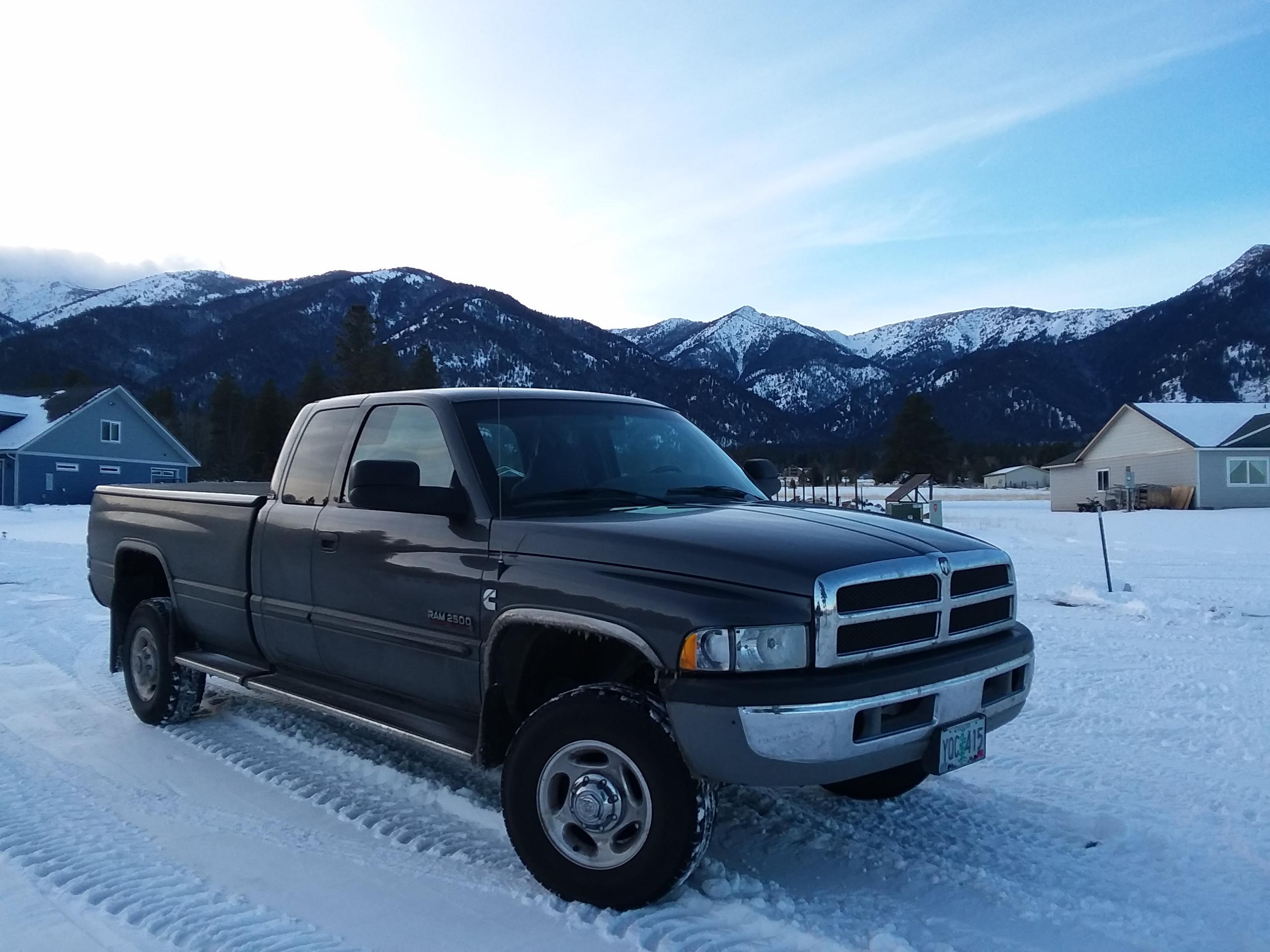
Everything posted by Tractorman
-
CAD&Free spin kit Advice
I now have 302,000 on my CAD axle with original axle seals. About 12,000 miles ago the right front axle seal was leaking to the point it was leaving oil on the floor every time I parked the truck. I was not looking forward to that repair. Turned out to be a blocked vent. A piece of hardware that fastened the vent hose to the frame or body had crushed the hose. - John
-
Grounds and electrical stuff.
