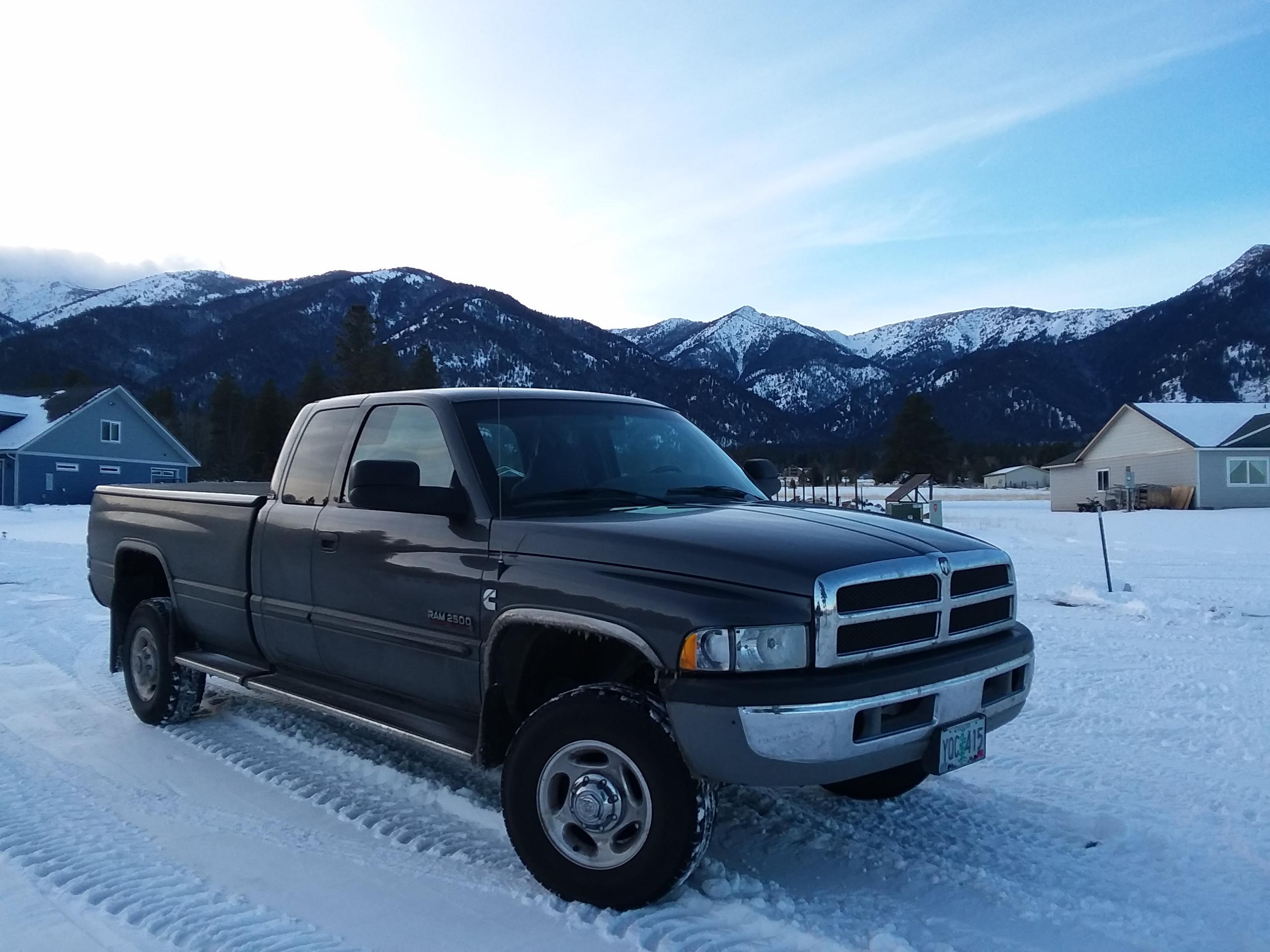
Everything posted by Tractorman
-
02 ram 3500 nv5600 pilot bushing
I don't have any suggestions for a pilot bearing / bushing, but I just wanted to pass on some information. I had an OEM pilot bearing failure at 297,000 miles (original clutch). The failure did some damage to the transmission input shaft pilot bearing surface. I elected to not replace the input shaft and I used the LUK replacement clutch and flywheel which basically replicates the OEM assembly. I also installed a needle type pilot bearing. I am not recommending anything here; it is just what I decided to do. I get to live with the consequences. Sometimes trying to get the maximum life out of everything is not the best decision. As hind sight I should have just replaced my clutch at around 250,000 miles. If I would have done that, the pilot bearing failure never would have occurred. The replacement clutch assembly, flywheel and needle type pilot bearing have since logged over 54,000 miles and the transmission / clutch operation is performing well at just over 350,000 miles on the original transmission. I plan on doing a scheduled clutch replacement again when I approach between 150,000 - 200,000 miles on the new clutch. Hopefully, the pilot bearing will last that long. In my case I think I could have had a pilot bearing failure with any type of pilot bearing with nearly 300,000 miles of operation, so I was not that concerned about using a needle type pilot bearing again. - John
-
Squeal and jump
This is true, but I don't think it is relevant in causing the "squeal and jump" that he is experiencing. That is why I stated it the way I did. For example, if there was any resistance from a faulty u-joint in the front driveshaft, the driveshaft would simply stop rotating - the differential gears would allow for that. - John
-
Squeal and jump
If his truck has a CAD on the front axle (which I think it does), there shouldn't be any noise from the front driveshaft even with worn out u-joints because the driveshaft would not be rotating unless 4wd was selected. @White wondee, I would first do a preliminary check of engine mounts, transmission mount and bell housing bolts, etc. just to make sure nothing is moving around when it shouldn't be. Check the rear driveshaft and carrier bearing, too. - John
-
Truck shakes at 55-65mph, Grinding/vibration when coming to stop as well.
If you compared your Quad speedometer with a GPS unit and they agreed with each other, then I'm thinking you have 4.10 gears - which would be a good match with the tires you have on your truck. - John
-
Truck shakes at 55-65mph, Grinding/vibration when coming to stop as well.
Are you sure about the 3.55:1 ratio? Have you checked your speedometer against a GPS unit? Only reason I am asking is because I have almost the same setup as Mike with the exception of me having an NV5600 (only a small difference in overdrive ratio). 245/75 R16 tires 3.55:1 axle ratio NV5600 transmission Tire size recalibrated by Smarty S03 My tach is approximately 1950 rpms at 65 mph in sixth gear. I have verified the speedometer with a Garmin GPS unit. - John
