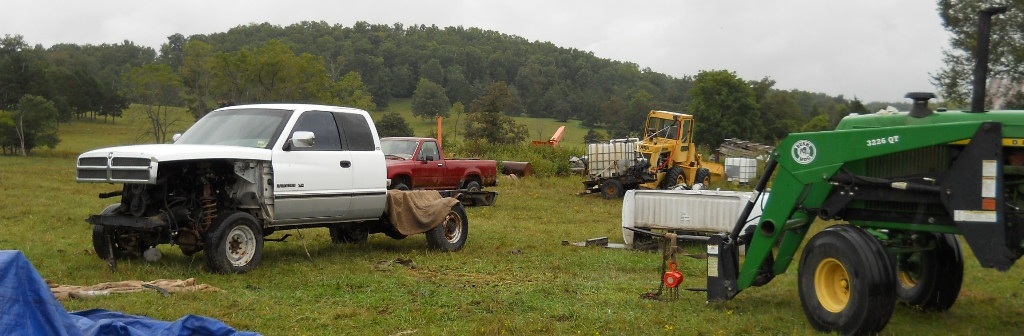
Everything posted by Cowboy
-
Power Steering Gear Rebuild
How to rebuild a 2nd Gen Power Steering Gear Box This How-To is for replacing all the seals in the gear box. For Steering Gear adjustment go here: Steering Gear Adjustment For just replacing the pitman shaft seal. All you have to do are steps “pitman shaft disassembly” & “pitman shaft assembly”. For replacing only the input shaft seal. There are multiple ways of skinning this cat, you can pull the old one out with a couple scews. Or you can slide the rotary valve assembly out enough to pull the front section off to replace the seal… Either way, it’s straight forward, though I would recommend either watching some videos, or reading a write-up first just so you know what you’re working with. If your box is as dirty as mine, I would suggest at least pulling the pitman arm and the piston out to clean everything up, you should be able to reuse the seals if need be. A couple Notes, Tips, and Tricks: Before we go and get our hands dirty. First, we’ll have to, well, get our hands dirty. Your first step should be to clean the living day lights out of the power steering gear box. This is a messy job and so any dirt or debris on the outside, will likely end up on the inside. Note, any dirt or debris on the inside will stay on the inside; it’s just the nature of this job. Get yourself a large clean area to work in. Preferably somewhere if you drop a small ball bearing, you’ll be able to find it. Get some small containers to hold various parts, along with a bunch of rags. Once you start to take it apart DO NOT spin the input shaft any more then necessary. If you go too far, there are little balls that will not only fall out of there guides, but also get jammed and prevent you from being able to take it apart. There are a lot of shims and seals, take note on how everything comes apart. So you can put it back in the same orientation as it came apart. Try and place things on the workbench in a way to make it easier to remember. Before removing a seal, make sure you have a new one in your rebuild kit, also make sure to lube each seal before installing it, along with any moving parts. When lubing seals and O-rings, it is best to dip them, you don’t want to stretch them out if you rub the oil onto them. Pitman Shaft Disassembly Here it sits, unsuspecting and unawares. 1. Take out the (4) 9/16” bolts holding the top cover on, along with the over center adjustment locknut. Now pull up on the cover, (you can also push in on the pitman arm, using a hammer to tap if necessary). 2. Now spin the cover 180* degrees, you should be able to see the teeth on the pitman arm shaft, there are 3 teeth in total. Center them in the hole so you can pull the pitman arm up through the top 3. Take your screwdriver and remove the first pitman shaft seal http://s20.postimg.org/i66fhigkt/PS_Gear_052.jpg 4. Then take the snap ring out and then other pitman shaft seal, along with the washers. Make note of every things orientation. Piston Disassembly 5. Now move to the back of the box, there is a snap ring holding the plug in the end, remove it. To do so, there is a hole on the outside you can put a punch into to dislodge the snap ring. 6. To push the plug out, turn the input shaft all to the left. Do not go any further then needed, and do not turn it back to the right. 7. Get ready for the piston to come out, which means having a clear work area encase any balls fall out, along with a container to put them all in. Once ready, then continue to turn the input shaft to the left. The piston will then come out of the housing, once turning the input shaft doesn’t push it out any further. Continue to push/pull the piston out by hand. Be sure to come straight out, as it likes to bind. 8. Now remove the two strap bolts, along with the tube, be ready for some balls to come out. 9. Put the piston in the vice with some wood blocks or rags to protect it, and remove the 1” hex plug. Rotary Valve Disassembly 10. Now remove the adjuster lock nut with a punch, and then the adjuster plug with a spanner wrench. 11. To remove the input shaft and rotary valve assembly from the housing, pull on the input shaft, you may need to (using a soft punch or block of wood) tap on the worm shaft within the housing to help get it out. There are some washers, and a pancake bearing that go on the worm shaft, be sure to make note of the orientation. 