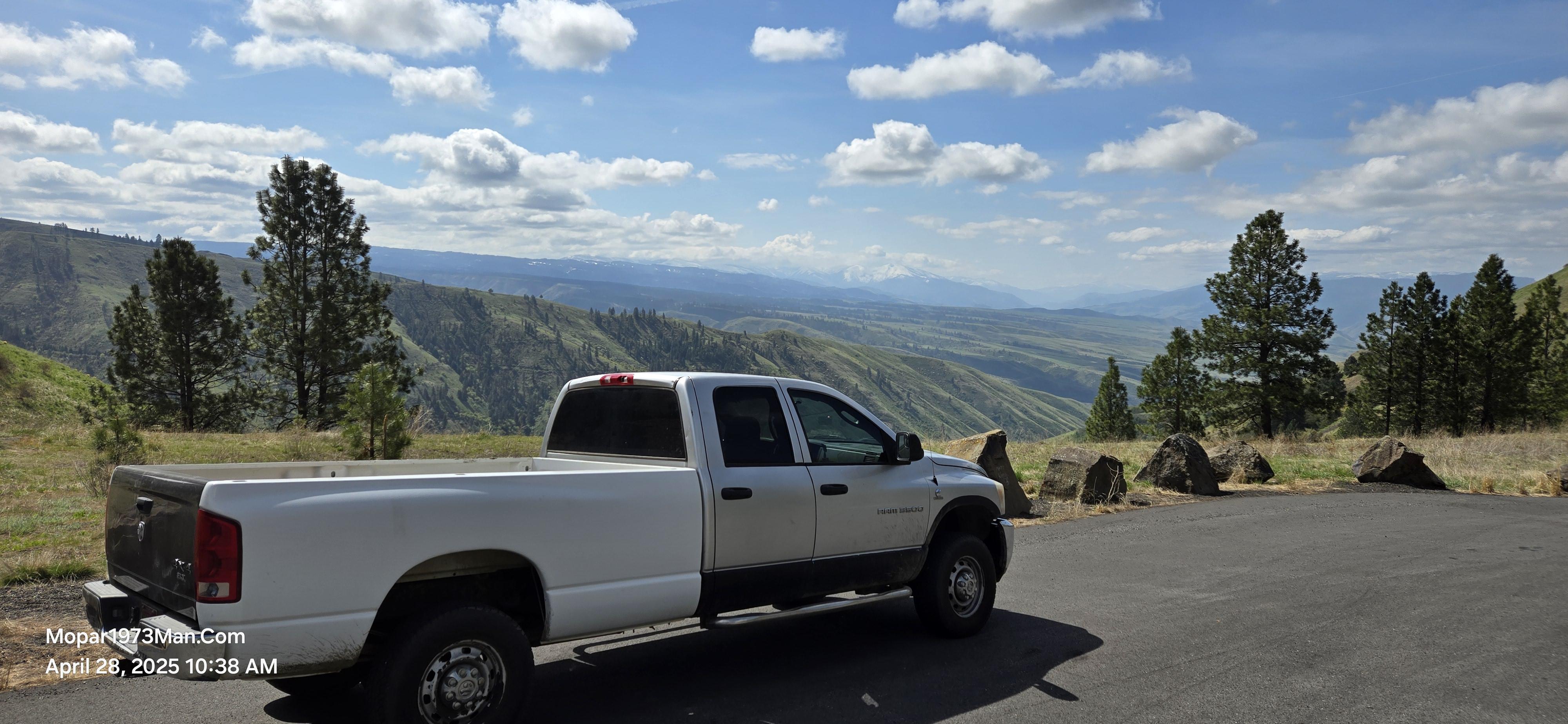
Everything posted by Mopar1973Man
-
1999 p-pumped 24v tps low voltage
I'm not sure what to say. I've got no idea what is left of the stocking wiring. Can you read error codes?
-
New VP44 - Engine requires excessive cranking when hot
Yes. It does. Mirrors the same signal from the ECM.
-
Oil Cooler Gasket
Kept yelling at the my truck to quit peeing in the shop. After 17 years you figure the truck would be house broke right?
-
fan clutch help
Fan does NOT lock till about 210 to 215*F. My truck runs 197*F to 205*F. Normal for my 195*F thermostat. About two needles width from the 190*F mark. Even my A/C temp rises in traffic and slow moving. Fan isn't locked and this totally normal.
-
Aftermarket Blend Doors
Not the UVs that kills the dash. Its the out right surface temperature that is cooking the oils out of the plastic. Then just takes vibration to crack the plastic.
-
fan clutch help
Doesn't matter. Its the thermostatic coil in the front that makes it lock or unlock. Housing doesn't mean anything.
-
Video showing engine fan engaging late
Yup. 208F to 212Fwhen mine locks the fan. Been like that for 17 years.
-
Help, Cummins Down..........1694 PCU Code
Yup... Like myself I blew my PCM, broke the mainshaft in the transmission, blew up the driver side front wheel bearing. Forget the idea of spare parts...
