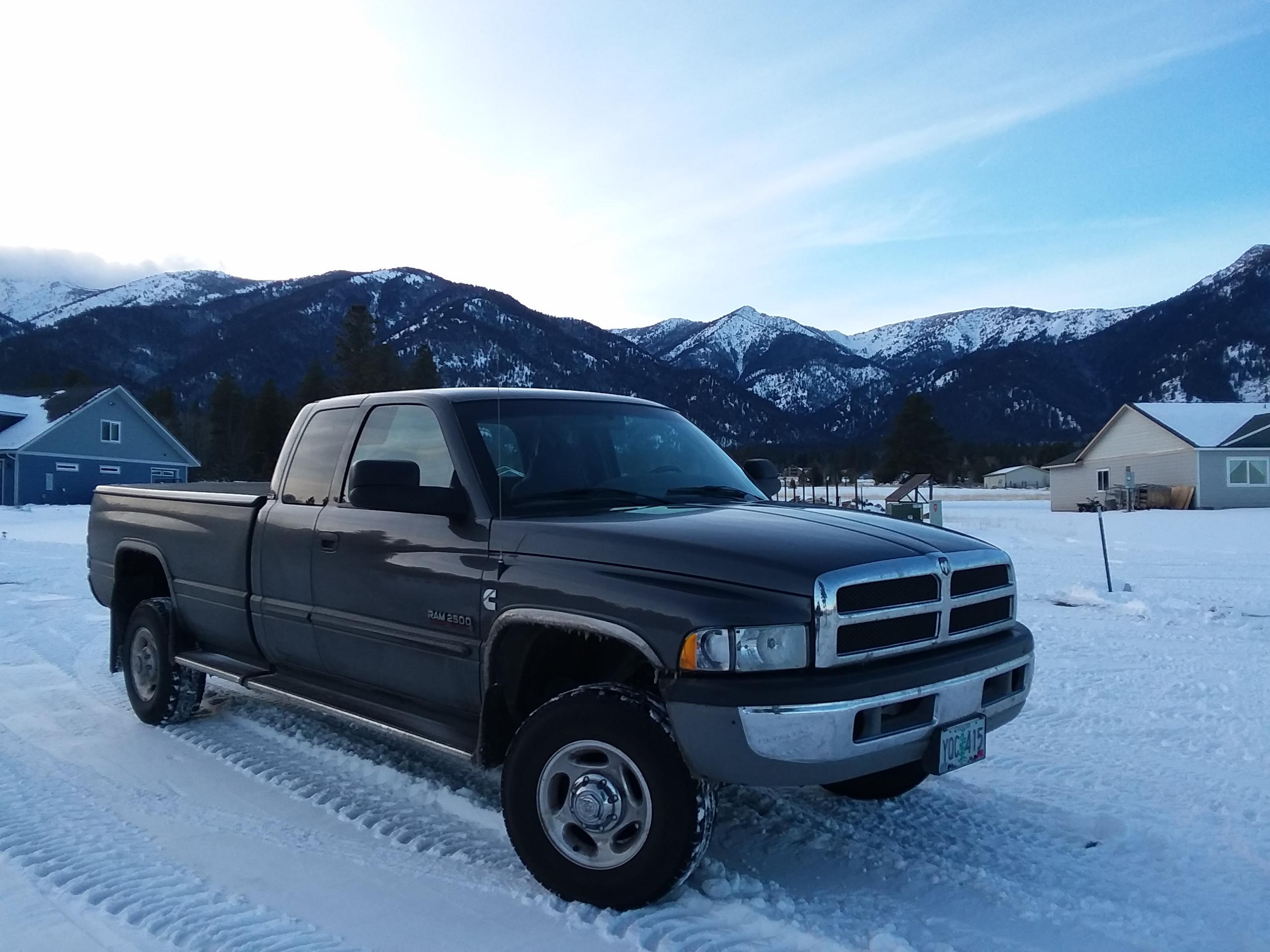
Tractorman
Yearly Subscription
-
Joined
-
Last visited
-
Currently
Viewing Forums Index
Everything posted by Tractorman
-
Hard start
Since it sounds like everything was running fine before you installed a new lift pump, I would thoroughly recheck your work - especially at the fuel connections. The fuel system may be losing its prime or drawing in air which will cause hard starts. Fuel lines or fittings can leak air in while engine is off and still show no signs of leaking fuel when engine is running. You should at least attach a fuel pressure test gauge at the VP44 inlet port to ensure the lift pump is doing its job. Before cranking the engine - try one bump start, then let go of the ignition key. The lift pump should run for about 20 seconds - then try starting the engine. If it starts right up it is an indication that you have a fuel supply problem. The overflow valve is very reliable. Don't start throwing parts at the problem until you have done some diagnostics. - John
-
NV5600 Fluid, Fast Coolers, Filter
I have followed the 1 quart overfill for more than half of the transmission life. Also, I have only used Pennzoil Synchromesh fluid since the truck was new - no particular reason other than that it was called for. The NV5600 has never had any repairs (other than a replacement rear seal) and is still running strong with no synchro issues at approximately 345,000 miles. - John
-
Won't start after releasing water/fuel from Fuel Filter housing
This would be a normal symptom for what you did (opening the drain in the filter housing). Air was introduced to the fuel supply for the injection pump. When you started the engine two hours later, the engine fired because there was fuel in the high pressure lines to the injectors. Moments later when the air arrived to the injection pump and finally to the high pressure injector lines, the engine died because air is compressible and when pressurized, it cannot reach injector pop-off pressure. So, step back a moment and relax. There is no reason to excessively crank the engine to diagnose this problem. All you will get is frustration, dead batteries, and lots of unwanted wear on the starter motor. The lift pump operates as follows: Key in run position - lift pump runs for about 1/4 of a second. Bump start and then key in run position - lift pump runs for about 20 seconds. If the lift pump does not run - then you will need to investigate why. It is quite possible that your lift pump has failed a long time ago and you just didn't know that. Because the VP44 has an internal vane pump to supply fuel to the high pressure part of the VP44, that vane pump could have been drawing fuel through a dead lift pump for a long time. When you introduced air into the system, the engine died and an electric lift pump is needed to purge the air from fuel filter housing, fuel lines, and the VP44. - John
-
T steering upgrade or no?
I have to agree with @Mopar1973Man regarding the stock "Y" type steering. For several years, when my truck was much newer, I was considering changing over the the "T" type steering because I thought the performance would be better. I don't think that now, mainly because of some of the improvements I have made over the years with the existing steering. I have had long life from the OEM ball joints and steering linkages. I also a have a couple of original steering joints still on the truck and the truck is approaching 350,000 miles. About 100,000 miles ago I set the caster to 4 1/2 degrees. That was probably the single most improvement I did. The truck drove much straighter