-
Possible ECM issues
Good info from @Dieselfuture. @Takendad, is it possible that you were unintentionally getting water on the PSG unit mounted on the VP44 injection pump while you pouring water on the ECM? If so, it is more likely that you are having solder problem in the PSG rather than the ECM. - John
-
Nv4500 getting harder to get into gear
Originally, my clutch pedal would not pull up. But one time while trying to detect a squeak under the dash, I pulled upward on the clutch pedal a little bit too vigorously and I heard a noise. From then on the clutch pedal could be raised at least a couple of inches with no resistance. I think a plastic tab broke where the pushrod goes into the master cylinder. It has had no ill effect on clutch operation and as I mentioned before, I am still running the OEM hydraulics. @dripley, this could have been why a new master cylinder corrected your situation. @Doubletrouble, I don't think that the upward travel distance of your clutch pedal is a factor in the problem you are experiencing. - John
-
Nv4500 getting harder to get into gear
I don't think so. Mine pulls up quite a bit farther than that and I still have the OEM hydraulics that are working fine. As long as the pedal sees resistance right away (from where the pedal rests), I think what you are describing is normal. It still doesn't exclude the possibility of having air in the system. - John
-
Nv4500 getting harder to get into gear
The truck may only have 151,000 miles on it, but it also has almost 20 years. Time takes a toll. I am still running the original hydraulics at 351,000 miles, but I lost the OEM pilot bearing at 297,000 miles. A pilot bearing that is dragging will display the symptoms you are describing. - John
-
No fuel gauge and no volt gauge
Did you hear the gremlins laughing at the installer? - John
-
Crank Position Sensor Acting Weird Now...
They hide in the electrical wires. The only time you can see them is when you let the smoke out. They like smoke. I can hear them sometimes..., but only when they are laughing at me. - John
-
p1690 Can't find what's wrong
Thanks for the clarification. I will have to check these wires on my truck. I hope you have fixed the problem. Keep us posted. - John
-
No electrical - ZIP. Up a creek without a paddle!
As long as your suction lines are unobstructed, you will not get cavitation. The only way to get a specific pressure reading would be to temporarily tee in a test port on the suction side of the lift pump and hook up a vacuum gauge. This test is normally unnecessary because there are other ways to prove that fuel is flowing without restriction. - John
-
p1690 Can't find what's wrong
So, are you saying the individual wires are showing bare copper? Or, are you saying the individual wires are still insulated, but the sheathing doesn't quite extend to the end? - John
-
p1690 Can't find what's wrong
Could you post a photo of the specific location you are referring to? - John
-
No electrical - ZIP. Up a creek without a paddle!