I just posted, but I see that Dripley beat me. He went into more depth and provided more information than I did. Are you using an electric soldering gun? What is the wattage? The joint in the photo looks like it needs more heat. Try adding some flux and more heat to the one in the photo and see if you can get the solder to flow using the procedure below. When soldering, hold the tip of the soldering gun against the crimped terminal. The heat will transfer through the crimp into the wires. Touch the solder at a point where the terminal edge meets the wires. When the terminal and wires get hot enough, the solder will start flowing. Keep the soldering gun tip on the crimped terminal and keep adding solder as it disappears through the crimp following the wire strands up to the insulation. Watch a couple of soldering videos on You Tube and do some testing until you get it right. As far terminal ends - personally I don't like insulated terminal ends because they are too difficult to crimp properly. I do what you did, but before crimping the terminal onto the wire, I place the proper size of heat shrink with sealant over the wire and push it out of the way. I then crimp the wire into a bare terminal end as you did (except that I will crimp it correctly) and solder the joint. After the joint cools, I move the heat shrink into position and finish the job. - John
-
Grounds and electrical stuff.
From looking at the photo, you need to rotate the terminal 180 degrees before you squeeze the crimping tool. The dimple created by the tool should be on flat side of the terminal and the "ears" of the terminal end will be contained by the curved part of the crimping tool. The resistance test is not a valid test. Only one strand of wire needs to be connected to show a "0" ohm reading. The solder job in the photo will not be a reliable connection electrically. If the surfaces were clean, flux was added, and the proper amount of heat was applied, the solder would have freely flowed through the connection and through the strands of wire up to the insulation. - John
-
Low Air Flow and Smoke/Burning Smell from Vents
Yes, they do and it is a worthwhile investment. The filters are washable, as well. I did my HVAC repairs one year ago and I did not want anything to be able to work its way into the ducts. I also installed a coarse screen over the inlet part of the upper fan housing. The screen fits around a removable part that can be accessed with the heater fan removed. If you don't do the Geno's cabin filter, at least add the coarse screen. - John
-
Greasing Transmission for Clutch Installation
Now that's good advice! - John
-
Greasing Transmission for Clutch Installation
I think you make a good argument here about the grease thickening and attracting dirt, that is why I use a very thin film. Luk is the manufacturer for the clutch I just installed in my truck and they say basically the same as the FSM. - John From Luk,
-
Greasing Transmission for Clutch Installation
To grease or not to grease... this is one of those topics that may leave some undecided. Good arguments can be made for both sides. In the end one will have to make the decision based on information from service manuals, professional and non-professional experience, and your own experience. Personally, I have always put a very thin coat of grease on the transmission input shaft splines and the transmission front bearing retainer sliding surface for the release bearing. From the FSM for 2002 truck. - John
-
ROUGH RIDING
I did the same thing. Only I didn't go outside and wait for it to cool off and then come back and hit it with a hammer. I was smarter. I stayed on the job and kept applying heat until it let loose. I never saw the ball stud, but I heard it hit several different places in the shop at supersonic speeds. It left quite a dent in the floor, too. It took a few minutes to find it, but it gave me some time to reflect on just how stupid I was for applying heat to a sealed ball joint. Fortunately, I and my helper were not injured, but not because of any skill on my part. - John
-
ROUGH RIDING
Me three. - John
-
Alternator diode heat
I think there are some things going on with the grid heater operation that are normal, but have not been mentioned so far. Also, I don’t think that the grid heaters are the problem (as in defective). To illustrate, consider a 136 amp alternator charging a circuit that is electrically sound maintaining 14.0 volts with engine running. Alternators typically put out their maximum rating at around 6,000 rpm (alternator speed) Engine pulley to alternator pulley ratio for diesel engines is approximately 3:1 (6.7 Cummins 3.22:1, not sure what 5.9 is) A diesel engine at idle – alternator is not capable of delivering rated output amperage. A diesel engine at high idle (1200 rpm) – alternator will deliver higher amperage, but probably not rated amperage. With engine running the alternator will deliver up to its rated output (dependent on alternator speed) if battery voltage at sensing location is pulled down by one or two tenths of a volt and held there. Example: If an electrical load pulls battery voltage down to 13.9 volts, the voltage regulator (PCM) will command alternator output, but only enough output to bring battery voltage back to 14.0. If a large electrical load, such a two grid heaters pulling 200 amps total load, is placed on the electrical system, the battery voltage will fall rapidly even if the alternator is delivering its rated output of 136 amps (136 amps being delivered – 200 amps being consumed = a 64 amp deficit). Battery voltage will continue to fall until combined battery amperage and alternator amperage is equal to the load amperage being consumed. If the alternator speed is less than rated speed, the alternator amperage to the batteries could be considerably be less, especially with an idling engine. Diodes by design generate a voltage drop, about .6 volts. This voltage drop generates very