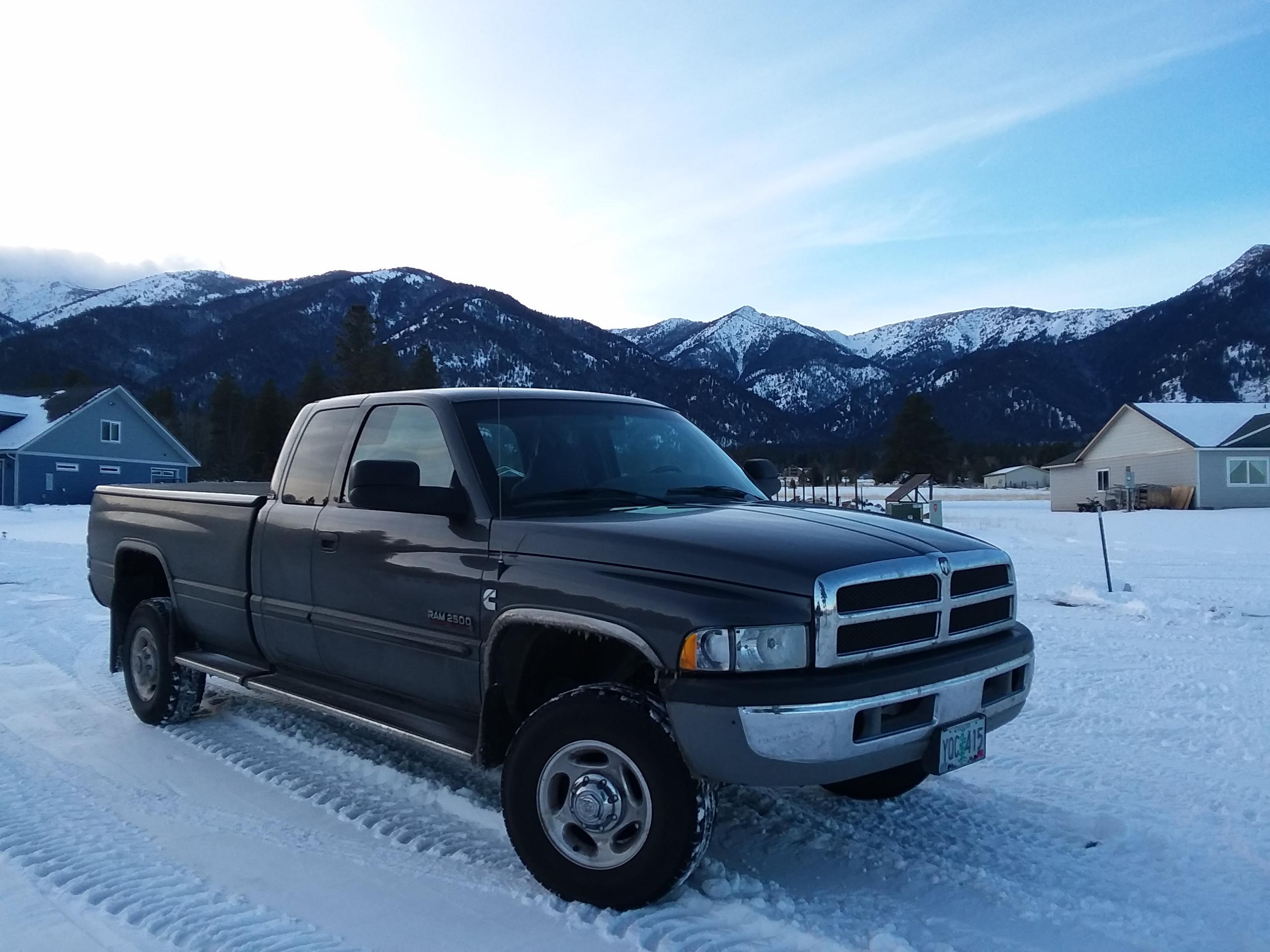
Everything posted by Tractorman
-
Looks like I am joining the 4th Gen ranks....
Thank you again. I will pass along this information to a friend with a 2011 truck who is considering converting to these headlights. Sounds like you and your family are liking the new truck. - John
-
Truck dies with hard acceleration
Things like this shouldn't be talked about on this forum. It's almost like using profanity. - John
-
Looks like I am joining the 4th Gen ranks....
