing session and soon you'll hear rear axle gear ratios discussed. For many performance cars, 3.73s and 4.10s are common gear choices. The rearend gear ratio refers to the relationship between the ring gear and the pinion gear. By simply dividing the ring gear tooth count by the pinion gear tooth count, the ratio is determined. For example, if we divide a ring gear with 41 teeth by a pinion gear with 10 teeth we find that the gear ratio is 4.10:1 (41/10 = 4.10). Tire diameter will also have an effect on a vehicle's final drive ratio. As tire diameter changes, so will engine rpm at a given speed. We can demonstrate this with the simplified formula: rpm = (mph x final gear ratio x 336*) / tire diameter (*see "Formulas for Success" sidebar). For example, given 65 mph, a tire diameter of 30 inches, and a final gear ratio of 4.10, the engine speed will be approximately 2,984 rpm--(65 mph x 4.10 final gear ratio x 336) / 30-inch diameter tire. If we reduce the tire diameter to 25 inches, the engine speed increases to 3,581 rpm. By installing shorter tires, the vehicle will accelerate as though it has a 4.73 (higher numerically) gear without the expense of gear swapping. Because transmissions are comprised of several gear choices, the transmission allows the vehicle to accelerate quickly with lower gears and to maintain a cruising rpm using higher gears. In the '60s and '70s, most transmissions offered three or four gears with a 1:1 high gear. Using a TH400 as an example, First gear is 2.48:1, Second gear is 1.48:1, and Third gear is 1:1. Multiplying the 2.48 First gear by the 4.10 rear axle results in a final drive ratio of 10.16:1 (2.48 x 4.10 = 10.16). For most street performance applications, a 10:1 final First gear ratio is usually considered optimal. The disadvantage of operating a 4.10:1 axle ratio on the street with a 1:1 high gear is excessive freeway engine speed. Fortunately, today's transmissions frequently utilize Overdrive high gears in the neighborhood of 0.70:1, which allow reduced engine speeds. Combine these overdrive transmissions with a 4.10 axle ratio and you have a fuel-friendly final drive ratio of 2.87:1 (4.10 x 0.70 = 2.87) in high gear. A TH200-4R overdrive automatic utilizes a First gear of 2.74, a Second of 1.57, a Third of 1.00, and a 0.67 Overdrive. With this transmission's First gear ratio of 2.74 combined with a 3.73 axle ratio, the final drive ratio >> yields a 10.22 (2.74 x 3.73 = 10.22). In overdrive, the final drive ratio equates to a Bonneville-ready 2.49:1. Making Torque Multiply Acceleration is all about torque. One way to accelerate more quickly is to multiply the torque at low speeds to help move the vehicle forward. That's what a torque converter does. The torque converter features a component called a stator. The stator changes the direction of oil flow to the pump impeller's rotating direction and also incorporates a one-way clutch assembly. This redirection of fluid increases torque by applying the energy remaining in the oil. By applying the basics of gear ratios and power leverage, you can easily improve acceleration without paying too steep a price in highway rpm. It's all in the ratios. The Numbers Game Choosing the proper gear ratio can give your car the performance you want. Remember, acceleration depends on torque. Engines that produce more torque generally require less gear for optimal acceleration. Tire diameter plays a big role in the final drive ratio and engine rpm. Shorter tires increase engine rpm and are sometimes an economical way to improve acceleration. Torque converters multiply torque at low speeds. If your engine produces low amounts of torque, a converter with a higher stall speed and greater torque ratio can improve acceleration. The trade-off is that a higher-stall converter slips more, which means a higher engine rpm at a given speed. Overdrive automatics like the 4xRE series offer a low First gear and a 0.7x Overdrive. This allows the use of performance gears during low-rpm freeway cruising. Rack-and-Pinion A rack-and-pinion gear system consists of a round gear known as the pinion and a flat, toothed component known as the rack. The principle is the same; however, rather than rotations, the ratio determines the linear distance traveled by the rack with each rotation of the pinion. Calculating Rack-and-Pinion Gear Ratio Instead of counting the number of teeth in each gear, the distance the rack moves is measured in inches. Measure the distance from the end of the rack to an arbitrary point, turn the pinion one full revolution and then measure the distance again. The difference is the gear ratio. Steering Gear Ratios Bear in mind that adding power assist does not quicken the steering; it only decreases the input effort. Remember, also, that the steering ratio required for your car is a function of the radius of the turns of the race track, and on dirt, the slide angle necessary to steer into. In general, converting from manual steering to power assisted steering will permit quickening the steering ratio by at least one step, and usually two. Typical applications of the various rack ratios appear in the chart (Figure 8). The "ratios" (1.57, 2.09, etc.) in the chart refer to rack and pinion gearing and are given as linear inches of rack shaft travel per turn of the pinion (or steering wheel). Since the rack steers the front wheels by means of levers (the steering arms out on the spindles), the actual overall steering ratio of the car depends as much on their length as on the diameter of the pinion gear driving the rack. How to measure the RACK ratio If there are no numbers stamped on the caps, or if you have reason to believe a different pinion has been installed, just