Maybe nobody wants to mention this because you asked not to be beat up for your decisions. I am not beating you up, either. Just wanted you to know that driving until the oil pressure gauge begins to drop means that the oil pump is beginning to pump air along with the oil because the oil level is so low. Engine bearings and the turbocharger bearing would be suffering under those conditions. Hopefully, no measurable damage was done. I would never consider installing an air separation system on my fuel system. I have never seen any real proof that it would beneficial enough to justify the additional cost. I have a frame rail mounted FASS lift pump (nothing special) with a suction strainer and OEM filtration. I just passed the 350,000 mile marker on my truck with the second VP44 logging over 260,000 miles now. Just wanted clarify something. Air entering the fuel system is not the same thing as cavitation. Cavitation is destructive. Air entering the fuel system could shorten the life of a high pressure pump over years of operation, but won't be nearly as destructive as cavitation. When air enters the suction side of a pump, the air will compress on the discharge side of the pump to whatever the pump's pressure is operating at. That is all that happens. Engine performance will likely be poor as the air will be mixed with the fuel in the high pressure lines, thus taking longer to reach pop off pressure due to the compressibility of the air. This will result in late timing and an improper amount of fuel injected. Cavitation is much more serious and can occur on an airtight system. If the suction side of a pump is under a partial, but fairly strong vacuum because of a suction restriction, the fuel pressure will drop below atmospheric pressure on the suction side of the pump and some of the fuel will vaporize. When vaporized fuel passes from the low pressure side of the pump and arrives at discharge side of the pump, a very strong implosion will occur precisely at the point of pressure change. These repeated implosions caused from fuel in a vapor state violently returning to fuel in a liquid state will hammer the same spot in the discharge side of the pump and will actually start removing metal from either the gears (or vanes) and / or the pump housing. Totally different behavior compared to air getting in the fuel system. - John
-
Torque Converter Acting Weird
Actually, that is not weird at all, in fact it is normal when there is stray voltage interfering with electronic components. For example, the PCM receives inputs (some wanted and some not) and makes decisions based on these inputs, such as when the torque converter should be locked or unlocked. When stray voltage influences these inputs, the PCM temporarily keeps track of them and determines whether or not to use them or discard them. If the stray voltage signals are frequent enough in a specific time period, the PCM will use these inputs along with the wanted inputs and make decisions accordingly. That's when the bad behavior shows up. When you replaced the batteries, the PCM lost all of this temporary information regarding the stray voltage inputs while the batteries were disconnected. So, that is why it took a couple of days for the problem to resurface. - John
-
Steering Issues/Cold Weather problems
Are you saying that you cannot turn the steering wheel at all? Or, are saying that you can turn the steering wheel a ways either direction and then it stops. If it is the former, then there is definitely something wrong. It could be many things - a relief pressure setting too low, something binding in the steering linkage, a stiff suspension ball joint, a faulty spool valve in the steering gearbox, etc. If it is the latter, then yes, it could be normal. As far as the power steering pump making noise when it is very cold outside, vane pumps are notorious for making a groaning noise when cold. Many vehicle manufacturers use vibration dampeners on the hoses to suppress the harmonics developed from the pump. I would thoroughly check the hose routing for the power steering pump and the brake booster for contact with the body or frame of the truck. Make sure the mounting of the brake booster is secure. Loose or touching components can easily transmit noise and vibrations into the cab. - John
-
Steering Issues/Cold Weather problems
This is just a personal opinion, but I think the power steering system on our generation of Dodge Rams is pushed to the limits from an engineering point of view. Years ago when I would design hydraulic systems for custom applications, I would always look at the maximum required force and maximum required speed of the system. I would then design the system to perform at 15% higher pressure and flow so that the system would never reach relief pressures or have the operation slow down under normal operating conditions. I don't think the engineers did that with our power steering systems. I think that the power steering pump is adequate for flow and pressure, but I think the steering gearbox is too light duty - mainly that the piston diameter is too small. Small piston area equates to a reduction of force with a specific pressure available (approximately 1500 psi maximum). Higher flow pumps do not help because it is the pressure that dictates the force (steering effort). I have 245 tires on my truck and a NAPA remanufactured power steering pump and a NAPA high ratio steering gearbox. When I am on a flat hard dry surface (concrete or asphalt) as I let the clutch out (slight drop in engine RPM) and turn away from a curb, I sometimes feel the power steering stall. It also did this when my truck was new with 265 tires and a slow ratio steering gearbox. Other than the noticeable brief stall under certain conditions, both pumps worked and work fine (the OEM I replaced at 215,000 miles although it was still working fine, and the NAPA one that am currently running). If the pump you received had the pressure relief valve set slightly low, the symptoms you describe would be logical. I don't think the quality control of setting / testing the relief valve pressure and setting /testing the flow control volume at a precise setting is there - especially with remanufactured pumps. - John