down the road and steering return was greatly improved. I have since replaced the steering gearbox (which was still good) with a quick ratio gearbox. I adjusted the overcenter adjustment using @Mopar1973Man's method and the truck now steers better than any other time during the life of the truck. I don't even think about the "T" style steering linkage anymore. I also run 245 tires and the truck height has never been modified. I even removed the steering stabilizer that I installed a few years ago because I thought it would improve steering performance. It didn't. - John
-
Thoughts on an electric fan?
In 1988 I installed a 4BTA Cummins engine in my Ford E150 van. It was a kit provided by Cummins which included an electric fan. After a year or so running with the electric fan, I removed it and installed a mechanical viscous fan and a shroud. Cooling performance was much better. No one has mentioned the fan shroud. The shroud is equally important as the fan. The combination fan and shroud on our trucks produce a laminar flow through the radiator and other components and use just about 100% of the radiator surface. The depth the fan is positioned into the shroud is important as well for maintaining maximum air flow. Some electric fans are suck through and some are push through. In general, push through fans are less efficient because the air is turbulent and flowing in many directions after passing through the fan blades. The turbulent air has to be redirected which causes resistance and reduced efficiency which means a push through fan will have to have a higher airflow rating to do the same job as a suck through fan. The stock mechanical viscous fan and shroud on our trucks does an excellent job - not sure why anyone would want to change that. - John
-
NV 4500 Removal
I learned that when I did my clutch job. I used a bottle jack and a board to spread the frame for removal. Then I studied the frame and I realized that the jack wasn't needed and I re-installed the crossmember without the jack. Somebody told me a long time ago... work smarter, not harder. Every once a while I exercise that option, but not too often - I don't want to overdo it. - John
-
Replaced master cylinder
Has the clutch engagement position of the clutch pedal changed when the problem started occurring? If it has not I would suspect that there is not a problem with the master / slave cylinder operation. Especially if the symptoms are the same after installing a new master / slave cylinder system. You could be right about a pilot bearing problem. When my pilot bearing began to fail, the symptoms were very similar to yours, hard shifting after driving for awhile. The drag from the failing pilot bearing had a minor effect on the pedal position in which the clutch engaged, but basically it was still the same position. I don't have near the miles on my truck as you, but I have been very fortunate so far; I am still operating with the original clutch master / slave cylinder at 344,000 miles. - John
-
24v injector install
Although the common rail runs higher pressures, I don't think that is as much of a factor as is the contamination the edge filters must deal with. I think the key is the phrase "common rail", which means any metal from the high pressure pump and / or other components in the path of getting to the common rail will be fed directly into every injector. This means that the edge filters could clog or be damaged easily. From what I have read, the VP44 injection pumps hardly ever fail in the manner of sending metal debris downstream. This could account for the edge filters staying very clean. I checked the 2002 repair manual for installing injectors and there is no mention of replacing crossover tubes. When I replaced my OEM injectors at 303,000 miles, I just inspected the tubes and re-used them. - John