12. Clean everything up as good as possible before taking apart the rotary valve. 13. To replace the input shaft seal, the front part should slip right off the input shaft. Use a screwdriver to pry the old seal out, and use a socket of the right size to press the new seal back in. Dip the seal in PS fluid before installation. 14. To take apart the rotary valve remove the brown O-ring on the end, and tap the input shaft in, it should come apart. 15. Take note how it comes apart. 16. Clean the crap out of everything. Input Shaft Assembly 17. Remove the Teflon seals, and the O-rings underneath them on the rotary valve. 18. Take the new Teflon ones and boil them in water for 5-10 minutes, dry them, dip them in PS fluid, then reinstall. Try not to twist, or stretch them anymore then you have to. 19. Reassemble. There is a peg in the input shaft, and a hole in the rotary valve that must go together (1st pic). And a slot and peg that must go together in the 2nd pic (peg not shown). 20. Now press the whole assembly into the housing, do not press on the input shaft. Piston Assembly 21. After cleaning everything, replace the Teflon seal like you did the others; boil it in water for 5-10 minutes, dry, then lube. Try not to stretch or twist it more then necessary. 22. The part you’ve been waiting for! Working with all them little balls! Clean them all up, and sort them. Half of them are shiny chrome looking, and half are a duller steel. (there is still a dull one in the chrome bin in the picture). 23. OK, now there is a couple ways of doing this, you can either buy the special tool, use a lot of bearing grease and hope the balls stick to the piston walls. Or make your own tool for the job… You may be able to find something that will work, it just has to keep the balls pressed to the outside, and be able to slip out when you install the piston. 24. Now install your special tool into the housing, make sure to push it in from the side with the O-ring. Start by pushing the ball bearings in. You want to alternate between shinny and dull. I like to drop on down the hole, then push it in a little ways with a punch, and then the next one. While saying “Chrome…. Dull…. Chrome….. Dull” to help remember which one I just did. I also think it’s a good idea to give them a little coat of grease as well. 25. You want to keep pushing them in the piston till you have 3 of each color let, 6 total. Then block the ends of the tube with a dab of grease, and put the balls in place. Remember to keep the alternating pattern going, and remember to install it the correct way to make the alternating pattern match what’s in the piston already. Picture is wrong, should be 6 not 4, makes life easier. 26. Put the two halves of the tubes together, set them in place, might take a little tap from a hammer to get them to sit correctly, and then install the straps down and you’re set. IIRC, you’re supposed to tighten the bolts to 4 ftlb’s. 27. OK, now with the worm gear already in the housing, push the piston into it’s final home, make sure your tool stays pushed up against the worm shaft, while you turning the worm shaft to the right (pull the piston in). Doing so will make it so while you push the piston in, the balls that a being kept in place by your special tool, will slip over the worm shaft into there final home. Pitman Shaft Assembly 28. Dip all the seals in PS fluid, and install, make sure to go in square, and don’t forget the snap ring in-between. 29. Now wrap the pitman shaft in one layer of electrical tape, to protect your new seals. And push it in from the top, ensure the piston teeth are centered in the housing. 30. Install the top cover with the lip of the rubber seal facing the cover, and bolt it down. 31. Put the 1” hex plug back in the back of the piston. 32. Install the O-ring for the big housing plug, along with the plug and the snap-ring, make sure to put the ends of the snap ring near the hole you used to get it out with, just so the next person doesn’t have to fight it. The instructions that came with my gates kit, were crap, so I thought I would make my own. Anything I should add or change, let me know.
