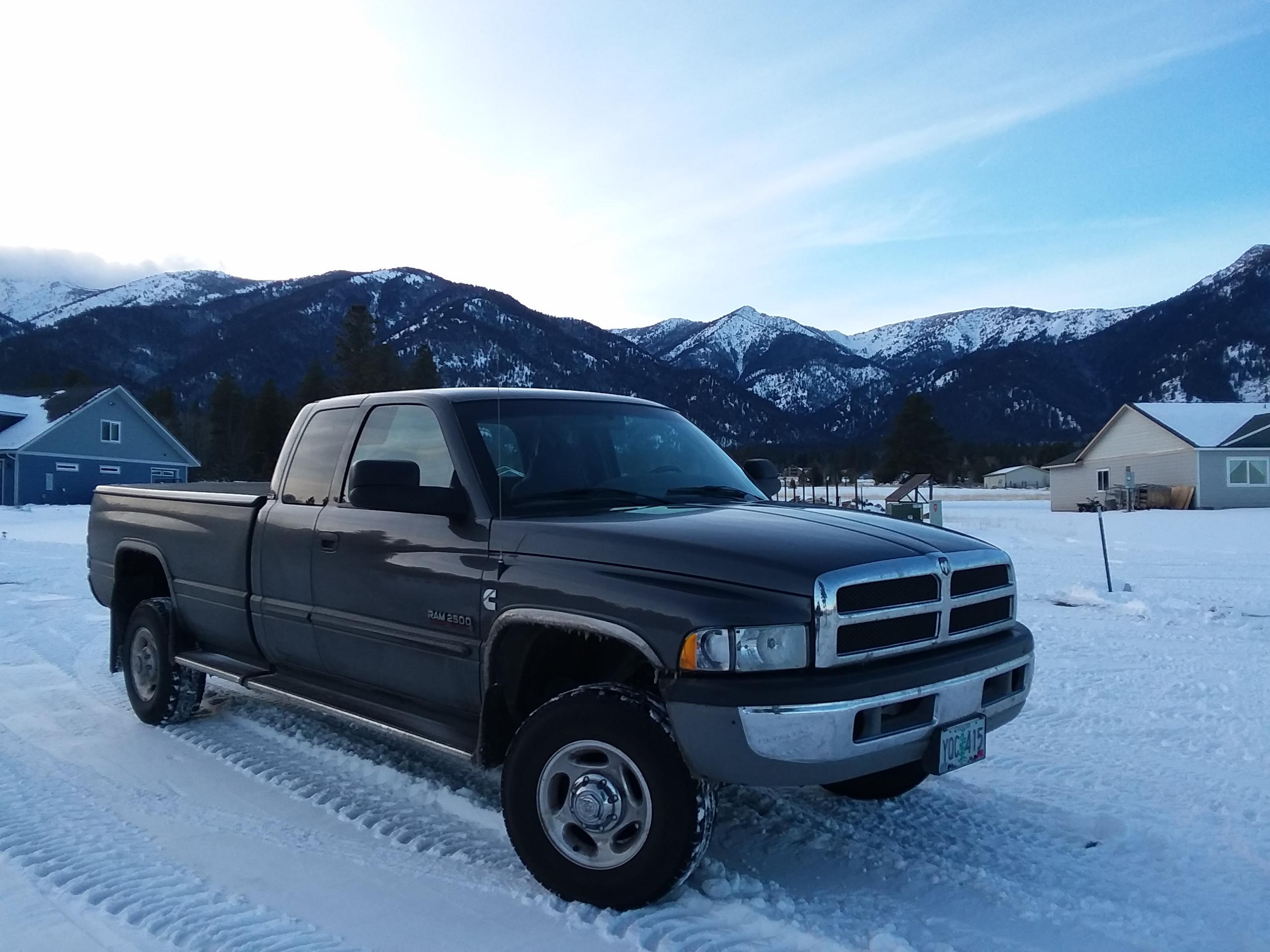
Everything posted by Tractorman
-
Blown Head Gasket...
@sooxies, one of your best indicators of cooling system problems can be observed by watching the coolant level in the overflow container. If it is checked first thing before you drive it for the day, it should be at its lowest level. If you check it after you just parked the truck, it should be at its highest level. If you check the level two days from now before you start the truck and it is 20 degrees colder outside, then the coolant level will be even lower than the two days previous. The point is, is that the coolant level will probably never be the same and that is normal. If the coolant level remains the same when checking the level under different conditions, that is a strong indicator there is a problem. So, the question always is - is the coolant level at the level it should be for the current conditions? You get the picture... I hope all is well. - John
-
Blown Head Gasket...