-
Aftermarket Blend Doors
I just places an order for gauges for a gent in Ontario. @mr.obvious. Going to be installing ISSPro EV2 gauges (Boost, Pyro, and EGT). He's also running a intank fuel pump. We both know the fuel pressure is sub-par with a intank lift pump. As for dash you can extend the life of the plastic by using Armor-All. The trick is to wash the plastics all off and the spray the Armor-All on and leave it cook in the sun. It will change from whitish to clear shine. This keeps some of the oils in the plastic for a bit longer. Mine is cracking but I'm holding it at bay for now. Eventually I'll need to do a dash top replacement like @dripley has. As for the HVAC system I've replaced the evaporator and heater core once. Blend door is still fine. Then vacuum motors still working fine. A/C works good. The heater works awesome even in subzero.
-
Help, Cummins Down..........1694 PCU Code
Not worth it. 17 years later I'm on the same ECM. You would have to send that spare in and have it reflashed with your software. There is 52 different version of software per year. You would be better off doing the W-T ground wire mod. Then doing the PCM protecting fuse. Way cheaper and no need to buy a second ECM and have it flashed.
-
Baffles?
Typically I aim for about 35 PSI low side. The hi side should be about 225 PSI on a hot day.
-
Not sure if I'm having a fuel issue or tranny issue
Could you fill out your signature so we know what we are working with exactly. Most likely the torque converter clutch is failing or the clutch packs in the transmission are done. Assuming 48RE... @Dynamic is a site transmission guru.
-
Oil Cooler Gasket
Finally had to change a oil cooler gasket on my truck. It has been seeping for the last 5 to 6 months leaving a small bit of coolant on the floor of the garage. I will let you all know that oil cooler gasket set is a Cummins only thing. I tried NAPA, Autozone and few others and no one stocks this gasket set. As for changing it out is pretty straight forward. You need to remove the air filter and the oil filter. On the oil filter housing remove the oil hose for the turbo. Then the bolts holding the oil cooler in place are all 10mm heads. After I got it pull out I compared the new and old gasket to realize that the rubber seal lip had failed. You can see its completely missing on the old gasket. This is where my coolant leak was from. Most likely just old age. Filter side of the oil cooler. Coolant side of the oil cooler. These photos are without clean up. Just removed and photos taken. 17 years of tap water and creek water the block has 385k miles and no signs of scale build up at all. As for clean up. Sharpen my puddy knife and scraped off the old rubber seal. Be very careful that no debris get into the oil holes below. I used a bit of brake clean and cleaned up the outer housing. Oil cooler I buffed the sealing edge with a scotch brite pad in a drill. Very lightly to just smooth the seal surface again. I did an extra step and chased the threads on the bolts to clean them up going back in. They were kind of corroded from dried coolant and oil. I used a 8mm x 1.25 die. The sandwich gasket between the filter and the cooler came off super easy and peeled off clean. I will mention that it much easier to stack up all the parts and pass two bolts through and get that started. DO NOT use any sealants here! Just bolt it up. I check the Dodge FSM for torque specs and found nothing about the oil cooler for installation. I was aiming for about 15 foot pounds on these bolts. Make sure to pull the thermostat so you can refill the block with coolant. After you start the engine and let it run a bit make sure to check the oil level too. I dumped the oil filter out and ended up adding oil to be in the normal range again.
-
Help, Cummins Down..........1694 PCU Code
@Auto Computer Specialist will test the ECm before even starting a repair and then notify you of what has failed as well.
-
Dead ECM
Yup. This is true. Still at this time its just little commuter cars. Still in all all the heavy duty stuff is handled by diesel engines. When I see trains running strictly electric then I'll worry. Still even today trains are diesel over electric motors. I don't think diesel engines are going anywhere. I still think at some point electric cars will fail. Because the US electricity grid is not capable of handling that kind of load. I've got a friend that has a family member in Cally with a electric car and pays MORE to recharge his electric car because of the price of electricity down in Cally is just scary high in price. Then if you use too many kilowatts then the price jumps again and nearly doubles. This just makes it better to own fossil fuel vehicle over electric. But even in Cally it $4.xx a gallon for either fuel.
-
Vacation fun
Pretty easy...
-
48 RE TRANNY WILL NOT MOVE
Time to tag @Dynamic he would know exactly what to do.
-
Mystery pedal thing
Yup. I figure that exactly what it was. My stupidity... Now I check the BHAF every time I install it by hanging it downward and shaking a few times. Even doing that with oil filters now too. Also will not pre-fill any oil filter any longer. Too much risk of any debris being accidentally poured in the filter.
-
Tuning help just bought a cummins
Typically not. Its the prime on the injection pump or the lift pump is allowing air into the system. Typically its a suction leak on the lift pump side which normally never leaks anything on the ground but continues to draw air in all the time running or not.