@AH64ID, thanks for the response. What do you think of the low beams alone, without fog lights. How are they for lighting a dark roadway ahead and off to the sides? - John
-
PDC
I do remember that you had trouble with the Joint connection #2 , but don't recall all of the details. However, many times people associate things like burnt electrical connections, melted solder, etc. to a short to ground somewhere in the electrical system. This is rarely the case and here is why. Assume an electrical circuit is protected by a 20 amp rated fuse and a short to ground occurs in the circuit. Instantly an excessive amount of current will flow and the fuse will blow quickly. No evidence of heat is likely to be found because the occurrence happens very fast. Now let's assume the same circuit has a continuous 10 amps flowing through it and is operating normally. Pretend that somewhere in that circuit there is a soldered or push-on connector has a poor connection. Imagine a volt meter connected to both sides of the connector - one side reads 13.5 volts, the other side reads 11.0 volts while 10 amps of current are flowing through the circuit. This equals a 2.5 volt differential across the connection while the connection has 10 amps flowing through it. The result: 2.5 volts (voltage drop) x 10 amps = 25 watts - yes, 25 watts of generated heat at a precise location. What do you think will happen over time? Think of it this way - you can buy a 25 watt soldering gun to melt solder at a precise location. In the second example you will note that the current flowing is only half of the rated fuse and the circuit is operating normally with the exception of the poor connection. A circuit in this status can operate for days or even months without detection until heat does enough damage to break the connection electrically... or start a fire. I don't think you will find a short to ground because I don't think one existed in the first place. - John
-
Borgeson Steering shaft upgrade
No worries. The required grinding is when a Borgeson steering box is being used with an OEM steering shaft. The grinding is done only on the adapter for the steering box shaft - not on the actual steering box shaft. So all is well. - John
-
Borgeson Steering shaft upgrade
I believe you should be good. Just make sure there is no contact with the steering box housing - in the photo everything looks okay. I probably didn't make myself clear about this. Borgeson's instructions aren't very clear about collar you mention. For safety reasons, all steering shafts must be built with a means to collapse in the event of a front end collisions. That is the main purpose of the long slip joint. I believe (because is not clear in the instructions) that the collar is there to stop the upper shaft from sliding down and disconnecting from the upper connection point in the event that the upper set screw backed off. By design the upper connection point is not fail safe. I set the collar on my steering shaft with very slight pressure against the rubber boot. I only snugged the set screw, only because I think it should give in the case of a front end collision. This is what I did - obviously you can decide where to position the collar and how tight the set screw should be. What else is of concern is that (at least on my truck and one other truck) the slip joint was so tight that no axial movement was allowed. Since the steering wheel is mounted in the cab and the steering box is mounted on the frame, there will be axial movement, although small - probably less that 1/4 ". With the sticky slip joint, the energy from the axial movement was transferred to the upper connection point and caused the set screw to continually work loose. It also transferred a random lumpy feel to the steering wheel that was quite annoying. I am rewriting this for clarification and because you didn't say whether or not you tested the slip joint for ease of operation before installation. I have read of two instances regarding the Borgeson shaft becoming loose at the top connection and the shaft actually separating from the steering wheel shaft while the vehicles were being driven. In both instances nobody was hurt. The one instance involved slow in-town driving and the vehicle was braked safely to a stop. The other instance involved mountain driving at higher speeds and fortunately the truck steered itself into the ditch on the uphill side of the road instead of over the several hundred foot drop off. So, I urge you to check for easy sliding operation of the slip joint. - John
-
Head gasket replacement