Could be normal. The air that you pump in will rise in temperature slightly and cool off (contraction) while you wait - the laws of physics. How much did the needle drop? Were you doing this in the evening while the ambient air was cooling? Was the system already pressurized to 16 psi when you started the engine? You mentioned that it rose to 17 psi in about 90 seconds. I have never performed this particular test, but I would expect the pressure to continue to rise at a slow pace because the engine is generating heat. This test showed good results. Overall, there is not a red flag saying that your head gasket is leaking combustion gases into the coolant. For your peace of mind though, you could do the combustion gas test kit for your coolant as @wil440suggested. I have never used one, but idea is a good one. - John
-
Blown Head Gasket...
While you are waiting for your pressure tester to arrive, go on-line and watch the 6 minute video below presented by Mityvac. The video shows you how to use the tester and to diagnose cooling system problems, particularly the potential head gasket problem. https://www.youtube.com/watch?v=cRoYbDDGHTk - John
-
Blown Head Gasket...
Not necessarily. If you are driving an empty truck around, the engine won't generate nearly as much heat as a loaded truck or a truck towing. So in your case the hose would likely have a firmness to it. As @Haggarpoints out, firmness is very suggestive and can be different for everybody. I apologize for directing your focus on that point. So, I would focus of something less suggestive, like monitoring the coolant level in the radiator and the overflow container for a few days and see if you can be confident that everything is either okay or at least narrow down the possibilities of what is going on. One thing for sure - in a normally operating cooling system the radiator should always be full to the brim. The pressure relief and the check valve that allows return flow inside the radiator cap ensure that the radiator will always be full. There really is only one time that you can safely check the coolant level in the radiator and that is when the engine has been off for several hours. And, when I say full, I mean that when you slowly remove the radiator cap in the morning before starting the engine, the coolant should flow or be ready to flow out of the opening. If it is down a half inch or more, something is not right. The following are some possible causes: * There is a small leak in the cooling system. A small amount of coolant leaks out while the engine is running. When the engine is shut off and the engine begins cooling and the pressure falls below atmospheric pressure, it is easier to draw air through the leak rather than lifting the coolant from the overflow container. * The radiator cap is dirty, faulty, not sealing, or just plain worn out - again drawing air into the cooling system as the engine cools down. * The small hose leading to the overflow container is cracked or not sealing which again allows air to be drawn back into the radiator while engine is cooling (a fairly common, but unobserved problem). * There are combustion gases flowing into the coolant while the engine is running. This is the most serious situation. As the combustion gases enter the cooling system the pressure will rise faster than normal. The gases, being lighter than the coolant, will move to the top of the radiator. When the pressure overcomes the radiator cap relief valve setting, the gases enter the overflow container along with some coolant. Once the flow of the combustion gases entering the cooling system match the flow of gases entering the overflow container a balance will have been achieved. At this point the radiator cap is allowing a continuous flow of gases at relief pressure to enter the overflow container. The engine will run fine and will probably not overheat. After the engine is shut off and cools completely, coolant will NOT return to the radiator because at engine shut down the coolant pressure was at the cap relief setting and there are compressed gases in the uppermost part of the radiator. After complete engine cooling the gases will decompress, but will still remain above atmospheric pressure, so no coolant returns to the radiator. As you can see, there are a lot of possibilities. I recommend that you start with the simple stuff in a methodical manner. Don't jump to the worst case scenario. A radiator and cap pressure tester is a very useful tool for finding leaks and for checking the condition of your radiator cap. The tester can usually be loaned or rented from an auto parts store. Keep us posted... - John
-
Post coolant flush help
The primary reason a gas engine heats to operating temperature rather quickly while idling and a comparable displacement diesel engine has a tough time getting to operating temperature while idling is because of the different way the air flows through each engine. Gas engines have a throttle plate. Diesel engines of our era and older do not. A gas engine works like this: an air and fuel mixture at the proper ratio enters the cylinder at a very low pressure at idle. The engine actually has to work to draw the air-fuel mixture around a mostly closed throttle plate before the mixture enters the cylinder. This creates a very low pressure downstream of the throttle plate - a vacuum of about 18" HG. That air-fuel ratio is at such a low density that it does not carry much combustion heat out the exhaust. Most of the heat goes to the water jacket, so the coolant warms quickly. A diesel engine with no throttle plate allows a full charge of air to enter the cylinder at idle and then a small amount of fuel is injected. The air density entering the cylinder is slightly lower than the ambient air density so lots of heat from combustion can be carried out the exhaust and a lot less heat will go to the water jacket. Plus, the engine does not have to work as hard to get the air into the cylinder in the first place because there is no throttle plate. A fully engaged viscous fan doesn't help matters either - just what you need on a cold winter day - a fan blowing cold air over an engine that is struggling to warm up! - John
-
Blown Head Gasket...