measure the distance from one tie rod hole (or from the end of the rack shaft) out to some stationary object (a piece of flat stock clamped to the frame rail). Turn the steering wheel (or the pinion) one full revolution and remeasure; the difference is the linear travel of the rack, which is the "gear ratio" of the rack and pinion. For reference, each additional tooth on the pinion increases the linear travel in one turn by slightly more than 1/4 inch. How to calculate the OVERALL steering ratio The overall steering ratio (12:1, 14:1, etc.) is measurable using turntables under the front wheels. Beginning with the front wheels pointed straight ahead, rotate the steering wheel one turn (360 degrees) one way, and read the turning angle of the front wheels from the turntable scales. You will have to resolve the difference between the right and left due to the Ackerman or steering toe; the usual method is to read the angle of the inside wheel, which is the maximum value. In road racing some prefer to average the two. As an example, if your reading is 36 degrees, dividing this into 360 gives you a quotient of 10, and thus a 10:1 overall steering ratio (if it is not possible to get a full turn out of the steering wheel, use three quarters of a turn and divide into 270). With a six-inch steering arm, a result of 10:1 is roughly what you could expect with a 3.14 rack. This measurement becomes more approximate with quicker racks and shorter steering arms, and because of the prevalence today of rack and pinion steering in short track stock cars it is common now to refer simply to rack travel numbers. Considerations Using a lower gear ratio like 4.10 with normal city or highway driving results in poorer fuel economy. The vehicle isn't utilizing the power exerted by the drive shaft, but it is having to generate it instead. It is suggested to have a higher gear ratio for typical driving to save on gas. A good gearing/tire combo calculator, created by Roy Grimm, is available on the web, found here: http://www.grimmjeeper.com/gears.html He states: This form allows you to calculate final drive ratios as well as see a comparison of speeds and RPMs within operating ranges of the vehicle. This calculator is useful for planning your rig, allowing you to see what kind of performance to expect from different combinations. Mopar1973man Cummins Gearing Calc.gsheet
-
Fixing oxidized headlights for cheap...
Mine was, yes. Although may not have been plastic -specific.. that, i don't remember.
-
Fixing oxidized headlights for cheap...
Agreed, that this will work.. and will work longer than just buffing the lenses with a restoration kit. But, I've done the 'clear coat' paint method years ago, and it was yellowed WITH paint-checking within a year's time. To clean them up after that, it's much easier and time-saving to just buy new ones, as the paint will take hours to strip/sand off to get back to square one.
-
Replace PCM?
All three of my trucks (both manual and autos, 96, 97, 01) reset the cruise light to OFF when the ignition was cycled.
-
Waiting for the Blizzard...
I wished it would snow here. This single digit temp with -10 to -20*F wind chills sucks more when I can still see the grass.. I mean, if it's gonna be this cold, then at least SNOW!!
-
Any Benefit to using deep cycle RV Batteries on the truck?
Had them in my '01. They sucked in the winter.
-
New injectors, possibly this weekend..
True, but he felt that with the timing being at stock, that is not the issue with the extremely poor fuel economy. We'll up the timing later, but want to explore other areas to see if there's a culprit elsewhere.
-
New injectors, possibly this weekend..
didnt touch the timing at this time, as we're trying to determine what the issue is. so leaving it stock timing keeps us at a baseline.
-
New injectors, possibly this weekend..
Timing is at 13.5 deg. We checked it on Sunday.
-
Torque Converter Lock / Unlock Issues
..As well as an inch pound torque wrench.. $75-100 but invaluable when it comes to trans work.
-
Torque Converter Lock / Unlock Issues
That's a model year thing. '99 up has a black plastic sensor called a transducer, where as the earlier models have a metal canister style sensor called a sensor; they perform the same function but are not interchangeable.
-
Forward-Most Univ. Joint In Fr. Ds: How?`
thanks, guys.. I don't have a torch, so that's out..
-
4Wd Shifter Rebuild?
the linkage bushings are tight. My shifter has a ton of lateral play and overall wobbliness.
-
Forward-Most Univ. Joint In Fr. Ds: How?`
I need to replace my front u-joint @ pinion, but I can get the damned clips out of it. Is there a trick without special tools? Also, ONCE they "out", do the caps tap out of the DS? Thanks, Rogan
-
4Wd Shifter Rebuild?
Yeas, so my 4WD shifter is sloppy, to say the least. Also, in 2WD, the knob is against the dash. The rod is adjusted as much as I can adjust it and still be able to select all tcase positions. As well, sometimes when I'm in 4WD (doesn't matter if it's LO or HI) I cannot get it back to 2WD without yanking/jacking with the shift-lever for a few minutes; quite the PITA.. Is there a method or repair for these darned things?
-
E Clip?
yeah, there's an e-clip on each end of the retainer shaft for the pedal(s). I actually drove my '96 for about a year with the left e-clip missing..
-
Alignment (front-end)
They didn't do anything to the rear axle for alignment.
-
100 watt bumper mounted driving lights
I mounted mine in the grill with some homemade brackets and supports. I'll try to find a picture..
-
Alaska Weather!
9* here in VA this morning. Supposed to get to 15 today with a WC of -15* Be in the singles to negs more this week. Eff this.