Actually, those spacers aren't useless. The exhaust fasteners (bolts) are designed to maintain their clamping force under thermal expansion / contraction and vibration. The hardness, diameter, length, and torque of the fastener is determined by the work it must do. A longer fastener will stretch a farther distance than a shorter fastener of the same specifications when torqued to the same value. It is the length of stretch of the fastener that keeps the manifold tight under all operating conditions. If the spacers were not used to keep the fastener lengths the same, then the shorter fastener (with less distance stretch) will likely become loose because its clamping force will be compromised under certain operating conditions. Using studs with lock washers / nuts or using bolts with retainers - either way, the lock washers / lock nuts or the retainers have nothing to do with clamping force. All they have to offer is if the fastener under a certain operating condition becomes loose, then the fastener won't back out. If Cummins has under-engineered the fasteners, or if the operator runs extremely high EGT's, then there is value in using the lock washers / nuts or using the retainers so the fastener won't fall out. I think either using bolts or studs are equally effective, unless some of the studs are of a shorter length. I certainly see the advantage of using studs for ease of manifold installation. I know I will be doing some head work in the near future. I will probably reuse the exhaust manifold bolts without the retainers and just periodically inspect the bolts for tightness. I think they will stay tight. - John
-
Choosing The Right Fuel Lift Pump For My Needs
Yes, that is correct. The internal vane pump generates more flow than can be used by the combination of supplying fuel for the injectors, internal control circuitry, and fuel flowing over the 14 psi relief valve returning to the tank regardless of any fueling demands. Because more flow is being generated than can be used, the pressure must rise to the relief pressure of the internal vane pump (over 100 psi) and flow the remaining fuel to the suction side of the internal vane pump. The lift pump must always generate more flow than the combination of the fuel being consumed by the injectors and the fuel being returned to the fuel tank from the VP44. If the lift pump does its job, there will always be a positive fuel pressure reading at the test port. The remainder of the fuel flow from the lift pump will flow over an internal lift pump relief valve and either return to the suction side of the pump or return to the fuel tank via a separate line. I don't have an explanation for this situation as there are some unknowns here and as you said this happened many years ago. It is possible that under wide open throttle, there were disruptions of fuel flow that the test gauge didn't show. Any disruption of fuel flow could cause bucking. When you added the booster pump, that could have masked the true flow problem and made the symptoms disappear. Just speculation on my part. It is very interesting that you mention this, because I am experiencing a similar condition, but only when towing up a continuous grade with a steady throttle, and not at full power. This symptom has appeared after installing new RV275 injectors. Our definition of bucking could be different, but I am going to try to figure out what is going on and I may even get to the point of adding another lift pump in series just to see if the symptoms disappear. If I do this, I will post the results. - John
-
Choosing The Right Fuel Lift Pump For My Needs
Yes, this is correct. Actually, it is not odd. There is a fixed displacement vane pump inside the VP44 injection pump. This vane pump rotates at the same rpm as the VP44 and provides fuel flow for cooling of the VP44 as well as some other duties. The internal vane pump provides much more fuel than is being consumed by the injectors. Consequently, the fuel pressure rises internally and the excess fuel is forced over a relief valve that is set at over 100 psi (not sure of the exact pressure) and the fuel is returned to the suction side of the internal vane pump. The inlet of the 14 psi relief valve is in common with the outlet of the internal vane pump (operating at more than 100 psi), so there is always fuel flowing over the 14 psi relief valve regardless of the lift pump pressure. The primary function of the lift pump is to supply more fuel to the VP44 than the VP44 can consume for cooling and powering the engine under all operating conditions. Since lift pump is flowing more fuel to the internal vane pump than the internal vane pump can use, this flow restriction is what determines the lift pump pressure reading that you see on the lift pump pressure gauge. My VP44 and lift pump were replaced under warranty at 87,000 miles. An in-tank lift pump was installed (a factory decision). The original lift pump was still good - 12psi at idle and 7 psi at wide open throttle at 2500 rpm in 5th gear. The in-tank lift pump tested at 6 psi at idle and 3 psi at wide open throttle in 5th gear. I was not concerned. I ran the configuration this way until 250,000 miles on the odometer and then I removed the in-tank pump and installed a frame mounted FASS 95 g/hr pump with a suction screen. I did this modification to make a roadside repair possible. At this time I also added a low fuel pressure warning switch with an indicator light on the dash. I am now at 309,000 miles. The replaced VP44 has logged 222,000 miles with lift pump pressures that never see anywhere near 14 psi and most of the time considerably less. Also, I have been using the Smarty S03 programmer for the last 50,000 miles and I just replaced the OEM injectors with RV275 injectors. All of the fuel lines are stock and with the exception of a 150 micron suction screen for the lift pump, the fuel filtration system is stock. Back in 2001, Mopar-Muscle posted the results of a test using a flow meter installed on the return line after the collection point of all returning fuel flow. Below is part of a thread out of the Cummins Forum showing the results of two tests. - John Test # 1 well some of you guys ain't gonna like this , especially those led to believe (and those that believe it) ... the bigger is a MUST theory . spent a couple minutes running some tests with a DIGITAL/mechnical flow meter and a MECHNICAL fuel pressure gauge , items under test ... 