-
‘99 2500 rough idle
You will be getting more qualified responses shortly, but I think that higher horsepower injectors simply have a bigger hole which makes it harder for the ECM to control fuel at idle. Getting the pop pressure set at a higher value will help. Also, a valve lash adjustment may help. Others will be responding soon. - John
-
Stuck brake caliper
Some times a good night's sleep does wonders. Glad to hear you are back on the road. - John
-
Stuck brake caliper
This is very likely your problem. There is a compensating port in the master cylinder that is immediately blocked on the forward stroke of the piston (stepping on the brake pedal). This port allows for thermal expansion and contraction of the brake fluid in the brake lines, brake components, and the calipers. It is operational only when the brake pedal is in the released position and the piston has completely returned. The compensating port is normally blocked with about 1/8" of forward piston travel. The photo below is a diagram of a generic brake master cylinder. In this photo the compensating port is called the "inlet" port. The symptoms that you described on your test drive match what would happen if the compensating port is blocked. Thermal expansion of the brake fluid just from operating the brakes and trapped brake fluid equal dragging brakes. - John
-
W-T ground mod
@GlasairIII, you did a good job posting your test results which makes it easier to diagnose. It also would make sense if this is the problem because before you did the W-T wiring mod, the alternator charge wire would have been charging the driver's side battery so the "problem" would have been hidden and everything would have seemed normal. - John
-
W-T ground mod
It looks to me that the electrical connection between batteries has been lost. I think that the PCM is sensing voltage from the driver's side battery, but alternator output is only getting to the passenger side battery. This would explain that while the truck is running, the driver's side battery voltage is falling (telling the alternator to increase the charging rate) and the passenger battery is rising (exceeding its normal limits). Try using a large jumper cable and connect passenger side battery positive terminal to driver's side positive battery terminal. Start the engine and if everything corrects itself, you have found the problem. If this doesn't not correct the problem, then do the same procedure, but only with the battery ground terminals. - John
-
W-T ground mod
First, double check all of your work. There could be a ground connection missing. How are you checking the alternator output? I would check voltage with the truck running at the following locations without grid heaters operating: * Negative lead to negative post on passenger side battery. Positive lead to positive post passenger side battery. Should be around 14 volts. * Negative lead to negative post on driver's side battery. Positive lead to positive post driver's side battery. Should be around 14 volts. * Negative lead to negative post on passenger side battery. Positive lead to alternator output post. Should be around 14 volts (maybe .1 or.2 volts higher than battery voltage due to resistance in smaller charge wire). Write down the readings and report back what you observe. - John
-
Best injector for "MY" truck?
Understood. - John
-
Best injector for "MY" truck?