You may have a valid concern..., or not. You didn't mention what the conditions were when you noticed the radiator hose was firm. Normal cooling system operation with a 15 psi cap and an overflow container and an engine that has been shut off for at least overnight works like this: * Before engine is started the radiator will be 100% full and the overflow container will be less than half full (coolant will have be drawn into the radiator from the overflow container during the night from a cooling engine. A one-way check inside the radiator cap accomplishes this task.) * As soon as the engine is started, pressure will start building as the coolant temperature rises with a closed thermostat. It won't be long before the pressure reaches 15 psi and some coolant is transferred to the overflow container. If you checked the firmness of the radiator hose at this time, you will find it very firm. This would be normal. * As you start driving the truck, additional fueling generates more heat and more coolant is transferred to the overflow container. After driving a while, a balance will occur as the thermostat adjusts to the rate the engine is heating and the radiator is cooling. At this time coolant stops being transferred to the overflow container because the coolant pressure is no longer rising. * As soon as you reduce the engine load (such as pulling off of the freeway and parking the truck) the coolant pressure drops considerably - down to as low as 2 or 3 psi. At this time with the engine still running the radiator hose should not be firm. If it is very firm, I would be concerned. (In the old days when trucks had top tank radiators and no overflow containers, this was the time to check coolant level on a warm engine). The next morning before the engine is started, the radiator should be 100% full and the coolant level in the overflow container should have dropped some. So, I would start from scratch and the first thing I would do is make sure that the radiator is 100% full and the overflow container at least 1/3 full before starting the truck after it set overnight. Then I would drive the truck and work the engine a bit and bring it home and before shutting the engine off, I would check the over flow container and the firmness of the radiator hose. If the hose is very firm, that could indicate that combustion gases are entering and pressurizing the cooling system. After several hours and before starting the engine again, I would check the coolant level in the radiator. It should be filled to the brim. If it is not, then again, this could be caused by combustion gases entering the cooling system. I would repeat this procedure everyday for at three days or so to get rid of the possibility of trapped air in the cooling system. A radiator pressure tester would be useful to find leaks and also to prove the radiator cap is relieving at the proper pressure and the cap doesn't leak. - John
-
Fuel pressure 5psi. 0 at WOT
I made no mention of running a VP44 without a lift pump. But since you mentioned it, some VP44 engines will continue to run normally even if the lift pump fails. For that to happen, the lift pump must have a free flow check valve internally and the failure must not block any flow. If the conditions are right, the internal vane pump in the VP44 continues to draw fuel from the tank. If the failed lift pump does not have an internal free flow check valve or the failure blocks fuel flow or introduces air, the engine will likely stumble or not run at all. - John
-
Fuel pressure 5psi. 0 at WOT
The 14 psi overflow valve inside the VP44 provides the path for fuel return flow for cooling the VP44. There is a fixed displacement internal gear pump ( a vane pump) with a relief setting of over 100 psi that by design provides more flow than can be consumed by the injectors and operating parts inside the VP44 with plenty of fuel flow left over to operate the 14 psi overflow valve and return fuel to the tank under all operating conditions. The lift pump flows directly to the inlet of the fixed displacement internal vane pump. No lift pump can make the internal vane pump deliver more fuel. A high volume lift pump that flows more fuel than the internal vane pump can flow just raises the VP44 inlet pressure, but DOES NOT flow more fuel through the internal vane pump. It can't because the internal vane pump is fixed displacement. The concept of using a lift pump is to provide a positive pressure to the VP44 inlet. If an engine is at wide open throttle and the inlet pressure of the VP44 is only 3 psi, all is well. 3 psi means that the inlet of the VP44 is charged so the internal gear pump will take care of the rest. I am posting this information because I truly believe that there were so many problems with VP44 trucks