localized heat. The example below assumes 40 amps are passing through a diode. Example: 40 amps x .6 volts = 24 watts (think of a 25 watt soldering gun) So, ( just my opinion) but I think that after the grid heaters are cycled , the starter is cranked, and finally the post grid heater cycles begin, that the diodes being hot to the touch on any alternator would be a normal condition. Another thought. An idling engine with grid heaters cycling would generate a specific amount heat in the diodes with a specific amount of air flowing past the diodes for cooling. An engine fast idling under the same conditions would generate more heat in the diodes, but would have more air flowing by the diodes for cooling. Would the diodes actually be cooler than the above example? Maybe, maybe not. Maybe the diode heatsink is inefficient or there could be other factors like what Haggar mentioned – quality control with diode manufacturing. One way that grid heaters could affect the life of an alternator could be in controlling the post heat cycle event – how long each cycle is activated and how long each cycle is deactivated. Also, are both grid heaters activated, or just one? I am not sure how that is supposed to work. I know that this information does not provide a definitive answer as to why your original alternator performed so well, but I just wanted to share what I have learned over the years and maybe some of the information can possibly help with diagnosing your issue. My method of avoiding repeated high alternator current output conditions has been to re-wire the grid heater control relays with a momentary switch so that I control when and how long the grid heater cycles and to avoid the post heat cycles completely. I know that this method sets a couple of codes, but I know what the codes mean and the codes have no impact on driveability. - John
-
What makes 24 valves sound different from each other?
I have completed the article. Your request got me thinking (I hate it when that happens). When I made the BHAF muffler I didn't follow through with any pressure drop tests regarding the air flow through the new pipe that was introduced into the air intake stream. So, I did some testing and put the results in the article. I also scrapped the plastic ribbed pipe idea and went to a simpler design. Dripley gets credit for the name "BHAF Muffler"/ I think this shortcut will get you to the article. - John
-
BHAF Muffler Uhh??
A BHAF Muffler - Uhh?? I like the Cummins engine, but I try to do anything I can to make the engine quieter. The BHAF air filter flows lots of air, but it also allows a lot of engine air intake noise to be heard in the cab – more noise than the factory air box and the factory air filter. This inspired the idea to experiment with a BHAF muffler on a big honkin’ air filter – in this case, a NAPA 2790. A BHAF muffler is not for everybody. If you like air intake sounds, turbo sounds, and amplified exhaust brake sounds inside your cab, then this project may not be for you. For my first muffler I used a length of ribbed plastic drain pipe inserted into the filter. I decided to measure the pressure drop through the pipe on a road test. I hooked up an analog water manometer gauge (mounted inside the cab) at connection port “B” for the test. All of the following tests were done driving the truck in fifth gear at wide open throttle approaching 2500 rpm. The pressure drop measurements are recorded below: Port “B” connection 4” H2O @ 27 psi boost @ 2500 rpm WOT – BHAF with NO muffler 20” H2O @ 27 psi boost @ 2500 rpm WOT – BHAF with plastic ribbed muffler 9” H2O @ 27 psi boost @ 2500 rpm WOT – BHAF with steel muffler Port “A” connection 1” H2O @ 27 psi boost @ 2500 rpm WOT – BHAF with or without mufflers The plastic pipe muffler failed in terms of pressure drop (20” H2O) probably due to the restrictive 3” inside diameter and ribbed internal surface. The steel pipe muffler is the winner. It is still effective as a muffler, but at a pressure drop of only 9” H2O under the same test conditions. The improved pressure drop is likely due to the increased inside diameter (from 3” to over 3 5/8”) and from a smooth inside wall compared to the ribbed plastic pipe. So, I scrapped the ribbed plastic muffler (although I ran it for 40,000 miles) and made a steel one. This muffler consists of one part – an 8” length of thin-walled steel exhaust pipe with an outside diameter of 3 13/16” and an inside diameter of 3 11/16” (wall thickness approximately 1/16”) These diameters could vary slightly – in my case the NAPA 2790 BHAF connection has been deformed to a slightly smaller diameter over time because when the filter was new there was nothing in place to support the tension of the intake hose clamp. For more BHAF information, IBMobile wrote an article regarding dimensions and specifications of the most popular BHAF’s – thank you IBMobile! Check your local muffler/exhaust shops in the area for a piece of exhaust pipe to meet these dimensions. If you can’t find an exact match, select a pipe that is slightly larger in diameter and then modify the pipe as described below. I made the thin-walled steel muffler piece from a slightly larger diameter exhaust pipe with a wall thickness of approximately 1/16”. After cutting it to the 8” length, I cut out and discarded a piece of the wall and reshaped the remaining pipe to the proper outer diameter with the aid of a vise. I stress relieved the pipe so the cut edges touched each other and then I soldered them together. I made sure that the seam joint was flush and smooth for an airtight seal. I inserted the muffler into the air filter leaving a small edge visible. This will allow for at least 3 inches of air space between the inside back wall of the air filter and the end of the pipe. I hope that you will enjoy a quieter ride in the cab without the sacrifice of performance. - John
- 13 comments
- 1 review
-
-
- 1
-
-
Air & Exhaust Article - BHAF Muffler Uhh??