-
Power Steering Fluid Leak
Well in a way it's nice to know it was rebuilt by someone who knew what he was doing, now whether or not he was paying attention is debatable. No special tools needed, though there is one that's nice to have. It's the one that this gentleman made out of wood. http://www.dieseltrucksite.com/showthread.php?t=1116
-
Power Steering Fluid Leak
Yes it fixes leaks, and yes there is adjustments for taking the slop out.
-
Knocking sound.
The_Hammer On the 12V's it's generally recommended to use the thinnest washers that way it's shooting as far in the bowl as possible with the higher than stock timing people typically run. As far as what's stock, I've seen each size in a stock application. notlimah Thanks, I'm glad you found it useful.
-
Knocking sound.
I'm in the market for a set of cores, I'm pretty cheap though. Otherwise I believe some vendors will buy your cores, you'd have to look at there website. I was never really happy with the 7 holes smoke wise, the current 5 holes seem to be better, but here is a compilation of videos of spooling from different RPM's. This was also with a HE341 which doesn't do as well below 1700 RPM as the HX35. This is also an apples to oranges comparison with a 24V as I adjust fueling based off the smoke output. Bottum of post #4 http://www.cumminsforum.com/forum/94-98-performance-parts-discussion/1976641-turbo-performance-blanket-review.html#post22877737
-
Knocking sound.
From the DAP website: Nozzles are flow matched at 100BAR (1500 PSI with Hydraulic Fluid) to +/- 0.03 LPM. And: Injectors are Pop Tested. Lee makes a good injector, I know plenty of people that will only buy his stuff when it comes to larger sizes that are more sensitive. Other places like DAP are supporting the penny chasers, they still give you a great product, but they have to skimp somewhere to be able to cut the price in half.
-
Knocking sound.
You will be happy with your selection. While not 100% scientific, after a quick test drive I'm currently siding with the 5 holes.
-
Knocking sound.
For a 5 hole, SAC if you can spare the cash, otherwise it doesn't really matter, they'll both run great. The nozzle is the wear item, the milage on the bodies doesn't really matter. On the cores, I believe DAP has two options, either send them the cores up front. Or pay an extra $100 that they will refund you once they receive your cores. This is handy for minimal truck down time. For bodies you have two options, either used bodies with unknown miles that they meticulously inspect, or brand new bosch bodies for an extra $150.
-
Knocking sound.
There is a never ending debate on 5 vs 7 hole injectors. If you really want 7x10 I have a set of nozzles I'd be happy to sell you after I'm done testing with them. They have 2k miles on them and are the exact same as what you linked, other than being nozzles and not the whole injector. The aforementioned neverending debate is why I'm doing this testing. I told DAP I wanted a set of each 5 and 7 hole nozzles that flow identical. And that's how I ended up with the 7x.00105's I've been running and 5x.0013's I'm in the middle of swapping (still have one left to set pop pressure on). On paper the 7 holes sound awesome, better atomization for a cleaner burn and more efficient power... Awesome! However it doesn't work like that, there are two main aspects, atomization and penetration. Atomization is great, but the greater the atomization the lower the penetration. Picture it like this. You have a garden hose on a hot summer day, and you are having a water fight with kids encircled around you. You only have a certain amount of time to hit as many kids as you can. If you have a finer spray, you can hit more kids at once, but it won't reach far enough to hit the kids on the outskirts. But if you have a jet, you can reach all the kids, but the beam it to direct and you'll end up drowning some kids while leaving others completely dry...
-
Knocking sound.
Carefull when purchasing injectors, especially 5x12's. Some vendors will sell cheap marine 370's as 5x12's. They are 5x12's but are the wrong 155° spray pattern, unless you have non-stock pistons you want 145°. 5x12's will be a good match for your 62 unless you want to go all out and squeeze every last bit of power out of it. Then 5x14's will do a little better up top. With the correct tuning, you can run basically any injector. When it comes to tuning, look into the AFC stop-bolt mod. Really handy.
-
Knocking sound.
I have been running 7x.00105 DAP nozzles for the last while on the stock HX35 (mines a 12V too). It took a little tuning but it turned out decent. I'm in the process of swapping in some 5x13's though for testing as they should both flow the same. Amongst the 12 valve guys we measure injector size by there hole count/size/angle. If a place is selling them as XXhp injector but doesn't specify the details, look elsewhere. DAP is typically where I get my stuff. That being said, 145° 5x12's in either a SAC or VCO should do you well, and is enough to support 400 RWHP easy. FWIW, I have a pop tester and would be happy to help in whatever way. I'd imagine the OBDLink shows flywheel horsepower, just something to keep in mind.