2000 RAM , DD2's , DD TTPM on level 2 (??) and a HOT PE , ( all levels tested the same at WOT)factory pickup , factory lift pump , factory fuel filter housing unmodified , all banjo bolts intact and unmodified except the banjo to the input of the lift pump is replaced with a 90* swept areoquip type -6AN hose end , the bolt at the lift pump had the schrader cut off and drilled and tapped to a 1/8 npt ( for the gauge) and the banjo fittings between the lift pump and the fitler housing have been drilled to 9/32nd . again all banjo bolts are not drilled out as i have on my ram ( test conducted on the DTT RAM ) . we installed ( LaserBob is helping me and getting #2 fuel poured on his head ) a Sonnex digital flow meter ( inside ID is 5/16") in the return line back to the tank , cut in right at the trans crossmember . gph numbers are fuel returned to the tank . DD2 , DD TTPM (True Torque Power Module) FP volume idle 11 psi 18gph cruise 8 psi 24gph WOT 2 psi 30gph DD2 , TTPM , HOT PE ANY LEVEL FP volume idle 11 psi 18gph cruise 8psi 24gph WOT 0 psi 30gph yes you read that correctly , fuel pressure went to 0 and the fuel volume back to the tank did not change from WOT with 2 psi . the truck did NOT stumble , buck , spit , fart , fall on it's face , nothing , ran like all heck at 0 psi , i will note , my truck ran the same at 0 psi with the DD3's , EZ and a HOT PE . tomorrow we will install -8 lines and an HP carter pump , take flow readings in exact same spot and see what the results are . Mopar-muscle, Apr 24, 2001 Report Test # 2 well , here we go again , todays test was interesting to say the least , and we believe we have it figured out . added the carter HP 15psi 110gph pump on the frame rail next to the tank , -8 bulkhead in the bottom center of the tank , -8 line to the pump , -6 line from this pump to the inlet of an unmodified factory 2000 fuel filter housing , the rest of the system is as delievered from the factory except for a banjo bolt that had the schrader cut off and tapped to 1/8 npt for the gauge , the digital flow meter in the exact same location reading flow back to tank after the tee on the engine . with DD2 , DDTM (True Torque Power Module) psi volume idle 11. 5psi 18gph cruise 9psi 24gph WOT 6 psi 30gph with the HOT PE on any level idle 11. 5psi 18gph cruise 9psi 24gph WOT 4psi 30gph with the addition of the new pump and larger gravity fed pickup point the flow to the tank did not change , though pressure was up , the carter having an internal bypass is living with the backpressure on its output . the concenus is the VP44 is the restriction . the return line from the pump is only returning the excess fuel from the VP44's own internal pump , the more you feed it the higher the backpressure on the line to the pump . the guys with the large pumps , bigger lines and regulator mounted as close to the VP44 as possible have a large amount of the excess flow returned directly to the tank , this is not a bad thing ,( except that at a low fuel level it is possible to foam the fuel in the tank with the large amount of fuel dumping back into it from 2 sources ) but is really overkill as the vp44 uses a set amount of fuel and this is proved by the higher pressure seen with no increase in flow back to the tank . again , the higher the pressure , the lower the flow , BillW explained it perfectly on the prime loc bashing thread and no one ( including myself) understood it or tryed to test it to see if it was true . someone asked if there was a pump that was between 60 and 100 gph , again carter to the rescue , there street pump , 15 psi , about 70 gph , this pump mounted as close to the tank as possible is the best scenerio . the factory designed the system to have the least amount of restriction with the most flow given the flow characteristics of the VP44 . i have not seen the info on HVAC's 34 hp increase with fuel system mod , i will be talking to him to find out the poop on that . we also felt what happens when you have no flow , we had a low fuel level in the tank and under the bulkhead at the botom of the tank , the engine cutout , if the 0psi had no flow , we would have experienced this same bucking . next we will move the factory lift pump back in place of the carter hp pump [This message has been edited by Mopar-muscle (edited 04-26-2001). ] Mopar-muscle, Apr 25, 2001 Report
-
What NV5600 fluids are yall running?
