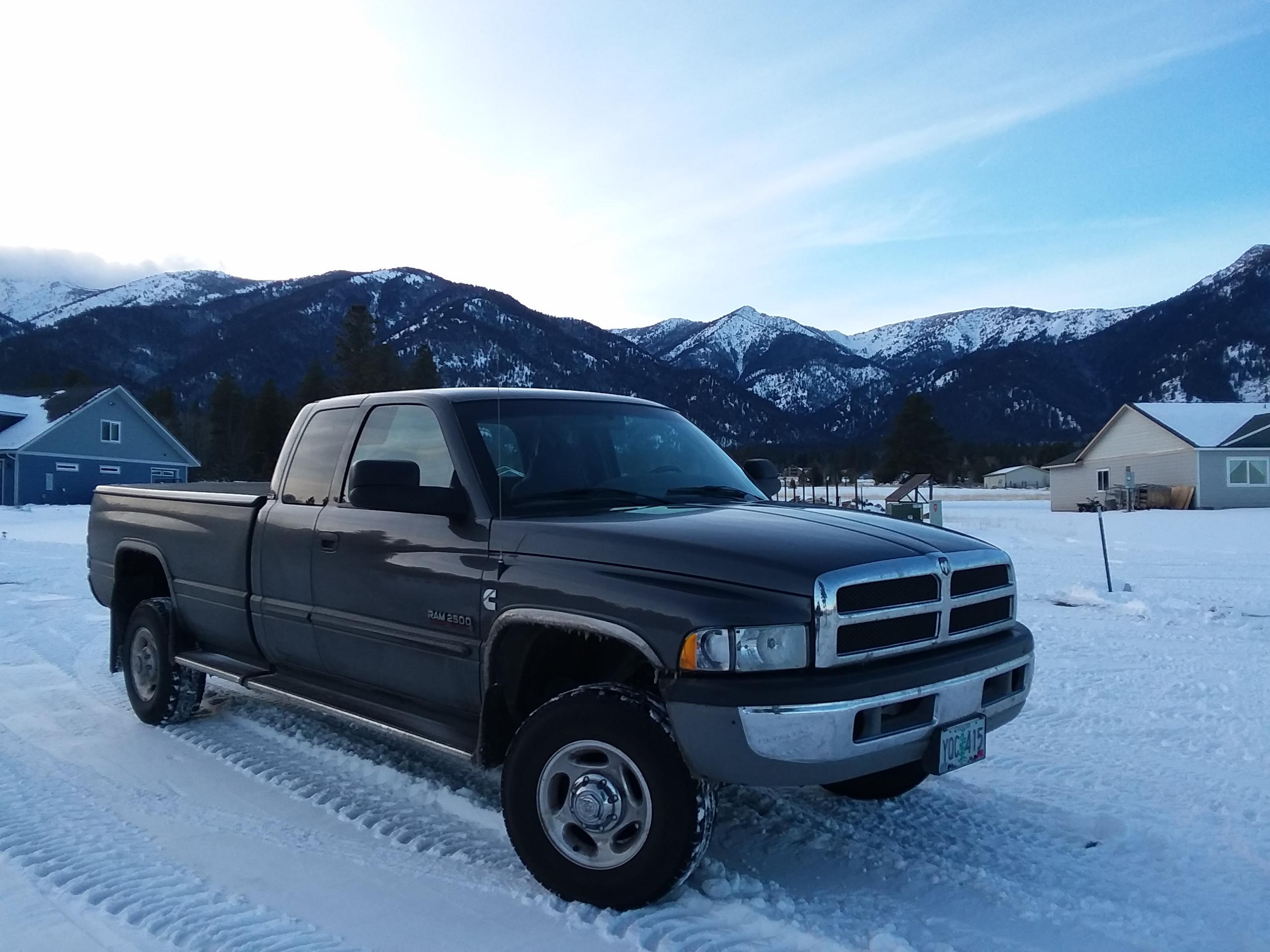
-
Tracing disappearing oil
So, it seems that the turbo was the fix in your case. At least you got lots of life from the old turbo. Any performance difference noticed with the new turbo? John
-
BAM, VP44 may have bit the dust.
