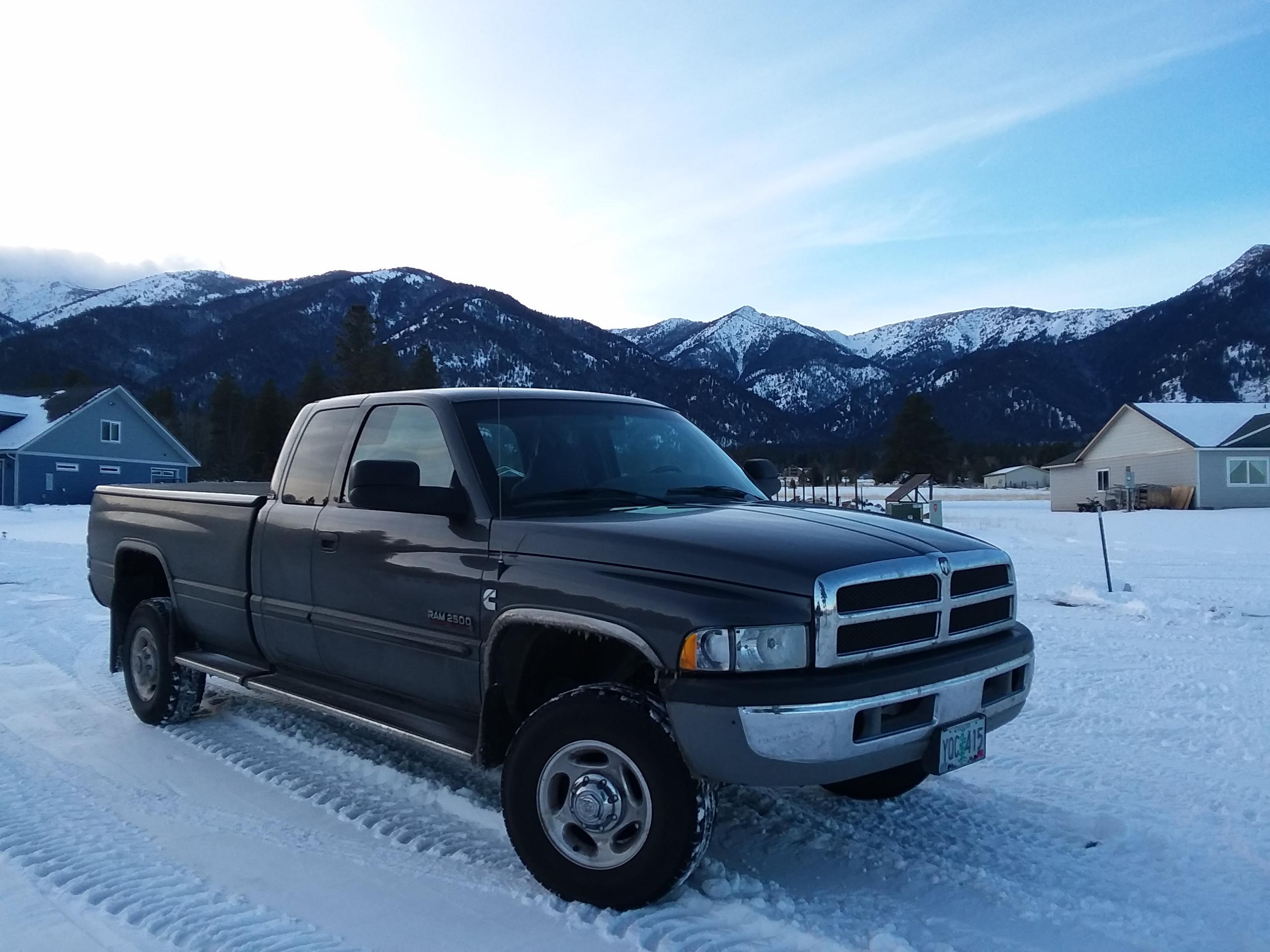
Everything posted by Tractorman
-
Vp44 psg removal
@Finlandese, just curious - your signature shows 295/75r15 Hankook Dynapro m/t tires. Are they really 15" tires, or is that just a typo? - John
-
VP44 Injection Pump Teardown - How it Works
I absolutely agree with this - and don't forget the timing piston, too. I think that blaming lift pump pressure was an easy out for Bosch while quietly fixing the afore mentioned issues without fanfare. At least they fixed them. - John
-
VP44 Injection Pump Teardown - How it Works
I believe I've heard someone talking about before where if the motor is not running the fuel will not get pushed passed a certain spot in vp. Vp needs to be turning for fuel to go through. That's what I heard, not sure how true that is I am a firm believer that this is true. The lift pump provides a positive pressure to the inlet of the fixed displacement vane inside the VP44 injection pump. Fluid cannot be pushed through a stopped fixed displacement pump. The best you can get is internal leakage that will dribble out some return fuel - certainly not enough for cooling. Just last week I installed a return line tee into the filler hose for better cooling of returned fuel (which was a success) I believe this modification will provide adequate cooling for the VP44 under all driving conditions. Before I completed the installation I performed two return flow tests into a five gallon bucket. My lift pump is a frame mounted FASS DRP-02. Not sure what the output is, but I know it is less than 100 gph. First test = 3 cycles of bump start (approximately 25 seconds each time for three times - engine not running, lift pump pressure 14 psi) - Results were barely a trickle entering the bucket. Second test = start engine and let idle, fuel pressure at 12 psi - fuel immediately begins pouring into the bucket quickly covering the bottom. I estimated about .3 gpm (about 18 gph) Raised engine rpm to approximately 1800 rpm - flow visibly increased. My truck currently has logged 355,000 miles - 87,000 miles on a warrantied VP44 and lift pump, and now 265,000 miles on the replaced VP44. This VP44 has never seen 14 psi ever at its inlet (lift pump pressure) with engine running. Most of the time it is 10 psi or less. This does not concern me as I know that there is always a positive pressure. I have posted the following copy of a post before, clearly showing the direct correlation between internal vane pump output and engine rpm. This was posted on a different site by Mopar-muscle, Apr 24, 2001, before I even owned my truck. Test # 1 well some of you guys ain't gonna like this , especially those led to believe (and those that believe it) ... the bigger is a MUST theory . spent a couple minutes running some tests with a DIGITAL/mechnical flow meter and a MECHNICAL fuel pressure gauge , items under test ... 2000 RAM , DD2's , DD TTPM on level 2 (??) and a HOT PE , ( all levels tested the same at WOT)factory pickup , factory lift pump , factory fuel filter housing unmodified , all banjo bolts intact and unmodified except the banjo to the input of the lift pump is replaced with a 90* swept areoquip type -6AN hose end , the bolt at the lift pump had the schrader cut off and drilled and tapped to a 1/8 npt ( for the gauge) and the banjo fittings between the lift pump and the fitler housing have been drilled to 9/32nd . again all banjo bolts are not drilled out as i have on my ram ( test conducted on the DTT RAM ) . we installed ( LaserBob is helping me and getting #2 fuel poured on his head ) a Sonnex digital flow meter ( inside ID is 5/16") in the return line back to the tank , cut in right at the trans crossmember . gph numbers are fuel returned to the tank . DD2 , DD TTPM (True Torque Power Module) FP volume idle 11 psi 18gph cruise 8 psi 24gph WOT 2 psi 30gph DD2 , TTPM , HOT PE ANY LEVEL FP volume idle 11 psi 18gph cruise 8psi 24gph WOT 0 psi 30gph yes you read that correctly , fuel pressure went to 0 and the fuel volume back to the tank did not change from WOT with 2 psi . the truck did NOT stumble , buck , spit , fart , fall on it's face , nothing , ran like all heck at 0 psi , i will note , my truck ran the same at 0 psi with the DD3's , EZ and a HOT PE . - John
-
Intermittent hard brake pedal