when they first came out that it generated a paranoia that can't seemed to be dropped. The paranoia was centered around lift pump pressure early on. However, Bosch fixed a lot of those VP44 problems without fanfare and a quality rebuilt VP44 is now pretty reliable - regardless of lift pump pressure. My replacement remanufactured VP44 (timing piston failure on the original) and lift pump conversion to tank was performed under warranty at 87,000 miles in 2005. The original lift pump never missed a beat. The converted in-tank lift pump operated at 6 psi at idle and 3 psi at wide open throttle. I drove it that way for over 150,000 miles with a Smarty tuner added. I replaced the in-tank lift pump with a frame mounted used FASS pump (a low volume one) at 250,000 miles on the truck. I did this only because I wanted an easy roadside repair in case the lift pump failed. The FASS lift pump operates at 12 psi at idle and 5 psi wide open throttle. That lift pump has been operating for over 4 years and 90,000 miles. I now have over 250,000 miles logged on the rebuilt VP44. I expect that I can have a VP44 pump failure at any time now, but I will not complain about the service life and I will not blame it on the lift pump. - John
-
Fuel delivery problem etc
As hindsight, I think that you may have had a hydrostatic lock caused by a severely leaking #6 injector. While you were having trouble starting the engine, lots of fuel could have leaked from the injector and collected in #6 cylinder. Then, when cranking the engine over, the fuel wouldn't compress and caused a hydrostatic lock - consequently, the horrible sounds and the starter shaft breaking. By the time you replaced the starter, the fuel leaked out of the cylinder via the end gaps of the piston rings. It would also explain why the compression is higher in #6 cylinder than the rest of the cylinders - some residual fuel is hanging around the compressions rings. As others have pointed out, starter shafts just don't break... - John
-
Body Roll
@Alexio Auditore, your topic title suggests that when your truck goes into a curve you get a lot of body roll (a steady lean of the vehicle throughout the curve). This could be caused by worn out spring or deteriorated anti-sway bar bushings, but not by stiffer shocks. The above statement suggests that that you are talking about a stiff side to side rocking motion. That would probably be caused by the stiffer shocks that you installed. I installed the 4600's on my truck because I heard that the 5100's were a bit stiff. If I interpreted what you were saying incorrectly, then just disregard my comments. - John
-
The Rise of the Shawty
My guess is regular cab short bed. - John
-
Idles fine, sluggish response, no boost, no codes
Whenever I perform any work on my truck and something else doesn't work right after I am done, I always go back to "What did I inadvertently do to create this problem?" First, I would retrace the steps taken when you when you worked on the fuel system and on the battery cables. - John
-
Heater core or something else?
Here is the filter and housing assembly. I use a Napa 4070 filter replacement. The filter housing is quality and one of the things I really like about the mounting is that two bolts can be removed and the whole assembly can be swung out of the way without disconnecting hoses to get access to other stuff. I purchased the assembly from Pure Diesel Power. - John
-
2001 Ram Headlights/Brake upgrades
Not to my knowledge. - John
-
2001 Ram Headlights/Brake upgrades
I second that. @1369x, your signature shows that you have a NV5600 transmission - you couldn't have a better setup for an exhaust brake. I also tow and have an exhaust brake to use with my NV5600 transmission. My first set of front brake pads lasted for over 215,000 miles. I am still on my second set at 340,000 miles. I am also on my original front brake calipers and front wheel bearings. I attribute the long life of the wheel bearings is due to lack of heat generated by the front brakes because the exhaust brake is doing most of the work to slow the truck and trailer. - John
-
Nv5600 clutch time
You will probably hear different opinions about pilot bearings / bushings. My original clutch replacement was at 297,000 miles due to a OEM pilot bearing failure (needle bearing style). It caused some damage to the transmission input shaft pilot bearing surface. When you buy clutch packages, new flywheels are cheap compared to trying to resurface and cleanup heat cracks and hot spots on the old flywheel. In my opinion resurfacing the old flywheel is not worth the risk of poor performance (grabby, chattering, slipping clutch) that could occur, especially when considering how much labor is involved to replaced it. - John
-
Finally hit 20MPG!