I have used the Pennzoil Synchromesh for the life of my NV5600 transmission - 308,000 miles so far. It has never had any shifting problems and has never been disassembled. I have replaced the rear shaft seal at 268,000 miles. I used this oil only because when the truck was new, synchromesh oil was required. Since it has worked well, I never tried anything else. - John
-
NV4500 temps with coolers
Just say that you used oil based paint. - John
-
Belt squeal fixed
The belt chirping is normal and the cause is the high speed rotating mass of the alternator rotor being forced to an abrupt stop. As alternator capacity has grown significantly over the years this symptom and worse symptoms for long stroke four cylinder engines and some six cylinder engines (especially diesel engines) have cropped up. For many long stroke four cylinder engines there was excessive belt movement while the engine was idling. A one-way clutch (de-coupler) pulley for the alternator was introduced in the late nineties for some four cylinder Chrysler vehicles. This de-coupler eliminates the tug of war on the serpentine belt at low engine speeds and allows the alternator rotor (not the pulley) to free wheel when the engine is shut off. It was an eye opener for me on my wie's 2006 New Beetle TDI. I didn't know about the de-coupler pulley back then and I unnecessarily replaced a belt tensioner because of engine noises, intermittent brief losses of power steering, and a serpentine belt that looked like it was wanting to leave the premise while the engine was idling. It turned out that the alternator de-coupler pulley locked up and was behaving like a solid pulley. I replaced the de-coupler pulley and the belt ran as smooth as glass, the engine became quiet at idle again, and the brief loss of power steering gone. I believe starting in late 2006, the Cummins engines use a de-coupler pulley on the alternator. I know there is one on my son-in-law's '06 and a friend of mine's '07. There is no belt chirp on these trucks because the alternator rotor can free wheel when engine is shut down. - John
-
Fueling issue
How did you test this pump? Did you test with a fuel gauge at the VP44 inlet? I am assuming that you had to drop the tank to replace the in-tank lift pump. Air would have been introduced into the fuel system during this repair. Did you verify with a gauge that the new lift pump was working before you started the engine? Also, did you use the "bump starter" method several times to run the lift pump for 20 seconds at a time to purge out air before you started the engine? If you have done none of the above then you have not verified that the new lift pump is working properly. Even if it is working properly, the air introduced during the repair may now be in the high pressure injector lines. This air would will have to be vented by loosening some injector lines at the head while the engine is being cranked over. - John
-
Morning Pic For Today...........Post A Pic around your place.....
-
Weird bearing noise
This is good information. I don't think the problem lies in the following: * pilot bearing (since it is not in operation with clutch pedal released) * clutch release bearing ( if it made that kind of noise, I would think that you would hear other release bearing noises when operating the clutch pedal) * transmission (fourth gear on a five speed is the 1:1 gear, so the counter shaft is not loaded) Things I would check: * carrier bearing - you can drive the truck for a bit and then stop and feel the bearing (carefully) for excessive heat. As mentioned earlier, if the bearing is making that kind of noise it will usually spin the outer part of the bearing inside the rubber mount. * anything belt driven - remove the serpentine belt and check all pulleys. Pay special attention to the fan pulley. * transfer case - if I recall, you have replaced it recently. Check that the shift lever linkage is in proper position for each selection. Just some thoughts, - John
-
Weird bearing noise
More information would really help forum members to help you. Can you provide any of the following information? * What gear were you in? * What was the road speed? * What was the engine rpm * Were you stopped, accelerating, decelerating? * Where did the sound come from? * Were the conditions the same each time it happened? These are a few things that only you know that could help with diagnosis. - John
-
Cylinder pressure
Typically, the maximum back pressure generated by the use of the exhaust brake is about 60 psi and exhaust manifold temperature will stay well under 500 degrees no matter the length of time used. I don't think there is anything to be concerned about. I have been using an exhaust brake for over 300,000 miles and I still have the original exhaust manifold setup. I use this exhaust brake many, many times per trip on every trip. I am sure they can, but I think it would be a preference, not a need. - John