Since the hydro booster was replaced, wouldn't the spool valve be a different valve? I am always suspicious when a component gets replaced and the problem symptoms don't change. That usually tells me that the original component did not fail. Usually. A couple of questions: Could a malfunction in the antilock brake system cause a intermittent hard pedal symptom? If so, wouldn't a code be set? Could an intermittent blockage of return line flow from the hydro booster cause a hard pedal symptom? This particular problem kind of baffles me. - John
-
Intermittent hard brake pedal
The truck belongs to my brother-in-law in Crescent City, Ca. The truck is a 2002 Quad Cab, 4x4, automatic transmission with approximately 170,000 miles on the truck. Every thing is stock. The problem: After about every 20 or 30 brake applications the brake pedal gets hard and there is no power assist. As soon as he releases the pedal, everything is back to normal. He took the truck to a shop. The guy who runs the shop is a very knowledgeable man and his business has an excellent reputation.. He asked if the power steering worked when the event occurred. My brother-in-law said that he didn't notice anything with the steering, but his focus was on stopping the truck.. The shop could not make the event re-occur. No codes were set. After discussion between the shop owner and my brother-in-law, it was determined to replace the hydra-boost with a remanufactured one. On the first long trip after the repair, the same event occurred twice again. This time my brother-in-law did not release the brake pedal until after he tested the steering to see if the power steering was working normally. It was. Any ideas on the cause? - John
-
Need a hand with engine speed signal
A good read. I didn't realize just how diversified Echlin is. - John
-
Need a hand with engine speed signal
I believe he means Echlin. They are a major brand name in electrical components. - John
-
No power in reverse
After doing a bit more reading, the HY35 turbo may spool better in that dead zone just because it has a smaller exhaust housing. However, exhaust gas temperatures may run hotter under higher rpm loads than the HX35 I guess you will find out when you make the exchange. - John
-
No power in reverse
What is the read axle gear ratio? It is not listed in your signature. It matters. Clearfield, Utah is above 4,000 ft elevation. - much lower air density than at sea level. Most turbochargers are out of their efficiency zones at low engine rpm, especially at higher elevations. Things that will negatively affect getting a turbocharger to spool up under a heavy load.: * 3.54:1 axle ratio vs. 4.10:1 axle ratio * low stall torque converter * 4,000 ft elevation * 2.21 reverse gear ratio vs 2.45 1st gear ratio You may not be experiencing the problem in first gear because you have more torque to the ground just because of the first gear ratio. This equates to less load on the engine. The combination of all of these things could easily put the engine into a condition that the turbocharger cannot gather enough air for efficient combustion when trying to move a heavy load from idle, consequently, lots of black smoke. I am not saying that there is not a transmission problem or another problem; I am just trying to show what is working against you, so that you can take it into consideration. If there is less load on the engine (less weight), there could be sufficient ambient air pressure (available oxygen) combined with a little boost to get the engine above 1200 rpm, which will get the turbo closer to its efficiency zone. Once that happens, the power comes on and the smoke clears. - John
-
No power in reverse
First gear ratio is 2.45:1, reverse gear is 2.21:1. Reverse gear provides less torque to the rear wheels. What is your rear axle ratio? I am guessing 3.54:1. I think you may be correct about this - especially if your rear axle ratio is 3.54:1. I also think that the HX35 turbo would be more suited for the low stall converter than the HY35 turbo. The HX35 should spool earlier in rpm's under load so it would be a better match with a low stall speed torque converter. - John
-
Fan clutch locked up
I think your fan clutch will work fine. There were probably a couple of gremlins living in it while it was on the shelf. They will quickly jump into your wiring harness now that you have installed the fan clutch. In fact, I think they already have, since you mentioned the fan clutch now seems to be working fine. - John
-
Fan clutch locked up
Also, an indicator for left hand thread. I believe the fan clutch nut is marked in this manner. I think I learned this from this site some time ago. - John
-
Fan clutch locked up