Use the weight distribution hitch. Even though you have a heavy duty truck, the tongue weight for a 7,000 lb trailer should be about 10-15% of the trailer weight. That equates to about 700-1000 lbs of weight on the hitch ball. This weight acts a lever (using the rear axle as a fulcrum) and unweights the front axle a few hundred pounds which affects steering and handling - even on a heavy duty truck. My travel trailer only weighs 4,000 lbs when loaded and I still use a weight distribution hitch. I've experimented towing with it and without. Night and day difference. - John
-
Heater core or something else?
I agree. My heater core started leaking in in 2008 at 136,000 miles. I didn't replace it until 2017 at 283,000 miles. I added a stop leak product twice early on - something that I tell other people not to do. Sometimes I'm not very bright. During the years the heater core was leaking, the fogging windows continued to be a problem and slowly became worse. I hardly ever added coolant to the system. A heater core doesn't have to leak very much coolant to interfere with keeping windows clear. Most of the time I didn't notice any coolant odor. Once I added the stop leak product, the coolant was always cloudy and you could see particulates in the coolant. It didn't matter how many times I changed the coolant, it wouldn't clean up. After I replaced the heater core, I finally installed a coolant filter in parallel with the heater core circuit. Over a three week period the coolant became crystal clear. I left the coolant filter in the circuit and periodically replace the filter. - John
-
2007 5.9 cut off while driving engine light flashing won’t turn over?
I am not really that familiar with the automatic transmission operation on a 2007 truck, but I would recheck every electrical connection related to the recent transmission work that you had done. It sounds like communication to the transmission has been lost. - John
-
Steering Pump and Seals
Likewise... I still have original OEM front wheel bearings, rear axle bearings and seals, wiper motor, evaporator core, right tie rod end, front and rear antisway bar bushings, brake booster, brake master cylinder, clutch master and slave cylinder - just to name a few. I think the quality of build peaked in 2002 - the last of the Second Generation. This motivates me to keep my truck. - John
-
Steering Pump and Seals
@dripley, it seems that you and @Mopar1973Man made the right choice in keeping the OEM power steering pump. - John
-
Steering Pump and Seals
It is likely that there is air still entrained in the system. Even after the initial bleeding of air, there is still lots of air trapped in various parts of the system - hoses, steering gear box, the brake booster accumulator , etc. The flow rate of the power steering pump is about 2 gallons per minute. The whole system only holds about one gallon of fluid, so that means that all the fluid circulates through system in about 30 seconds. I am just using round numbers here, but you get the idea. Once the engine is started, the fluid and air immediately mix and both are carried rapidly through the system. The only place for the air to separate from the fluid is when the fluid enters the reservoir and slows its velocity enough to allow for the air bubbles to rise to the top of the fluid and escape. When the fluid is cold, this separation takes longer and a lot of the air is recirculated back through the system. When I change power steering fluid, after the initial bleeding I start the engine and shut if off almost immediately giving the aerated fluid entering the reservoir a little time to release the air. I do this a few times allowing the engine to run longer each time. While the engine is off, I completely discharge the accumulator by stepping on the brake pedal several times (air can be trapped here). Eventually, with the front axle on jack stands, I steer from stop to stop using the same procedure. During this whole operation I frequently check and top off the fluid in the reservoir. I then drive the truck to get the fluid to full operating temperature which helps get the remaining air separated from the fluid. Regarding the power steering feels weak problem: I have had three power steering pumps on my truck through its life of 340,000 miles (I am the original owner). The first one did not fail - I replaced it at 215,000 miles with a new Borgeson just as a maintenance procedure. In hindsight, I should have kept it. At 290,000 miles the Borgeson pump failed. I replaced it with a Napa remanufactured pump along with a Napa custom ordered remanufactured quick ratio steering gear box. All is well so far and I really like the gearbox. ALL of my power steering pumps in my opinion are NOT heavy duty and are not adequate for the heavy front end of a Cummins powered truck . All of them could be stalled at idle with foot on the brake and steering hard to the left or the right before reaching the steering stop. Just one opinion, - John
-
Heater Core
@Alexio Auditore, once you get the evaporator core clean (dash removal method or whatever you figure out), install one of Geno's cabin filters. It is a great investment and your HVAC system will stay clean. - John
-
Clapping coming from exhaust
Have you checked valve lash? Have you verified that each intake and exhaust valve are making their full travel? How many miles on the engine? How many miles on the injectors? Are they stock injectors? What is the history of the truck? Your video does not play for me. - John
-
Clapping coming from exhaust
"Clapping coming from exhaust." Sounds like you have an audience. Can you describe the sound with more detail and tell us what conditions generate the sound? - John