I never had the OEM injectors pop tested or spray pattern tested. I replaced them at 303,000 miles with RV275's. The OEM's still performed fine - good fuel mileage, no hard starts, and no abnormal EGT's when towing (the last 50,000 miles with Smarty S03). I am not discounting what others are saying about higher horse power injectors, but I intend to run the RV275's for more than 150,000 miles. The photo below shows the OEM injectors at 303,000 miles. - John
-
Alternator Question
I don't think it is a bad idea. My view is a bit one-sided because my only experience is with a Bosch alternator. I ran that alternator for 215,000 miles before I replaced the brushes and bearings. There was no performance issue - I just did it for maintenance. And, since my grid heaters have not post-cycled since the truck was new, this could be why my alternator has been very reliable. However, when I had about 120,000 miles on the truck, I asked a very reputable auto-electric repair shop about replacing the brushes and bearings on my alternator. He asked which one do I have - a Bosch or a Denso? I told him Bosch and he said that he would be happy to change them out, but the brushes are about at at there half-life and the bearings at about one-third life. He recommended that I just keep running it for awhile, which I did. - John
-
Alternator Question
I am still using my original Bosch alternator. Two sets of brushes, one bearing set, and still original diodes. Still passed the AC voltage test last time I checked. One thing I have done different is that I rewired control of the grid heaters to a momentary switch inside the cab. I choose when to use them and they never operate after the engine starts, so there is minimal impact on the alternator. I did the mod when the truck was new - the current odometer reading is 344,000 miles. Just another way of looking at alternator problems. - John
-
Bleeding new VP44 and injectors
Only when he is towing his travel trailer... - John
-
Front brakes dragging
@jtrakel, did you perform the above test? If so, was the passenger side rotor significantly hotter than the driver's side? No. The brake booster doesn't know left from right or front from rear. Are you sure that you are smelling brakes? If you are smelling brakes caused from a dragging pad on a rotor, I would pull off the road and check each rotor on both axles. The one that is overheating should be obvious. - John
-
3rd or 4th gen fuel pump in 2nd gen
Not comparing the supply system in my truck to the supply system in your truck at all. Just pointing out that regardless of which fuel supply system is used, if a positive pressure is present at the inlet of the VP44, I believe there will always be flow over the 14 psi overflow valve because the internal vane pump dictates that flow by engine rpm at a higher pressure (over 100 psi). One thing for sure. Lift pumps cannot push more fuel flow through the internal vane pump than the internal vane pump is displacing at any given moment because the internal vane pump is a fixed displacement pump. Simply stated, the lift pump and the VP44 internal vane pump are plumbed in a series circuit. The outlet pressure for each unit can be different, but the flow is the same while they are both operating in a series circuit. Of course, nothing is ever simple. Example: At a given moment the lift pump may have a flow rate of 30 gph, and let's just say it is returning 5 gph to the tank. This would mean that the VP44 internal vane pump would be flowing 25 gph in that same moment (matching the actual flow from the lift pump (30 gph - 5 gph (return fuel) equal 25 gph). The fuel pressure could be10 psi at the lift pump outlet at that moment, but the VP44 internal vane pressure could be 120 psi if that is what the relief valve is set for. The actual relief valve pressure setting for the internal vane pump is still a mystery, but I believe it is somewhere around 120 psi. Also, my VP44 replacement and in-tank lift pump conversion covered under warranty was done at 87,000 miles on the odometer. Lift pump pressure was 6 psi at idle and 3 psi at WOT with the new system. The original engine mounted lift pump acutually never failed. At 250,000 miles on the odometer (over 4 years ago) I removed the in-tank lift pump and installed a used FASS lift pump on the frame. The in-tank pump was still working fine, I just wanted an easy roadside repair in case the lift pump left me stranded. The FASS lift pump shows 12 psi at idle and 6 psi at WOT. The current odometer is now 344,000 miles. The current VP44 has never seen any inlet pressure higher than 12 psi and that is only at idle, but I believe that the 14 psi overflow valve is always operating and returning adequate fuel flow to the tank for the above stated reasons.. - John
-
3rd or 4th gen fuel pump in 2nd gen
@Haggar, thanks for the reply and the video information. I have watched this video a few years ago. I would really like to hear what the narrator has to say in English. I think it would be very informative. Some people were seriously trying to figure out the mystery of the VP44 back in 2001 (before I even bought my truck). The return flow testing that Mopar-Muscle did in 2001 supports my belief that the internal vane pump provides the fuel flow for the 14 psi overflow valve. The lift pump only ensures that there is a positive pressure at the inlet of the VP44 - a positive pressure means adequate flow. Part of my factory fix from the dealer when my VP44 failed at 87,000 miles was to install an in-tank pump that operated at 6 psi (idle) and 3 psi (WOT). I currently have 257,000 miles on that VP44. @wil440, you may be interested in the following read, as well. Test # 1 well some of you guys ain't gonna like this , especially those led to believe (and those that believe it) ... the bigger is a MUST theory . spent a couple minutes running some tests with a DIGITAL/mechnical flow meter and a MECHNICAL fuel pressure gauge , items under test ... 