-
Dead ECM
Electric cars out here will not make it. Too far from charging stations and you'll need a diesel generator to just recharge if your stuck some where without power. We still have people out here living without city power. Just the logging industry needs diesel powered equipment and diesel trucks to bring logs to the mill. Farmers still will need diesel powered tractors and diesel trucks to haul cattle or food to the market.
-
Smarty s03 today :)
Just for information value. From the Dodge FSM. 310 Bar is equal to 4,500 PSI +/- 250 PSI is equal to 293 (4250 PSI) bar to 327 bar (4,750 PSI). I know this is what the Dodge FSM states. What Bosch ESI Tronic states a different number and span.
-
Oil Temperature vs. Timing
I found another secret I've got to share with the group. For guys with manuals or not using the transmission temp sender. Remove the test plug on the oil filter housing and then install the transmission temperature sender. The secret found. If you want to find out if your over advancing timing its is super simple. Measure the engine oil temperature. When I started I was roughly +10°F over the coolant temperature. I was starting to test MPG in different RPM ranges. Found the lower bands tend to run hot oil wise and tend to be a bit low in MPG number still. After figuring out a new timing map now I'm roughly 20°F below coolant temperature on the flat highway run. If coolant is 197°F it can run 178°F to 181°F in oil temperature now. Since advancing the timing tends to burn more in the cylinder the block coolant was rising quite a bit and trapping more heat in the engine oil. Dropped 2° of timing in the 1,500 RPM range and this flipped the other direction to -20°F cooler. Worth it to install the sensor in the engine oil port. Remember... When you seeing heat that is a percentage of work energy turned into heat. The more you can trim off the heat in every device right down to the rear axle this means more power being put to the ground efficiently.
-
Left arm is happy again.
Now seeing the photos it looks like headliner material that they used. Foam backed fabric. I was thinking of recovering that piece with something else like vinyl.
- HVAC Case Removal
-
Replacing Injectors
Replacing injectors on a CR engine isn't much different that changing injectors on a 24V. There is a few differences but the process is the same. First you need to make sure the fuel rail area is clean. Best to take a power washer and blow all the crud and dirt off the fuel rail side of the head. Remove the intake horn and grid heater. Pack a few rags in the intake to prevent anything from falling in by chance. Now you need to remove the fuel rail and all the connecting lines to the head. It will come out in one piece with the rail and the lines attached. Be aware the overflow valve has a banjo and sealing washers on top and bottom. There is a few wires to remove. The two injectors control plugs on the driver side of the head. There are two sensors there on the intake. Now remove the valve cover. You should be looking at the injectors and the wiring for them. Take a 8mm socket and remove all the connections. Then lift the wiring gasket up and out. 10mm socket and remove all the exhaust rockers. I suggest laying a rag out and laying them all out in the order removed. This way you can put back without adjusting the valve lash all over again. Suggested to do a valve lash after removing the rockers. You'll need a 24mm wrench for removing the crossover tube nuts. Socket will work but the back might be a bit too limited. Now using a small flat blade screwdriver you can lightly pry the connector tubes out. Suggested to replace the crossover tubes. Now with a 8mm socket you can remove the two bolts holding each injector down. Using a flat blade screwdriver hook the solenoid collar and carefully pry upwards out of the head. When it does come up make sure to check for the copper washer on the tip and no left in the head. Assembly is fairly straight forward as well. Now when installing the injectors you can place each injector in its hole make sure to locate the crossover hole towards the driver side. Another way to see it is the hold down collar is square toward the front and rounded towards the rear at least for the 2006 I have here. Now you need to seat the injector in its hole tighten the injector hold down to about 44 inch/pounds. This is only to push the injector into the head. I used a nut driver and 8mm socket and tighten till the injector is fully seated and backed off the bolts till loose again. Now you can push each crossover tube into place. Do note the position of the locating balls on the shank they face upwards might twist just a little bit to find the notch. Now twist in the crossover tube nuts. Torque them to 11 foot/pounds. Now you can torque the injector hold downs to 89 inch/pounds. Now you switch back and do a final torque of the crossover tubes to 37 foot/pounds. Lay the the integrated gasket / wiring down and lightly torque the nuts to 11 inch/pounds. Just much easier having the 8mm nut driver and lightly tighten the nuts. Be aware over tighten will damage the injector and this is a very expensive mistake not to make! Now you can install the rocker arms. This is why I lay them out in order then you can get them back in place without having to do a valve lash adjustment. The bolt is torqued to 27 foot/pounds. It is suggested to do a valve lash adjustment but you can quickly check after installing the rockers if that is needed or not with a feeler gauge. You can now install the fuel rail and connect all the lines again. Make sure to get both sealing washer on the overflow valve. Don't forget the supply tube from the CP3. Slip in the valve cover and tighten down. Install the grid heater and the intake horn. Priming is simple. Loosen only #1 injector line. Crank for about 5 seconds you should have fuel dribbling out. Now tighten and crank again it should start right up in about 5 seconds of cranking.