-
Quiet exhaust
Whoops, wrong thread. With a CAD axle the front driveshaft wouldn't spin.... If it was a perfect world.... It spins.
-
Any reccomendations on a good DVM
I hope so too. The stand wasn't even out when it fell and broke it off. I have no idea why the knob broke. My old fluke started giving me random readings last month as well... I hope it's the battery.
-
Any reccomendations on a good DVM
My old EX530 took a dump a couple months ago, really disappointed in it. A couple years ago it fell and broke the stand and battery cover off. Then finally this happened. Basically the knob no longer works.
-
???disc vs drum brakes
Drum + Exhaust Brake > Disk. I wouldn't let the rear disks be the "Be all end all" of your decision. Tyler, you could always get a 4" inline unit, that's what the '99 has. I must have gotten luck with the '96, The brakes on it have proven fine for me. I'd have to do some back to back testing to notice much difference between them and the '99 when hauling. Then again it does have a '97 vacuum booster so... EDIT: Whoops, we're on page two... The '99 has the EB across from the drive shaft, and while there's a little delay, it's not that bad in the scheme of things. And yes it does sneeze when you let it of. Sounds like a big rig.
-
loss of overdrive when ac is turned on
On just install a big rig Leece-Neville alternator...
-
advise for an exhaust brake.
Yes. http://www.cumminsforum.com/forum/94-98-non-powertrain/1753153-my-diy-exhaust-brake.html
-
advise for an exhaust brake.
There are a lot of different choices between compressed air actuated, vacuum actuated, and even fully electric. The two names you hear of the most are BD and Pac-brake. The Pac-brake is compressed air actuated so that adds another level of complication. The BD unit is vacuum actuated so that has it's perks. Both those brands have a pressure regulator of sorts instead of your typical hole in the flapper, this give you better braking at low RPM's. And of course there is the option of building your own. Also, once you have one, you'll never go back. I use mine all the time with normal driving unloaded. It's also a good idea to use it frequently to prevent any components from becoming clogged with soot and such.
-
concensus of running EGT's
215 '96, 280 Bar, 285/75/16, NV4500 5th gear, ~75° Ambient Temps Averaged over the course of 47 minutes on I70. EGT's - 680.4°F Pre IC - 185.3°F Post IC - 79.0°F Boost - 7.9 psi Drive - 9.4 psi RPM - 2071 MPH - 73.0
-
NV4500 and 50 SAE GL-4 Synthetic Trans Fluid
EDIT: I guess when you say "these engines" you're referring to the 24V, so I'll just keep my trap shut.
-
NV4500 and 50 SAE GL-4 Synthetic Trans Fluid
I've noticed this with even how people drive my trucks as well as their own. People that drive straight pipe trucks generally lug the crap out of them. Just cause it sounds like you're killing it, doesn't mean you are. Our trucks will make torque, but they don't necessarily like it. And the rest of the driveline for sure doesn't. I only go into 5th above 1500 RPM. Below 1750 RPM I try to keep boost below 10 psi. On an on ramp, I'll accelerate to 60-65MPH in 4th then pop it in 5th to cruise. I love good MPG, but more than that I love MP$. I hit peak torque around 1400 RPM, but you won't find me asking for that power or cruising around that low in the RPM. That's good to hear about the MPG increase with 50W, I hope to swap to 50W myself before to long as well.
-
HY/HX swap
Most people that swap to a HX also increase the boost. If you were to run both turbos at the same pressure I don't think there would be that large of a difference, though I've been wrong before. Despite popular belief, the HY exhaust flows better.
-
NV5600 Fluid, Fast Coolers, Filter
Fast Coolers - $164.99 / 2 = $84.85 DIY Filter... Thing - $6.88 + $14 = $20.88 $84.85 / $20.88 = 4.06 So as long as this thing cools a 1/4 as good as a fast cooler, Success!
-
HY/HX swap
You bet.
-
NV4500 and 50 SAE GL-4 Synthetic Trans Fluid
Just feeling the case on restroom stops and such. Hardly scientific in any way.