-
Left turn signal working wipers
@wil440, this is a very good example of why resistance checks using an ohmmeter and visual checks are not reliable for diagnosing electrical problems The ohmmeter just tells you there is a connection, but does not tell you anything about the quality of the connection - same with the visual check. I am glad you stayed with it and went back to the problem ground wire connection. - John
-
Battery Temp Sensor question
You guys and your popcorn...., - John
-
Battery Temp Sensor question
This is more very good information for diagnostics. This confirms that a large amount of current was flowing from the battery to the alternator. The glowing bolt confirms that the specific connection was a very poor connection - one with high resistance. The fuse did not blow because even though the current flow was high, it was still below the fuse rating. The rest of the wiring and connections were likely good because they did not get hot and handled the amperage load properly. This test has absolutely zero value for high current applications. Perform a simple test. Separate a single strand of wire from a 16 gauge mulit-strand wire. Cut the single strand wire to 12 inches in length. Test it with your ohmmeter - you will find that it reads zero ohms of resistance. Would you use that single strand wire for your charge wire? Keep the information coming. I would like to find out what exactly happened to your alternators. - John
-
Battery Temp Sensor question
@JAG1, this is very good detailed information which may help diagnose your failing alternators. I need to confirm - are you talking about the fuse you installed in the charge wire to the passenger side battery. I am assuming that you are. There is no mystery about the glowing bolt. The glowing bolt scene is telling you something very specific and emphasizes the importance of a good electrical connection. Just because a connector is tight does not mean the connector has a good electrical connection. This is also why I do not rely on physical inspections when it comes to wiring connections that handle high current loads - I perform voltage drop tests, but more about that later. They are easy to do and give you very accurate information about the condition of a connection. The only thing that can make that bolt glow is a poor connection at that exact location. The proof is that the fuse did not blow (because the current did not exceed its rating) and the other connector on the alternator side of the fuse holder was electrically sound. So, regardless of which way the current was flowing (charging current flowing to battery or battery current flowing to failed shorted alternator), the poor connection is a problem of its own and needs to be fixed. I still don't know what caused your alternator failures, but detailed observations like the one from you above should get us there. Can you describe the failed part or parts on each alternator? - John - John
-
Battery Temp Sensor question
Thank you for acknowledging and posting the fact that solenoids didn't fail in the closed position. I was having trouble understanding how a solenoid failing in the closed position would not discharge your batteries rapidly while the truck was shut off and to not see a low dash voltage gauge reading while the truck was running. So, is it correct to assume at this time that you have had two alternator failures with unknown causes? - John
-
volt gauge at 0
@dripley, this may be a place to start. This is the operational description of the voltage gauge from my 2002 repair manual. This may at least explain why your problem corrected itself for now. Hope this helps, - John Operation The voltage gauge gives an indication to the vehicle operator of the electrical system voltage. This gauge is controlled by the instrument cluster circuit board based upon the cluster programming and electronic messages received by the cluster from the Powertrain Control Module (PCM) over the Chrysler Collision Detection (CCD) data bus. The voltage gauge is an air core magnetic unit that receives battery current on the instrument cluster electronic circuit board through the fused ignition switch output (st-run) circuit whenever the ignition switch is in the On or Start positions. The cluster is programmed to move the gauge needle back to the low end of the scale after the ignition switch is turned to the Off position. The instrument cluster circuitry controls the gauge needle position and provides the following features: † Charge Fail Message - Each time the cluster receives a message from the PCM indicating a charge fail condition (system voltage is 10.8 volts or lower), the gauge needle is moved to the 8 volt graduation on the gauge scale and the check gauges indicator is illuminated. The gauge needle remains on the 8 volt graduation and the check gauges indicator remains illuminated until the cluster receives a message from the PCM indicating there is no charge fail condition (system voltage is 10.9 volts or higher, but lower than 16.7 volts), or until the ignition switch is turned to the Off position, whichever occurs first. On models equipped with the optional diesel engine, the instrument cluster is programmed to support the voltmeter gauge needle above the low end of normal graduation and suppress the check gauges indicator operation until ten seconds after the engine intake manifold air heater has completed its cycle.