-
freezing fuel filter
I have a similar setup, but I am using a FASS frame mounted lift pump with a Napa 3270 screen on the inlet side. This fuel screen is 140 micron rated, significantly more coarse than your Wix 33007 50 micron filter. Your filter would be very easy to replace with the Napa 3270 screen and it just might fix your problem. - John
-
killer dowel pin question
@Dieselfuture, I apologize for my dry sense of humor. I did know what you meant and actually I am in the same boat with my 2002 truck. I will also be checking my potential KDP when it is becomes necessary. Of course, we could schedule replacing the seal as a maintenance item instead of waiting for failure (oops, there goes my humor again).. After all, it's not like we haven't gotten the miles out of the seal. - John
-
killer dowel pin question
Maybe the KDP will fall out and make it leak sooner, then your wish would be granted. Of course, then there might be other minor things to repair as well. - John
-
W-T ground mod
I have been manually operating my grid heaters with a momentary switch that switches both on at the same time since December of 2001, and for 307,000 miles. If there were to be any negative side effects, I think they would have surfaced by now. I like the fact that I am still using my original Bosch alternator with only one brush and bearing set replacement and that replacement was done as a maintenance procedure at 216,000 miles - not as a failure. So, @Dieselfuture, I would not be concerned. Curiosity finally got the best of me, so I did an experiment today. I wired my grid heaters back to factory (I know - sounds crazy). I used two test lights simultaneously at each grid heater positive terminal (heavy wire connection at the grid heater). I performed the following tests with ambient temperature in the shop at 50 degrees: 1. Key switch on, Wait to Start light on. The test lights did not light. I then realized that I am using the IAT Fooler, so that made sense. I am certain that both test lights would have lit had the IAT circuit been returned to OEM wiring since that is how they worked before I added my momentary switch modification. This isn't the part that I was curious about, anyway. 2. Start engine after Wait to Start light goes out. Both test lights lit and stayed lit for about 15 seconds. One light dropped out and the other light dropped out about 5 seconds later. After a few seconds one test light turned on for about 5 seconds and then turned off. Another 5 or ten second passed and the other test light turned for about 5 seconds and then turned off. This cycle kept repeating itself. Of course, because I am not crazy, I put my momentary switch back into operation. Also, just for curiosity, I have checked a 2003 truck and a 2006 truck - they both use one relay to operate both grid heaters simultaneously. They cannot be operated independently. I thought that was interesting. - John
-
Looks like I am joining the 4th Gen ranks....
@AH64ID, congratulations on your new ride! At some point down the road could you let me know what you think of the OEM headlights on your new truck? Daniel Stern (of Daniel Stern Lighting) recommends converting older 4th generation reflector style OEM headlights to the newer projector style OEM headlights - your year of truck was mentioned. I would like to get your opinion. Thank you in advance, - John
-
Dead tach, water temp & oil pressure?
I can't say whether or not a 6.7 viscous damper will work on an 02, but I have read that engine OEM dampers that have replaced with the 6.7 viscous damper, it is necessary to remove the damper when replacing the serpentine belt. You may want to check that out if it matters to you. I have the Fluidampr on my truck ( 4 years and 90,000 miles) and no need to remove it when changing the belt. For me the Fluidampr works as advertised and there have been no issues. - John
-
2000rpm max and no codes.
To rephrase what @Mopar1973Man is saying: 10 mv AC, 30 mv AC, 50 mv AC, and 100 mv AC would be saying the same thing as .010 v AC, .030 v AC, .050 v AC, and .100 v AC respectively. So, if @2001white's meter is showing .57 mv, that would be the same as .00057 v AC. That seems a bit off the scale to me, but I may not be reading his meter correctly. - John If this isn't confusing enough, let me know so that I can make it more confusing.
-
High Pitched "Cricket" Buzz
Don't rule out a boost leak. I have heard boost leaks that have a reed sound (like in a musical instrument). In two cases the cause was a broken hose clamp and the reed-like sound was coming from the vibrating hose end under certain boost conditions. Some of the symptoms you have described could match that of a boost leak. - John