Sounds like you are enjoying your new truck. I imagine that the 8 spd transmission with good converter lock-up management and good shift quality would make it an excellent transmission for just about every type of driving situation. If the opportunity should arise, would you mind checking a couple of things and then reporting back? I am interested in how the torque converter lock-up responds under certain specific conditions. What is the lowest gear (in manual shift mode) that the torque converter will lock up and stay locked up with a working exhaust brake? Please give engine rpm and road speed. After defining that gear, will that gear still allow the torque converter to re-lock and the exhaust brake to re-engage, if the converter was unintentionally unlocked? If so, will the converter lock up without having to gain road speed to make it lock up. Does the torque converter lock-up and exhaust brake operate any differently when selecting specific gears in the tow-haul mode? These questions pertain to descending a long, steep down grade with 20 mph and 25 mph curves hauling a heavy load. I am going to be out of town for about four days, so I probably won't have internet access for immediate future replies. Thank you, John
-
Tracing disappearing oil
Thanks for the clarification. Still curious as to if you noted any restriction when you inspected the removed oily drain hose from the old turbo. John
-
Tracing disappearing oil
I always thought that the "W" is for internal waste gate - no "W", no internal waste gate. Am I wrong? Sounds like your project went well - let us know how the truck is doing in another 500 miles or so. I just crossed the 400,000 mile mark on my OEM HX35W, so I am interested to see if your engine oil consumption was for sure from the old turbo. The photo with the oily return hose - after removing that hose, could you tell if it was causing any restriction to flow? Thanks for posting your fix. John
-
Death wobble for the 1st time ever in a 2nd Gen Cummins
That is good news. I didn't catch this on my first read. That would definitely be a contributor to "death wobble". John
-
Problem with idle cut off
I am very interested to see if replacing the intake gasket is really the fix, or is it just coincidental and something else got corrected? I can see how a leaking intake gasket could cause delayed power and low boost (your most recent complaint), but I don't see how it would affect idle or cause stalling. Just my thoughts. Keep us posted for any symptoms that may return: low idle rpm stalling John
-
Left turn radius much less than right turn
So, you are saying that the TIRES were pointed straight ahead and you counted the maximum turns of the steering wheel (about 4 1/4 turns stop to stop) and you centered the steering wheel (2 1/8 turns back to center from either stop)? And, after doing this, the drag link does not align with the Pitman arm? This tells me that the steering wheel is not centered in the steering box. If it is centered, the steering wheel can only be turned approximately 2 1/8 turns each way with the drag link disconnected. In fact, it seems like the steering wheel is a full turn off-center. Not sure what you expect to gain here since the Pitman arm is indexed to the sector shaft. The drag link should not make contact with anything. You will need to address this. There are mechanical steering stops located on the lower front side of each end of the axle housing. When your situation is corrected, your steering to full left and full right will contact these stops. John
-
Left turn radius much less than right turn
Something doesn't seem right here. Lots more questions. Can you give more detail about the event (forward speed, position of the steering wheel when contact was made)? Did you perform the T-style steering conversion yourself? Did you perform the alignment yourself? Did you ensure that the steering gear box was centered and tires were in the straight ahead position BEFORE you connected the drag link to the Pitman arm? Typically the Pitman arm is indexed in a manner that would allow for four different directions of installing (90° apart). That doesn't mean that yours is this way. Have you checked that your new steering linkage is not binding on something when you steer to the left? John
-
-
Left turn radius much less than right turn
Which tire was involved with the "bumped into a concrete pedestal thing?" It would take some serious force to strip the spines on the Pitman arm / sector shaft. Personally, I wouldn't drive the truck until the steering issue is figured out. Possibly, the Pitman arm is bent. Diagnosing this problem is going to be a bit more difficult since you swapped to the T type steering before you fixed the steering problem. Is the steering wheel centered when driving straight down the road? I would put the front end of the truck on jack stands and remove the front tires. Verify that the steering spindle "stops" contact the left and right axle "stops". If steering to one direction does not reach the "stop", then the steering gearbox can be over stressed on hard turns in that direction. If either steering "stop" cannot be reached, then something is still bent, or the steering gear box is no longer centered on the steering linkage after you did the steering conversion. John
-
Tracing disappearing oil
Observing soot at the end of the tailpipe is normal for this era of truck, especially if you have larger than stock injectors. Disconnect the compressor discharge plumbing from the turbo and inspect for an oily mess. Then, disconnect the exhaust band on the exhaust side and inspect for the same. It is possible. The hone pattern intentionally put into the cylinder walls is used as a mild abrasive to condition the outer wear surface of the piston rings for the first 1,000 miles or so of driving. During this period of time, the best mating of the rings to the cylinder wall will occur, resulting in the least oil consumption and least engine blow-by. Using a slippery synthetic oil during break-in reduces the effectiveness of the abrasive characteristics of honing the cylinder walls - it will have a more likely effect of polishing the piston rings and the cylinder walls, resulting in more oil consumption and more engine blow-by. Try performing the oil cap rattle test for the poor man's method of checking engine blow-by. John
-
Death wobble for the 1st time ever in a 2nd Gen Cummins
I would wait for him to drive the truck for at least a month plus a few hundred miles before I would consider it repaired. Many people who experienced death wobble have posted the repairs here on this site, only to experience the death wobble again weeks, or even months later. John
-
Pilothouse/RAM3500 build
👍! John
-
Death wobble for the 1st time ever in a 2nd Gen Cummins
Same method that I use. I have the engine running as well to allow the power steering to put a maximum amount of force to the linkages. Years ago, I set the caster to 4 1/2° positive. It was the best single steering performance improvement on my truck. John
-
Drop rpms
It almost sounds like the "high idle" is being activated. If you drive the truck with the coolant sensor disconnected, does the idle rpm stay where it should? John Some time ago, I did some research regarding this. It seems to be a bit of an anomaly that occurs on some vehicles when static electricity generated from the rubber part of the harmonic balancer jumps to the oil pan as a spark. The good news is that there is no cause for concern. John
-
Death wobble for the 1st time ever in a 2nd Gen Cummins
How does the track bar look. How are you testing the track bar or steering linkage? John