2000 RAM , DD2's , DD TTPM on level 2 (??) and a HOT PE , ( all levels tested the same at WOT)factory pickup , factory lift pump , factory fuel filter housing unmodified , all banjo bolts intact and unmodified except the banjo to the input of the lift pump is replaced with a 90* swept areoquip type -6AN hose end , the bolt at the lift pump had the schrader cut off and drilled and tapped to a 1/8 npt ( for the gauge) and the banjo fittings between the lift pump and the fitler housing have been drilled to 9/32nd . again all banjo bolts are not drilled out as i have on my ram ( test conducted on the DTT RAM ) . we installed ( LaserBob is helping me and getting #2 fuel poured on his head ) a Sonnex digital flow meter ( inside ID is 5/16") in the return line back to the tank , cut in right at the trans crossmember . gph numbers are fuel returned to the tank . DD2 , DD TTPM (True Torque Power Module) FP volume idle 11 psi 18gph cruise 8 psi 24gph WOT 2 psi 30gph DD2 , TTPM , HOT PE ANY LEVEL FP volume idle 11 psi 18gph cruise 8psi 24gph WOT 0 psi 30gph yes you read that correctly , fuel pressure went to 0 and the fuel volume back to the tank did not change from WOT with 2 psi . the truck did NOT stumble , buck , spit , fart , fall on it's face , nothing , ran like all heck at 0 psi , i will note , my truck ran the same at 0 psi with the DD3's , EZ and a HOT PE . tomorrow we will install -8 lines and an HP carter pump , take flow readings in exact same spot and see what the results are . Mopar-muscle, Apr 24, 2001 Report Test # 2 well , here we go again , todays test was interesting to say the least , and we believe we have it figured out . added the carter HP 15psi 110gph pump on the frame rail next to the tank , -8 bulkhead in the bottom center of the tank , -8 line to the pump , -6 line from this pump to the inlet of an unmodified factory 2000 fuel filter housing , the rest of the system is as delievered from the factory except for a banjo bolt that had the schrader cut off and tapped to 1/8 npt for the gauge , the digital flow meter in the exact same location reading flow back to tank after the tee on the engine . with DD2 , DDTM (True Torque Power Module) psi volume idle 11. 5psi 18gph cruise 9psi 24gph WOT 6 psi 30gph with the HOT PE on any level idle 11. 5psi 18gph cruise 9psi 24gph WOT 4psi 30gph with the addition of the new pump and larger gravity fed pickup point the flow to the tank did not change , though pressure was up , the carter having an internal bypass is living with the backpressure on its output . the concenus is the VP44 is the restriction . the return line from the pump is only returning the excess fuel from the VP44's own internal pump , the more you feed it the higher the backpressure on the line to the pump . the guys with the large pumps , bigger lines and regulator mounted as close to the VP44 as possible have a large amount of the excess flow returned directly to the tank , this is not a bad thing ,( except that at a low fuel level it is possible to foam the fuel in the tank with the large amount of fuel dumping back into it from 2 sources ) but is really overkill as the vp44 uses a set amount of fuel and this is proved by the higher pressure seen with no increase in flow back to the tank . again , the higher the pressure , the lower the flow , BillW explained it perfectly on the prime loc bashing thread and no one ( including myself) understood it or tryed to test it to see if it was true . someone asked if there was a pump that was between 60 and 100 gph , again carter to the rescue , there street pump , 15 psi , about 70 gph , this pump mounted as close to the tank as possible is the best scenerio . the factory designed the system to have the least amount of restriction with the most flow given the flow characteristics of the VP44 . i have not seen the info on HVAC's 34 hp increase with fuel system mod , i will be talking to him to find out the poop on that . we also felt what happens when you have no flow , we had a low fuel level in the tank and under the bulkhead at the botom of the tank , the engine cutout , if the 0psi had no flow , we would have experienced this same bucking . next we will move the factory lift pump back in place of the carter hp pump [This message has been edited by Mopar-muscle (edited 04-26-2001). ] Mopar-muscle, Apr 25, 2001 Report
-
3rd or 4th gen fuel pump in 2nd gen
It would seem that it should be that simple. I am trying to find my source of information regarding the internal workings of the VP44. It was posted around 2007 in the Turbo Diesel Register. From what I understand, the internal vane pump displaces more fuel than can be used by the injectors and all the internal working components of the VP44, including the 14 psi overflow valve. As fuel is metered into the inlet area of the high pressure pump the fuel becomes common with the 14 psi overflow valve. I believe it is because the inlet flow into the high pressure pump being metered is why the vane pump will send the portion of the unused fuel flow over its own relief (over 100 psi) and the overflow valve will operate at the lower pressure of 14 psi. I will find this information and post it here. It may take awhile. The photo below clearly shows that the overflow valve is not in the vane pump inlet. - John
-
Gear Ratios and Transfer case failures - related/unrelated
Whew!! That sounds better. - John
-
Gear Ratios and Transfer case failures - related/unrelated
"Trigonometry"? That's a big word. - John