A BHAF Muffler - Uhh?? I like the Cummins engine, but I try to do anything I can to make the engine quieter. The BHAF air filter flows lots of air, but it also allows a lot of engine air intake noise to be heard in the cab – more noise than the factory air box and the factory air filter. This inspired the idea to experiment with a BHAF muffler on a big honkin’ air filter – in this case, a NAPA 2790. A BHAF muffler is not for everybody. If you like air intake sounds, turbo sounds, and amplified exhaust brake sounds inside your cab, then this project may not be for you. For my first muffler I used a length of ribbed plastic drain pipe inserted into the filter. I decided to measure the pressure drop through the pipe on a road test. I hooked up an analog water manometer gauge (mounted inside the cab) at connection port “B” for the test. All of the following tests were done driving the truck in fifth gear at wide open throttle approaching 2500 rpm. The pressure drop measurements are recorded below: Port “B” connection 4” H2O @ 27 psi boost @ 2500 rpm WOT – BHAF with NO muffler 20” H2O @ 27 psi boost @ 2500 rpm WOT – BHAF with plastic ribbed muffler 9” H2O @ 27 psi boost @ 2500 rpm WOT – BHAF with steel muffler Port “A” connection 1” H2O @ 27 psi boost @ 2500 rpm WOT – BHAF with or without mufflers The plastic pipe muffler failed in terms of pressure drop (20” H2O) probably due to the restrictive 3” inside diameter and ribbed internal surface. The steel pipe muffler is the winner. It is still effective as a muffler, but at a pressure drop of only 9” H2O under the same test conditions. The improved pressure drop is likely due to the increased inside diameter (from 3” to over 3 5/8”) and from a smooth inside wall compared to the ribbed plastic pipe. So, I scrapped the ribbed plastic muffler (although I ran it for 40,000 miles) and made a steel one. This muffler consists of one part – an 8” length of thin-walled steel exhaust pipe with an outside diameter of 3 13/16” and an inside diameter of 3 11/16” (wall thickness approximately 1/16”) These diameters could vary slightly – in my case the NAPA 2790 BHAF connection has been deformed to a slightly smaller diameter over time because when the filter was new there was nothing in place to support the tension of the intake hose clamp. For more BHAF information, IBMobile wrote an article regarding dimensions and specifications of the most popular BHAF’s – thank you IBMobile! Check your local muffler/exhaust shops in the area for a piece of exhaust pipe to meet these dimensions. If you can’t find an exact match, select a pipe that is slightly larger in diameter and then modify the pipe as described below. I made the thin-walled steel muffler piece from a slightly larger diameter exhaust pipe with a wall thickness of approximately 1/16”. After cutting it to the 8” length, I cut out and discarded a piece of the wall and reshaped the remaining pipe to the proper outer diameter with the aid of a vise. I stress relieved the pipe so the cut edges touched each other and then I soldered them together. I made sure that the seam joint was flush and smooth for an airtight seal. I inserted the muffler into the air filter leaving a small edge visible. This will allow for at least 3 inches of air space between the inside back wall of the air filter and the end of the pipe. I hope that you will enjoy a quieter ride in the cab without the sacrifice of performance. - John View full Cummins article
-
Exhaust Brake Minimum Setup 2002 Cummins w/ Manual Trans
I don't think it is about whether or not it is an automatic or a manual - I think it is about whether you have a 12 valve or a 24 valve engine, being the 24 valve engine already has the heavier valve springs. I think. - John
-
Exhaust Brake Minimum Setup 2002 Cummins w/ Manual Trans
I don't have a throttle switch or clutch switch with my exhaust brake setup and I use a momentary foot switch on the floor below the clutch pedal to operate the exhaust brake. I agree that you shouldn't use the exhaust brake and throttle at the same time, but for a different reason - that reason being that it would be possible to float the exhaust valves resulting in engine damage. How would EGT's "skyrocket" if you throttled while using the exhaust brake? I am not saying that it didn't happen to you - I am just trying to understand. In my thinking, the maximum air flow through the engine could only be what could pass through the orifice in the exhaust brake valve while it was closed. The turbocharger would not be able to spool up because the drive pressure on both sides of the turbine wheel would be virtually the same pressure. So in essence, the engine would be performing as a naturally aspirated engine with a severely restricted air flow. To support my theory, I took my truck for a test drive and attempted to accelerate with the exhaust brake actuated in fifth gear. Engine rpms peaked and stabilized at about 1700 rpm, boost remained at zero psi, and the EGT's peaked and stabilized at 800 degrees, and lots of black smoke poured out of the exhaust pipe. The zero psi boost, the 800 degree EGT, and the black smoke were about what I expected to see since there was not nearly enough air to burn the fuel to generate power or heat. - John