I bought one from Geno's 6 years ago and 135,000 miles ago. It is still working fine. I thought my OEM fan wasn't operating properly, but it turned out that it was fine. The dirty oily mess in the in the center of the radiator was the problem. @dripley, I think the steady coolant temperature reading your are seeing after the clutch fan permanently locked up would be expected. There is now a much more stable flow of air passing through the radiator all of the time which equates to less temperature swing, which means the thermostat can regulate the coolant temperature easier. - John
-
Preparing for road trip.
But, if you would have broken a belt halfway back from the moon, you really would have been glad you had the old one under the back seat..., just sayin' - John
-
Preparing for road trip.
I agree that you cannot prepare for everything, but one extra step I take is to remove the serpentine belt and spin all of the accessory pulleys. Check for excessive shaft movement or rough bearings. I even modified the top of the fan shroud to make the belt removal and inspection easy. My brother-in-law's 2003 truck was slated for a long trip, so I showed him what to be looking for. It turned out that the fan hub bearing was very rough when rotated by hand. Couldn't feel it or hear with the truck running. That could have been an expensive catastrophic failure. - John
-
Pacbrake Install - ECM Signal
I am curious as to where that switch would be mounted (just for my own information), whether it is at the throttle in the cab or by the APPS in the engine compartment. I have an older style vacuum operated PacBrake that I wired in myself. I did not use a throttle switch or a clutch switch. I relayed the solenoid valve and the relay is operated with a momentary foot switch that I mounted on the floor right beside where my left foot rests. This setup makes it not very likely to operate the throttle and the exhaust brake at the same time. However, if the PacBrake micro switch would be a reliable setup, I would be interested in mounting one in my truck. Let us know how you resolved your problem. - John
-
Pacbrake Install - ECM Signal
I may not be able to help much here, but if you answer some questions, others may be able to help. Is the air solenoid for the PacBrake valve controlled by a relay? If so, is it your intention to have the ECM wired to the coil of the relay so that the ECM determines when the engine is at idle and allows for the exhaust brake to work? Does PacBrake provide detailed information (such as theory of operation) as to how the system is intended to work? I don't know what Pin #20 from the ECM's job is. I just went through my factory service manual wiring diagrams and I did not find pin #20 from the ECM - I could have missed seeing it, though. This site provides wiring diagrams for your truck. They should be available to you. - John
-
Truck is dead, will start and then die
Don't skip the step of checking battery voltage while the engine is running as outlined in my previous post. It is a basic step, but it is important. Let us know the results. - John
-
Truck is dead, will start and then die
I don't know where the scanner senses system voltage, so I would use a regular DVM and check voltage at each battery. Should be right around 14.0 volts - a little higher if ambient temperature is low and a little lower if ambient temperature is high. Each battery should be within about .03 volts of each other. - John
-
Gen 3 track bar conversion
Wow! I had no idea! Sorry for that suggestion. When I increased the caster on my truck, I just cranked the adjustment to make the the lower control arm longer, almost to the maximum setting. I just guessed. I had to make a couple of minor adjustments to allow for the crown of the road. When I had it like I wanted, I could let go of the steering wheel and the truck would track very slightly to the right over a long distance.. Of course, in the UK it would be to the left! Then I had it checked at an alignment shop just to have a record (4.5° positive both sides). It is unfortunate that you cannot do this. Then end result was good. The truck steered much better going straight down the road as well as into and coming out of curves. Coming out of curves, the steering wheel returned to center quickly on its own - very responsive. For you, I am sure it will be worth the hassle. I know that you are not going to change your tire size, but here is the difference between the stock tire size vs the tire size that you are running. The tire info from my door jamb on my truck shows 245/75R-16 for tire size. I think your '99 truck is the same. - John