-
No Vacuum after Oil Change
If it is a line connection at fault, you really can't blame the mechanic, especially if the lines have not been replaced for a long time. There are various size hoses and connections with plastic T's and fittings. The hoses get brittle or soft and crack or tear.. Carefully inspect each connection. The HVAC system will default to defrost mode if the vacuum supply is lost. This is designed for safety to ensure that the inside of the windshield will not fog. Let us know what you find. - John
-
No Vacuum after Oil Change
It shouldn't for an oil and filter change, but you also said that he fuel filter was to be changed. That is in the area of vacuum lines. There are some large and small vacuum connections starting from the vacuum pump (large ones) up to the firewall near the rear of the valve cover. Any one of those connections could have been knocked loose or cracked - John
-
6 Speed manual transmission ~ NV5600 ~ General Questions
I use the throttle to match engine rpm to road speed (for a specific gear). The rpm matching must be done while the transmission is passing through neutral with the clutch engaged (foot off of the clutch pedal) When the road speed and engine rpm are matched, then quickly clutch and select the appropriate gear while holding the matching rpm with the throttle. This procedure works whether upshifting or downshifting. For example, when I prepare for a downshift, I start easing up on the throttle until the engine is unloaded in reference to the drive train. I then freeze the throttle position and select neutral without using the clutch pedal. The gear shifter slides easily into neutral because there is no torque on the gear. While the transmission is passing through neutral, I raise the engine rpm's to match the downshift gear speed (dictated by road speed) and again freeze the throttle position while clutching and slipping the transmission into gear, thus competing the downshift. The whole process actually happens q uickly and the results are smooth and seamless shifting. There is very little wear on the synchronizers or the pilot bearing because the transmission input shaft is rotating at engine speed ant the gear being selected will be matched to road speed. Back in the 70's, the truck driving school I attended taught the double clutching method, essentially the same as I explained above, but the first clutching would occur when pulling the transmission into neutral. The rest of the procedure was the same. One thing for sure, if the clutch is disengaged (pedal depressed) while the transmission is passing through neutral during a shift, the transmission input shaft speed will start slowing quickly and cannot be controlled with the throttle. Consequently, the synchronizer will have to do all of the work to match the gear to road speed. Also, since the engine and transmission input speeds will not be the same, unnecessary wear will be placed on the pilot bearing. During upshifts because the engine speed and the transmission input shaft speed fall off together naturally, the complete shift can be made with a single clutch while passing through neutral and timing the next gear selection. But, this procedure doesn't work for downshifting because the transmission input shaft must be engaged to the engine in order to raise the transmission input shaft speed for the downshift using the throttle. Hope this helps, - John
-
What makes 24 valves sound different from each other?
I think I can do that - give me a couple of days. - John
-
What makes 24 valves sound different from each other?
Mine is actually quieter than the factory air filter and box. If you end up doing the project, let us know what you think after you are done. Be sure to get an airtight seal between the parts. I think you will like the end results. Please resist the urge to glue feathers on the ribbed pipe - it won't make it any quieter and it might dust the turbo, you know, like a feather duster? - John
-
What makes 24 valves sound different from each other?
Sorry for the confusion. In a different post I had shown some photos of a silencer that I made for the inside of a BHAF. Dripley named it a BHAF muffler. I noticed in your video that I could hear the throaty sound of the intake part of the engine. The silencer that I made makes that sound go away - for me quieter is better.. I think the shortcut below will get you there. - John
-
What makes 24 valves sound different from each other?