-
Gen 3 track bar conversion
@wil440, you might consider taking the truck to an alignment shop to get a printout of your current caster, camber, and toe settings. That would give you a reference point as to where your caster setting is currently and help you to determine whether or not you want to change it, or how much you want to change it. My truck came from the factory with about 3 degrees positive caster. The truck was a wanderer. I reset the caster to 4.5 degrees positive and the wandering ceased. One of the best and least expensive steering mods I have made. - John
-
99 auto immediately after refreshed injectors stalls when placed in D or R
The lines are important. Each graduation is 125 rpm - rather stupid in my opinion. Watching your video, I see the tach needle just below the 750 rpm graduation mark on your truck. 800 rpm would look more like the photo below. Just took the photo using my truck. - John
-
Nv4500 getting harder to get into gear
@dripley, you might not have known it at the time, but the gremlins probably came out of the electrical wires for a few minutes and were laughing at you. You were given a chance to catch them, but no, you were probably all focused on where your truck was heading. I actually installed a clutch safety switch on my tractor just to protect myself from doing the very same thing. It was always tempting to just reach over and start the engine while standing beside the tractor. Now I have to sit in the seat and depress the clutch pedal to start the engine. The switch has kept me out of trouble. - John
-
02 ram 3500 nv5600 pilot bushing
I think that is a good way to go. I think the sealed ball bearing will keep out contamination better because it has its own seal and sealing surface. My replacement needle bearing has a seal on both ends, but its ability to seal is largely determined by the surface condition of the input shaft which is no longer in good condition on my truck. I would not count on that. In my instance I was driving in a rural area about ten miles from my destination when I noticed a subtle change in the way the transmission was shifting - no noises at all. At the next stop sign, I could not select any gear from neutral. I had to shut the engine off, select first gear and then restart the engine to get moving again. The rest of the trip I just floated the gears and did California stops. However, I needed to make a left turn across two very busy lanes of a four lane road to a place of business. So, while I was waiting for an opportunity to turn, I had the transmission in first gear, clutch pedal depressed with engine idling - something I normally never do. I knew it was going to be a couple of minutes before I would be able to turn. About a minute later there was a muffled screech (barely audible) that lasted about 1/4 of a second (that was when the needle bearings left their home). I am certain that was when the input shaft damage occurred. The good news was that the transmission was instantly back to shifting normal again because the pesky pilot bearing left the premises, which made parking the truck easy and the trip back home much less stressful. Who needs a pilot bearing anyway!! I think the sealed ball bearing will a good choice for you, but what is more important (I learned this the hard way) is to schedule a clutch replacement at a specific mileage, not run it until you have problems. - John
-
02 ram 3500 nv5600 pilot bushing
You have made some good observations. I really have nothing to back up what I am going say, but I think there might be more to the story. I think there may be other factors that give the needle bearing a long life. 1. there is not a lot of weight resting on the needle bearing. Most of the weight is supported by the transmission input shaft bearing. (some gasoline powered engines do not even support the transmission input shaft on the flywheel side). 2. the pilot shaft end would ride on a thin film of lubricant which would allow for each bearing to slide while it rotated. I could not imagine a needle bearing surviving at 6400 rpm. I think they are rotating much slower - but I could be wrong about this. From Wikipedia (the source for everything!) : "Compared to ball bearings and ordinary roller bearings, needle bearings have a greater surface area in contact with the races, so they can support a greater load." I do think that contamination is the downfall of the needle type pilot bearing. Anyway, just some thoughts. - John