Your truck needs my BHAF muffler kit. - John
-
Bad ECM or wrong vp44??
But if you were and you leaned up against an electric fence, you might understand how back feeding could occur. - John
-
Alternator diode heat
I agree with your above statement. The multi-meters that I use currently and in the past do not display a value lower than .1 ohm. Will your multi-meter display a value lower than .1 ohm, such as .01 ohm? If your meter is limited to measuring in tenths of an ohm (like mine), then theoretically the 95 amp element would be rounded down to .1 ohms. If your meter can measure in one-hundredths of an ohm, then the 95 amp element would be rounded to .13 which would be a value that you can work with. So, what I am trying to say is since the meters that I have worked with are limited to measuring within a tenth of an ohm, a .1 ohm reading could really be .08 ohms (150 amps), or .13 ohms (92.3 amps), for example. Since the meter would round these numbers to .1, one could draw an incorrect conclusion about how much actual amperage draw there is. This is why I don't use an ohmmeter to check for resistance on a high amperage circuit with the meters that I am familiar with. I still think that using a quality charging system tester with a clamp style ammeter would give you the most accurate intake heater current draw in a real-life situation and also tell you which heaters are operating after the engine is running during post heat cycles. Plus, you can check the output of the alternator during post heat cycles with or with out high idle. I apologize now if I have made this topic more confusing than it should be. - John
-
Alternator diode heat
I don’t think that a resistance test on a high amperage circuit will have much value, primarily because the resistance changes greatly as the element is heated. Your test results kind of show that. For example, using Ohm’s Law based on your tests, the following results would be true if there is 12 volts available at the intake heater and the wiring is good condition: Cold intake heater at 12 volts / .1 ohm = 120 amps. (A bit high, but in the ballpark) Warm intake heater at 12 volts / .5 ohm = 24 amps. (I don’t think this is accurate) I think that a quality load tester with a clamp-on ammeter would get the results that you are looking for quickly. You could load test each intake heater circuit individually with the engine off, and then with the engine running. You could also test actual alternator output while grid heaters are cycling with or without high idle. I think using above test procedure would be very informative and you would quickly know whether or not the air intake heaters are performing as they should. This morning I performed a voltage drop test on the intake heater circuits. I prefer voltage drop tests over just inspecting electrical connections. Voltage drop tests tell you exactly what is going on with pinpoint accuracy because the test is being performed while the circuit is under its normal load. Many times I have seen what appears to be a clean and tight electrical connection, but the connection fails the voltage drop test because it is a dirty connection “electrically”. So, here is the information regarding my test. My truck is an ’02 with just over 300,000 miles on the original Bosch alternator. The intake heaters were modified to be operated manually by a momentary switch shortly after the truck was new. Since I only use the intake heaters when needed (never after engine is started), the alternator has had an easy life. At 215,000 miles as a maintenance procedure, I replaced only the brushes and bearings on the alternator. The current batteries in my truck are Group 24, 890 CCA @ 32*, 725 CCA @ 0*. The batteries are four months old. I manually performed two 10 second heat cycles with engine off, then three heat cycles with the engine running. I allowed a brief recharge time between cycles. I recorded the following readings in the last 5 seconds of the fourth and fifth heat cycle with engine running: Voltage drop = .6 volts from left positive battery post to each intake heater positive stud terminal. Voltage drop = 11.0 volts from each intake heater positive stud to common intake heater negative stud terminal. Voltage drop = .12 volts from common intake heater negative stud terminal to left negative battery post. The average battery voltage remained at about 11.7 volts during the last 5 seconds of each test. The sum of the voltage drops under load equals the average battery voltage under load within .02 of a volt. The .6 volt drop in the first test represents each fusible link in the positive side of the circuit, so this voltage drop is expected. The .12 volt drop in the third test represents a good ground circuit (should be under .2 volt drop.) The 11.0 volt drop in the second test represents the electrical load – the actual work being done. The voltage drop tests that I performed do not tell me the amperage draw of the intake heaters, but they do tell me that the condition of the wiring is good and the intake heaters are working. I only posted the voltage drop testing information because I think is the best method for maintaining good electrical connections before problems occur. One of the many benefits from using voltage drop testing is that any potential poor connection is never disturbed, but easily found during the test. Voltage drop testing is a very powerful diagnostic tool for determining the quality of electrical connections, but the procedure is probably the least used and the most misunderstood. - John